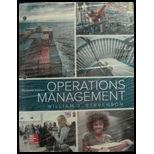
Concept explainers
Determine material requirements plans for pans N and V and subassembly I as described in Solved Problem 3 for each of the following:
a. Assume that there are currently 100 Ns on hand and scheduled receipts of 40 Is and 10 Vs at the beginning of week 3. No Es are on hand: 120 Es are needed at the start of week 5.
b. Assume on-hand and scheduled receipts as in part a. Now suppose that 100 Es are needed at the stmt of week 5 and 55 at the start of week 7. Also, use multiples of these order sizes: N, 800; V, 200. Use lot-for-lot ordering for I.
C. Using your answer to part b, update the MRP for V, using the following additional information for each of these cases: (1) one week has elapsed (making it the start of week 2), and (2) three weeks have elapsed (making it the start of week 4).
The updated master
a)

To prepare A Material requirement plan for the given information.
Introduction: Materials Requirement Planning (MRP) is the planning or scheduling system, which is used in the manufacturing process. It is used to plan the number of items required to produce one unit of finished goods (end item).
Explanation of Solution
Given information:
On-hand balances are 100 units of Component N and 0 units of Component E. Scheduled receipts is 40 units of Component I and 10 units of Component C would arrive at the beginning of Week 3. 120 units of Component E are needed at the beginning of Week 5.
Product structure tree:
Prepare master schedule:
Week | 1 | 2 | 3 | 4 | 5 | 6 | 7 | 8 |
Quantity | 120 |
Develop a material requirement planning for End item E:
- It is given that Person X has received an order to deliver 120 units of End item E, which must be shipped at the start of week 5.
- Beginning inventory is given as 0 units.
- Net requirement can be calculated by subtracting the projected on-hand from the gross requirement. Hence, the net requirement is 120 units (120-0).
- Planned order release is the order given by the company and planned order receipts is the order received by the firm.
- Lead-time is given as 1 week. Company requires 120 units in the beginning of week 5. Hence, they need to order for 120 units (as the lot size is lot-for-lot) on previous week (as the lead-time is 1 week). Thus, company need to order the required units in week 4.
Develop a material requirement planning for Component I (2):
- End item E is the parent item of Component I (2). Hence, the planned order release of E is the gross requirement for Component I (2). As number of units required is 2 for Component I, the planned order release row should be multiplied with 2 to attain the gross requirement column of Component I.
- Beginning inventory is given as 0 units.
- Scheduled receipt is 40 units at the beginning of week 3.
- Net requirement can be calculated by subtracting the projected on-hand from the gross requirement. Hence, the net requirement is 200 units on week 4 (240-40).
- Planned order release is the order given by the company and planned order receipts is the order received by the firm.
- Lead-time is given as 1 week. Company requires 200 units in the beginning of week 4. Hence, they need to order for 200 units (as the lot size is lot-for-lot) on previous week (as the lead-time is 1 week). Thus, company need to order the required units in week 3.
- Projected on hand inventory for week 5 is 0 units. Calculation is as follows:
Develop a material requirement planning for Component N (4):
- Component I (2) is the parent item of Component N (4). Hence, the planned order release of Component I (2) is the gross requirement for Component N (4). As number of units required is 4 for Component N, the planned order release row should be multiplied with 2 to attain the gross requirement column of Component N.
- Beginning inventory is given as 100 units.
- Net requirement can be calculated by subtracting the projected on-hand from the gross requirement. Hence, the net requirement is 700 units on week 3 (800-100).
- Planned order release is the order given by the company and planned order receipts is the order received by the firm.
- Lead-time is given as 2 weeks. The company requires 700 units in the beginning of week 3. Hence, they need to order for 700 units (as the lot size is lot-for-lot) two weeks before (as the lead-time is 2 weeks). Thus, company need to order the required units in week 1.
- Projected on hand inventory for week 4 is 0 units. Calculation is as follows:
Develop a material requirement planning for Component V:
- Component I (2) is the parent item of Component V. Hence, the planned order release of Component I (2) is the gross requirement for Component V. As number of units required is 1 for Component V, the planned order release row should be multiplied with 1 to attain the gross requirement column of Component V.
- Beginning inventory is given as 0 units.
- Scheduled receipt is 10 units at the beginning of week 3.
- Net requirement can be calculated by subtracting the projected on-hand from the gross requirement. Hence, the net requirement is 190 units on week 3 (200-10).
- Planned order release is the order given by the company and planned order receipts is the order received by the firm.
- Lead-time is given as 2 weeks. The company requires 700 units in the beginning of week 3. Hence, they need to order for 700 units (as the lot size is lot-for-lot) two weeks before (as the lead-time is 2 weeks). Thus, company need to order the required units in week 1.
- Projected on hand inventory for week 4 is 0 units. Calculation is as follows:
b)

To prepare A Material requirement plan for the given information.
Introduction: Materials Requirement Planning (MRP) is the planning or scheduling system, which can be used in the manufacturing process. It is used to plan the number of items required to produce one unit of finished goods (end item).
Explanation of Solution
Given information:
On-hand balances are 100 units of Component N and 0 units of Component E. Scheduled receipts is 40 units of Component I and 10 units of Component C would arrive at the beginning of week 3. 100 units of Component E are needed at the beginning of week 5 and 55 units needed at the beginning of week 7. Lot size is multiple of 800 for Component N, multiples of 200 for Component V, and lot-for-lot for Component E and Component I.
Product structure tree:
Develop a material requirement planning for End item E:
- It is given that Person X has received an order to deliver 100 units of End item E in the start of week 5 and 55 units of End item E in the start of week 7.
- Beginning inventory is given as 0 units.
- Net requirement can be calculated by subtracting the projected on-hand from the gross requirement. Hence, the net requirement is 100 units in week 5 (100-0).
- Planned order release is the order given by the company and planned order receipts is the order received by the firm.
- Lead-time is given as 1 week. Company requires 100 units in the beginning of Week 5. Hence, they need to order for 100 units (as the lot size is lot-for-lot) on previous week (as the lead-time is 1 week). Thus, company need to order the required units in week 4.
Develop a material requirement planning for Component I (2):
- End item E is the parent item of Component I (2). Hence, the planned order release of E is the gross requirement for Component I (2). As number of units required is 2 for Component I, the planned order release row should be multiplied with 2 to attain the gross requirement column of Component I.
- Beginning inventory is given as 0 units.
- Scheduled receipt is 40 units at the beginning of week 3.
- Net requirement can be calculated by subtracting the projected on-hand from the gross requirement. Hence, the net requirement is 160 units on week 4 (200-40).
- Planned order release is the order given by the company and planned order receipts is the order received by the firm.
- Lead-time is given as 1 week. Company requires 160 units in the beginning of week 4. Hence, they need to order for 160 units (as the lot size is lot-for-lot) on previous week (as the lead-time is 1 week). Thus, company need to order the required units in week 3.
- Projected on hand inventory for week 5 is 0 units. Calculation is as follows:
Develop a material requirement planning for Component N (4):
- Component I (2) is the parent item of Component N (4). Hence, the planned order release of Component I (2) is the gross requirement for Component N (4). As number of units required is 4 for Component N, the planned order release row should be multiplied with 2 to attain the gross requirement column of Component N.
- Beginning inventory is given as 100 units.
- Net requirement can be calculated by subtracting the projected on-hand from the gross requirement. Hence, the net requirement is 540 units on week 3 (640-100).
- Planned order release is the order given by the company and planned order receipts is the order received by the firm.
- Lead-time is given as 2 weeks. The company requires 540 units in the beginning of week 3. Hence, they need to order for 800 units (as the lot size is multiples of 800) two weeks before (as the lead-time is 2 weeks). Thus, company need to order the required units in week 1.
- Projected on hand inventory for week 4 is 260 units. Calculation is as follows:
- Projected on hand inventory for week 6 is 620 units. Calculation is as follows:
Develop a material requirement planning for Component V:
- Component I (2) is the parent item of Component V. Hence, the planned order release of Component I (2) is the gross requirement for Component V. As number of units required is 1 for Component V, the planned order release row should be multiplied with 1 to attain the gross requirement column of Component V.
- Beginning inventory is given as 0 units.
- Scheduled receipt is 10 units at the beginning of week 3.
- Net requirement can be calculated by subtracting the projected on-hand from the gross requirement. Hence, the net requirement is 150 units on week 3 (160-10).
- Planned order release is the order given by the company and planned order receipts is the order received by the firm.
- Lead-time is given as 2 weeks. The company requires 150 units in the beginning of week 3. Hence, they need to order for 200 units (as the lot size is multiples of 200) two weeks before (as the lead-time is 2 weeks). Thus, company need to order the required units in week 1.
- Projected on hand inventory for week 4 is 50 units. Calculation is as follows:
- Projected on hand inventory for week 6 is 140 units. Calculation is as follows:
c)
1)

To prepare: Material requirement plan for the given information.
Introduction: Materials Requirement Planning (MRP) is the planning or scheduling system, which can be used in the manufacturing process. It is used to plan the number of items required to produce one unit of finished goods (end item).
Explanation of Solution
Given information:
On-hand balances are 100 units of Component N and 0 units of Component E. Scheduled receipts is 800 units of Component N and 200 units of Component V would arrive at the beginning of week 3. Lot size is multiple of 800 for Component N, multiples of 200 for Component V, and lot-for-lot for Component E and Component I.
Week 1 has elapsed. Hence, plan has to be prepared from week 2 through week 9. 100 units of Component E are needed at the beginning of week 5 and 55 units needed at the beginning of week 7. In addition to that, 100 units of End item E are needed in week 9.
Product structure tree:
Develop a material requirement planning for End item E:
- It is given that Person X has received an order to deliver 100 units of End item E in week 5, 55 units in week 7, and 100 units in week 9.
- Beginning inventory is given as 0 units.
- Net requirement can be calculated by subtracting the projected on-hand from the gross requirement. Hence, the net requirement is 100 units (100-0).
- Planned order release is the order given by the company and planned order receipts is the order received by the firm.
- Lead-time is given as 1 week. Company requires 100 units in the beginning of week 5. Hence, they need to order for 100 units (as the lot size is lot-for-lot) on previous week (as the lead-time is 1 week). Thus, company need to order the required units in week 4.
Develop a material requirement planning for Component I (2):
- End item E is the parent item of Component I (2). Hence, the planned order release of E is the gross requirement for Component I (2). As number of units required is 2 for Component I, the planned order release row should be multiplied with 2 to attain the gross requirement column of Component I.
- Beginning inventory is given as 0 units.
- Scheduled receipt is 40 units at the beginning of week 3.
- Net requirement can be calculated by subtracting the projected on-hand from the gross requirement. Hence, the net requirement is 160 units on week 4 (200-40).
- Planned order release is the order given by the company and planned order receipts is the order received by the firm.
- Lead-time is given as 1 week. Company requires 160 units in the beginning of week 4. Hence, they need to order for 160 units (as the lot size is lot-for-lot) on previous week (as the lead-time is 1 week). Thus, company need to order the required units in week 3.
- Projected on hand inventory for week 5 is 0 units. Calculation is as follows:
Develop a material requirement planning for Component N (4):
- Component I (2) is the parent item of Component N (4). Hence, the planned order release of Component I (2) is the gross requirement for Component N (4). As number of units required is 4 for Component N, the planned order release row should be multiplied with 2 to attain the gross requirement column of Component N.
- Beginning inventory is given as 100 units.
- Scheduled receipt is 800 units at the beginning of week 3
- Net requirement can be calculated by subtracting the projected on-hand from the gross requirement. Hence, the net requirement is 180 units on week 5 (440-260).
- Planned order release is the order given by the company and planned order receipts is the order received by the firm.
- Lead-time is given as 2 weeks. The company requires 180 units in the beginning of week 5. Hence, they need to order for 800 units (as the lot size is multiples of 800) two weeks before (as the lead-time is 2 weeks). Thus, company need to order the required units in week 3.
- Projected on hand inventory for week 4 is 260 units. Calculation is as follows:
- Projected on hand inventory for week 6 is 620 units. Calculation is as follows:
Develop a material requirement planning for Component V:
- Component I (2) is the parent item of Component V. Hence, the planned order release of Component I (2) is the gross requirement for Component V. As number of units required is 1 for Component V, the planned order release row should be multiplied with 1 to attain the gross requirement column of Component V.
- Beginning inventory is given as 0 units.
- Scheduled receipt is 210 units at the beginning of week 3.
- Net requirement can be calculated by subtracting the projected on-hand from the gross requirement. Hence, the net requirement is 60 units on week 5 (110-50).
- Planned order release is the order given by the company and planned order receipts is the order received by the firm.
- Lead-time is given as 2 weeks. The company requires 700 units in the beginning of week 3. Hence, they need to order for 700 units (as the lot size is lot-for-lot) two weeks before (as the lead-time is 2 weeks). Thus, company need to order the required units in week 1.
- Projected on hand inventory for week 4 is 50 units. Calculation is as follows:
- Projected on hand inventory for week 6 is 140 units. Calculation is as follows:
1)

To prepare: Material requirement plan for the given information.
Introduction: Materials Requirement Planning (MRP) is the planning or scheduling system, which can be used in the manufacturing process. It is used to plan the number of items required to produce one unit of finished goods (end item).
Explanation of Solution
Given information:
On-hand balances are 100 units of Component N and 0 units of Component E. Scheduled receipts is 800 units of Component N and 200 units of Component V would arrive at the beginning of week 3. Lot size is multiple of 800 for Component N, multiples of 200 for Component V, and lot-for-lot for Component E and Component I.
Week 1 has elapsed. Hence, plan has to be prepared from week 2 through week 9. 100 units of Component E are needed at the beginning of week 5 and 55 units needed at the beginning of week 7. In addition to that, 100 units of End item E are needed in week 9.
Product structure tree:
Develop a material requirement planning for End item E:
- It is given that Person X has received an order to deliver 100 units of End item E in week 5, 55 units in week 7, and 100 units in week 9.
- Beginning inventory is given as 0 units.
- Net requirement can be calculated by subtracting the projected on-hand from the gross requirement. Hence, the net requirement is 100 units (100-0).
- Planned order release is the order given by the company and planned order receipts is the order received by the firm.
- Lead-time is given as 1 week. Company requires 100 units in the beginning of week 5. Hence, they need to order for 100 units (as the lot size is lot-for-lot) on previous week (as the lead-time is 1 week). Thus, company need to order the required units in week 4.
Develop a material requirement planning for Component I (2):
- End item E is the parent item of Component I (2). Hence, the planned order release of E is the gross requirement for Component I (2). As number of units required is 2 for Component I, the planned order release row should be multiplied with 2 to attain the gross requirement column of Component I.
- Beginning inventory is given as 0 units.
- Scheduled receipt is 40 units at the beginning of week 3.
- Net requirement can be calculated by subtracting the projected on-hand from the gross requirement. Hence, the net requirement is 160 units on week 4 (200-40).
- Planned order release is the order given by the company and planned order receipts is the order received by the firm.
- Lead-time is given as 1 week. Company requires 160 units in the beginning of week 4. Hence, they need to order for 160 units (as the lot size is lot-for-lot) on previous week (as the lead-time is 1 week). Thus, company need to order the required units in week 3.
- Projected on hand inventory for week 5 is 0 units. Calculation is as follows:
Develop a material requirement planning for Component N (4):
- Component I (2) is the parent item of Component N (4). Hence, the planned order release of Component I (2) is the gross requirement for Component N (4). As number of units required is 4 for Component N, the planned order release row should be multiplied with 2 to attain the gross requirement column of Component N.
- Beginning inventory is given as 100 units.
- Scheduled receipt is 800 units at the beginning of week 3
- Net requirement can be calculated by subtracting the projected on-hand from the gross requirement. Hence, the net requirement is 180 units on week 5 (440-260).
- Planned order release is the order given by the company and planned order receipts is the order received by the firm.
- Lead-time is given as 2 weeks. The company requires 180 units in the beginning of week 5. Hence, they need to order for 800 units (as the lot size is multiples of 800) two weeks before (as the lead-time is 2 weeks). Thus, company need to order the required units in week 3.
- Projected on hand inventory for week 4 is 260 units. Calculation is as follows:
- Projected on hand inventory for week 6 is 620 units. Calculation is as follows:
Develop a material requirement planning for Component V:
- Component I (2) is the parent item of Component V. Hence, the planned order release of Component I (2) is the gross requirement for Component V. As number of units required is 1 for Component V, the planned order release row should be multiplied with 1 to attain the gross requirement column of Component V.
- Beginning inventory is given as 0 units.
- Scheduled receipt is 210 units at the beginning of week 3.
- Net requirement can be calculated by subtracting the projected on-hand from the gross requirement. Hence, the net requirement is 60 units on week 5 (110-50).
- Planned order release is the order given by the company and planned order receipts is the order received by the firm.
- Lead-time is given as 2 weeks. The company requires 700 units in the beginning of week 3. Hence, they need to order for 700 units (as the lot size is lot-for-lot) two weeks before (as the lead-time is 2 weeks). Thus, company need to order the required units in week 1.
- Projected on hand inventory for week 4 is 50 units. Calculation is as follows:
- Projected on hand inventory for week 6 is 140 units. Calculation is as follows:
2)

To prepare: Material requirement plan for the given information.
Introduction: Materials Requirement Planning (MRP) is the planning or scheduling system, which can be used in the manufacturing process. It is used to plan the number of items required to produce one unit of finished goods (end item).
Explanation of Solution
Given information:
On-hand balances are 100 units of Component N and 0 units of Component E. Lot size is multiple of 800 for Component N, multiples of 200 for Component V, and lot-for-lot for Component E and Component I.
Two weeks (week 2 and week 3) has elapsed. Hence, plan has to be prepared from week 4 through week 11. 100 units of Component E are needed at the beginning of week 5 and 55 units needed at the beginning of week 7. In addition to that, 100 units of End item E are needed in week 9.
Planned order releases from 2nd and 3rd week should be used as scheduled receipt units. Scheduled receipt are 160 units of Component I at the start of 4th week, 800 units of Component N at the start of 5th week, and 200 units of Component V at the start of 5th week.
Product structure tree:
Develop a material requirement planning for End item E:
- It is given that Person X has received an order to deliver 100 units of End item E in week 5, 55 units in week 7, and 100 units in week 9.
- Beginning inventory is given as 0 units.
- Net requirement can be calculated by subtracting the projected on-hand from the gross requirement. Hence, the net requirement is 100 units at week 5 (100-0).
- Planned order release is the order given by the company and planned order receipts is the order received by the firm.
- Lead-time is given as 1 week. Company requires 100 units in the beginning of week 5. Hence, they need to order for 100 units (as the lot size is lot-for-lot) on previous week (as the lead-time is 1 week). Thus, company need to order the required units in week 4.
Develop a material requirement planning for Component I (2):
- End item E is the parent item of Component I (2). Hence, the planned order release of E is the gross requirement for Component I (2). As number of units required is 2 for Component I, the planned order release row should be multiplied with 2 to attain the gross requirement column of Component I.
- Beginning inventory is given as 40 units.
- Scheduled receipt is 160 units at the beginning of week 4.
- Net requirement can be calculated by subtracting the projected on-hand from the gross requirement. Hence, the net requirement is 100 units on week 6 (110-0).
- Planned order release is the order given by the company and planned order receipts is the order received by the firm.
- Lead-time is given as 1 week. Company requires 110 units in the beginning of week 6. Hence, they need to order for 110 units (as the lot size is lot-for-lot) on previous week (as the lead-time is 1 week). Thus, company need to order the required units in week 5.
- Projected on hand inventory for week 5 is 0 units. Calculation is as follows:
Develop a material requirement planning for Component N (4):
- Component I (2) is the parent item of Component N (4). Hence, the planned order release of Component I (2) is the gross requirement for Component N (4). As number of units required is 4 for Component N, the planned order release row should be multiplied with 2 to attain the gross requirement column of Component N.
- Beginning inventory is given as 260 units.
- Scheduled receipt is 800 units at the beginning of week 3
- Net requirement can be calculated by subtracting the projected on-hand from the gross requirement. Hence, the net requirement is 180 units on week 7 (800-620).
- Planned order release is the order given by the company and planned order receipts is the order received by the firm.
- Lead-time is given as 2 weeks. The company requires 180 units in the beginning of week 7. Hence, they need to order for 800 units (as the lot size is multiples of 800) two weeks before (as the lead-time is 2 weeks). Thus, company need to order the required units in week 5.
- Projected on hand inventory for week 5 is 1,060 units. Calculation is as follows:
- Projected on hand inventory for week 6 is 620 units. Calculation is as follows:
Develop a material requirement planning for Component V:
- Component I (2) is the parent item of Component V. Hence, the planned order release of Component I (2) is the gross requirement for Component V. As number of units required is 1 for Component V, the planned order release row should be multiplied with 1 to attain the gross requirement column of Component V.
- Beginning inventory is given as 50 units.
- Scheduled receipt is 200 units at the beginning of week 5.
- Net requirement can be calculated by subtracting the projected on-hand from the gross requirement. Hence, the net requirement is 60 units on week 7 (200-140).
- Planned order release is the order given by the company and planned order receipts is the order received by the firm.
- Lead-time is given as 2 weeks. The company requires 60 units in the beginning of week 7. Hence, they need to order for 200 units (as the lot size is multiples of 200) two weeks before (as the lead-time is 2 weeks). Thus, company need to order the required units in week 5.
- Projected on hand inventory for week 6 is 140 units. Calculation is as follows:
Want to see more full solutions like this?
Chapter 12 Solutions
OPERATIONS MANAGEMENT (LL) >CUSTOM<
Additional Business Textbook Solutions
Business in Action (8th Edition)
Principles of Operations Management: Sustainability and Supply Chain Management (10th Edition)
Principles Of Operations Management
Operations Management: Processes and Supply Chains (11th Edition)
OPERATIONS MANAGEMENT IN THE SUPPLY CHAIN: DECISIONS & CASES (Mcgraw-hill Series Operations and Decision Sciences)
Operations Management: Sustainability and Supply Chain Management (12th Edition)
- A partially completed inventory record for the motor subassembly is shown in Figure.a. Complete the last three rows of the record by using the L4L rule.b. Complete the last three rows of the record by using the POQ rule with P = 2.c. Complete the last three rows of the record by using the POQ rule with P = 2.d. If it costs the company $1 to hold a unit in inventory from one week to the next, and the cost to release an order is $50, which of the lot sizing rules used above will provide the lowest inventory holding + order release cost?arrow_forwardA partially completed inventory record for the motor sub-assembly is shown in Figure 11.39. a. Complete the last three rows of the record by using the L4L rule. b. Complete the last three rows of the record by using the POQ rule with P = 2. c. Complete the last three rows of the record by using the POQ rule with P = 2. d. If it costs the company $1 to hold a unit in inventory from one week to the next, and the cost to release an order is $50, which of the lot sizing rules used above will provide the lowest inventory holding + order release cost?arrow_forwardUsing the information in Problem (The demand for subassembly Sis 100 units in week 7.Each unit ofS requires 1 unit ofT and 2 units ofU. Each unit ofT requires I unit ofY, 2 units ofW, and 1 unit of X. Finally, eachunit of U requires 2 units of Y and 3 units of Z. One firm manufacturesall items. It takes 2 weeks to make S, 1 week to make T, 2 weeks to make U, 2 weeks to make Y, 3 weeks to make W,I week to make X, 2 weeks to make Y, and I week to make Z.a) Construct a product structure. Identify all levels, parents, and components.b) Prepare a time-phased product structure. ), construct a netmaterial requirements plan using the following on-hand inventory.arrow_forward
- The demand for subassembly Sis 100 units in week 7.Each unit ofS requires 1 unit ofT and 2 units ofU. Each unit ofT requires I unit ofY, 2 units ofW, and 1 unit of X. Finally, eachunit of U requires 2 units of Y and 3 units of Z. One firm manufacturesall items. It takes 2 weeks to make S, 1 week to make T, 2 weeks to make U, 2 weeks to make Y, 3 weeks to make W,I week to make X, 2 weeks to make Y, and I week to make Z.a) Construct a product structure. Identify all levels, parents, and components.b) Prepare a time-phased product structure.arrow_forwardThe MRP Department has a problem. Its computer “died” just as it spit out the following information: Planned order release for item J27 = 640 units in week 2. The firm has been able toreconstruct all the information they lost except the master schedule for end item 565. The firm isfortunate because J27 is used only in 565s. Given the following product structure tree and associated inventory status record information, determine what master schedule entry for 565 wasexploded into the material requirements plan that killed the computer.arrow_forwardGiven the product structure, master productionschedule, and inventory status in Figure 14.13, and assuming therequirements for each BOM item is I:a) develop a gross requirements plan for Item C;b) develop a net requirements plan for Item C.arrow_forward
- Montague Composite makes a unit A, which consists of two units of B, three units of C, and four units of D. C is composed of three units of D and two units of E. Items A, C, D and E have on-hand inventories of 10, 20, 30 and 40 units respectively. Item B has a scheduled receipt of 50 units in period 1, and C has a scheduled receipt of 90 units in period 1. Lot-for-lot sizing is used for items A and B. Item C requires a minimum lot size of 60 units. D and E must be purchased in multiples of 35 and 55 respectively. Lead times are one period for items A, B and C, and two periods for items D and E. The gross requirements for A are 180 in period 5, and 220 in period 8. Determine the planned-order releases for all items using template 2 (provided at the end of the paper)arrow_forwardA firm that produces electric golf carts has just received an order for 200 carts, which must be ready for delivery at the start of week 8. Information concerning the product structure, lead times, and quantities on hand is shown in the following table. Use this information to do each of the following: a. Develop a material requirements plan that will provide 200 golf carts by week 8, assuming lot-for-lot ordering. (Excel)arrow_forwardA table is assembled using three components, as shown in the accompanying product structure tree.The company that makes the table wants to ship 100 units at the beginning of day 4, 150 units atthe beginning of day 5, and 200 units at the beginning of day 7. Receipts of 100 wood sections arescheduled at the beginning of day 2. There are 120 legs on hand. There are 60 braces on hand. Leadtimes (in days) for all items are shown in the following table. Prepare a material requirements planusing lot-for-lot ordering.arrow_forward
- Heather Adams, production manager for a Colorado exercise equipment manufacturer, needs to schedule an order for 50 UltimaSteppers, which are to be shipped in week 8. Assume lot-for- lot ordering. Below is information about the steppers and the quantity required for each parent. Item Lead Time On Hand Inventory Components Stepper 2 20 A(1), B(3), C(2) A 1 10 D(1), F(2) B 2 30 E(1), F(3) C 3 10 D(2), E(3) D 1 15 E 2 5 F 2 20 Develop a product structure diagram for Develop a net material requirements plan forarrow_forwardIn a MRP problem, A is a MPS item. Every A requires 2 B’s and 3 C’s. Every B requires 5 C’s. All lead times are two periods. All initial inventory values are 0. Use lot-for-lot method for order quantities for all items. What is the low level code (LLC) for B and C?arrow_forwardFigure 11.38 shows a partially completed inventory recordfor the real wheel subassembly. Gross requirements, sched-uled receipts, lead time, and current on-hand inventory areshown.a. Complete the last three rows of the record for an FOQ of200 units. b. Complete the last three rows of the record by using anFOQ of 100 units.c. Complete the last three rows of the record by using theL4L rule.arrow_forward
- Practical Management ScienceOperations ManagementISBN:9781337406659Author:WINSTON, Wayne L.Publisher:Cengage,Operations ManagementOperations ManagementISBN:9781259667473Author:William J StevensonPublisher:McGraw-Hill EducationOperations and Supply Chain Management (Mcgraw-hi...Operations ManagementISBN:9781259666100Author:F. Robert Jacobs, Richard B ChasePublisher:McGraw-Hill Education
- Purchasing and Supply Chain ManagementOperations ManagementISBN:9781285869681Author:Robert M. Monczka, Robert B. Handfield, Larry C. Giunipero, James L. PattersonPublisher:Cengage LearningProduction and Operations Analysis, Seventh Editi...Operations ManagementISBN:9781478623069Author:Steven Nahmias, Tava Lennon OlsenPublisher:Waveland Press, Inc.
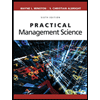
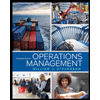
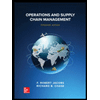
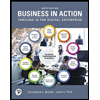
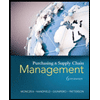
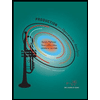