OPERATIONS MGMT - FIRST DAY
2018th Edition
ISBN: 9780135391242
Author: HEIZER
Publisher: PEARSON
expand_more
expand_more
format_list_bulleted
Question
Chapter 13, Problem 5P
Summary Introduction
To evaluate: Plan C
Introduction: The aggregate plan is the output of sales and operations planning. The major concern of aggregate planning is the production time and quantity for the intermediate future. Aggregate planning would encompass a time prospect of approximately 3 to 18 months.
Expert Solution & Answer

Want to see the full answer?
Check out a sample textbook solution
Students have asked these similar questions
QUESTION ONEProduct X is made of two units of Y and three units of Z. Y is made of one unit of A and two units of B. Z is made of two units of A and four units of C. the lead time for each material is given in table 1.Table 1. Lead time Components X 1Y 2Z 3A 2B 1C 3
Required;a) Construct the bill of material (BOM)b) If 100 units of X are required, how many units of each components areneeded? c) Develop a time-phased product structure, showing when each item shouldbe ordered. And in what quantity? d) Develop Gross Requirements Plan for each component.
QUESTION THREEa) Zambia Breweries has a backlog of 250 crates of Fanta drinks at the end of December. The demand of Fanta drinks is expected to be 400 crates in January, 500 crates in February and 550 crates in March. Each worker can produce 50 crates of drinks per month with regular wage costing the company K10 000 per worker per month. Hiring cost has been calculated to be K25 000 per. Hiring cost has also been calculated to be K50 000 per worker. Backlog cost have been determined to cost the company K250 per worker. There are no cost associated with carrying the inventory.
Develop a level of production plan (aggregate plan) and determine the cost.
b) Explain why aggregate planning is necessary in production and operation management.c) Define the meaning and what happens at each of these aggregate capacity planning;i) Matching Demand approachii) Level Capacity approach.
Q3
The numbers for March are correct.
Cost table:
LayoffHiringInventory
Totals: 36 36 55,209
Costs: $54,000 $162,000 $165,627
Cost of plan:$381,627
Planning values
Starting inventory: 3,000
Starting and ending workforce: 214
Hours worked per month per hour: 240
Hours per unit: 30
Hiring cost per worker: $4,500
Layoff cost per worker: $1,500
Monthly per-unit holding cost: $3
Forecasted sales:
Month Forecasted salesMarch 1,649April 1,427May 1,137June 976July 1,531August 1,976September 2,470October 2,529November 3,016December 2,910January 2,434February 1,945
Chapter 13 Solutions
OPERATIONS MGMT - FIRST DAY
Ch. 13 - Prob. 1DQCh. 13 - Why are SOP teams typically cross-functional?Ch. 13 - Prob. 3DQCh. 13 - Prob. 4DQCh. 13 - Prob. 5DQCh. 13 - Prob. 6DQCh. 13 - Question: 7. What is level scheduling? What is the...Ch. 13 - Question: 8. Define mixed strategy. Why would a...Ch. 13 - Prob. 9DQCh. 13 - Prob. 10DQ
Ch. 13 - Question: 11. What is the relationship between the...Ch. 13 - Prob. 12DQCh. 13 - Question: 13. What are major limitations of using...Ch. 13 - Prob. 14DQCh. 13 - Question: 13.1 Prepare a graph of the monthly...Ch. 13 - Prob. 2PCh. 13 - The president of Hill Enterprises, Terri Hill,...Ch. 13 - Prob. 4PCh. 13 - Prob. 5PCh. 13 - Prob. 6PCh. 13 - Prob. 7PCh. 13 - Prob. 8PCh. 13 - Prob. 9PCh. 13 - Question: 13.10 The SOP team (see Problem 13.9)...Ch. 13 - Prob. 11PCh. 13 - Prob. 12PCh. 13 - Prob. 13PCh. 13 - Question: 13.14 Jerusalem Medical Ltd., an...Ch. 13 - Prob. 15PCh. 13 - Prob. 16PCh. 13 - Prob. 17PCh. 13 - Question: 13.18 Jose Martinez of El Paso has...Ch. 13 - Prob. 19PCh. 13 - Prob. 24PCh. 13 - Prob. 25PCh. 13 - Prob. 26PCh. 13 - Prob. 1CSCh. 13 - Prob. 2CSCh. 13 - Prob. 1VCCh. 13 - Prob. 2VCCh. 13 - Question: 3. What are some concerns the team needs...
Knowledge Booster
Similar questions
- QUESTION: Present a closing statement explaining the benefits to Stayer of applying activity-based costing to its R&D activity for both in-house and outside charging purposes.arrow_forwardDiscussion Question: Discuss the requirements for strategic management of IS/IT. What are some challenges to implementing these requirements?arrow_forwardquestion: How much profit is added if you are given an additional 50 Yards of Material?arrow_forward
- Question 1 choose 1 solution: You've had a lot on your plate lately, and I know it's been stressful. So how will your plan help you to get back to a better work/life balance? Option 1: I think the best thing I can do at this point is take my vacation. I've been working late almost every night for weeks now, and things aren't slowing down. I considered cancelling or postponing the trip, but it makes more sense for me to go away and come back refreshed. Option 2: By setting you up as the point of contact, I'll make sure that people know who to go to when I'm away. I toyed with handing out my cell number and making myself available for calls, but that seemed like a mistake. This way, the team has leadership they can turn to, and I can still take my vacation. Both sides are covered. Option 3: I'm going to focus on keeping on task and putting things in perspective. You know, prioritizing issues that come up and exercising a little mental discipline to remind myself that the situation…arrow_forwardpart 2 solution neededarrow_forwardQuestion-2- Hershey Chocolate Corporation was the first company that produced milk chocolate in America. With the passage to time, it focused only on chocolate production, and manufactured many innovative products. After the Second World War, it managed to export its products to 90 countries. In2006, its sales reached 5 billion dollars, and employed over 14,300 people. The objective of the project is to deploy an ERP system covering sales and procurement process. The following is the required schedule of the event. (Marks-10) Activity Duration- Weeks Immediate Predecessors A–Select consultant for selecting system 2 _____________ B–Meet with consultant to discuss ERP 4 A C–Meet with Board of Directors to explain proposal 1 A D–Develop request for proposals to give to vendors 3 B,C E–Obtain vendor proposals 4 D F–Develop organization business cases including training 8 E G–Present business cases to Board of Directors 1…arrow_forward
- Question 3 List any five (5) costs prevalent in aggregate planning in the motor car industry.arrow_forwardQ.14 At M3 Marketing a new marketing campaign development project for a client begins with two activities ideation and budgeting/contracting. Ideation, or coming up with ideas for the campaign, occurs in parallel with (i.e., at the same time as,) the budgeting/contracting work which determines the costs and terms of the relationship. These activities take four and three weeks, respectively. Once ideation is complete, advertising content drafting begins and lasts two weeks. When the budget is set and the ad drafting is complete, the activity to determine the advertising channels can begin. Determining the ad channels takes three weeks. When ad drafting is complete and the advertising channels are determined, two activities can start. First, final campaign collateral can be developed over the next six weeks. The second activity is rollout planning, which requires four weeks. After collateral development and rollout planning are finished, the advertising campaign rollout is executed over…arrow_forwardQuestion 1 Part 1 Read the case below and answer true/false Case Assignment: CEC Entertainment, Inc (Chuck E. Cheese’s)For more than 35 years, Chuck E. Cheese’s has been one of the nation’s go-to venues for children’s birthday parties and rainy afternoon outings. Operating under the slogan “Where a kid can be a kid,” there are more than 575 Chuck E. Cheese’s locations in 47 states and 10 foreign countries or territories. Their goal is to provide a fun and safe environment for children to play and families to create memories, but in 2015 Chuck E. Cheese’s made improvements notfor the children, but for the parents. “Your average kid who comes to Chuck E. wants to come 11 times a year; they come three times a year. The difference between that and the 11 times a year they want to come is the mom and dad veto,” said Tom Leverton, CEO of CEC Entertainment, Inc. “What we’ve been doing over the past couple of years especially is trying to address the mom and dad…arrow_forward
- Q2) 3. What is long range plan?arrow_forwardQuestion 4 If Standard output is 140 units, X has completed 110 units, Y has completed: 125 units, Z has completed: 165 units, standard rate is 30 taka/unit then what would be their wage based on Taylor and Merrick’s plan? Identify similarities and dissimilarities of the above-mentioned plan.arrow_forwardQuestion Consider the following transactions occurring during a given fortnight. Remi's wage for his casual job is $600, paid on his bank transaction account (transaction 1); his scholarship allowance for studying is $150, paid on his bank transaction account (transaction 2); he pays a rent of $250 through a bank account transfer (transaction 3); the coupons on his portfolio of bonds pays $70 on his transaction account (transaction 4); he receives $350 in his transaction account for selling shares he had bought at $300 (transaction 5); he buys a TV worth $920 with his debit card (transaction 6). Draw Remi's balance sheet and represent how the six transactions above have affected it. Use one single balance sheet, indicate the value of the variations (sign followed by a number) and use only one name for each item [example: equity name appears only once even if several transactions are under equity] No explanations are required. How much of the funding of the TV comes from…arrow_forward
arrow_back_ios
SEE MORE QUESTIONS
arrow_forward_ios
Recommended textbooks for you
- Practical Management ScienceOperations ManagementISBN:9781337406659Author:WINSTON, Wayne L.Publisher:Cengage,Operations ManagementOperations ManagementISBN:9781259667473Author:William J StevensonPublisher:McGraw-Hill EducationOperations and Supply Chain Management (Mcgraw-hi...Operations ManagementISBN:9781259666100Author:F. Robert Jacobs, Richard B ChasePublisher:McGraw-Hill Education
- Purchasing and Supply Chain ManagementOperations ManagementISBN:9781285869681Author:Robert M. Monczka, Robert B. Handfield, Larry C. Giunipero, James L. PattersonPublisher:Cengage LearningProduction and Operations Analysis, Seventh Editi...Operations ManagementISBN:9781478623069Author:Steven Nahmias, Tava Lennon OlsenPublisher:Waveland Press, Inc.
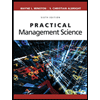
Practical Management Science
Operations Management
ISBN:9781337406659
Author:WINSTON, Wayne L.
Publisher:Cengage,
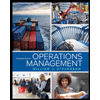
Operations Management
Operations Management
ISBN:9781259667473
Author:William J Stevenson
Publisher:McGraw-Hill Education
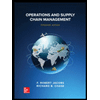
Operations and Supply Chain Management (Mcgraw-hi...
Operations Management
ISBN:9781259666100
Author:F. Robert Jacobs, Richard B Chase
Publisher:McGraw-Hill Education
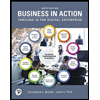
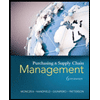
Purchasing and Supply Chain Management
Operations Management
ISBN:9781285869681
Author:Robert M. Monczka, Robert B. Handfield, Larry C. Giunipero, James L. Patterson
Publisher:Cengage Learning
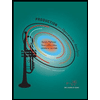
Production and Operations Analysis, Seventh Editi...
Operations Management
ISBN:9781478623069
Author:Steven Nahmias, Tava Lennon Olsen
Publisher:Waveland Press, Inc.