1 Describe the
.docx
keyboard_arrow_up
School
Einstein College of Australia *
*We aren’t endorsed by this school
Course
113
Subject
Accounting
Date
May 21, 2024
Type
docx
Pages
6
Uploaded by ElderMeerkat4444
1. Describe the FIFO principle.
A technique for storing and rotating food is called first in, first out (FIFO). The food that has been
in storage the longest ("first in") should be the next food utilised ("first out") in a FIFO system.
This technique assists households and restaurants in organising their food storage and in using
food before it spoils
Explain how regular inventory checks can support rock rotation and replenishment.
Stock rotation is a way of minimizing potential stock loss due to expiration. When rotating stock
be sure to use the FIFO rule, and also verify expiration on all products. In some cases, you may
receive a shorter dated product then the one on the shelf. How does this happen? Sometimes
the wholesaler has made an error on FIFO, or may be trying to push their product out to you so
they don't encounter the
loss. Sometimes short items are sold to buyers at a lower cost so that the buyer can maximize
profits and the seller can minimize loss. If a stock item is nearing its sell-by date, stock may be
reduced. Its price is lowered in order to be more appealing to customers. Reduced stock is usually
included in the rotation of stock, and is therefore moved to the front of the shelf ahead of any
unreduced stock. In most cases you may consider not replenishing this item, removing it from
your inventory and removing the order sticker, or changing your reorder point on your POS. Be
sure to check with your wholesaler on the return policy and capitalize on the benefits of
returning versus discounting, or how much to discount based on how much you will get just
returning it
3. Describe the product life cycle (PLC) and cover the four stages in your answer.
A product's life cycle is the period of time between its initial consumer introduction and its
eventual removal from the market. It is often divided into four stages: introduction, growth,
maturity, and decline.
4. What is meant by the term slow-moving item?
Items that move slowly are those that have a low turnover rate and are kept in the warehouse for
a lengthy time. The reason why slow-moving products are stored or take up a lot of room is
because they sell slowly
5. LIst four reasons why an item may become a slow-moving item
This problem can be brought on by a number of things, including inaccurate sales projections, a
slowing market, aggressive rival promotions, or even your procurement team's desire to acquire
more products in order to reduce per-unit costs. 6. List two ways that you can check
for slow-moving items.
Every day, spot-check four inventory items.
Do the math for inventory turnover.
• Examine the typical days to sell (or use).
Analyse the storage costs for inventory items.
Utilise sales data to forecast trends.
®.X
TEACHERS
HEALTHY
7
Segregation of food items and non-food items reduces the risk of contamination. List three
strategies you can apply to ensure these items remain segregated.
• A bin for wet waste like leftover food, vegetable or fruit peels, tea bags, etc.
Dry waste should be further divided into plastic, metal, glass and paper.
Electronic waste like CDs, pen drives, bulbs, tube-lights, computer systems, electric cables,
keyboards, batteries, motherboards etc.
Describe each of the following inventory systems:
a) Ledger inventory system: A physical or digital record called an inventory ledger keeps track of
inventory transactions. All transactions recorded in this ledger should add up to the same amount
as the relevant account's total in the general ledger.
b) Integrated point-of-sale system: An integrated POS links the software and hardware used by
your company to handle payments, such as a credit card reader and inventory management
systems. Your payment system may become more effective and linked thanks to this connection
9. List the key procedures involved in ordering stock. Briefly explain what happens at each stage.
Order processing, a crucial component of order fulfilment, is the workflow that guarantees client
orders are accurately processed and delivered to the appropriate location. Order processing may
be carried out by a single person or small group, depending on the size of a company's activities,
or it may take place at a distribution centre or warehouse where pickers, sorters, and packers
collaborate to execute orders. Order placement: When a consumer places an order, the
company normally sends the order's data, such as the goods, quantities, shipping information,
and delivery addresses, to an order management system. Based on the delivery address and item
availability, the OMS will automatically choose the best warehouse location to ship from if the
business has several fulfilment centres or warehouse locations. Both delivery costs and travel
times are lowered as a
result. • Picking inventory: The act of removing a certain number of products from stock in order
to fill client orders. Because it directly affects the efficiency of the whole order processing
workflow, order picking must be a tightly regulated procedure. The faster orders are correctly
chosen, the faster they may be packed and sent.
• Sorting: During this step, selected things are divided into groups based on where they will be
used. For instance, each item must be sorted into its proper order before it can be packaged and
dispatched if zone or batch picking techniques are utilised.
• Packing: The act of placing products into suitable shipping boxes in a protected manner. Along
with weighing the parcels and labelling them with the recipients' addresses and any relevant
delivery instructions, packing also include packaging.
10. List two ways that an order for stock may be made.
Market orders and limit orders are the two primary forms of orders that investors can use to
purchase or sell stocks. Market orders frequently execute instantly at the current market price.
Limit orders won't go into effect until the market price reaches the investor's desired price.
11. List four pieces of information you would expect to see in a loss/wastage log or report.
Record how much is being wasted.
If you have a scale, the best option is to place the food in an empty bus tub and weigh the waste.
Record its weight in the logbook (including the weight of the bus tub). Later, a manager can
subtract the known tare weight of the bus tub.
If you do not have a scale, record the number of portions leftover or the volume (1/2 a pot, 2
gallons, etc.)
Chefs and Managers should review yesterday's waste logbook at the beginning of the following
day's shift.
The top 5 waste items should be discussed with the kitchen team at a pre-shift meeting. Ask the
team for ideas to reduce those items.
12. Why is it important to ensure that loss and wastage of items is reflected in the inventory
system?
Increases profitability and makes sure you can complete open or incoming orders. Additionally,
inventory management saves money. Understanding stock trends can help you better utilise the
stock you already have by allowing you to know how much and where you have it in stock.
13. Answer Count things up. Before you go shopping, take stock of what you already have in your
pantry, refrigerator, and freezer to avoid overspending.
Plan your meals.
Safely store and consume leftovers.
Your preview ends here
Eager to read complete document? Join bartleby learn and gain access to the full version
- Access to all documents
- Unlimited textbook solutions
- 24/7 expert homework help
Related Questions
1. Explain which of the conversion methods would be suitable for the following. Justify your choice:
Upgrading the software for an Automatic Banking Machine (ABM/ATM)
Adding a new inventory system along with new computerized cash registers in a supermarket
Implementing a student course management system in a university
2. List four reasons why your participation as a user of an information system is critical during the systems development life cycle, linking the concepts of user involvement and change management in a software implementation project.
3. Why is it so important to understand how a business process works when trying to develop a new information system?
TASK B:
In the context of the impact of a change on an organization, How would you characterize the following changes?
Adding electronic scoreboards to a cricket grounds.
A Telco consolidating call centres in one country.
A Telco installing fibre-to-the-home to replace copper wires.
A Telco launching a TV service.
arrow_forward
1. What is the major advantage of using a perpetual inventory system?
a. It provides efficient internal control over materials.
b. It avoids inventory shortages and overages.
c. It avoids losses due to theft.
d. It minimizes error in posting receipts and issues of materials.
2. If the 300 defective bolts(normal spoilage) were repaired and management wanted to be sure the incremental costs did not exceed the cost of producing new units, how would the rework costs be accounted for:
a. Charged to overhead and spread over the costs of all products.
b. Expensed as extraordinary.
c. Charged to those belts repaired.
d. As normal materials, labor and overhead.
arrow_forward
Which of the following is the best
description of the operating cycle?
Multiple Choice
The length of time that it takes to convert
raw materials into inventory
The length of time that it takes to convert
raw materials into accounts receivable
The length of time to acquire raw
materials and receive payment for them
when sold
None of the options
arrow_forward
How can you provide recommendations to improve efficiency in a parts store?
arrow_forward
Silver Limited is a manufacturing company that produces furniture. To improve efficiency and usefulness, Silver Limited is constantly incorporating advanced, information technology into its business information systems. When Silver Limited does not have available production capacity, sometimes it purchases furniture from outside suppliers to fulfill customer orders.
First, Inventory Control prepares a purchase requisition when inventory approaches the reorder point and sends it to Purchasing and Accounts Payable. Then, Purchasing locates the authorized vendor in the vendor file, prepares a purchase order, and updates the purchase order file. Purchasing then sends the purchase order to Vendor, Receiving, and Accounts Payable. Accounts Payable prepares a summary of all purchase orders issued that day and forwards the total to General Ledger for posting to the GL file. Goods arrive at Receiving with a packing slip. Receiving prepares a receiving report and forwards it with the goods to…
arrow_forward
Silver Limited is a manufacturing company that produces furniture. To improve efficiency and usefulness, Silver Limited is constantly incorporating advanced, information technology into its business information systems. When Silver Limited does not have available production capacity, sometimes it purchases furniture from outside suppliers to fulfill customer orders.
First, Inventory Control prepares a purchase requisition when inventory approaches the reorder point and sends it to Purchasing and Accounts Payable. Then, Purchasing locates the authorized vendor in the vendor file, prepares a purchase order, and updates the purchase order file. Purchasing then sends the purchase order to Vendor, Receiving, and Accounts Payable. Accounts Payable prepares a summary of all purchase orders issued that day andforwards the total to the General Ledger for posting to the GL file. Goods arrive at Receiving with a packing slip. Receiving prepares a receiving report and forwards it with the goods to…
arrow_forward
Silver Limited is a manufacturing company that produces furniture. To improve efficiency and usefulness, Silver Limited is constantly incorporating advanced, information technology into its business information systems. When Silver Limited does not have available production capacity, sometimes it purchases furniture from outside suppliers to fulfill customer orders.
First, Inventory Control prepares a purchase requisition when inventory approaches the reorder point and sends it to Purchasing and Accounts Payable. Then, Purchasing locates the authorized vendor in the vendor file, prepares a purchase order, and updates the purchase order file. Purchasing then sends the purchase order to Vendor, Receiving, and Accounts Payable. Accounts Payable prepares a summary of all purchase orders issued that day and forwards the total to General Ledger for posting to the GL file. Goods arrive at Receiving with a packing slip. Receiving prepares a receiving report and forwards it with the goods to…
arrow_forward
Silver Limited is a manufacturing company that produces furniture. To improve efficiency and usefulness, Silver Limited is constantly incorporating advanced, information technology into its business information systems. When Silver Limited does not have available production capacity, sometimes it purchases furniture from outside suppliers to fulfill customer orders.
First, Inventory Control prepares a purchase requisition when inventory approaches the reorder point and sends it to Purchasing and Accounts Payable. Then, Purchasing locates the authorized vendor in the vendor file, prepares a purchase order, and updates the purchase order file. Purchasing then sends the purchase order to Vendor, Receiving, and Accounts Payable. Accounts Payable prepares a summary of all purchase orders issued that day andforwards the total to the General Ledger for posting to the GL file. Goods arrive at Receiving with a packing slip. Receiving prepares a receiving report and forwards it with the goods to…
arrow_forward
Silver Limited is a manufacturing company that produces furniture. To improve efficiency and usefulness, Silver Limited is constantly incorporating advanced, information technology into its business information systems. When Silver Limited does not have available production capacity, sometimes it purchases furniture from outside suppliers to fulfill customer orders.
First, Inventory Control prepares a purchase requisition when inventory approaches the reorder point and sends it to Purchasing and Accounts Payable. Then, Purchasing locates the authorized vendor in the vendor file, prepares a purchase order, and updates the purchase order file. Purchasing then sends the purchase order to Vendor, Receiving, and Accounts Payable. Accounts Payable prepares a summary of all purchase orders issued that day and forwards the total to General Ledger for posting to the GL file. Goods arrive at Receiving with a packing slip. Receiving prepares a receiving report and forwards it with the goods to…
arrow_forward
ABC Company is a manufacturing company that produces furniture. To improve efficiency and usefulness, ABC Company is constantly incorporating advanced, information technology into its business information systems. When Silver Limited does not have available production capacity, sometimes it purchases furniture from outside suppliers to fulfill customer orders.
First, Inventory Control prepares a purchase requisition when inventory approaches the reorder point and sends it to Purchasing and Accounts Payable. Then, Purchasing locates the authorized vendor in the vendor file, prepares a purchase order, and updates the purchase order file. Purchasing then sends the purchase order to Vendor, Receiving, and Accounts Payable. Accounts Payable prepares a summary of all purchase orders issued that day and forwards the total to General Ledger for posting to the GL file. Goods arrive at Receiving with a packing slip. Receiving prepares a receiving report and forwards it with the goods to…
arrow_forward
Sears Roebuck, the most well-known and oldest mail-order retailer in the country, discontinued its mail-order operations in 1993. Other mail-order marketers are using information systems to trim printing and postage costs of their catalogs. They also want to more effectively target their customers. Explain how an appropriately designed coding system for inventory items, incorporated in a relational database system with SQL capabilities, could allow more cost-efficient and effective mail-order operations. Sketch the necessary database table structure.
arrow_forward
An analysis of selling costs shows: (You may select more than one answer. Single click the box with the question mark to produce a check mark for a
correct answer and double click the box with the question mark to empty the box for a wrong answer. Any boxes left with a question mark will be
automatically graded as incorrect.)
| Management may want to consider offering discounts for large orders.
| Small orders are preferable to medium sized orders.
O Large orders are preferable to medium sized orders.
O Marketing should be focused on small sized orders.
arrow_forward
Firms keep supplies of inventory for which of the following reasons?
To provide a feeling of security for the workforce
To maintain dependence of operations
To meet variation in product demand
arrow_forward
Pretoria - The Gauteng department of economic development, through the Gauteng office of consumer affairs,
has warned suppliers not to inflate prices of essential items, amidst reports of food shortages following the
widespread riots and vandalism.
Which of the following will NOT change the supply of a good produced?
OA. A change in the cost of labour of that good produced.
OB. Looting due to civil unrest.
OC. An improvement in the technology used to produce that good.
OD. A change in the consumers income.
arrow_forward
What are some basics to consider when opening a parts store to improve efficiency??
arrow_forward
An on-line merchandiser analyzes demographic data to identify the states with the highest birth rates to determine which regional fulfillment centers should store the most diapers and baby formula. This is an
example of
Select one:
a. factory automation.
b. predictive analytics.
c. customer profitability analysis.
d. sustainability.
arrow_forward
SEE MORE QUESTIONS
Recommended textbooks for you
Principles of Accounting Volume 1
Accounting
ISBN:9781947172685
Author:OpenStax
Publisher:OpenStax College
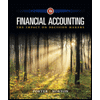
Financial Accounting: The Impact on Decision Make...
Accounting
ISBN:9781305654174
Author:Gary A. Porter, Curtis L. Norton
Publisher:Cengage Learning
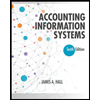
Accounting Information Systems
Accounting
ISBN:9781337619202
Author:Hall, James A.
Publisher:Cengage Learning,
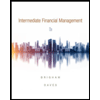
Intermediate Financial Management (MindTap Course...
Finance
ISBN:9781337395083
Author:Eugene F. Brigham, Phillip R. Daves
Publisher:Cengage Learning
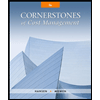
Cornerstones of Cost Management (Cornerstones Ser...
Accounting
ISBN:9781305970663
Author:Don R. Hansen, Maryanne M. Mowen
Publisher:Cengage Learning
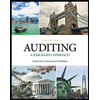
Auditing: A Risk Based-Approach (MindTap Course L...
Accounting
ISBN:9781337619455
Author:Karla M Johnstone, Audrey A. Gramling, Larry E. Rittenberg
Publisher:Cengage Learning
Related Questions
- 1. Explain which of the conversion methods would be suitable for the following. Justify your choice: Upgrading the software for an Automatic Banking Machine (ABM/ATM) Adding a new inventory system along with new computerized cash registers in a supermarket Implementing a student course management system in a university 2. List four reasons why your participation as a user of an information system is critical during the systems development life cycle, linking the concepts of user involvement and change management in a software implementation project. 3. Why is it so important to understand how a business process works when trying to develop a new information system? TASK B: In the context of the impact of a change on an organization, How would you characterize the following changes? Adding electronic scoreboards to a cricket grounds. A Telco consolidating call centres in one country. A Telco installing fibre-to-the-home to replace copper wires. A Telco launching a TV service.arrow_forward1. What is the major advantage of using a perpetual inventory system? a. It provides efficient internal control over materials. b. It avoids inventory shortages and overages. c. It avoids losses due to theft. d. It minimizes error in posting receipts and issues of materials. 2. If the 300 defective bolts(normal spoilage) were repaired and management wanted to be sure the incremental costs did not exceed the cost of producing new units, how would the rework costs be accounted for: a. Charged to overhead and spread over the costs of all products. b. Expensed as extraordinary. c. Charged to those belts repaired. d. As normal materials, labor and overhead.arrow_forwardWhich of the following is the best description of the operating cycle? Multiple Choice The length of time that it takes to convert raw materials into inventory The length of time that it takes to convert raw materials into accounts receivable The length of time to acquire raw materials and receive payment for them when sold None of the optionsarrow_forward
- How can you provide recommendations to improve efficiency in a parts store?arrow_forwardSilver Limited is a manufacturing company that produces furniture. To improve efficiency and usefulness, Silver Limited is constantly incorporating advanced, information technology into its business information systems. When Silver Limited does not have available production capacity, sometimes it purchases furniture from outside suppliers to fulfill customer orders. First, Inventory Control prepares a purchase requisition when inventory approaches the reorder point and sends it to Purchasing and Accounts Payable. Then, Purchasing locates the authorized vendor in the vendor file, prepares a purchase order, and updates the purchase order file. Purchasing then sends the purchase order to Vendor, Receiving, and Accounts Payable. Accounts Payable prepares a summary of all purchase orders issued that day and forwards the total to General Ledger for posting to the GL file. Goods arrive at Receiving with a packing slip. Receiving prepares a receiving report and forwards it with the goods to…arrow_forwardSilver Limited is a manufacturing company that produces furniture. To improve efficiency and usefulness, Silver Limited is constantly incorporating advanced, information technology into its business information systems. When Silver Limited does not have available production capacity, sometimes it purchases furniture from outside suppliers to fulfill customer orders. First, Inventory Control prepares a purchase requisition when inventory approaches the reorder point and sends it to Purchasing and Accounts Payable. Then, Purchasing locates the authorized vendor in the vendor file, prepares a purchase order, and updates the purchase order file. Purchasing then sends the purchase order to Vendor, Receiving, and Accounts Payable. Accounts Payable prepares a summary of all purchase orders issued that day andforwards the total to the General Ledger for posting to the GL file. Goods arrive at Receiving with a packing slip. Receiving prepares a receiving report and forwards it with the goods to…arrow_forward
- Silver Limited is a manufacturing company that produces furniture. To improve efficiency and usefulness, Silver Limited is constantly incorporating advanced, information technology into its business information systems. When Silver Limited does not have available production capacity, sometimes it purchases furniture from outside suppliers to fulfill customer orders. First, Inventory Control prepares a purchase requisition when inventory approaches the reorder point and sends it to Purchasing and Accounts Payable. Then, Purchasing locates the authorized vendor in the vendor file, prepares a purchase order, and updates the purchase order file. Purchasing then sends the purchase order to Vendor, Receiving, and Accounts Payable. Accounts Payable prepares a summary of all purchase orders issued that day and forwards the total to General Ledger for posting to the GL file. Goods arrive at Receiving with a packing slip. Receiving prepares a receiving report and forwards it with the goods to…arrow_forwardSilver Limited is a manufacturing company that produces furniture. To improve efficiency and usefulness, Silver Limited is constantly incorporating advanced, information technology into its business information systems. When Silver Limited does not have available production capacity, sometimes it purchases furniture from outside suppliers to fulfill customer orders. First, Inventory Control prepares a purchase requisition when inventory approaches the reorder point and sends it to Purchasing and Accounts Payable. Then, Purchasing locates the authorized vendor in the vendor file, prepares a purchase order, and updates the purchase order file. Purchasing then sends the purchase order to Vendor, Receiving, and Accounts Payable. Accounts Payable prepares a summary of all purchase orders issued that day andforwards the total to the General Ledger for posting to the GL file. Goods arrive at Receiving with a packing slip. Receiving prepares a receiving report and forwards it with the goods to…arrow_forwardSilver Limited is a manufacturing company that produces furniture. To improve efficiency and usefulness, Silver Limited is constantly incorporating advanced, information technology into its business information systems. When Silver Limited does not have available production capacity, sometimes it purchases furniture from outside suppliers to fulfill customer orders. First, Inventory Control prepares a purchase requisition when inventory approaches the reorder point and sends it to Purchasing and Accounts Payable. Then, Purchasing locates the authorized vendor in the vendor file, prepares a purchase order, and updates the purchase order file. Purchasing then sends the purchase order to Vendor, Receiving, and Accounts Payable. Accounts Payable prepares a summary of all purchase orders issued that day and forwards the total to General Ledger for posting to the GL file. Goods arrive at Receiving with a packing slip. Receiving prepares a receiving report and forwards it with the goods to…arrow_forward
- ABC Company is a manufacturing company that produces furniture. To improve efficiency and usefulness, ABC Company is constantly incorporating advanced, information technology into its business information systems. When Silver Limited does not have available production capacity, sometimes it purchases furniture from outside suppliers to fulfill customer orders. First, Inventory Control prepares a purchase requisition when inventory approaches the reorder point and sends it to Purchasing and Accounts Payable. Then, Purchasing locates the authorized vendor in the vendor file, prepares a purchase order, and updates the purchase order file. Purchasing then sends the purchase order to Vendor, Receiving, and Accounts Payable. Accounts Payable prepares a summary of all purchase orders issued that day and forwards the total to General Ledger for posting to the GL file. Goods arrive at Receiving with a packing slip. Receiving prepares a receiving report and forwards it with the goods to…arrow_forwardSears Roebuck, the most well-known and oldest mail-order retailer in the country, discontinued its mail-order operations in 1993. Other mail-order marketers are using information systems to trim printing and postage costs of their catalogs. They also want to more effectively target their customers. Explain how an appropriately designed coding system for inventory items, incorporated in a relational database system with SQL capabilities, could allow more cost-efficient and effective mail-order operations. Sketch the necessary database table structure.arrow_forwardAn analysis of selling costs shows: (You may select more than one answer. Single click the box with the question mark to produce a check mark for a correct answer and double click the box with the question mark to empty the box for a wrong answer. Any boxes left with a question mark will be automatically graded as incorrect.) | Management may want to consider offering discounts for large orders. | Small orders are preferable to medium sized orders. O Large orders are preferable to medium sized orders. O Marketing should be focused on small sized orders.arrow_forward
arrow_back_ios
SEE MORE QUESTIONS
arrow_forward_ios
Recommended textbooks for you
- Principles of Accounting Volume 1AccountingISBN:9781947172685Author:OpenStaxPublisher:OpenStax CollegeFinancial Accounting: The Impact on Decision Make...AccountingISBN:9781305654174Author:Gary A. Porter, Curtis L. NortonPublisher:Cengage LearningAccounting Information SystemsAccountingISBN:9781337619202Author:Hall, James A.Publisher:Cengage Learning,
- Intermediate Financial Management (MindTap Course...FinanceISBN:9781337395083Author:Eugene F. Brigham, Phillip R. DavesPublisher:Cengage LearningCornerstones of Cost Management (Cornerstones Ser...AccountingISBN:9781305970663Author:Don R. Hansen, Maryanne M. MowenPublisher:Cengage LearningAuditing: A Risk Based-Approach (MindTap Course L...AccountingISBN:9781337619455Author:Karla M Johnstone, Audrey A. Gramling, Larry E. RittenbergPublisher:Cengage Learning
Principles of Accounting Volume 1
Accounting
ISBN:9781947172685
Author:OpenStax
Publisher:OpenStax College
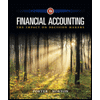
Financial Accounting: The Impact on Decision Make...
Accounting
ISBN:9781305654174
Author:Gary A. Porter, Curtis L. Norton
Publisher:Cengage Learning
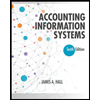
Accounting Information Systems
Accounting
ISBN:9781337619202
Author:Hall, James A.
Publisher:Cengage Learning,
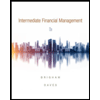
Intermediate Financial Management (MindTap Course...
Finance
ISBN:9781337395083
Author:Eugene F. Brigham, Phillip R. Daves
Publisher:Cengage Learning
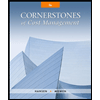
Cornerstones of Cost Management (Cornerstones Ser...
Accounting
ISBN:9781305970663
Author:Don R. Hansen, Maryanne M. Mowen
Publisher:Cengage Learning
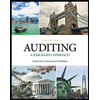
Auditing: A Risk Based-Approach (MindTap Course L...
Accounting
ISBN:9781337619455
Author:Karla M Johnstone, Audrey A. Gramling, Larry E. Rittenberg
Publisher:Cengage Learning