W3_Lab
docx
School
Defense Acquisition University *
*We aren’t endorsed by this school
Course
MET230
Subject
Mechanical Engineering
Date
Dec 6, 2023
Type
docx
Pages
9
Uploaded by charleshaskett
MET230
Hydraulics and Pneumatics Systems
Instructor:
Mohsen Latifi
Lab 3
Hydraulics and Pneumatics Systems
Student Name(s):
Charles Haskett
Honor Pledge:
I pledge to support the Honor System of ECPI. I will refrain from any form of academic
dishonesty or deception, such as cheating or plagiarism. I am aware that as a member of the
academic community, it is my responsibility to turn in all suspected violators of the honor code. I
understand that any failure on my part to support the Honor System will be turned over to a
Judicial Review Board for determination. I will report to the Judicial Review Board hearing if
summoned.
Charles Haskett
Date:
Contents
Abstract
.......................................................................................................................................................
3
Introduction
.................................................................................................................................................
3
Procedures or Problem Statement
................................................................................................................
4
Part I: Exercise One Pneumatic System
....................................................................................................
4
Part II: Exercise Two Pneumatic System
...................................................................................................
4
Data Presentation & Analysis
......................................................................................................................
5
Predictions
...............................................................................................................................................
5
Required Screenshots
..............................................................................................................................
5
Conclusion
...................................................................................................................................................
6
References
...................................................................................................................................................
7
2
Abstract
In this course, the student will be instructed on how to use Automation Studio simulation
software to create various pneumatic systems. This will teach the student not only how to build a
pneumatic schematic using symbols but also how to construct a ladder diagram to oversee the
pneumatic circuit. In addition to using symbols already known to the student, new schematic
symbols will be introduced for the ladder diagram. The student will be required to observe the
pneumatic circuit and predict its outcome. The student will be tasked with building the schematic
and ladder diagram and then simulating the circuit to confirm their predictions.
I
ntroduction
Pneumatics is a system that utilizes compressed air to operate machinery automatically. It is
commonly used in industrial manufacturing, garages, and dental offices. The compressed air is
filtered and dried to protect the components, and lubrication may be added to improve
performance. The system generates power through linear or rotary motion using air at a pressure
of 60 to 120 PSI. Hydraulics is a similar system that utilizes oil at much higher pressure, ranging
from 800 to 5000 PSI.
3
Your preview ends here
Eager to read complete document? Join bartleby learn and gain access to the full version
- Access to all documents
- Unlimited textbook solutions
- 24/7 expert homework help
Procedures or Problem Statement
Part I: Exercise One Pneumatic System
During the exercise, I began by placing the schematic symbols for the pneumatic circuit that I
was already familiar with. Once I had all the symbols required for the pneumatic circuit, I
proceeded to build it. First, I connected the pressure source to the electronically controlled
valve, which I then connected to a variable throttle. I connected the other side of the variable
throttle to the end cap of the cylinder. I then connected a line from the rod side of the cylinder
back to the electronically controlled valve and then to the exhaust.
After completing the pneumatic circuit, I moved on to locating and placing the schematic
symbols required to build the ladder diagram to control the pneumatic circuit. The ladder
diagram needed the following symbols: a twenty-four-volt power source, a reference power
source, a normally closed pushbutton (for stop), a normally open pushbutton (for start), two
open connectors, a limit switch, a coil, and a solenoid. The twenty-four-volt power source
powered the entire ladder diagram, and the reference power source represented the ground to
complete the electrical circuit.
The stop pushbutton and the start pushbutton started the first rung with one of the open
connectors connected between the stop and start connection and the other side connected
between the start and limit switch. The limit switch was connected between the start
pushbutton and the coil. The second rung consisted of the second open connector and the
solenoid source.
Please see Figure 1 for the schematic of the exercise one system.
Part II: Exercise Two Pneumatic System
During the exercise, I first placed the schematic symbols for the pneumatic circuit that I was
already familiar with. Once I had all the symbols required, I proceeded to build the circuit. I
connected the pressure source to the double solenoid electronically controlled valve, and then
connected the valve to the double action cylinder. Two pressure switches were connected, one
between the valve and cylinder, and the other in the line from the valve to the cylinder. The
exhaust was then connected to the valve, completing the pneumatic circuit schematic.
After completing the pneumatic circuit, I moved on to placing the schematic symbols required
for building the ladder diagram. The ladder diagram needed the following symbols: a 24-volt
power source, a reference power source, a toggle switch, two proximity switches, and two
solenoids.
For the schematic of the exercise two system, please refer to Figure 2.
5
Data Presentation & Analysis
Predictions
Exercise I:
I believe that when the Start pushbutton is momentarily pressed the cylinder will begin to
extend and retract automatically until the start pushbutton is released.
Exercise II:
I believe that when the toggle switch is closed the cylinder will begin to extend and retract
automatically and continue to repeat the process until the toggle switch is opened.
Required Screenshots
Figure 1. Exercise One Pneumatic System Schematic
Figure 2. Exercise Two Pneumatic System Schematic
Your preview ends here
Eager to read complete document? Join bartleby learn and gain access to the full version
- Access to all documents
- Unlimited textbook solutions
- 24/7 expert homework help
7
Conclusion
In the first exercise of this lab, I constructed the pneumatic circuit. Building the circuit was
relatively easy, except for finding the correct electronically controlled four/two-way valve that
the circuit required. Once I found the right valve, I completed the circuit. Next, I moved on to
building the ladder diagram that would control the pneumatic circuit. However, I faced some
issues in locating the correct schematic symbols for the ladder diagram. Some of the locations I
tried gave an error stating that the system could not be used with the current pneumatic circuit.
Eventually, I found the right location for the symbols and completed the ladder diagram without
any further problems. I connected the symbols with the respective connections of the pneumatic
circuit and started the simulation. During the simulation, I observed that my prediction was
partially correct. When I pressed the start pushbutton, the cylinder extended and retracted
automatically. However, I was unaware that the longer I kept the start pushbutton pressed, the
less the rod would fully retract. I found that the rod would not fully retract until I released the
start pushbutton and the system returned to its original state.
The second exercise was easier to complete than the first one since it had similar schematic
symbols. However, I couldn't find the double solenoid electrically controlled four/two-way valve
required for the circuit. So, I had to modify the one I had by removing the spring and adding the
second solenoid. After modifying the valve, I was able to complete the pneumatic circuit. The
ladder diagram was simple too since I had already learned the location of the symbols from the
first exercise. Once I finished building the pneumatic circuit and ladder diagram, I started the
simulation. When I closed the toggle switch, the cylinder behaved exactly as I had predicted. It
extended and retracted continuously until I opened the toggle switch. The pneumatic circuit then
returned to its original position, with the rod fully retracted.
References
Esposito, A. (2014). Fluid Power with Applications. Essex: Pearson.
Inc, F. T. (2023). Automation Studio Educational Edition. Retrieved from Famic Technologies
Inc: https://www.famictech.com/en/Products/Automation-Studio/Educational-Edition
Your preview ends here
Eager to read complete document? Join bartleby learn and gain access to the full version
- Access to all documents
- Unlimited textbook solutions
- 24/7 expert homework help
Related Documents
Related Questions
Help!!! Please answer all Correctly!!! Please
arrow_forward
Jeff was just hired by GSI, Inc. to be their Environmental and Safety Coordinator. This is Jeff's first position after completing his engineering degree. He had taken a course in safety engineering as part of his studies and felt confident that he could handle the job.
Management at GSI, Inc. has assured him that they are committed to maintaining a safe workplace. They have never had an individual dedicated to this task full-time. They will implement his recommendations if he can justify them.
As Jeff begins to get familiar with the operations, he spends considerable time on the production floor. He notices workers clean their tools before break with a liquid from an unmarked 55-gallon drum. They also use this liquid to clean residue from their skin. They use paper towels to dry their tools and hands, throw these towels in the trash, and head to the break room for a snack and/or smoke.
In talking with the workers, Jeff learns of some of their concerns. Several people mention…
arrow_forward
Jeff was just hired by GSI, Inc. to be their Environmental and Safety Coordinator. This is Jeff's first position after completing his engineering degree. He had taken a course in safety engineering as part of his studies and felt confident that he could handle the job.
Management at GSI, Inc. has assured him that they are committed to maintaining a safe workplace. They have never had an individual dedicated to this task full-time. They will implement his recommendations if he can justify them.
As Jeff begins to get familiar with the operations, he spends considerable time on the production floor. He notices workers clean their tools before break with a liquid from an unmarked 55-gallon drum. They also use this liquid to clean residue from their skin. They use paper towels to dry their tools and hands, throw these towels in the trash, and head to the break room for a snack and/or smoke.
In talking with the workers, Jeff learns of some of their concerns. Several people…
arrow_forward
Jeff was just hired by GSI, Inc. to be their Environmental and Safety Coordinator. This is Jeff's first position after completing his engineering degree. He had taken a course in safety engineering as part of his studies and felt confident that he could handle the job.
Management at GSI, Inc. has assured him that they are committed to maintaining a safe workplace. They have never had an individual dedicated to this task full-time. They will implement his recommendations if he can justify them.
As Jeff begins to get familiar with the operations, he spends considerable time on the production floor. He notices workers clean their tools before break with a liquid from an unmarked 55-gallon drum. They also use this liquid to clean residue from their skin. They use paper towels to dry their tools and hands, throw these towels in the trash, and head to the break room for a snack and/or smoke.
In talking with the workers, Jeff learns of some of their concerns. Several people…
arrow_forward
Help!!! Please answer part B correctly!!! Please
arrow_forward
Question 2
You are a biomedical engineer working for a small orthopaedic firm that fabricates rectangular shaped fracture
fixation plates from titanium alloy (model = "Ti Fix-It") materials. A recent clinical report documents some problems with the plates
implanted into fractured limbs. Specifically, some plates have become permanently bent while patients are in rehab and doing partial
weight bearing activities.
Your boss asks you to review the technical report that was generated by the previous test engineer (whose job you now have!) and used to
verify the design. The brief report states the following... "Ti Fix-It plates were manufactured from Ti-6Al-4V (grade 5) and machined into
solid 150 mm long beams with a 4 mm thick and 15 mm wide cross section. Each Ti Fix-It plate was loaded in equilibrium in a 4-point bending
test (set-up configuration is provided in drawing below), with an applied load of 1000N. The maximum stress in this set-up was less than the
yield stress for the…
arrow_forward
Need help with this
arrow_forward
please read everything properly... Take 3 4 5 hrs but solve full accurate drawing on bond paper don't use chat gpt etc okk
arrow_forward
Help!!! Please answer part b correctly like part A. Please!!!!
arrow_forward
Help!!! Please answer all Correctly!!! Please
arrow_forward
You go on a road trip to escape the cold winter days of Kirkland Lake, Ontario to the warm beaches of Moonbeam, Ontario. Since it is a long drive and you are leaving early in the morning, you make sure to check the tire pressure and make sure it is at the recommended level.
At lunchtime, you stop for gas and decide to check your car's tire pressure again. You also notice that the tires seem to be a little bit larger than when you left.
The driver's manual suggests a pressure between 205 and 220 kPa. Knowing that the tires heat up while driving; do you expect your reading to be high, low or the same as the recommended tire pressure? Why? Since you plan on staying in Moonbeam a while to see the sights, you think it would be best to adjust your tire pressure. What adjustments should be made to your tires? Should you make these adjustments as soon as you arrive, or the following day?
arrow_forward
Help.
arrow_forward
Write an essay discussing how important safety is to your engineering profession. Also,
identify and explain the Hazard Communication processes and procedures commonly
found in your engineering profession.
arrow_forward
dear tutor please provide neat and clean and detailed answer.
dont copy from google
adress both questions well
arrow_forward
Task 1
You are employed as a mechanical engineer within an unnamed research center, specializing in the development.
of innovative air conditioning systems. Your division is tasked with providing computer-based modeling and
design solutions using computational fluid dynamics through ANSYS software. Your primary responsibilities.
involve the analysis of horizontal channel dynamics to meet specific criteria. Under the guidance of your
immediate supervisor, you have been assigned unique responsibilities within an ongoing project. As a member of
the research team, your role includes constructing an appropriate model and executing a sequence of simulation.
iterations to explore and enhance channel performance. Figure 1 provides a visualization of the horizontal channel
under consideration. Consider 2D, incompressible, steady flowin a horizontal channel at a Reynolds number of
150. The schematic below illustrates the channel flow, not drawn to scale. For simplicity, neglect gravity. The…
arrow_forward
ENGR 2411 Applied England Environmental Science
Spring 2024 Semester
The University of Oklahoma School of Civil
Problem 2-(40 pts.)
Prerequisite Quiz
Statics
Page 3 of 4
Your Mind Harper loves to zipline. Every summer they travel the Midwest looking for
new line adventures. During
they became increasingly concerned
abour the tension in the zipline cable recent adve friend take a picture of them while on
They had a
his line and want you to determine the tension in each of the cables. Look how much
fn Harper is having!
Cable AB has a length of 150 ft and Cable BC has a length of 195 ft. Harper has a weight of
100 lbs (this is the force from Harper). The angle formed by 0-12° and the angle formed
by a 37 Assume that the harness holding your friend is perfectly vertical when the
picture was taken. Using this information and the information in the image below
determine the tension in cables AB and BC. (hint: Draw a free body diagram to get
started)
ef
Sammy
Answer
arrow_forward
Select all true statements.
O To obtain a mining lease, the holder of a mining claim must absolutely acquire
surface rights.
| Mechanized stripping is used to expose the bedrock linearly to test the
geological unit of interest on its full width, perpendicular to its contact with the
surrounding units.
The apparent length of a mineralized zone of interest is always shorter than its
true width.
Upon reaching commercial production, the purchaser of a mineral exploration
property can pay a certain amount to the seller in exchange for a reduction of
the percentage of the Net Smelter Return (NSR) retained by the seller.
arrow_forward
Question 3
You are working on a design team at a small orthopaedic firm. Your team is starting to work on a lower limb
(foot-ankle) prosthesis for individuals who have undergone foot amputation (bone resection at the distal tibia). You remember hearing
about "osseointegration" in an exciting orthopaedic engineering class you attended at Clemson, so you plan to attach the foot
prosthesis using a solid metal rod inserted into the distal tibia. You think stainless steel or titanium alloy might be a useful rod material.
You decide to begin this problem by identifying typical tibial bone anatomy and mechanical behavior (as provided in the tables and
image below). You assume the tibial bone can be modeled as a hollow cylinder of cortical bone, as represented in the image. You
anticipate the length of the rod will be 1/2 the length of the tibia.
Q3G: Critical Thinking: What would you propose to your team as the next step in this analysis? Is it reasonable to assume the rod
will experience the…
arrow_forward
C)If both cyclists have 170 mm cranks on their bikes, what will be the mechanical advantage (considering only the movement of the feet with a constant force for walking and riding), in percent, that each rider will have achieved over walking the same distance? (This can
be found by dividing the distance wallked by the distance the feet move in riding.)
arrow_forward
SEE MORE QUESTIONS
Recommended textbooks for you
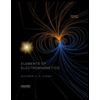
Elements Of Electromagnetics
Mechanical Engineering
ISBN:9780190698614
Author:Sadiku, Matthew N. O.
Publisher:Oxford University Press
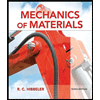
Mechanics of Materials (10th Edition)
Mechanical Engineering
ISBN:9780134319650
Author:Russell C. Hibbeler
Publisher:PEARSON
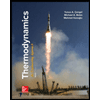
Thermodynamics: An Engineering Approach
Mechanical Engineering
ISBN:9781259822674
Author:Yunus A. Cengel Dr., Michael A. Boles
Publisher:McGraw-Hill Education
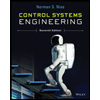
Control Systems Engineering
Mechanical Engineering
ISBN:9781118170519
Author:Norman S. Nise
Publisher:WILEY
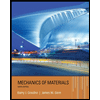
Mechanics of Materials (MindTap Course List)
Mechanical Engineering
ISBN:9781337093347
Author:Barry J. Goodno, James M. Gere
Publisher:Cengage Learning
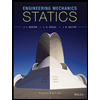
Engineering Mechanics: Statics
Mechanical Engineering
ISBN:9781118807330
Author:James L. Meriam, L. G. Kraige, J. N. Bolton
Publisher:WILEY
Related Questions
- Help!!! Please answer all Correctly!!! Pleasearrow_forwardJeff was just hired by GSI, Inc. to be their Environmental and Safety Coordinator. This is Jeff's first position after completing his engineering degree. He had taken a course in safety engineering as part of his studies and felt confident that he could handle the job. Management at GSI, Inc. has assured him that they are committed to maintaining a safe workplace. They have never had an individual dedicated to this task full-time. They will implement his recommendations if he can justify them. As Jeff begins to get familiar with the operations, he spends considerable time on the production floor. He notices workers clean their tools before break with a liquid from an unmarked 55-gallon drum. They also use this liquid to clean residue from their skin. They use paper towels to dry their tools and hands, throw these towels in the trash, and head to the break room for a snack and/or smoke. In talking with the workers, Jeff learns of some of their concerns. Several people mention…arrow_forwardJeff was just hired by GSI, Inc. to be their Environmental and Safety Coordinator. This is Jeff's first position after completing his engineering degree. He had taken a course in safety engineering as part of his studies and felt confident that he could handle the job. Management at GSI, Inc. has assured him that they are committed to maintaining a safe workplace. They have never had an individual dedicated to this task full-time. They will implement his recommendations if he can justify them. As Jeff begins to get familiar with the operations, he spends considerable time on the production floor. He notices workers clean their tools before break with a liquid from an unmarked 55-gallon drum. They also use this liquid to clean residue from their skin. They use paper towels to dry their tools and hands, throw these towels in the trash, and head to the break room for a snack and/or smoke. In talking with the workers, Jeff learns of some of their concerns. Several people…arrow_forward
- Jeff was just hired by GSI, Inc. to be their Environmental and Safety Coordinator. This is Jeff's first position after completing his engineering degree. He had taken a course in safety engineering as part of his studies and felt confident that he could handle the job. Management at GSI, Inc. has assured him that they are committed to maintaining a safe workplace. They have never had an individual dedicated to this task full-time. They will implement his recommendations if he can justify them. As Jeff begins to get familiar with the operations, he spends considerable time on the production floor. He notices workers clean their tools before break with a liquid from an unmarked 55-gallon drum. They also use this liquid to clean residue from their skin. They use paper towels to dry their tools and hands, throw these towels in the trash, and head to the break room for a snack and/or smoke. In talking with the workers, Jeff learns of some of their concerns. Several people…arrow_forwardHelp!!! Please answer part B correctly!!! Pleasearrow_forwardQuestion 2 You are a biomedical engineer working for a small orthopaedic firm that fabricates rectangular shaped fracture fixation plates from titanium alloy (model = "Ti Fix-It") materials. A recent clinical report documents some problems with the plates implanted into fractured limbs. Specifically, some plates have become permanently bent while patients are in rehab and doing partial weight bearing activities. Your boss asks you to review the technical report that was generated by the previous test engineer (whose job you now have!) and used to verify the design. The brief report states the following... "Ti Fix-It plates were manufactured from Ti-6Al-4V (grade 5) and machined into solid 150 mm long beams with a 4 mm thick and 15 mm wide cross section. Each Ti Fix-It plate was loaded in equilibrium in a 4-point bending test (set-up configuration is provided in drawing below), with an applied load of 1000N. The maximum stress in this set-up was less than the yield stress for the…arrow_forward
- Help!!! Please answer all Correctly!!! Pleasearrow_forwardYou go on a road trip to escape the cold winter days of Kirkland Lake, Ontario to the warm beaches of Moonbeam, Ontario. Since it is a long drive and you are leaving early in the morning, you make sure to check the tire pressure and make sure it is at the recommended level. At lunchtime, you stop for gas and decide to check your car's tire pressure again. You also notice that the tires seem to be a little bit larger than when you left. The driver's manual suggests a pressure between 205 and 220 kPa. Knowing that the tires heat up while driving; do you expect your reading to be high, low or the same as the recommended tire pressure? Why? Since you plan on staying in Moonbeam a while to see the sights, you think it would be best to adjust your tire pressure. What adjustments should be made to your tires? Should you make these adjustments as soon as you arrive, or the following day?arrow_forwardHelp.arrow_forward
arrow_back_ios
SEE MORE QUESTIONS
arrow_forward_ios
Recommended textbooks for you
- Elements Of ElectromagneticsMechanical EngineeringISBN:9780190698614Author:Sadiku, Matthew N. O.Publisher:Oxford University PressMechanics of Materials (10th Edition)Mechanical EngineeringISBN:9780134319650Author:Russell C. HibbelerPublisher:PEARSONThermodynamics: An Engineering ApproachMechanical EngineeringISBN:9781259822674Author:Yunus A. Cengel Dr., Michael A. BolesPublisher:McGraw-Hill Education
- Control Systems EngineeringMechanical EngineeringISBN:9781118170519Author:Norman S. NisePublisher:WILEYMechanics of Materials (MindTap Course List)Mechanical EngineeringISBN:9781337093347Author:Barry J. Goodno, James M. GerePublisher:Cengage LearningEngineering Mechanics: StaticsMechanical EngineeringISBN:9781118807330Author:James L. Meriam, L. G. Kraige, J. N. BoltonPublisher:WILEY
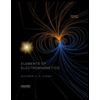
Elements Of Electromagnetics
Mechanical Engineering
ISBN:9780190698614
Author:Sadiku, Matthew N. O.
Publisher:Oxford University Press
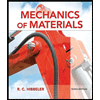
Mechanics of Materials (10th Edition)
Mechanical Engineering
ISBN:9780134319650
Author:Russell C. Hibbeler
Publisher:PEARSON
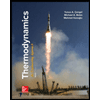
Thermodynamics: An Engineering Approach
Mechanical Engineering
ISBN:9781259822674
Author:Yunus A. Cengel Dr., Michael A. Boles
Publisher:McGraw-Hill Education
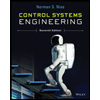
Control Systems Engineering
Mechanical Engineering
ISBN:9781118170519
Author:Norman S. Nise
Publisher:WILEY
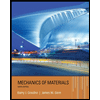
Mechanics of Materials (MindTap Course List)
Mechanical Engineering
ISBN:9781337093347
Author:Barry J. Goodno, James M. Gere
Publisher:Cengage Learning
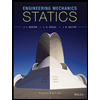
Engineering Mechanics: Statics
Mechanical Engineering
ISBN:9781118807330
Author:James L. Meriam, L. G. Kraige, J. N. Bolton
Publisher:WILEY