Many chemical engineering process designs require heating. The process heaters and furnaces may cover a wide range of sizes and be used for a variety of purposes, including generation of steam and direct heating of reactors. Heaters and furnaces must be designed to generate the required amount of heat and to transfer it to the pace where it is needed. In addition, they must be designed to operate efficiently and safely. Most heaters use either gas of liquid fuels, but a significant fraction use solid fuels. Some use a combination fuel such as finely powdered coal suspended in oil. Regardless of the type of fuel or the rate of heat generation, most heaters and furnaces have one thing in common: somewhere in the design, there is a fire. The fire may be small or large, depending on the rate of heat generation, but the burner temperature will nearly always be very hot. Temperatures inside the furnace or heater will be above 2000oF and the walls of the furnace or heater will frequently be above 2000oF as well. Thus, the walls of the heater or furnace must be well-insulated to minimize heat loss. There is also another reason for insulating the walls. Generally, plant operators must be near the heaters or furnaces and they must be protected from the heat. Protection takes at least two considerations. First, the environment must be cool enough for operators to work in the areas for whatever time is necessary for their work. Second, even though the environment near the heater or furnace is cool, the actual surfaces may be hot enough to burn unprotected skin. A furnace is designed to reach interior wall temperatures of 2500oF. IT is lined with firebrick 4 inches thick having an average thermal conductivity of 0.2 BTU/hr-ft-oF. The firebrick is attached to a steel shell 0.25 inches thick. The temperature of the steel shell currently reaches 220oF, and workers must avoid the furnace because of the danger of being burned. A new engineer is asked to determine the thickness of a layer of insulation which will be applied to the outside of the steel shell to reduce the outside temperature to 120oF. She knows the temperature of the steel shell must not exceed 500oF because the steel will begin to weaken and the bonding agent used to attach the insulation to the steel will start to deteriorate. a) What thickness of external insulation with a thermal conductivity of 0.35 BTU/hr-ft-oF will be needed? b) By what percent will the heat loss from the furnace be reduced? c) The engineer assumes the temperature drop across the steel to be negligible because the steel layer is thin and the thermal conductivity of steel is about 25 BTU/hr-ft-oF, which is about 100 times the value for the insulating materials. Once she has determined the thickness for the outer insulation layer, she calculates the temperature drop across the steel layer. Was her assumption of negligible temperature drop valid?
Many chemical engineering process designs require heating. The process heaters and furnaces may cover a wide range of sizes and be used for a variety of purposes, including generation of steam and direct heating of reactors. Heaters and furnaces must be designed to generate the required amount of heat and to transfer it to the pace where it is needed. In addition, they must be designed to operate efficiently and safely. Most heaters use either gas of liquid fuels, but a significant fraction use solid fuels. Some use a combination fuel such as finely powdered coal suspended in oil.
Regardless of the type of fuel or the rate of heat generation, most heaters and furnaces have one thing in common: somewhere in the design, there is a fire. The fire may be small or large, depending on the rate of heat generation, but the burner temperature will nearly always be very hot. Temperatures inside the furnace or heater will be above 2000oF and the walls of the furnace or heater will frequently be above 2000oF as well. Thus, the walls of the heater or furnace must be well-insulated to minimize heat loss.
There is also another reason for insulating the walls. Generally, plant operators must be near the heaters or furnaces and they must be protected from the heat. Protection takes at least two considerations. First, the environment must be cool enough for operators to work in the areas for whatever time is necessary for their work. Second, even though the environment near the heater or furnace is cool, the actual surfaces may be hot enough to burn unprotected skin.
A furnace is designed to reach interior wall temperatures of 2500oF. IT is lined with firebrick 4 inches thick having an average thermal conductivity of 0.2 BTU/hr-ft-oF. The firebrick is attached to a steel shell 0.25 inches thick. The temperature of the steel shell currently reaches 220oF, and workers must avoid the furnace because of the danger of being burned. A new engineer is asked to determine the thickness of a layer of insulation which will be applied to the outside of the steel shell to reduce the outside temperature to 120oF. She knows the temperature of the steel shell must not exceed 500oF because the steel will begin to weaken and the bonding agent used to attach the insulation to the steel will start to deteriorate.
- a) What thickness of external insulation with a thermal conductivity of 0.35 BTU/hr-ft-oF will be needed?
- b) By what percent will the heat loss from the furnace be reduced?
- c) The engineer assumes the temperature drop across the steel to be negligible because the steel layer is thin and the thermal conductivity of steel is about 25 BTU/hr-ft-oF, which is about 100 times the value for the insulating materials. Once she has determined the thickness for the outer insulation layer, she calculates the temperature drop across the steel layer. Was her assumption of negligible temperature drop valid?

Trending now
This is a popular solution!
Step by step
Solved in 7 steps with 6 images

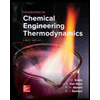
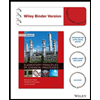
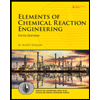
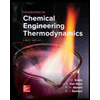
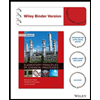
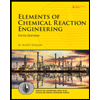
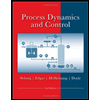
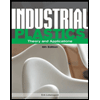
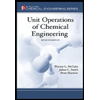