CE 3700 Labs 3.4 and 5 Report
docx
keyboard_arrow_up
School
Louisiana State University *
*We aren’t endorsed by this school
Course
3700
Subject
Mechanical Engineering
Date
Apr 3, 2024
Type
docx
Pages
10
Uploaded by MagistrateSandpiper307
CE 3700 Engineering Materials Laboratory “Compressive Strength on Cement Mortar Cubes” (Lab 3)
“Compressive Strength on Cylinders and Slump Test” (Lab 4)
&
“Compressive Strength Testing on Mortar Cubes and Concrete Cylinders” (Lab 5)
Performed By:
Group 1
Section 2
Submitted by: Danielle Brigoli
Date Performed: Date Submitted:
February 8
th
, 22
nd
, and 29
th
March 5th
Department of Civil and Environmental Engineering Louisiana State University Spring 2024
Introduction & Purpose: Compressive Strength on Cement Mortar Cubes:
This experiment aims to determine the compressive strength of 3 different Cement Mortar Cubes at three other plastic conditions. Before experimenting, students must follow the test procedure ASTM C-1099 and these conditions to determine which water quantity allows for the greatest compressive strength. Each group must perform on the assigned water ratio of 1kg of
water to 4kg of cement and use the ASTM C-1099 procedure to determine how much any of the materials could be hard or soft enough to measure their compressive stress (psi). The compressive length will be determined using the Forney Compression Tester 14-21 days after curing to see how much load the material weighs (lbs). In most cases, this experiment is used for everyday life because of the specific strength of concrete, and the contractor would provide the cheapest way to use the precise cement-to-water ratio.
Compressive Strength for Slump of Concrete Cement:
The slump test for Portland cement aims to measure the material's workability. It is vital because normal concrete slumps are 2-4 inches. The significance of this experiment is making sure the slump value is acceptable; if the slump is 4-6 inches, the material would have a high slump value, which is not optimum. The use of this experiment is to determine the proper plastic mixture for the given design criteria. Highway pavements use plastic concrete at a slump test of 1 inch, so this experiment is used daily in concrete design for roads and buildings. Compressive Strength on Mortar Cubes and Cylindrical Concrete Specimens:
In this procedure, once the strength of the mortar cube is known, students must be able to measure the optimum cement-to-water ratio for ideal compressive strength by allowing specimens to cure for seven days. Then, it is tested for failure using a Forney Compression tester.
The significance of this procedure is to know the strength of a material when selecting concrete for a specific purpose and in concrete design while it is to help determine concrete’s portioning and mixing. Significance and Use: Sypnosis in all labs as described:
In this experiment, students must determine the compressive strength of 3 cement mortar cubes and three cylindrical mixtures. The results will differ depending on the group's water ratio and the cement’s stress and load. At the end of the experiment, students must calculate the weight
and determine that the compressive strength is strong enough, or it could fail.
Apparatus/ Equipment:
Compressive Strength on Cement Mortar Cubes:
Weights and Weighing Devices
Glass Graduates
Specimen Molds (2 in. Cube)
Mixer, Bowl, and Paddle
Flow Table and Flow Mold
Tamper
Trowel
Moist Cabinet or Room
Testing Machine
Compressive Strength for Slump of Concrete Cement:
Cylinder Molds
Tampering Rod
Mallets
Small Tools
Sampling and Mixing Pan
Testing Machine
Compressive Strength on Mortar Cubes and Cylindrical Concrete
Specimens:
Mold
Tamping Rod
Measuring Device
Scoop
Test Materials:
Portland Cement Concrete, Water Cement Ratio
Your preview ends here
Eager to read complete document? Join bartleby learn and gain access to the full version
- Access to all documents
- Unlimited textbook solutions
- 24/7 expert homework help
These test materials are used to perform this lab for the Portland cement, composed of several different materials such as limestone, silica, alumina, iron oxide, and gypsum. The sample weight differs slightly from ASTM C 109, C 109M, which requires 1375 g of sand, 245 g
of water, and 500 g of cement. In this experiment, there are 907.2 g of sand and cement and 453.6 g of water. In conclusion, the water-cement ratio of 0.50.
Compressive Strength of Cylindrical Concrete Specimens and Slump Test
The cement used in this lab is type 1 Portland Cement, with ASTM C192, ASTM C143, and ASTM C39 standards. The group was assigned a mix for a water-cement ratio of 0.38 and a target compressive strength of 2500 psi. Each component of the mixture weighed 4.22 lb of cement, 3.32 lb of water, 18.54 lb for the Coarse Aggregate, and 12.74 lb of fine aggregate. The total material weight will reach up to 38.82 lb. Test Procedure:
Portland Cement Concrete, Water Cement Ratio (3 Mortar Cubes) (Lab 4):
The procedure that the Portland Cement Concrete experiment required was done in compliance with ASTM-150, C-109, and C-39. Each of the three groups was given a different water/cement ratio, with our group testing a w/c ratio of 50%, which utilized 453.6 grams of water.
We mixed half of the predetermined amounts of water, sand, and cement until the mixture was uniform and then mixed the rest of the materials. Once the mixture was uniform, half the material was transferred to a three-cube mold measuring 2 x 2 x 2 inches. The tampering tool was then used to remove any air bubbles from the mold. Then, the material's last half was added and tampered down to eliminate air bubbles (Figure 2). A rubber mallet was used to tap on the sides of the mold to get any other air bubbles out of the mold (Figure 3). A scraper was then applied to the top to smooth the mold, allowing the compressive machine to get the best data for the tests with uniform samples. The samples were then placed into a 100% humidity room to cure. Once curing for seven days was complete, the samples were subjected to the compressive strength test until failure was reached. Figure 1
Figure 2
Figure 3
Compressive Strength of Cylindrical Concrete Specimens and Slump Test (Labs 5 & 6):
ASTM C192 did the test procedure, but the molds are set for seven days to cure rather than 28 days, as suggested in the ASTM standards. To begin, the materials of water, Portland cement, fine aggregate, and coarse aggregate were weighed and placed into separate containers (Figure 4 & 5). The materials were mixed to form a uniform mixture using the hands of the person experimenting. The mixed material was then placed into a 12-inch cone mold and filled 1/3 at a time (Figure 6). After serving a third, it was tampered with 25 times to remove air bubbles. This was repeated three times till the metal cone was full. The mold was then tapped on its sides to remove any excess air on the sides. The mold was put onto the ground according to ATSM standards and removed. The slump was then measured by placing the mold next to the concrete sample and the distance measured between the height difference. The slump for our group was 5.5 inches (Figure 7). The material was then removed from the floor and put into the container. A third of the material was poured into the three-cylinder molds and then tampered with to remove excess air bubbles. This was repeated till the molds were full. A rubber mallet was then used to hit the sides of the molds to help release the last air bubbles and evenly disperse
the mixture. Due to low vibration, a table was used to remove the previous air bubbles for the water-cement ratio. The straight edge was then used to smooth the top of the cylinder molds (Figure 8). After the specimen was covered and placed in the humid room, it was allowed to cure
for seven days. After seven days, the molds were removed, and sample dimensions and weight were recorded. These samples were then placed into the specimen machine and had a load applied till they reached failure.
Figure
4 Figure
5 Figure
6
Figure 7 Slump Test Figure 8 Analysis of Results: Portland Cement Concrete, Water Cement Ratio (3 Mortar Cubes) (Lab 4)
The material's strength is determined by dividing the total force by the area of the perpendicular cross-section. With the lack of aggregate in the mixture, the compound made was a mortar. The water-cement ratio for group
1 was 0.5, while the other groups used a 0.4 and 0.3 water-cement ratio. The
main goal was to determine the average rate of failure when a load was applied to each sample. It was also to see how the rates of failures for each group compared with the water or cement ratio.
TABLE 1: Group 1 Individual Cube Results
Sample
Area (In^2)
Load At Failure (lbs)
Compressive Strength (psi)
1
4
37658
9414.5
2
4
37254
9313.5
3
4
15663
3915.75
TABLE 2: Average Cube Strengths of All Groups
Group
W/C Ratio
Sand (g)
Cement (g)
Water
(g)
Average Load
At Failure (lbs)
Average Compressive
Strength (psi)
1
0.3
907.2
907.2
272.2
37456
9364
2
0.4
907.2
907.2
362.9
28852
7213
3
0.5
907.2
907.2
453.6
25347
6336.75
Your preview ends here
Eager to read complete document? Join bartleby learn and gain access to the full version
- Access to all documents
- Unlimited textbook solutions
- 24/7 expert homework help
This graph represents the average load failure of all three group samples after the compressive strength test was performed, which was based on the calculations from 28 days to cure: as shown in the graph, the larger the w/c ratio, the weaker the concrete sample. Graph 1: This
chart describes the relationship between the average compressive strength of the mortal cubes tested and water-cement ratios in all three groups.
Compressive Strength of Cylindrical Concrete Specimens and Slump Test (Labs 5 & 6
):
Note that the cross-sectional area of cylinders is 12.566 inches^2. During the slump test, the mixture had a 3-inch displacement center. This places the concrete into the medium workability category. Tables 3 and 4 show that lower water-cement ratios produce more robust cylinders. The slump test results in group 1 are about 5 inches. After removing the triangular dome, it turns out that the measurement for the slump test comes out to be 5.5 inches (See figure 7). TABLE 3: Group 1 Individual Cylinder Results (0.67 W/C Ratio)
Sample
Load At Failure (lbs)
Compressive
Strength (psi)
1
26164
2082.13
2
23294
1853.73
3
25020
1991.09
0.25
0.3
0.35
0.4
0.45
0.5
0.55
0
1000
2000
3000
4000
5000
6000
7000
8000
9000
10000
Compressive Strength and W/C Ratio on the Cement Concrete (3 Mortal Cubes)
W/C Ratio
Compressive Strength (psi)
TABLE 4: Average Cylinder Strength for All Three Groups
Group
Water/Cement
Ratio
Average Load At
Failure (lbs)
Average Compressive
Strength (psi)
1
0.67
24826
1975.65
2
0.51
41360
3291.42
3
0.38
56539
4499.36
Graph 2: This graph represents the compressive strength of the W/C Ratio for Cylinders. Findings and conclusion: Portland Cement Concrete, Water Cement Ratio (3 Mortar Cubes) (Lab 4):
In Table 2, the three mortal cubes show more strength when they have a lower water/cement ratio. Though certain mixtures may be more robust, they are not always the most cost-effective. The cube did not break into the shape of an hourglass, likely because of incomplete blending and mixing of the water/cement that is given measurements. The cubes also may not have been tampered with. The picture on figure 9 shows the cube before the compression.
0.35
0.4
0.45
0.5
0.55
0.6
0.65
0.7
0
500
1000
1500
2000
2500
3000
3500
4000
4500
5000
Compressive Strength and W/C Ratio for Cylinders
Figure 9
Compressive Strength of Cylindrical Concrete Specimens and Slump Test (Labs 5 & 6
):
The test results from the procedure show that smaller W/C ratios result in cylinders that can withstand more stress. However, there must be some threshold where insufficient water results in weaker concrete that breaks easily. Again, using more water, if possible, can be more effective. In this lab, finding a cylinder that can resist 2600 pounds of stress would require more water and less material than the most robust concrete in group three. Using the formula from the chart, the ideal W/C ratio would be 0.65, which is closer to the group 1s ratio than the other groups. The type 3 failures align with the amount of time for the concrete to cure. In figures 10 and 11 shows the cylinder’s before and after compression. Figure 11 shows the cracks diagonal to the parallel like pattern in a 7 day compressive strength.
Your preview ends here
Eager to read complete document? Join bartleby learn and gain access to the full version
- Access to all documents
- Unlimited textbook solutions
- 24/7 expert homework help
Figure 10. Before compression Figure 11. After compression
Related Documents
Related Questions
Please find the following using the graph provided.
1. Resilience (use calculated yield point)
2. Toughness
please explain the calcualtion and equation needed. Thank you!
arrow_forward
Note:-
• Do not provide handwritten solution. Maintain accuracy and quality in your answer. Take care of plagiarism.
• Answer completely.
• You will get up vote for sure.
arrow_forward
Test Specimen
4140 CF steel
6061 T6 Al
Gray Cast iron 40
FC Brass 360
Impact Energy (J or ft-lb)
48.5 ft-lb
25 ft-lb
12 ft-lb
27 ft-lb
Impact Strength (J/m
or ft-lb/in)
123.096 ft-lb/in
63.452 ft-lb/in
What is the final analysis/ overall observation from the data?
30.457 ft-lb/in
68.528 ft-lb/in
arrow_forward
Need help with this Mechanics of Materials review
arrow_forward
dear tutor please provide neat and clean and detailed answer.
dont copy from google
adress both questions well
arrow_forward
Pls help ASAP
arrow_forward
Mild steel 1
Young;s modulus 1219.5
Yield strain and stress (0.4101,500.08)
Failure stress and strain :not able to find because the given data shows the experiment did not reach the failure point.
if the material stress and strain does not reach a failure point ,what dose it means , does it means that the material is more stronger?
arrow_forward
In your summer internship, you are tasked with measuring the ultimate tensile strength of a material to determine if it meets your company’s (Superior Super Ships Inc) specification. Your boss is worried that the new low-cost supplier, Shoddy Alloys Inc, may not be reliable but it is the only way to source on-time the SS304 needed to make finishings for Jeff Bezos’ new yacht, the Black Pearl. You collect several load versus displacement curves, as illustrated below. The initial diameter of the round gauge section is 0.25 in.
You also collect the instantaneous diameter of the specimen during the test using a laser.
Using the provided data, calculate what is the ultimate tensile strength measured in this test?
arrow_forward
Department of Mechanical Engineering
PRINCIPLES OF COMPUTER AIDED ENGINEERING – MENG303
Please solve the problem by keupord
arrow_forward
1.
1100
A.
30%
B.
1.1 m
1.0 m
A
F= 255 N
0.5 m
1.5 m
DGB
WARNING! The figure is not drawn to scale. For the force in the chain CB, ca
IMAGES NOTES DISCUSS UNITS STATS HELP
PREFERENCES
Part Description
the magnitude of component
parallel to the hinge axis of the
door,
(include units with answer)
0.5 m
Answer
118.77 N
Format Check
the magnitude of the component
parallel to the edge of the door that 218.17 N
is perpendicular to the hinge axis,
(include units with answer)
Format Check
Save
25 pts.7 75%
5% try penalty
31.67 pts.95%
5% try penalty
Status
Tr
● W
#tries:
**
Tr
• W.
#tries:
arrow_forward
Figure 1 shows the tensile testing results for different materials. All specimens have an initial
diameter of 12 mm and an initial gauge length of 50 mm.
300
250
Low carbon steel
Network polymer
200
Crystalline polymer
150
Amorphous polymer
100
50
5
10
15
20
25
30
Strain (%)
Figure 1: Stress-strain curve
b. Determine the following parameters for each material:
• the tensile strength
the 0.2% offset yield strength
the modulus of elasticity
• the ductility
Stress (MPa)
LO
arrow_forward
Question 2
You are a biomedical engineer working for a small orthopaedic firm that fabricates rectangular shaped fracture
fixation plates from titanium alloy (model = "Ti Fix-It") materials. A recent clinical report documents some problems with the plates
implanted into fractured limbs. Specifically, some plates have become permanently bent while patients are in rehab and doing partial
weight bearing activities.
Your boss asks you to review the technical report that was generated by the previous test engineer (whose job you now have!) and used to
verify the design. The brief report states the following... "Ti Fix-It plates were manufactured from Ti-6Al-4V (grade 5) and machined into
solid 150 mm long beams with a 4 mm thick and 15 mm wide cross section. Each Ti Fix-It plate was loaded in equilibrium in a 4-point bending
test (set-up configuration is provided in drawing below), with an applied load of 1000N. The maximum stress in this set-up was less than the
yield stress for the…
arrow_forward
Units: mmgs
Mass = 538.9662 grams Volume = 199617.1105 cubic millimeters Surface area = 32076.7718 square millimeters
Material: 6061 Alloy
Any direction/guidance on how to make this would be greatly appreciated. Thank you!
arrow_forward
Viscosity (Pa-s)
400
1016
1014
1012
1010
108
105
104
10²
1
200
800
Borosilicate
glass
Temperature (°F)
1200 1600 2000
96% silica
glass
Working range
Melting point
400 600
Fused
silica
2400 2800 3:200
Strain point
Annealing point
Softening point
Working point
Soda-lime glass
1018
1016
1014
1012
1010
108
106
104
10²
800 1000 1200 1400 1600 1800
Temperature (°C)
Viscosity (P)
arrow_forward
Please give the detailed solution.
Don't use chatgpt for this question.
Thanks
arrow_forward
Hi can you please help me with the attached question?
arrow_forward
Stuck need help!
Problem is attached. please view attachment before answering.
Really struggling with this concept.
Please show all work so I can better understand !
Thank you so much.
arrow_forward
Don’t use ai pls
arrow_forward
How many kilograms of nickel must be added to 5.66 kg of copper to yield a liquidus temperature of 1200°C? Use Animated Figure.
kg
i
arrow_forward
Pls don’t use ai and fast :)
arrow_forward
Please help
arrow_forward
SEE MORE QUESTIONS
Recommended textbooks for you
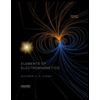
Elements Of Electromagnetics
Mechanical Engineering
ISBN:9780190698614
Author:Sadiku, Matthew N. O.
Publisher:Oxford University Press
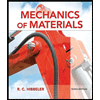
Mechanics of Materials (10th Edition)
Mechanical Engineering
ISBN:9780134319650
Author:Russell C. Hibbeler
Publisher:PEARSON
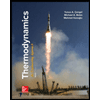
Thermodynamics: An Engineering Approach
Mechanical Engineering
ISBN:9781259822674
Author:Yunus A. Cengel Dr., Michael A. Boles
Publisher:McGraw-Hill Education
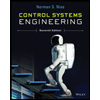
Control Systems Engineering
Mechanical Engineering
ISBN:9781118170519
Author:Norman S. Nise
Publisher:WILEY
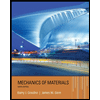
Mechanics of Materials (MindTap Course List)
Mechanical Engineering
ISBN:9781337093347
Author:Barry J. Goodno, James M. Gere
Publisher:Cengage Learning
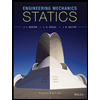
Engineering Mechanics: Statics
Mechanical Engineering
ISBN:9781118807330
Author:James L. Meriam, L. G. Kraige, J. N. Bolton
Publisher:WILEY
Related Questions
- Please find the following using the graph provided. 1. Resilience (use calculated yield point) 2. Toughness please explain the calcualtion and equation needed. Thank you!arrow_forwardNote:- • Do not provide handwritten solution. Maintain accuracy and quality in your answer. Take care of plagiarism. • Answer completely. • You will get up vote for sure.arrow_forwardTest Specimen 4140 CF steel 6061 T6 Al Gray Cast iron 40 FC Brass 360 Impact Energy (J or ft-lb) 48.5 ft-lb 25 ft-lb 12 ft-lb 27 ft-lb Impact Strength (J/m or ft-lb/in) 123.096 ft-lb/in 63.452 ft-lb/in What is the final analysis/ overall observation from the data? 30.457 ft-lb/in 68.528 ft-lb/inarrow_forward
- Mild steel 1 Young;s modulus 1219.5 Yield strain and stress (0.4101,500.08) Failure stress and strain :not able to find because the given data shows the experiment did not reach the failure point. if the material stress and strain does not reach a failure point ,what dose it means , does it means that the material is more stronger?arrow_forwardIn your summer internship, you are tasked with measuring the ultimate tensile strength of a material to determine if it meets your company’s (Superior Super Ships Inc) specification. Your boss is worried that the new low-cost supplier, Shoddy Alloys Inc, may not be reliable but it is the only way to source on-time the SS304 needed to make finishings for Jeff Bezos’ new yacht, the Black Pearl. You collect several load versus displacement curves, as illustrated below. The initial diameter of the round gauge section is 0.25 in. You also collect the instantaneous diameter of the specimen during the test using a laser. Using the provided data, calculate what is the ultimate tensile strength measured in this test?arrow_forwardDepartment of Mechanical Engineering PRINCIPLES OF COMPUTER AIDED ENGINEERING – MENG303 Please solve the problem by keupordarrow_forward
- 1. 1100 A. 30% B. 1.1 m 1.0 m A F= 255 N 0.5 m 1.5 m DGB WARNING! The figure is not drawn to scale. For the force in the chain CB, ca IMAGES NOTES DISCUSS UNITS STATS HELP PREFERENCES Part Description the magnitude of component parallel to the hinge axis of the door, (include units with answer) 0.5 m Answer 118.77 N Format Check the magnitude of the component parallel to the edge of the door that 218.17 N is perpendicular to the hinge axis, (include units with answer) Format Check Save 25 pts.7 75% 5% try penalty 31.67 pts.95% 5% try penalty Status Tr ● W #tries: ** Tr • W. #tries:arrow_forwardFigure 1 shows the tensile testing results for different materials. All specimens have an initial diameter of 12 mm and an initial gauge length of 50 mm. 300 250 Low carbon steel Network polymer 200 Crystalline polymer 150 Amorphous polymer 100 50 5 10 15 20 25 30 Strain (%) Figure 1: Stress-strain curve b. Determine the following parameters for each material: • the tensile strength the 0.2% offset yield strength the modulus of elasticity • the ductility Stress (MPa) LOarrow_forwardQuestion 2 You are a biomedical engineer working for a small orthopaedic firm that fabricates rectangular shaped fracture fixation plates from titanium alloy (model = "Ti Fix-It") materials. A recent clinical report documents some problems with the plates implanted into fractured limbs. Specifically, some plates have become permanently bent while patients are in rehab and doing partial weight bearing activities. Your boss asks you to review the technical report that was generated by the previous test engineer (whose job you now have!) and used to verify the design. The brief report states the following... "Ti Fix-It plates were manufactured from Ti-6Al-4V (grade 5) and machined into solid 150 mm long beams with a 4 mm thick and 15 mm wide cross section. Each Ti Fix-It plate was loaded in equilibrium in a 4-point bending test (set-up configuration is provided in drawing below), with an applied load of 1000N. The maximum stress in this set-up was less than the yield stress for the…arrow_forward
arrow_back_ios
SEE MORE QUESTIONS
arrow_forward_ios
Recommended textbooks for you
- Elements Of ElectromagneticsMechanical EngineeringISBN:9780190698614Author:Sadiku, Matthew N. O.Publisher:Oxford University PressMechanics of Materials (10th Edition)Mechanical EngineeringISBN:9780134319650Author:Russell C. HibbelerPublisher:PEARSONThermodynamics: An Engineering ApproachMechanical EngineeringISBN:9781259822674Author:Yunus A. Cengel Dr., Michael A. BolesPublisher:McGraw-Hill Education
- Control Systems EngineeringMechanical EngineeringISBN:9781118170519Author:Norman S. NisePublisher:WILEYMechanics of Materials (MindTap Course List)Mechanical EngineeringISBN:9781337093347Author:Barry J. Goodno, James M. GerePublisher:Cengage LearningEngineering Mechanics: StaticsMechanical EngineeringISBN:9781118807330Author:James L. Meriam, L. G. Kraige, J. N. BoltonPublisher:WILEY
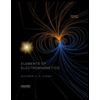
Elements Of Electromagnetics
Mechanical Engineering
ISBN:9780190698614
Author:Sadiku, Matthew N. O.
Publisher:Oxford University Press
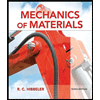
Mechanics of Materials (10th Edition)
Mechanical Engineering
ISBN:9780134319650
Author:Russell C. Hibbeler
Publisher:PEARSON
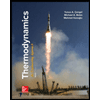
Thermodynamics: An Engineering Approach
Mechanical Engineering
ISBN:9781259822674
Author:Yunus A. Cengel Dr., Michael A. Boles
Publisher:McGraw-Hill Education
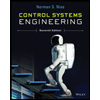
Control Systems Engineering
Mechanical Engineering
ISBN:9781118170519
Author:Norman S. Nise
Publisher:WILEY
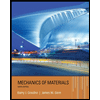
Mechanics of Materials (MindTap Course List)
Mechanical Engineering
ISBN:9781337093347
Author:Barry J. Goodno, James M. Gere
Publisher:Cengage Learning
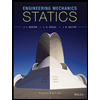
Engineering Mechanics: Statics
Mechanical Engineering
ISBN:9781118807330
Author:James L. Meriam, L. G. Kraige, J. N. Bolton
Publisher:WILEY