a. An estimate of the non-value-added cost caused by each activity b. The root caused of the activity cost (such as plant layout, process design, and product design) c. The appropriate cost reduction measure: activity elimination, activity reduction, activity sharing, or activity selection
For situations 1 trough 6, provide the following information:
a. An estimate of the non-value-added cost caused by each activity
b. The root caused of the activity cost (such as plant layout, process design, and product design)
c. The appropriate cost reduction measure: activity elimination, activity reduction, activity sharing,
or activity selection
1. It takes 1 hour and six pounds of material to produce a product using a traditional manufacturing process. A process reengineering study provided a new manufacturing process design (using existing technology) that would take 30 minutes and four pounds of material. The cost per labor hour is $12, and the cost per pound of material is $10
2. With its original design, a product requires 10 hours of setup time. Redesigning the product could replace the setup time to an absolute minimum of 30 minutes. The cost per hour of setup time is $250.
3. A product currently requires eight moves. By redesigning the manufacturing layout, the number of moves can be reduced from five to zero. The cost per move is $15.
4. Inspection time for a plant is 4,000 hours per year. The cost of inspection consists of salaries of four inspectors, totaling $100,000. Inspection also uses supplies costing $3 per inspection hour. A supplier evaluation program, product redesign, and process redesign reduced the need for inspection by creating a zero-defect environment.
5. Each unit of a product required seven components, the average number of components is 7.3 due to component failure, requiring rework and extra components. By developing relations with the right suppliers and increasing the quality of the purchased component, the average number of components can be reduced to seven components per unit. The cost per component is $600.
6. A plant produces 100 different electronics products. Each product requires an average of eight components that are purchased externally. The components are different for each part. By redesigning the products, it is possible to produce the 100 products so that they all have five components in common, this will reduce the demand for purchasing, receiving, and paying bills. Estimates savings from the reduced demand are $750,000 per year.

Trending now
This is a popular solution!
Step by step
Solved in 5 steps

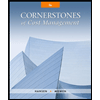
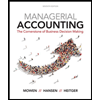
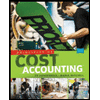
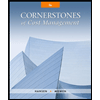
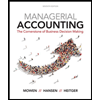
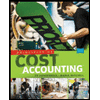
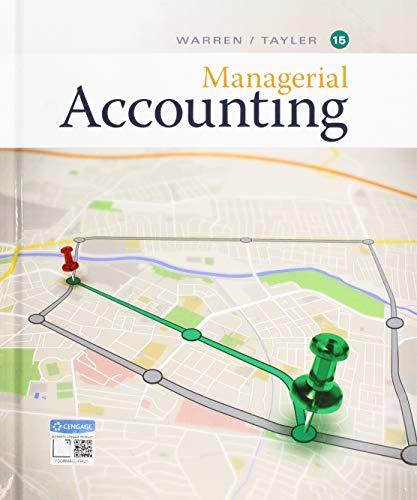
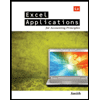