ChE201 HW6
docx
School
University of North Dakota *
*We aren’t endorsed by this school
Course
201
Subject
Chemistry
Date
Apr 3, 2024
Type
docx
Pages
7
Uploaded by DoctorDragonflyMaster198
Mullis, Ashton Rayne
Professor Bowman
ChE-201 Fundementals
20240304
HW6
1) The attached drawing 01-A-004/1 is a process flow diagram (PFD) for one small section of a
much larger butane isomerization plant. PFDs are normally printed on 11”x17” sheets of
paper. For this problem we will focus on a mass balance around the first isobutane reactor
R201, where n-butane is converted into isobutane, along with some C1-C3 side products.
a) What is the fractional conversion of n-butane to isobutane?
b) What is the fractional conversion of butanes (n-butane and isobutane) to C1-C3?
c) What other process units would you suggest be included in the plant to increase the
overall conversion?
Solutions
(A)
f
i
=
n
i
Reacted
n
i
Fed
= 520000
−
230000
520000
lb
hr
=
0.56
n
−
butane
(B) in – out / total out f
i
=
(
520000
+
12000
)
−(
230000
+
300000
)
(
230000
+
300000
)
=
0.0038
butanes
c1-c3
(C.) The conversion between A-B is very low, so assuming there is buildup of excess reactant in the system, it would be best to add a separator to remove the reacted product from the excess, and then send the excess stream back via a recycle stream or purge stream, depending on the purity of the recyclable.
2) Solid calcium fluoride (CaF2) reacts with sulfuric acid to form solid calcium sulfate and
gaseous hydrogen fluoride (HF). The HF is then dissolved in water to form hydrofluoric acid.
A source of calcium fluoride is fluorite ore containing 96.0 wt% CaF2 and 4.0% SiO2. In a
typical hydrofluoric acid manufacturing process, fluorite ore is reacted with 93 wt% aqueous
sulfuric acid, supplied 15% in excess of the stoichiometric amount. Ninety-five percent of the
ore dissolves in the acid. Some of the HF formed reacts with the dissolved silica in the
reaction
6HF+SiO2(aq)→H2SiF6(s)+2H2O(l)
The hydrogen fluoride exiting from the reactor is subsequently dissolved in enough water to produce 60.0 wt% hydrofluoric acid. a) Draw and label a flow diagram for this process b) Calculate the quantity of fluorite ore needed to produce a metric ton of aqueous
hydrofluoric acid. (Some of the given data are not needed to solve the problem)
Solutions
(A) (B) Basis 0f 100kg Ore Inlet stream 6 mols of HF = 600kg=6E5g required for reaction.
Fluorine, 18.998 amu
HF, 20.01 g/mol
60%
wt HF ratio needed for reaction
=
600
kg×
1000
g
1
kg
÷
20.01
g
mol
=
3
×
10
4
n HF
96%
wt Ca F
2
=
9.6E5
gCa F
2
×
(
20.01
×
2
nF
)
78.07
gmol
−
1
Ca F
2
=
4.92E5
g×
0.95
=
4.68E5
g÷
18.998
Famu
=
2.46E4
n
F
1
T
ore
Basis Silica 1.0 – 0.60HF = 40%wt silica Silica, 60.08 g/mol
4E4
gSilica
60.08
gmo l
−
1
silica
=
6.7E2
nsilica
∈
mixture×
6
nratioS
:
F
=
4.00E3
n F excess
2.46E4nF – 4.00E3nF = 2.06E4n HF 3.00E4
nHF
2.06E4
nHF
=
1.46
MT = 1460kg
3) A catalytic reactor is used to produce formaldehyde from methanol in the reaction,
CH3OH→HCHO+H2
A single-pass conversion of 60.0% is achieved in the reactor. The methanol in the reactor
product is separated from the formaldehyde and hydrogen in a multiple-unit process. The
production rate of formaldehyde is 720. kg/h.
a) Calculate the required feed rate of methanol to the process (kmol/h) if there is no recycle.
b) Suppose the unreacted methanol is recovered and recycled to the reactor and the single-
pass conversion remains 60%. Determine the required fresh feed rate of methanol (kmol/h) and the rates (kmol/h) at which methanol enters and leaves the reactor.
c) The single-pass conversion in the reactor, Xsp, affects the costs of the reactor (Cr) and the
separation process and recycle line (Cs). What effect would you expect an increased Xsp would have on each of these costs for a fixed formaldehyde production rate?
(Hint: To get a 100% single-pass conversion you would need an infinitely large reactor, and
lowering the single-pass conversion leads to a need to process greater amounts of fluid through both process units and the recycle line.) What would you expect a plot of (Cr+Cs) versus Xsp to look like? What does the design specification Xsp=60% probably
represent?
Solutions
(A)
Your preview ends here
Eager to read complete document? Join bartleby learn and gain access to the full version
- Access to all documents
- Unlimited textbook solutions
- 24/7 expert homework help
˙
n
=
750
kg
hr
×
1
kmol
30.031
gmo l
−
1
formaldehyde
=
25.0
kmol
hr
formaldehyde
Given
:60%
methanol conversionrate
MethanolConverstion
−
Feed Rate Required
=
˙
n
1
=
25.0
=
60
100
=
25.0
×
100
60
=
41.7
kmol
hr
methanol
(B) Methanol Feed, Input Stream
Fresh Feed Rate into Reactor is 1methanol :1 formaldehyde in=out ,25 kmol/hr.
Fresh Conversion Rate, 25
25
n
1
+
n
3
=
0.60
…n
3
=
16.
6
out
(C.) An increase in XSP reactor size would inherently increase the cost since a new larger reactor will be required. However, since the reactor is producing a product of methanol at a higher production rate it would save costs of having to install (or make use of decreases if one exists already) a recycle stream and separator into the system, which would also increase energy costs of the system overall. Assuming the system is at a decreasing conversion and then the overall conversion rate is
increased due to the addition of a larger reactor or recycle stream, then the production would begin to increase, translation to y
=
x
2
, thus it would be a parabola with concavity being positive. 4) One process for the production of methanol is the catalytic reaction of carbon dioxide and
hydrogen. The chemical reaction is given by:
C O
2
+
3
H
2
→C H
3
OH
+
H
2
O
The diagram for the process is shown below. It is desired to produce 1000 mol/hr of methanol. The single pass conversion of the reactor is 10% while the overall conversion is 80% (both in terms of hydrogen). Note, carbon dioxide in the fresh feed is in 20% excess and all of the product (methanol) and byproduct (water) is removed in the condenser. a) Why is the recycle stream included in the design? b) What is the purpose of the purge stream? In other words, why would this design not
work without the purge stream? c) List two reasons (with supporting explanation) why the single pass conversion might be
so low.
d) Determine the flow rate and composition of the feed stream (F). e) Determine the flow rate and composition of the purge stream (P). f) What percentage of the flow leaving the condenser enters the purge stream? g) Determine the recycle ratio (R/F).
Solutions
(A)
Since the conversion rate is not to completion on the first pass through, the raw materials are refed back into the process. The purpose of a recycle stream is to reuse reactants, to save costs on fresh feed materials.
(B) The purge stream makes this process a steady-state system, since there is accumulation of
unprocessed, the purge stream prevents this process from becoming a semi-batch process. (Maintaining reaction equilibrium) (C.) 1. Perhaps the molar ratio of feed reactants and recycle stream is not correct, too much or too little could cause a smaller conversion rate of desired product.
2. Perhaps the systems temperature needs to be adjusted to meet the activation energy requirements of solution.
(D) F = 5250 mol/hr Fa= 3750 mol/hr
Fb= 1500 mol/hr
(E.) P= 1250 mol/hr
Pq= 500 mol/hr
Pp= 750 mol/hr
(F) P/Cin 1250
mol
hr
44000
mol
hr
×
100
=
2.84%
(G) R/F
Your preview ends here
Eager to read complete document? Join bartleby learn and gain access to the full version
- Access to all documents
- Unlimited textbook solutions
- 24/7 expert homework help
43750
5250
mol
/
hr
=
8.
3
%
Related Questions
15)
arrow_forward
2. Consider a gas-phase reaction:
A + 2B → C
that takes place in a packed-bed reactor (PBR) with a catalyst
volume of 0.2 L. The feed rate of A is 0.1 mol/s and the feed rate of
B is 0.2 mol/s. The reaction rate constant is 0.01 L/(mol*s) and the
pressure drop across the catalyst bed is 2 bar. What is the conversion
of A at the exit of the reactor?
arrow_forward
Mhlo
arrow_forward
PREV
1
2
3
NEXT
Based on your ICE table (Part 1) and the definition of Kb, set up the expression for Kb in
order to determine the unknown. Each reaction participant must be represented by one
tile. Do not combine terms.
Kb =
[0]
[0.50]
(x)
[x +4.20]
[x - 4.20]
[x+6.3 x 10
< PREV
1
[2x]
=
3.8 × 10-10
RESET
[4.20]
[6.3 x 10-5]
[1.6 × 10-19]
[3.8 × 10-19]
[x-6.3 x 10] [x+1.6 × 10-9] [x-1.6 x 10-19 [x+3.8 x 10-9] [x-3.8 x 10-19
2
3
Based on your ICE table (Part 1) and the equilibrium expression for Kb (Part 2),
determine the original concentration of C6H5NH3+.
[C6H5NH3+]
=
M
RESET
0
8.3 × 1010
0.86
1.2
10
2.1
0.50
arrow_forward
on 1:
2A
The gas phase decomposition (k = 0.001 s) is carried out in a plug flow reactor at 300°C and 10 atm. Reactor
feed rate of A is 2 mol/s, and contains 75 mol% inert. Determine the length of 0.0254 m diameter pipe needed
to reach 99% conversion.
Question 2:
A+2B
C+D
2028.616
The liquid-phase reaction is first order in both A and B with k=0.0017m³/mol.min at 461°K with
E-11273Cal/mol. The initial entering concentrations of A and B are 1.8 mol/m³ and 6.6mol/m³, respectively.
What is the rate of reaction (X=90) at 298°K?
Question 3:
For The following reaction
A-1.2611X10-5
Calculate the equilibrium conversion and concentration for the gas phase reaction
A+B
2C
The reaction carried out in a flow reactor with no pressure drop. the feed is equal molar which is 3 at
a temperature of 400 K and 10 atm. At this temperature, Kc= 8(dm³/mol)².
Question 4:
PA+B C + 2D
ll in the following table for CB and X.assuming as a liquid phase & initial concentration of CA-1N
CA
1
CB
0.15
X
0.9
0.8
0.7…
arrow_forward
Dear Bartleby, please help me.Do not use any software and please show complete steps for part b
arrow_forward
Analyze the following reaction mechanism:
1. H2O2 → H2O + O
2. O + CF2CI2 → CIO + CF2CI
3. CIO + O3 → CI + 202
4. Cl + CF2CI → CF2CI2
From the mechanism provided, write the overall balanced
equation for this chemical reaction. Ignore phases.
4-
2.
2+
3+
4+
1
2
3
4
6
8
04
O6
Do
1
3
8.
(s)
(1)
(g)|(aq)
+
F
CI
H
C
Reset
• x H2O || Delete
3.
arrow_forward
The initial reaction rate for the elementary reactor
2A + В > 4C
was measured as a function of temperature when the concentration of A was 2M and that
B was 1.5 M
-rA
(mol/dm³.s)
0.002
0.046
0.72
8.33
Т (К)
300
320
340
360
a) Calculate the activation energy
b) Calculate the frequency factor
c) Calculate the rate constant as a function of temperature using T=300 Kas the
base case
arrow_forward
The following irreversible reaction takes place in a batch reactor? → B
Consider the same reaction, first-order irreversible reaction with respect to A. The concentration of A after one minute is 2 mol dm-3. If k is the same (k = 1 min-1), determine the initial concentration of A.
arrow_forward
What is m and n
arrow_forward
#10-4-4 thanks
arrow_forward
With all details
arrow_forward
Use the energy diagram to state if the reactor favors the formation of products or reactants and explain the expected size of the equilibrium constant.
arrow_forward
Based on your ICE table (Part 2) and the definition of Ka, set up the expression for Ka in
order to determine the unknown. Each reaction participant must be represented by one
tile. Do not combine terms.
Ka =
2.9 × 10-8
RESET
[0]
(0.13]
[0.37]
(0.010]
[0.040]
[0.10]
[0.40]
[x]
[2x]
[0.13 + x)
[0.13-x]
[0.010+x]
[0.010-x]
[0.040 + x] [0.040 - x]
[0.10+x]
[0.10-x]
[0.40+x]
[0.40-x]
PREV
2
Based on your ICE table (Part 2) and the equilibrium expression for Ka (Part 3),
determine the pH of solution.
pH =
RESET
0
7.3 × 10*
5.86
18.74
1.4 × 10+
0.13
8.14
0.89
arrow_forward
2:18
1
4
7
+/-
Question 1 of 12
Consider the radioisotope 235U
(half life = 7.04 × 108 years). What
is the first order rate constant for
235U?
2
5
8
| 1/years
3
60
9
O
Submit
Tap here or pull up for additional resources
XU
x 100
arrow_forward
Run
Reactants
Temperature (Celsius)
Initial Rate (kPa/s)
1
10 ml 3% H2O2 = 5ml 0.5M KI
23.0
0.0798
2
5ml 3% H2O2 = 5ml 0.5 M KI
23.0
0.0391
3
5ml 3% H2O2 + 10ml 0.5 M KI
23.0
0.0794
Run
Initial Rate (mol/L*s)
[H2O2] after mixing
[I-] after mixing
1
3.24 x 10^-5
0.147 M
0.0417 M
2
1.59 x 10^-5
0.0733 M
0.417 M
3
3.23 x 10^-5
0.0733 M
0.0833 M
Calculate the rate law for the reaction
arrow_forward
9
arrow_forward
2. The following laboratory data were collected in a batch adsorption
study. Plot the data according to Freundlich Isotherm and determine
the values for the constants n and KF. A volume of 500 mL is placed
in each flask, and the waste has an initial COD of 100 mg/L.
Flask No Mass of C (mg) Volume Flask (mL) Final COD (mg/L)
965
740
548
398
265
168
500
500
500
500
500
500
500
3.5
5.2
12.5
20.5
33
100
arrow_forward
Question 7
For numbers 7 to 8:
For the kinetics ABC, each step being first-order, for reaction
occurring in a constant-volume batch reactor (only A present initially).
Calculate k₁ tmax for each of the cases:
K = K₂/k₁ = 10
1.00
0.30
0.25
NOTG
O 0.42
arrow_forward
pls help asap
arrow_forward
A + B -> C
what is m and n?
arrow_forward
Decomposition of H202 Data (1) - Word
Search
Design
Layout
References
Mailings
Review
View
Developer
Help
12 A A Aa
、 |A|三▼三▼i、|EE|2↓T
Po
lal
AaBbCcD AABBCCD AaBbC AABBCCC Aa
I U - ab x, x A A-
|■===|=。12-田
T No Spac.. Heading 1
T Normal
Heading 2
Titl
Font
Paragraph
Styles
Chemical equation used:
2 Mn04 + 5 H2O2 + 6 H* →2 Mn2+ + 5 02 + 8 H2O
[MnO4] = 0.0090 M
Volume H2O2 used: 1.0 mL
Volume H2S04 used: 7.0 mL
Trial 1: 41.9 mL MnO4 used
Trial 2: 40.4 mL used
Trial 3: 40.01 mL used
Remember you want to find the M (mol/L) of H2O2. You must use stoichiometry to find
moles of H2O2 and the volume of hydrogen peroxide used to get liters. Calculate the
concentration for each trial and average the results.
Thar nocho mictrv
arrow_forward
In a batch reactor, reactant A is steadily converted into product B. The initialconcentration of reactant A is 100 mg/L. During a 10-hour reaction course, it wasobserved that the concentration of A in the reactor decreased at a constant rate of 10mg/L per hour. Based on the result, you can determine that the transformation reactionA→B follows ( ) with respect to reactant A.
arrow_forward
I need help with this problem. I want to see detailed steps.
arrow_forward
SEE MORE QUESTIONS
Recommended textbooks for you
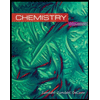
Chemistry
Chemistry
ISBN:9781305957404
Author:Steven S. Zumdahl, Susan A. Zumdahl, Donald J. DeCoste
Publisher:Cengage Learning
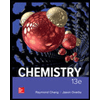
Chemistry
Chemistry
ISBN:9781259911156
Author:Raymond Chang Dr., Jason Overby Professor
Publisher:McGraw-Hill Education
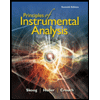
Principles of Instrumental Analysis
Chemistry
ISBN:9781305577213
Author:Douglas A. Skoog, F. James Holler, Stanley R. Crouch
Publisher:Cengage Learning
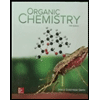
Organic Chemistry
Chemistry
ISBN:9780078021558
Author:Janice Gorzynski Smith Dr.
Publisher:McGraw-Hill Education
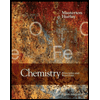
Chemistry: Principles and Reactions
Chemistry
ISBN:9781305079373
Author:William L. Masterton, Cecile N. Hurley
Publisher:Cengage Learning
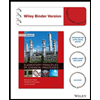
Elementary Principles of Chemical Processes, Bind...
Chemistry
ISBN:9781118431221
Author:Richard M. Felder, Ronald W. Rousseau, Lisa G. Bullard
Publisher:WILEY
Related Questions
- 15)arrow_forward2. Consider a gas-phase reaction: A + 2B → C that takes place in a packed-bed reactor (PBR) with a catalyst volume of 0.2 L. The feed rate of A is 0.1 mol/s and the feed rate of B is 0.2 mol/s. The reaction rate constant is 0.01 L/(mol*s) and the pressure drop across the catalyst bed is 2 bar. What is the conversion of A at the exit of the reactor?arrow_forwardMhloarrow_forward
- PREV 1 2 3 NEXT Based on your ICE table (Part 1) and the definition of Kb, set up the expression for Kb in order to determine the unknown. Each reaction participant must be represented by one tile. Do not combine terms. Kb = [0] [0.50] (x) [x +4.20] [x - 4.20] [x+6.3 x 10 < PREV 1 [2x] = 3.8 × 10-10 RESET [4.20] [6.3 x 10-5] [1.6 × 10-19] [3.8 × 10-19] [x-6.3 x 10] [x+1.6 × 10-9] [x-1.6 x 10-19 [x+3.8 x 10-9] [x-3.8 x 10-19 2 3 Based on your ICE table (Part 1) and the equilibrium expression for Kb (Part 2), determine the original concentration of C6H5NH3+. [C6H5NH3+] = M RESET 0 8.3 × 1010 0.86 1.2 10 2.1 0.50arrow_forwardon 1: 2A The gas phase decomposition (k = 0.001 s) is carried out in a plug flow reactor at 300°C and 10 atm. Reactor feed rate of A is 2 mol/s, and contains 75 mol% inert. Determine the length of 0.0254 m diameter pipe needed to reach 99% conversion. Question 2: A+2B C+D 2028.616 The liquid-phase reaction is first order in both A and B with k=0.0017m³/mol.min at 461°K with E-11273Cal/mol. The initial entering concentrations of A and B are 1.8 mol/m³ and 6.6mol/m³, respectively. What is the rate of reaction (X=90) at 298°K? Question 3: For The following reaction A-1.2611X10-5 Calculate the equilibrium conversion and concentration for the gas phase reaction A+B 2C The reaction carried out in a flow reactor with no pressure drop. the feed is equal molar which is 3 at a temperature of 400 K and 10 atm. At this temperature, Kc= 8(dm³/mol)². Question 4: PA+B C + 2D ll in the following table for CB and X.assuming as a liquid phase & initial concentration of CA-1N CA 1 CB 0.15 X 0.9 0.8 0.7…arrow_forwardDear Bartleby, please help me.Do not use any software and please show complete steps for part barrow_forward
- Analyze the following reaction mechanism: 1. H2O2 → H2O + O 2. O + CF2CI2 → CIO + CF2CI 3. CIO + O3 → CI + 202 4. Cl + CF2CI → CF2CI2 From the mechanism provided, write the overall balanced equation for this chemical reaction. Ignore phases. 4- 2. 2+ 3+ 4+ 1 2 3 4 6 8 04 O6 Do 1 3 8. (s) (1) (g)|(aq) + F CI H C Reset • x H2O || Delete 3.arrow_forwardThe initial reaction rate for the elementary reactor 2A + В > 4C was measured as a function of temperature when the concentration of A was 2M and that B was 1.5 M -rA (mol/dm³.s) 0.002 0.046 0.72 8.33 Т (К) 300 320 340 360 a) Calculate the activation energy b) Calculate the frequency factor c) Calculate the rate constant as a function of temperature using T=300 Kas the base casearrow_forwardThe following irreversible reaction takes place in a batch reactor? → B Consider the same reaction, first-order irreversible reaction with respect to A. The concentration of A after one minute is 2 mol dm-3. If k is the same (k = 1 min-1), determine the initial concentration of A.arrow_forward
arrow_back_ios
SEE MORE QUESTIONS
arrow_forward_ios
Recommended textbooks for you
- ChemistryChemistryISBN:9781305957404Author:Steven S. Zumdahl, Susan A. Zumdahl, Donald J. DeCostePublisher:Cengage LearningChemistryChemistryISBN:9781259911156Author:Raymond Chang Dr., Jason Overby ProfessorPublisher:McGraw-Hill EducationPrinciples of Instrumental AnalysisChemistryISBN:9781305577213Author:Douglas A. Skoog, F. James Holler, Stanley R. CrouchPublisher:Cengage Learning
- Organic ChemistryChemistryISBN:9780078021558Author:Janice Gorzynski Smith Dr.Publisher:McGraw-Hill EducationChemistry: Principles and ReactionsChemistryISBN:9781305079373Author:William L. Masterton, Cecile N. HurleyPublisher:Cengage LearningElementary Principles of Chemical Processes, Bind...ChemistryISBN:9781118431221Author:Richard M. Felder, Ronald W. Rousseau, Lisa G. BullardPublisher:WILEY
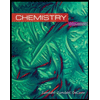
Chemistry
Chemistry
ISBN:9781305957404
Author:Steven S. Zumdahl, Susan A. Zumdahl, Donald J. DeCoste
Publisher:Cengage Learning
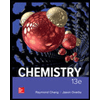
Chemistry
Chemistry
ISBN:9781259911156
Author:Raymond Chang Dr., Jason Overby Professor
Publisher:McGraw-Hill Education
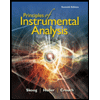
Principles of Instrumental Analysis
Chemistry
ISBN:9781305577213
Author:Douglas A. Skoog, F. James Holler, Stanley R. Crouch
Publisher:Cengage Learning
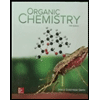
Organic Chemistry
Chemistry
ISBN:9780078021558
Author:Janice Gorzynski Smith Dr.
Publisher:McGraw-Hill Education
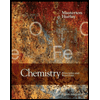
Chemistry: Principles and Reactions
Chemistry
ISBN:9781305079373
Author:William L. Masterton, Cecile N. Hurley
Publisher:Cengage Learning
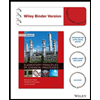
Elementary Principles of Chemical Processes, Bind...
Chemistry
ISBN:9781118431221
Author:Richard M. Felder, Ronald W. Rousseau, Lisa G. Bullard
Publisher:WILEY