Discuss THREE (3) potential benefits Santa Cruz will gain once they used enter- prise application as discussed in Q2(b). (c)
Discuss THREE (3) potential benefits Santa Cruz will gain once they used enter- prise application as discussed in Q2(b). (c)
Chapter2: Planning, Implementing, And Evaluating Marketing Strategies
Section2.1: Boltbus Offers Affordable Transportation For Tech-savvy Consumers
Problem 2VC
Related questions
Question
management information system
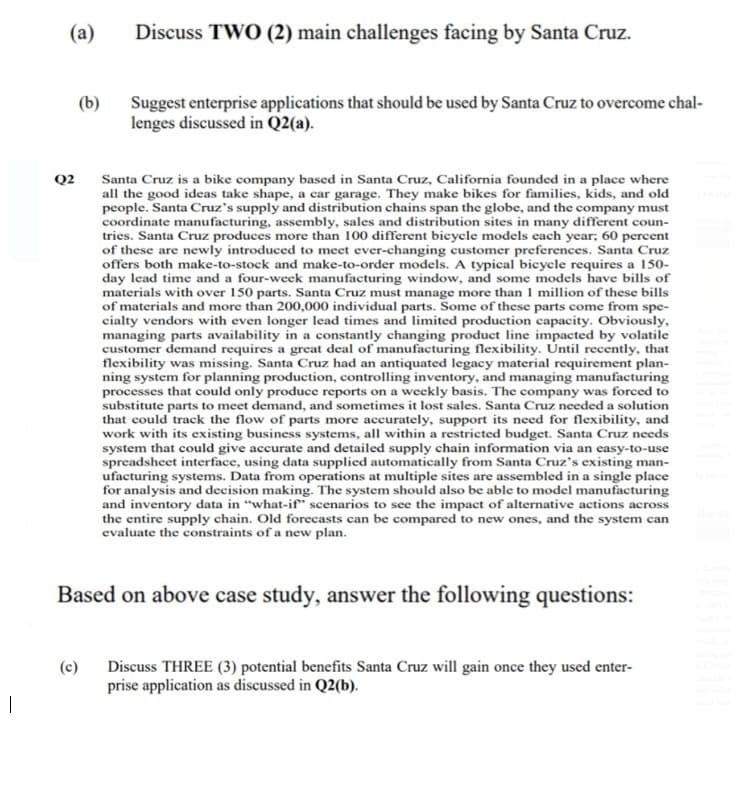
Transcribed Image Text:(a)
Discuss TWO (2) main challenges facing by Santa Cruz.
(b)
Suggest enterprise applications that should be used by Santa Cruz to overcome chal-
lenges discussed in Q2(a).
Q2
Santa Cruz is a bike company based in Santa Cruz, California founded in a place where
all the good ideas take shape, a car garage. They make bikes for families, kids, and old
people. Santa Cruz's supply and distribution chains span the globe, and the company must
coordinate manufacturing, assembly, sales and distribution sites in many different coun-
tries. Santa Cruz produces more than 100 different bicycle models each year; 60 percent
of these are newly introduced to meet ever-changing customer preferences. Santa Cruz
offers both make-to-stock and make-to-order models. A typical bicycle requires a 150-
day lead time and a four-week manufacturing window, and some models have bills of
materials with over 150 parts. Santa Cruz must manage more than 1 million of these bills
of materials and more than 200,000 individual parts. Some of these parts come from spe-
cialty vendors with even longer lead times and limited production capacity. Obviously,
managing parts availability in a constantly changing product line impacted by volatile
customer demand requires a great deal of manufacturing flexibility. Úntil recently, that
flexibility was missing. Santa Cruz had an antiquated legacy material requirement plan-
ning system for planning production, controlling inventory, and managing manufacturing
processes that could only produce reports on a weekly basis. The company was forced to
substitute parts to meet demand, and sometimes it lost sales. Santa Cruz needed a solution
that could track the flow of parts more accurately, support its need for flexibility, and
work with its existing business systems, all within a restricted budget. Santa Cruz needs
system that could give accurate and detailed supply chain information via an easy-to-use
spreadsheet interface, using data supplied automatically from Santa Cruz's existing man-
ufacturing systems. Data from operations at multiple sites are assembled in a single place
for analysis and decision making. The system should also be able to model manufacturing
and inventory data in "what-if" scenarios to see the impact of alternative actions across
the entire supply chain. Old forecasts can be compared to new ones, and the system can
evaluate the constraints of a new plan.
Based on above case study, answer the following questions:
(c) Discuss THREE (3) potential benefits Santa Cruz will gain once they used enter-
prise application as discussed in Q2(b).
|
Expert Solution

This question has been solved!
Explore an expertly crafted, step-by-step solution for a thorough understanding of key concepts.
Step by step
Solved in 4 steps

Recommended textbooks for you