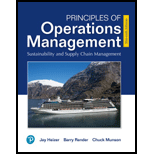
Concept explainers
a)
To evaluate: Plan D
Introduction: The aggregate plan is the output of sales and operations planning. The major concern of aggregate planning is the production time and quantity for the intermediate future. Aggregate planning would encompass a time prospect of approximately 3 to 18 months.
a)

Answer to Problem 6P
Plan D has been evaluated. The total cost of plan D is $128,000.
Explanation of Solution
Given information:
The production for all the months is 1,600 units. Overtime cost is $50 per unit. The maximum allowable inventor in the warehouse is 400 units or less. The demand requirement from period 0 to 8 is as follows:
Period | Expected demand |
0 | 0 |
1 | 1,400 |
2 | 1,600 |
3 | 1,800 |
4 | 1,800 |
5 | 2,200 |
6 | 2,200 |
7 | 1,800 |
8 | 1,800 |
Evaluate the cost of the plan:
Plan D | ||||||
Period | Demand | Production | Overtime (units) | Ending inventory | Stock-outs (units) | Extra cost |
0 | 200 | |||||
1 | 1,400 | 1,600 | - | 400 | $8,000 | |
2 | 1,600 | 1,600 | - | 400 | $8,000 | |
3 | 1,800 | 1,600 | - | 200 | $4,000 | |
4 | 1,800 | 1,600 | - | - | $0 | |
5 | 2,200 | 1,600 | 320 | - | 280 | $44,000 |
6 | 2,200 | 1,600 | 320 | - | 280 | $44,000 |
7 | 1,800 | 1,600 | 200 | - | $10,000 | |
8 | 1,800 | 1,600 | 200 | - | $10,000 | |
Total | 14,600 | 1,040 | 1,000 | $128,000 |
Note: Production is given as 1,600 units. The ending inventory for December is given as 200 units. If the production is more than or equal to the demand, then there would be inventory. If the demand is more, then there would be stock out. Maximum overtime units allowed is 320 units (20% of production)
Calculate the ending inventory or stock-out for Period 1:
It is calculated by adding the production and ending inventory of the previous month and subtracting the result from the demand. The ending inventory for Period 1 is 400.
Calculate the ending inventory or stock-out for Period 2:
It is calculated by adding the production and ending inventory of the previous month and subtracting the result from the demand. The ending inventory for Period 2 is 400.
Calculate the ending inventory or stock-out for Period 3:
It is calculated by adding the production and ending inventory of the previous month and subtracting the result from the demand. The ending inventory for Period 3 is 200.
Calculate the ending inventory or stock-out for Period 4:
It is calculated by adding the production and ending inventory of the previous month and subtracting the result from the demand. The ending inventory for Period 4 is 0.
Calculate the ending inventory or stock-out for Period 5:
As the demand is more than the production, there would be a stock-out.
It is calculated by subtracting the production from the demand. The result should then be subtracted from the overtime units. Hence, the stock-out units for Period 5 is 280 units.
Calculate the ending inventory or stock-out for Period 6:
As the demand is more than the production, there would be a stock-out.
It is calculated by subtracting the production from the demand. The result should then be subtracted from the overtime units. Hence, the stock-out units for Period 6 is 280 units.
Calculate the ending inventory or stock-out for Period 7:
It is calculated by subtracting the production from the demand. The result should then be subtracted from the overtime units. Hence, the stock-out units for Period 7 is 0 units.
Note: Overtime units of 320 units would lead to a negative value. Hence, it was taken as 200 units.
Calculate the ending inventory or stock-out for Period 8:
It is calculated by subtracting the production from the demand. The result should then be subtracted from the overtime units. Hence, the stock-out units for Period 8 is 0 units.
Note: Overtime units of 320 units would lead to negative value. Hence, it was taken as 200 units.
Calculate the extra cost for Period 1:
It is calculated by multiplying the extra inventory units and inventory holding cost. The inventory holding cost is given as $20 per unit. Hence, the extra cost for period 1 is $8,000
Calculate the extra cost for Period 2:
It is calculated by multiplying the extra inventory units and inventory holding cost. Inventory holding cost is given as $20 per unit. Hence, the extra cost for period 2 is $8,000
Calculate the extra cost for Period 3:
It is calculated by multiplying the extra inventory units and inventory holding cost. Inventory holding cost is given as $20 per unit. Hence, the extra cost for period 3 is $4,000
Calculate the extra cost for Period 4:
As there are no overtime units, ending inventory units, or stock-out units, there would not be any extra costs.
Calculate the extra cost for Period 5:
It is calculated by adding the product of overtime units and inventory holding overtime cost per unit, and the product of stock-out units and stock-out cost per unit. Stock-out cost is given as $100 per unit and overtime cost is given as $50 per unit. Hence, the extra cost for period 5 is $44,000
Calculate the extra cost for Period 6:
It is calculated by adding the product of overtime units and inventory holding overtime cost per unit, and the product of stock-out units and stock-out cost per unit. Stock-out cost is given as $100 per unit and overtime cost is given as $50 per unit. Hence, the extra cost for period 6 is $44,000
Calculate the extra cost for Period 7:
It is calculated by adding the product of overtime units and inventory holding overtime cost per unit, and the product of stock-out units and stock-out cost per unit. Stock-out cost is given as $100 per unit and overtime cost is given as $50 per unit. Hence, the extra cost for period 7 is $10,000
Calculate the extra cost for Period 8:
It is calculated by adding the product of overtime units and inventory holding overtime cost per unit, and the product of stock-out units and stock-out cost per unit. Stock-out cost is given as $100 per unit and overtime cost is given as $50 per unit. Hence, the extra cost for period 8 is $10,000
Calculate the total cost of Plan D:
It is calculated by adding the extra costs of all the periods.
Hence, the total cost for Plan D is $128,000.
b)
To determine: Plan E
Introduction: The aggregate plan is the output of sales and operations planning. The major concern of aggregate planning is the production time and quantity for the intermediate future. Aggregate planning would encompass a time prospect of approximately 3 to 18 months.
b)

Answer to Problem 6P
Plan E has been evaluated. The total cost of Plan E is $140,000.
Explanation of Solution
Given information:
Production for all the months is 1,600 units. Overtime cost is $50 per unit. Maximum allowable inventor in the warehouse is 400 units or less. Demand requirement from period 0 to 8 is as follows:
Period | Expected demand |
0 | 0 |
1 | 1,400 |
2 | 1,600 |
3 | 1,800 |
4 | 1,800 |
5 | 2,200 |
6 | 2,200 |
7 | 1,800 |
8 | 1,800 |
Evaluate the cost of the plan:
Plan E | |||||
Period | Demand | Production | Subcontract (units) | Ending inventory | Extra cost |
0 | 200 | ||||
1 | 1,400 | 1,600 | - | 400 | $8,000 |
2 | 1,600 | 1,600 | - | 400 | $8,000 |
3 | 1,800 | 1,600 | - | 200 | $4,000 |
4 | 1,800 | 1,600 | - | - | $0 |
5 | 2,200 | 1,600 | 600 | - | $45,000 |
6 | 2,200 | 1,600 | 600 | - | $45,000 |
7 | 1,800 | 1,600 | 200 | - | $15,000 |
8 | 1,800 | 1,600 | 200 | - | $15,000 |
Total | 14,600 | 1,600 | 1,000 | $140,000 |
Note: Production is given as 1,600 units. The ending inventory for December is given as 200 units. If the production is more than or equal to the demand, then there would be inventory. If the demand is more, then there would be subcontract.
Calculate the ending inventory or subcontract for Period 1:
It is calculated by adding the production and ending inventory of previous month and subtracting the demand from the result. The ending inventory for Period 1 is 400.
Calculate the ending inventory or subcontract for Period 2:
It is calculated by adding the production and ending inventory of previous month and subtracting the demand from the result. The ending inventory for Period 2 is 400.
Calculate the ending inventory or subcontract for Period 3:
It is calculated by adding the production and ending inventory of previous month and subtracting the demand from the result. The ending inventory for Period 3 is 200.
Calculate the ending inventory or subcontract for Period 4:
It is calculated by adding the production and ending inventory of previous month and subtracting the demand from the result. The ending inventory for Period 4 is 0.
Calculate the ending inventory or subcontract for Period 5:
As the demand is more than the production, there would be a subcontract.
It is calculated by subtracting the production from the demand. Hence, the subcontract units for Period 5 is 600 units.
Calculate the ending inventory or subcontract for Period 6:
As the demand is more than the production, there would be a subcontract.
It is calculated by subtracting the production from the demand. Hence, the subcontract units for Period 6 is 600 units.
Calculate the ending inventory or subcontract for Period 7:
It is calculated by subtracting the production from the demand. The result should then be subtracted from the overtime units. Hence, the subcontract units for Period 7 is 200 units.
Calculate the ending inventory or subcontract for Period 8:
It is calculated by subtracting the production from the demand. The result should then be subtracted from the overtime units. Hence, the subcontract units for Period 8 is 0 units.
Calculate the extra cost for Period 1:
It is calculated by multiplying the extra inventory units and inventory holding cost. Inventory holding cost is given as $20 per unit. Hence, the extra cost for period 1 is $8,000
Calculate the extra cost for Period 2:
It is calculated by multiplying the extra inventory units and inventory holding cost. Inventory holding cost is given as $20 per unit. Hence, the extra cost for period 2 is $8,000
Calculate the extra cost for Period 3:
It is calculated by multiplying the extra inventory units and inventory holding cost. Inventory holding cost is given as $20 per unit. Hence, the extra cost for period 3 is $4,000
Calculate the extra cost for Period 4:
As there are no overtime units, ending inventory units, and subcontract units, there would not be extra costs.
Calculate the extra cost for Period 5:
It is calculated by multiplying the subcontract units and subcontract cost per unit. Subcontract cost is given as $75 per unit. Hence, the extra cost for period 5 is $45,000
Calculate the extra cost for Period 6:
It is calculated by multiplying the subcontract units and subcontract cost per unit. Subcontract cost is given as $75 per unit. Hence, the extra cost for period 6 is $45,000
Calculate the extra cost for Period 7:
It is calculated by multiplying the subcontract units and subcontract cost per unit. Subcontract cost is given as $75 per unit. Hence, the extra cost for period 7 is $15,000
Calculate the extra cost for Period 8:
It is calculated by multiplying the subcontract units and subcontract cost per unit. Subcontract cost is given as $75 per unit. Hence, the extra cost for period 8 is $15,000
Calculate the total cost of Plan E:
It is calculated by adding the extra costs of all the periods.
Hence, the total cost for Plan E is $140,000.
The total cost for Plan D is preferable when compared with Plan E. However, Plan C, with the total cost of $86,000 is preferable over other plans.
Want to see more full solutions like this?
Chapter 13 Solutions
EBK PRINCIPLES OF OPERATIONS MANAGEMENT
- Hill’s operations manager (see Problems 13.3 through13.5) is also considering two mixed strategies for January–August: Produce in overtime or subcontracting only when there isno inventory.◆ Plan D: Keep the current workforce stable at producing1,600 units per month. Permit a maximum of 20% overtime atan additional cost of $50 per unit. A warehouse now constrainsthe maximum allowable inventory on hand to 400 units or less.◆ Plan E: Keep the current workforce, which is producing 1,600units per month, and subcontract to meet the rest of the demand.Evaluate plans D and E and make a recommendation.arrow_forwardConsuela Chua, Inc., is a disk drive manufacturer in need of an aggregate plan for July through December. The company has gathered the following data: What will each of the two fo llowing strategies cost?a) Vary the workforce so that production meets demand. Chuahad eight workers on board in June.b) Vary overtime only and use a constant workforce of eight.arrow_forwardA producer of pottery is considering the addition of a new plant to absorb the backlog of demand that now exists. The primary location being considered will have fixed costs of $9,200 per month and variable costs of 70 cents per unit produced. Each item is sold to retailers at a price that averages 90 cents.a. What volume per month is required in order to break even?b. What profit would be realized on a monthly volume of 61,000 units? 87,000 units?c. What volume is needed to obtain a profit of $16,000 per month?d. What volume is needed to provide a revenue of $23,000 per month?e. Plot the total cost and total revenue lines.arrow_forward
- Summertime Products makes outdoor shirts. Data relating to the coming year’s planned operations follows: Sales (200,000 shirts) P 5,000,000 Cost of good sold 3,500,000 Gross profit P 1,500,000 Selling and administrative expenses 1,100,000 Income P 400,000 The factory has capacity to make 240,000 shirts per year. Fixed cost included in cost of goods sold was P 1,000,000. The only variable selling, general, and administrative expenses are a 10% sales commission and a P 2.00 per shirt licensing fee paid to the designer. A chain store manager has approached the sales manager of Summertime Products offering to buy 30,000 shirts at P18 per shirt. These shirts would be sold in areas where Summertime’ shirts are not now sold. The sales manager believes that the accepting the offer would result in a loss because the average total cost of a shirt is P 23 ([3,500,000+P 1,100,000]/200,000). He feels that even though sales commissions would not be paid on the order, a loss would still result.…arrow_forwardOperation management 1. What should Douglas Hall do for the coming season? For the next year? 2. What are the implications for the future of tennis at Playa Dorada Resort? Consider the following: Douglas Hall understands he needs to tackle both court capacity and price structure. The tennis facilities are at full capacity in March and April and near capacity in January and February. 287 housing units are scheduled to complete in the next 12 months which will result in the amount of guests to increase by about 50%. Guests have expressed their concern of peak playing hour time unavailability (9-11, 4-6). Playa dorado has been marketed as a Tennis hot spot and many guests have an expectation of playing tennis. Issue 1: Expense of preferred court type To maintain guest satisfaction and their continued frequency it is it seems important to get more courts, albeit at their expense, which might be a net loss the company as they will predominantly be used during peak months. Each guest should…arrow_forwardState how the long term capacity and the short term compacity considerations differ ? i need short answer to the point !!arrow_forward
- When demand for future resources is expected to decrease, the company can start to plan ways to shed the capacity so that it will not be burdened with significant excess capacity in future quarters”. • Identify the strategy of capacity to be used by the company. State the reason to choose the strategy.arrow_forward1) How would you determine the capacity of the restaurant business stated above (TROPICAL BITES) and measure its efficiency. Use an example to illustrate. 2) How can you reach economies of scale in the restaurant business/ company and how? 3) What other element of capacity planning would you consider for the restaurant business and why?arrow_forwardA producer of pottery is considering the addition of a new plant to absorb the backlog of demand that now exists. The primary location being considered will have fixed costs of $7,900 per month and variable cost of 62 cents per unit produced. Each item is sold to retailers at a price that averages 85 cents. (Round all answers to a whole number.) a. What volume per month is required in order to break even? b. What profit would be realized on a monthly volume of 65,000 units? 85,000 units? c. What volume is needed to obtain a profit of $13,000 per month? d. What volume is needed to provide a revenue of $20,000 per month?arrow_forward
- Practical Management ScienceOperations ManagementISBN:9781337406659Author:WINSTON, Wayne L.Publisher:Cengage,
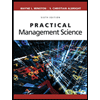