What is Overall Equipment Effectiveness?
Overall equipment effectiveness or OEE as it is known can be defined as a widely standard to measure manufacturing productivity. In other words, it can also be defined as the exact percentage of time which is productive. If the score of overall equipment effectiveness is 100%, it is an indication that only good parts are being manufactured with no stop time. Hence OEE of 100% means 100% quality, performance & also availability.
Measuring OEE is considered to be the best practice because it gives an insight to the organization on how to improve the manufacturing process. Hence this metric serves the purposes of identification of losses, improvement of productivity by reducing wastage & also benchmarking the developments.
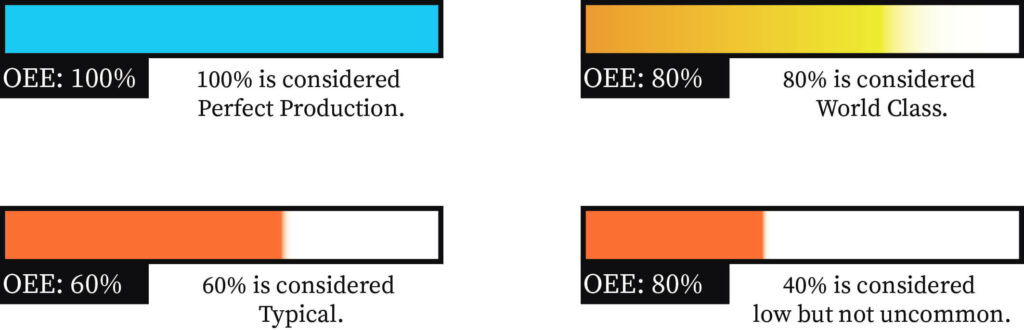
The formula for overall equipment effectiveness:
Example
The number of shift hours in a day is 6 hours or 21,600 seconds and the number of units produced in a day is 3,000 units. Time taken to produce a single unit is 6 hours. The number of defects in a day is 60. Considering the example, the ideal cycle time is 6 hours, the good count is 3,000 units, and the planned production time is 21,600 seconds
Hence overall equipment effectiveness = 83.33%
Terminologies in OEE
Following are some of the terms which are to be known for overall equipment effectiveness:
- Fully productive time: This is the production time after considering all the losses.
- Planned production time: This is the total time that the equipment is expected to generate productivity.
- Run time: This is the time when the system is scheduled for production.
- Cycle time: This is the time taken by the system to manufacture a single part.
- Total count: This is the count of all the produced parts including the defective ones.
- Good count: This refers to those parts that satisfy the quality standards.
- Good parts: These are produced parts that satisfy the standards & do not require rework also.
- Quality: This implies the produced parts which do not meet the quality standards & also the ones which require rework. Quality can be calculated as Good count/Total count.
- Performance: This indicates the number of times when the production has been stopped. A good OEE score means that activities are conducted as fast as possible. Performance can be calculated as: (Ideal cycle time*Total count)/Run time.
- Availability: Availability includes the stoppage time which is both planned & not planned. A good availability score in terms of OEE is an indication that the operations are conducted as per the planned production time. Availability can be calculated as Run time/Planned production time.
Calculation of OEE
Overall equipment effectiveness can be calculated by following two simple methods. They are as follows:
- Simple calculation: First & foremost method in calculating the OEE is the proportion of fully productive to production time. Hence OEE = (Good count*Ideal cycle time)/Planned production time
- Preferred calculation: This calculation is based on three vital elements namely performance, quality & availability. Hence OEE = performance*quality*availability. When compared with the previous method, this is the preferred method because it not only provides the OEE score but also the numbers that resulted in losses for the company.
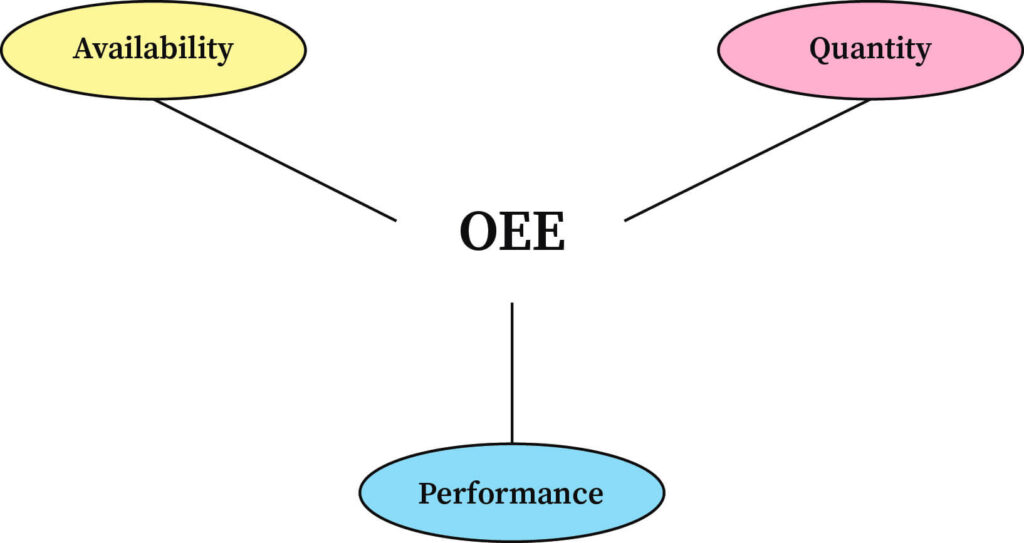
Six Major Losses in case of Overall Equipment Effectiveness
The main objective of OEE is to avoid the losses that arise from productivity. These losses can be divided as follows:
Losses can be divided into three categories each having two sub-divisions of losses:
Available losses:
- Failure of equipment: Under this type of loss, the equipment would not work at the time of scheduled activity thereby causing unplanned downtime. Some of the examples under this type are the breakdown of equipment, failure of tools, etc.
- Setup and adjustments: In this case loss can arise because of various reasons like any maintenance that was planned well in advance, conducting the inspection, any changeovers, etc.
Quality losses:
- Reduction in yield: This refers to the production of damaged parts from the time the firm was started till stability in the production is being achieved. This can mainly arise at the time of any wrong settings, machine warm-ups, etc.
- Process defects: This refers to any damaged parts which were produced when the production was constant & that includes scrap parts or parts that involve reworking. The major reason for this defect can be because of wrong settings of the equipment, errors in the equipment, etc.
Performance losses:
- Reduction in the speed: This would happen when the operation takes place slowly than the ideal cycle time. This can happen because of reasons like unfavorable conditions in the environment, equipment not maintained properly, materials of substandard quality, etc.
- Idling & minor stops: Also referred to as shortstop, this happens when the machine breaks for a small-time period. The reason for this can be due to any jam, hindrance in the flow, because of cleaning or incorrect settings, etc.
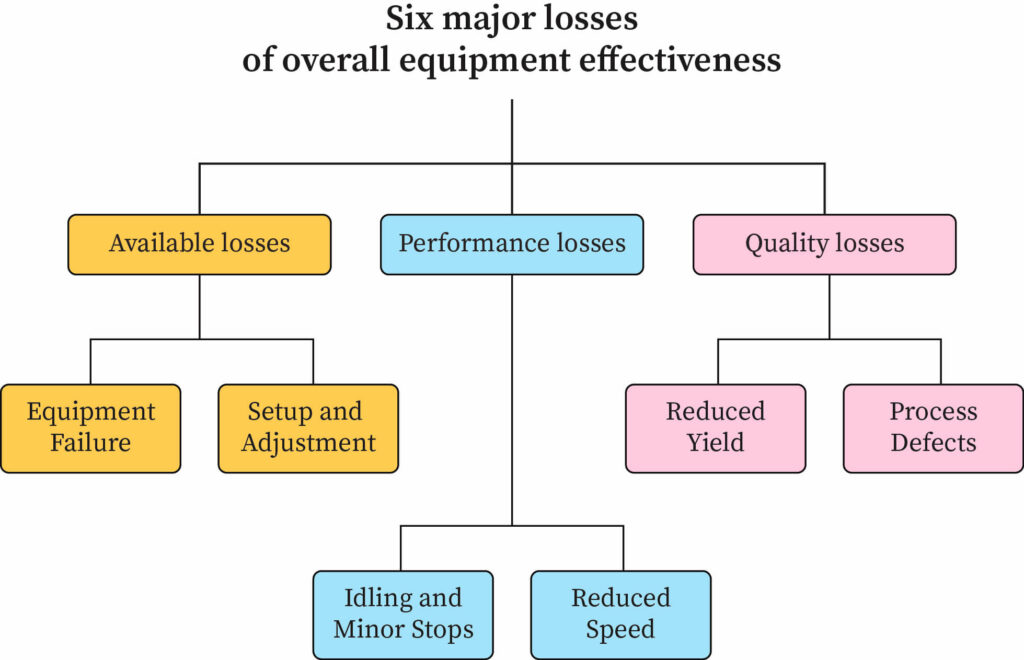
Advantages of Using the Overall Equipment Effectiveness
Following are some of the benefits of using the OEE
- Helps in increasing competence: The main objective of any firm is to always reduce loss at the time of production which thereby increases the competitiveness of the firm among its rivals. With the help of OEE, the organization can identify any weakness in the production activities & thereby take suitable measures.
- Analyze performance: OEE helps the firm to analyze production-related issues by emphasizing visibility rather than making any guesses. This can help to work on improvements.
- Increase the workforce: Various sources of information like downtime of the operator, data relating to productivity, etc. can help the company to allocate the resources to suitable areas, identify areas of excess allocation & decide where new hires would be required.
- Reducing machinery costs: OEE is a type of strategy which helps in understanding the real performance of the equipment & also provides a signal to the organization regarding future issues like repairs, breakdowns, etc. Effectiveness in the equipment can result in the reduction of maintenance costs, failure of the machine, etc.
- Return on investment: Companies generally make huge investments in machines. Hence it is always required to achieve a maximum return on investment. Using the OEE strategy can help in producing an additional percentage of products at the same time period. This can create a great impact on the bottom line.
Context and Applications
This topic is significant in the professional exams for both undergraduate and graduate courses, especially for
- B.Sc. Biochemistry and Molecular biology
- Bachelor of Molecular and cellular biology
- M.Sc. Biological science
- M.Sc. in Bimolecular chemistry
- Masters in Biotechnology
Want more help with your operations management homework?
*Response times may vary by subject and question complexity. Median response time is 34 minutes for paid subscribers and may be longer for promotional offers.
Search. Solve. Succeed!
Study smarter access to millions of step-by step textbook solutions, our Q&A library, and AI powered Math Solver. Plus, you get 30 questions to ask an expert each month.
Overall Equipment Effectiveness Homework Questions from Fellow Students
Browse our recently answered Overall Equipment Effectiveness homework questions.
Search. Solve. Succeed!
Study smarter access to millions of step-by step textbook solutions, our Q&A library, and AI powered Math Solver. Plus, you get 30 questions to ask an expert each month.