Operations Management Test-1
.docx
keyboard_arrow_up
School
Confederation College *
*We aren’t endorsed by this school
Course
511
Subject
Economics
Date
Feb 20, 2024
Type
docx
Pages
5
Uploaded by SargentResolveRat28
1.
Aggregate planning in manufacturing ties organizational strategic goals to a production plan.
Ans.
True
2.
A small metal shop operates 10 hours each day, producing 100 parts/hour. If productivity were increased 20%, how many hours would the plant have to work to produce 1000 parts?
Ans. between 8 and 9 hours.
New production rate = 100 parts/hour + (20% * 100 parts/hour)
= 100 parts/hour + (0.20 * 100 parts/hour)
= 100 parts/hour + 20 parts/hour
= 120 parts/hour
Now, we can calculate the number of hours required to produce 1000 parts using the new production rate:
Number of hours = Total parts / Production rate
= 1000 parts / 120 parts/hour
= 8.33 hours
Since the metal shop operates for 10 hours each day, it would need to work between 8 and 9 hours to produce 1000 parts.
Therefore, the answer is option D. between 8 and 9 hours.
3.
The objective of aggregate planning is to meet demand while ________ over the planning period.
Ans.
minimizing cost
4.
Disaggregation is the process of breaking the aggregate plan into greater detail.
Ans.
True.
5.
Dependence on an external source of supply is found in which of the following aggregate planning strategies?
Ans.
Subcontracting
6.
Which of the following statements is true?
Ans.
The person most responsible for initiating use of interchangeable parts in manufacturing was Eli Whitney.
7.
Gibson Valves produces cast bronze valves on an assembly line, currently producing 1600 valves per shift. If the production is increased to 2000 valves per shift, labour productivity will increase by
Ans.
[(2000-1600)/1600 * 100] % = (0.25*100) % = 25%
8.
Which of the following are the primary functions of all organizations?
Ans.
marketing, production/operations, and finance/accounting
9.
Which of the following actions is consistent with the use of pure level strategy?
Ans.
use inventory to meet demand requirements.
10.
Osprey Machine Works has the following demand requirements and other data for the upcoming four quarters.
Quarter
Demand
Previous quarter's output
2500 units
1
2300
Beginning inventory
200 units
2
2400
Stockout (backorder) cost
$50 per unit
3
2600
Inventory holding cost
$10 per unit at
end of quarter
4
2100
Hiring workers
$4 per unit
Laying off workers
$8 per unit
Unit cost
$30 per unit
Overtime
$10 extra per unit
What is the total cost of pursuing a level aggregate plan over the coming year?
Ans.
11.
Aggregate planning occurs over the medium or intermediate future of 3 to 18 months.
Ans.
True
12.
The Dulac Box plant produces 500 cypress packing boxes in two 10-hour shifts. What is the productivity of the plant?
Ans.
25 boxes/hr
13.
Operation Management is the set of activities that creates value in the form of goods and services by transforming inputs into outputs.
Ans.
True
14.
What is the effort to plan the coordination of demand forecasts with functional areas of the firm and its supply chain?
Ans.
sales and operations planning
15.
The Dulac Box plant produces 500 cypress packing boxes in two 10-hour shifts. Due to higher demand, they have decided to operate three 8-hour shifts instead. They are now able to produce 600 boxes per day. What has happened to productivity?
Ans.
It has increased by 20%. (
[(600-500)/500]*100%
)
16.
Which of the following statements about aggregate planning is true?
Ans.
Aggregate planning uses the adjustable part of capacity to meet production requirements.
17.
The service sector has lower productivity improvements than the manufacturing sector because
Ans.
services usually are labour-intensive.
18.
Which of the following is the best example of a pure service.?
Ans.
Counselling
19.
Martin Manufacturing has implemented several programs to improve its productivity. They have asked you to evaluate the
firm's productivity by comparing this year's performance with last year's. The following data are available:
Last Year
This Year
Output
10,500 units
12,100 units
Labour Hours
12,000
13,200
Utilities
$7,600
$8,250
Capital
$83,000
$88,000
Has Martin Manufacturing improved its productivity during the past year?
Ans.
Output per labor hour:
Last Year: 10,500 units / 12,000 labor hours = 0.875 units per labor hour
This Year: 12,100 units / 13,200 labor hours = 0.916 units per labor hour
Output per dollar of capital:
Last Year: 10,500 units / $83,000 = 0.126 units per dollar of capital
This Year: 12,100 units / $88,000 = 0.138 units per dollar of capital
Yes
20.
Productivity in Canada has increased significantly every year since 1973.
Ans.
False
21.
Which of the following statements about aggregate planning is true?
Ans.
A pure chase strategy allows lower inventories when compared to pure level scheduling.
22.
A firm practices the pure chase strategy. Production last quarter was 1000. Demand over the next four quarters is estimated to be 900, 700, 1000, and 1000. Hiring cost is $20 per unit, and firing cost is $5 per unit. Over the next year, the sum of hiring and layoff costs will be
Ans.
$7500
Quarter 1:
Demand = 900
Output (last quarter) = 1000
Layoffs = Output (last quarter) - Demand = 1000 - 900 = 100 units
Layoff cost = Layoffs * Firing cost per unit = 100 * $5 = $500
Quarter 2:
Demand = 700
Output (last quarter) = 900 (after layoffs)
Layoffs = Output (last quarter) - Demand = 900 - 700 = 200 units
Layoff cost = Layoffs * Firing cost per unit = 200 * $5 = $1000
Quarter 3:
Demand = 1000
Output (last quarter) = 700 (after layoffs)
Hiring = Demand - Output (last quarter) = 1000 - 700 = 300 units
Hiring cost = Hiring * Hiring cost per unit = 300 * $20 = $6000
Quarter 4:
Demand = 1000
Output (last quarter) = 1000
No hiring or layoffs needed
Hiring cost = 0
Layoff cost = 0
Total sum of hiring and layoff costs over the next year:
Total cost = Sum of hiring costs + Sum of layoff costs
Total cost = $6000 + $500 + $1000 + $0 = $7500
Therefore, the sum of hiring and layoff costs over the next year, assuming the pure chase strategy, will be $7500.
23.
The _______ strategy maintains a constant output rate, or workforce level, over the planning horizon.
Ans.
Level Strategy
24.
Technology combined with rapid international communication of news, entertainment, and lifestyles is dramatically increasing the life span of products.
Ans.
False
25.
All organizations, including service firms such as banks and hospitals, have a production function.
Ans.
True
26.
_______ means designing green products and packaging that minimize resource use, can be recycled or reused, and are generally environmentally friendly.
Ans.
Sustainability
27.
Which of the following attributes is most typical of a service?
Ans.
production and consumption occur simultaneously
28.
Which of the following would most likely fall under the scope of only an operations manager?
Ans.
setting inventory levels
29.
Aggregate planning is capacity planning for
Ans.
the intermediate range.
30.
In level scheduling, what is kept uniform from month to month?
Ans.
production/workforce levels
31.
A foundry produces circular utility access hatches (manhole covers). Currently, 120 covers are produced in a 10-hour shift. If labour productivity can be increased by 20%, it would then be
Ans.
New Labor Productivity = Current Labor Productivity * (1 + Percentage Increase)
New Labor Productivity = 12 covers/hr * (1 + 0.20) = 12 covers/hr * 1.20 = 14.4 covers/hr
Therefore, if labor productivity is increased by 20%, the new labor productivity would be 14.4
32.
Reasons to study Operations Management include
Ans.
knowing how goods and services are consumed.
33.
Among the ethical and social challenges facing operations managers are
Ans.
honouring financial commitments.
providing an efficient workplace.
ensuring quality products
maintaining a sustainable environment.
34.
Planning tasks associated with loading, sequencing, expediting, and dispatching typically fall under
Ans.
short-range plans.
35.
Customer interaction is often high for manufacturing processes, but low for services.
Ans.
False
36.
Which of the following statements is true?
Ans.
Each manufacturing employee now produces about 20 times more than in 1950.
37.
Which of the following aggregate planning strategies is a "capacity option"?
Ans.
changing inventory levels
38.
The purchasing function is concerned with
Ans.
generating the demand for the organization's products or services.
39.
Eagle Fabrication has the following aggregate demand requirements and other data for the upcoming four quarters.
Quarter
Demand
Previous quarter's output
Your preview ends here
Eager to read complete document? Join bartleby learn and gain access to the full version
- Access to all documents
- Unlimited textbook solutions
- 24/7 expert homework help
Related Questions
Suppose you sell items on a web site like Etsy and making them requires you to rent some equipment costing $1000 per year as a fixed cost. The materials for making these items cost $30 per item as a variable cost, and you sell them for a price of $50 each.
What number of items D' must you make and sell each year for you to breakeven on the cost of this activity?
You may be able to raise your sales price and then sell fewer items to maximize profit.
Since other people make and sell similar items, a higher price lowers the demand for your
product according to the price function p = $120 - 1.5 D. What is the profit maximizing
number of items D* that you would need to make and sell to maximize profit?
What is the profit earned for the annual number of items made and sold in part b?
arrow_forward
Pls help-)
arrow_forward
In the attached table, from 200 to 300 units of output, the average cost of
production is
in the short run.
Question 35
a rising
b
C
d
Selected answer will be automatically saved. For keyboard navigation, press up/down arrow keys to select an answer.
falling
constant
Output
0
indeterminant
100
200
300
400
Total Cost
$5,000
$5,700
$6,300
$7,100
$8,000
□
Variable Cost
$0
$700
$1,300
$2,100
$3,000
arrow_forward
Cost Analysis
A company manufactures fuel tanks for cars.
The total weekly cost (in dollars) of producing X fuel tanks is given by..
C(x) = 10000 +90x - 0.05x²
%3D
Find the exact cost of producing the 501st item.
(Round to the nearest 2 decimal places, if needed)
HINT: Steps to fiınd actual or exact (cost/revenue/profit)
1. Find the cost of x = 5003B
2. Then find the cost of x = 501%3;
3. Then subtract
ASUS
3
近
arrow_forward
1. In the short term, if your friend has Rp 200,000,000 per week, how many apps is he able to produce?
2. If your friend wants to produce 18 apps per week in the long term, how many programmers (L) dan cloud servers (K) are needed, and what is the total cost?
arrow_forward
Fast pls solve this question correctly in 5 min pls I will give u like for sure
Sub
arrow_forward
Just answered a and b
arrow_forward
Only typed answer
arrow_forward
E-commerce has had an explosive growth in the last year due to the pandemic. Many different retail companies with home delivery have had a significant increase in sales.
Imagine such a company with home delivery by trucks. Each truck costs NOK 600 per hour including all costs. The average distance per trip is 40 KM and they deliver approximately 60 packages per trip.
a. Calculate the cost per delivery. Make your own assumptions for the parameters that affect the time of the processes, like speed, loading time and unloading time. What would be their price per delivery, if they want a profit of 5%?
b. Discuss the risk for the transport provider in your price calculation.
arrow_forward
2. What is the relationship between the total cost curve, and the average cost per unit? Explain
their relationship, and draw a diagram showing how the two are related.
The total cost of production, in thousands of dollars, is C(q) = q³ 12q² + 60q, where q is in
thousands and 0 ≤ q ≤ 8.
(a) Graph C(q). Estimate visually the quantity at which average cost is minimized.
(b) Determine analytically the exact value of q at which average cost is minimized.
arrow_forward
Ike's Bikes is a major manufacturer of bicycles. Currently, the company produces bikes using only one factory. However, it is considering expanding
production to two or even three factories. The following table shows the company's short-run average total cost each month for various levels of
production if it uses one, two, or three factories. (Note: Q equals the total quantity of bikes produced by all factories.)
Number of Factories Q = 100 Q = 200
520
400
660
480
800
560
1
2
3
Average Total Cost
(Dollars per bike)
Q = 300
Q = 400
320
400
320
320
400
320
Q = 500
560
480
400
Q = 600
800
660
520
Suppose Ike's Bikes is currently producing 100 bikes per month in its only factory. Its short-run average total cost is $
per bike.
Suppose Ike's Bikes is expecting to produce 100 bikes per month for several years. In this case, in the long run, it would choose to produce bikes
using
On the following graph, plot the three short-run average total cost curves (SRATC) for Ike's Bikes from the…
arrow_forward
Plz fast
arrow_forward
5. Costs in the short run versus in the long run
Ike's Bikes is a major manufacturer of bicycles. Currently, the company produces bikes using only one factory. However, it is considering expanding
production to two or even three factories. The following table shows the company's short-run average total cost (SRATC) each month for various
levels of production if it uses one, two, or three factories. (Note: Q equals the total quantity of bikes produced by all factories.)
Number of Factories
1
2
3
Q = 100 Q 200
440
280
380
480
620
800
Average Total Cost
(Dollars per bike)
Q = 300
Q = 400
240
320
240
240
320
240
Q = 500
480
380
280
Q = 600
800
620
440
Suppose Ike's Bikes is currently producing 100 bikes per month in its only factory. Its short-run average total cost is $
per bike.
Suppose Ike's Bikes is expecting to produce 100 bikes per month for several years. In this case, in the long run, it would choose to produce bikes
using
On the following graph, plot the three SRATC curves for…
arrow_forward
Please answer question with details on how to do it. Thank you.
arrow_forward
EX22
arrow_forward
Question 27
When marginal product increases, marginal cost increases.
True
False
Moving to another question will save this response.
arrow_forward
SEE MORE QUESTIONS
Recommended textbooks for you
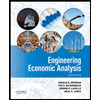
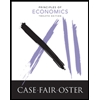
Principles of Economics (12th Edition)
Economics
ISBN:9780134078779
Author:Karl E. Case, Ray C. Fair, Sharon E. Oster
Publisher:PEARSON
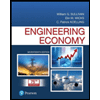
Engineering Economy (17th Edition)
Economics
ISBN:9780134870069
Author:William G. Sullivan, Elin M. Wicks, C. Patrick Koelling
Publisher:PEARSON
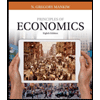
Principles of Economics (MindTap Course List)
Economics
ISBN:9781305585126
Author:N. Gregory Mankiw
Publisher:Cengage Learning
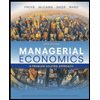
Managerial Economics: A Problem Solving Approach
Economics
ISBN:9781337106665
Author:Luke M. Froeb, Brian T. McCann, Michael R. Ward, Mike Shor
Publisher:Cengage Learning
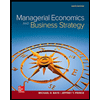
Managerial Economics & Business Strategy (Mcgraw-...
Economics
ISBN:9781259290619
Author:Michael Baye, Jeff Prince
Publisher:McGraw-Hill Education
Related Questions
- Suppose you sell items on a web site like Etsy and making them requires you to rent some equipment costing $1000 per year as a fixed cost. The materials for making these items cost $30 per item as a variable cost, and you sell them for a price of $50 each. What number of items D' must you make and sell each year for you to breakeven on the cost of this activity? You may be able to raise your sales price and then sell fewer items to maximize profit. Since other people make and sell similar items, a higher price lowers the demand for your product according to the price function p = $120 - 1.5 D. What is the profit maximizing number of items D* that you would need to make and sell to maximize profit? What is the profit earned for the annual number of items made and sold in part b?arrow_forwardPls help-)arrow_forwardIn the attached table, from 200 to 300 units of output, the average cost of production is in the short run. Question 35 a rising b C d Selected answer will be automatically saved. For keyboard navigation, press up/down arrow keys to select an answer. falling constant Output 0 indeterminant 100 200 300 400 Total Cost $5,000 $5,700 $6,300 $7,100 $8,000 □ Variable Cost $0 $700 $1,300 $2,100 $3,000arrow_forward
- Cost Analysis A company manufactures fuel tanks for cars. The total weekly cost (in dollars) of producing X fuel tanks is given by.. C(x) = 10000 +90x - 0.05x² %3D Find the exact cost of producing the 501st item. (Round to the nearest 2 decimal places, if needed) HINT: Steps to fiınd actual or exact (cost/revenue/profit) 1. Find the cost of x = 5003B 2. Then find the cost of x = 501%3; 3. Then subtract ASUS 3 近arrow_forward1. In the short term, if your friend has Rp 200,000,000 per week, how many apps is he able to produce? 2. If your friend wants to produce 18 apps per week in the long term, how many programmers (L) dan cloud servers (K) are needed, and what is the total cost?arrow_forwardFast pls solve this question correctly in 5 min pls I will give u like for sure Subarrow_forward
- Just answered a and barrow_forwardOnly typed answerarrow_forwardE-commerce has had an explosive growth in the last year due to the pandemic. Many different retail companies with home delivery have had a significant increase in sales. Imagine such a company with home delivery by trucks. Each truck costs NOK 600 per hour including all costs. The average distance per trip is 40 KM and they deliver approximately 60 packages per trip. a. Calculate the cost per delivery. Make your own assumptions for the parameters that affect the time of the processes, like speed, loading time and unloading time. What would be their price per delivery, if they want a profit of 5%? b. Discuss the risk for the transport provider in your price calculation.arrow_forward
- 2. What is the relationship between the total cost curve, and the average cost per unit? Explain their relationship, and draw a diagram showing how the two are related. The total cost of production, in thousands of dollars, is C(q) = q³ 12q² + 60q, where q is in thousands and 0 ≤ q ≤ 8. (a) Graph C(q). Estimate visually the quantity at which average cost is minimized. (b) Determine analytically the exact value of q at which average cost is minimized.arrow_forwardIke's Bikes is a major manufacturer of bicycles. Currently, the company produces bikes using only one factory. However, it is considering expanding production to two or even three factories. The following table shows the company's short-run average total cost each month for various levels of production if it uses one, two, or three factories. (Note: Q equals the total quantity of bikes produced by all factories.) Number of Factories Q = 100 Q = 200 520 400 660 480 800 560 1 2 3 Average Total Cost (Dollars per bike) Q = 300 Q = 400 320 400 320 320 400 320 Q = 500 560 480 400 Q = 600 800 660 520 Suppose Ike's Bikes is currently producing 100 bikes per month in its only factory. Its short-run average total cost is $ per bike. Suppose Ike's Bikes is expecting to produce 100 bikes per month for several years. In this case, in the long run, it would choose to produce bikes using On the following graph, plot the three short-run average total cost curves (SRATC) for Ike's Bikes from the…arrow_forwardPlz fastarrow_forward
arrow_back_ios
SEE MORE QUESTIONS
arrow_forward_ios
Recommended textbooks for you
- Principles of Economics (12th Edition)EconomicsISBN:9780134078779Author:Karl E. Case, Ray C. Fair, Sharon E. OsterPublisher:PEARSONEngineering Economy (17th Edition)EconomicsISBN:9780134870069Author:William G. Sullivan, Elin M. Wicks, C. Patrick KoellingPublisher:PEARSON
- Principles of Economics (MindTap Course List)EconomicsISBN:9781305585126Author:N. Gregory MankiwPublisher:Cengage LearningManagerial Economics: A Problem Solving ApproachEconomicsISBN:9781337106665Author:Luke M. Froeb, Brian T. McCann, Michael R. Ward, Mike ShorPublisher:Cengage LearningManagerial Economics & Business Strategy (Mcgraw-...EconomicsISBN:9781259290619Author:Michael Baye, Jeff PrincePublisher:McGraw-Hill Education
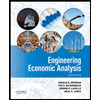
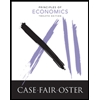
Principles of Economics (12th Edition)
Economics
ISBN:9780134078779
Author:Karl E. Case, Ray C. Fair, Sharon E. Oster
Publisher:PEARSON
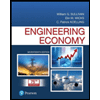
Engineering Economy (17th Edition)
Economics
ISBN:9780134870069
Author:William G. Sullivan, Elin M. Wicks, C. Patrick Koelling
Publisher:PEARSON
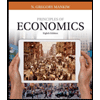
Principles of Economics (MindTap Course List)
Economics
ISBN:9781305585126
Author:N. Gregory Mankiw
Publisher:Cengage Learning
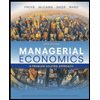
Managerial Economics: A Problem Solving Approach
Economics
ISBN:9781337106665
Author:Luke M. Froeb, Brian T. McCann, Michael R. Ward, Mike Shor
Publisher:Cengage Learning
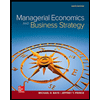
Managerial Economics & Business Strategy (Mcgraw-...
Economics
ISBN:9781259290619
Author:Michael Baye, Jeff Prince
Publisher:McGraw-Hill Education