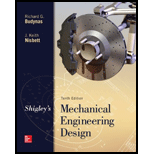
Concept explainers
The speed reducer of Prob. 14-24 is to be used for an application requiring 40 hp at 1145 rev/min. For the gear and the pinion, estimate the AGMA factors of safety for bending and wear, that is, (SF)P, (SF)G, (SH)P, and (SH)G. By examining the factors of safety, identify the threat to each gear and to the mesh.
14-24 A speed-reducer has 20° full-depth teeth, and the single-reduction spur-gear gearset has 22 and 60 teeth. The diametral pitch is 4 teeth/in and the face width is

The factor of safety for bending for pinion.
The factor of safety for bending for gear.
The factor of safety for wear for pinion.
The factor of safety for wear for gear.
Answer to Problem 25P
The factor of safety for bending for pinion is
The factor of safety for bending for gear is
The factor of safety for wear for pinion is
The factor of safety for wear for gear is
Explanation of Solution
Write the expression for diameter of pinion.
Here, the number of teeth on pinion is
Write the expression for diameter of the gear.
Here, the number of teeth on gear is
Write the expression for velocity of the pinion.
Here, the number of rotation made by pinion is
Write the expression for constant of transmission accuracy level number.
Here, the transmission accuracy level number is
Write the expression for constant
Write the expression for dynamic factor.
Write the expression for allowable bending stress number through hardened steels.
Here, the brinel hardness number is
Write the expression for stress cycle factor for bending.
Here, the number of cycles is
Write the expression for allowable stress.
Here, the reliability factor is
Write the expression for load correction factor for uncrowned teeth.
Write the expression for pinion proportion factor.
Here, the face width is
Write the expression for pinion proportion modifier for straddle mounted pinion.
Write the expression for mesh alignment factor.
Here, the empirical constant is
Write the expression for mesh alignment correction factor.
Write the expression for load distribution factor
Write the expression for overload factor for pinion.
Write the expression for overload factor for gear.
Write the expression for transmitted load in pinion.
Here, the spur gear geometry factor is
Write the expression for transmitted load for gear.
Write the expression for gear ratio.
Here, the number of teeth on gear is
Write the expression for pitting resistance stress cycle factor for pinion.
Write the expression for pitting resistance stress cycle factor for gear.
Write the expression for geometry factor.
Here, the pressure angle is
Write the expression for hardness ratio factor
Write the expression for contact fatigue strength for pinion.
Write the expression for contact fatigue strength for gear.
Write the expression for pinion contact endurance strength.
Write the expression for transmitted load.
Write the expression for gear contact strength.
Write the expression for transmitted load.
Her, the elastic coefficient is
Write the expression for transmitted load.
Write the expression for factor of safety based on load and stress for pinion bending.
Write the expression for factor of safety based on load and stress for gear bending.
Write the expression for factor of safety based on load.
Write the expression for based on stress.
Write the expression for factor of safety on load.
Write the expression for factor of safety based on stress.
Conclusion:
Substitute
Substitute
Substitute
Substitute
Substitute
Substitute
Substitute
Substitute
Substitute
Substitute
Refer to table 14-9, “Empirical constant
Substitute
Substitute
Refer Figure 14-6, “spur gear geometry factor”, to obtain the geometry factor for number of teeth
Since the thickness of gear is constant so
Rim thickness
Since the loading is uniform so
Refer table 14-2, “values of the lewis form factor
Substitute
Substitute
Substitute
Substitute
Substitute
Substitute
Substitute
Substitute
Substitute
Substitute
Substitute
Substitute
Substitute
Substitute
Substitute
Substitute
Thus, the factor of safety for bending for pinion is
Substitute
Thus, the factor of safety for bending for gear is
Substitute
Substitute
Thus, the factor of safety for wear for pinion is
Substitute
Substitute
Thus, the factor of safety for wear for gear is
The factor of safety for wear for pinion is
Want to see more full solutions like this?
Chapter 14 Solutions
Shigley's Mechanical Engineering Design (McGraw-Hill Series in Mechanical Engineering)
- A truck equipped with a 50 HP engine uses a roller chain as the final drive to the rear axle. The driving sprocket runs at 225 rpm with a center distance of approximately 500 fpm. The transmission efficiency between the engine and the driving sprocket is 85%. 1.1 Determine the pitch and width of chain to be used. 1.2 Determine the number of teeth in each sprocket and the pitch diameters.arrow_forwardXY=11 By examine the parameters given, evaluate the maximum power-transmitting capacity, based on AGMA bending strength for both gears.arrow_forwardTwo mating gears of 20 and 50 teeth of 20° pressure angle has path of contact equal to 35 mm What will be the arc of contact, (cos20 = 0.9397, tan 20°= 0.36397)arrow_forward
- A chain drive using bush roller chain transmits 5.6 kW of power. The driving shaft on an electric motor runs at 1440 r.p.m. and velocity ratio is 5. The centre distance of the drive is restricted to 550 ± 2% mm and allowable pressure on the pivot joint is not to exceed 10 N/mm2. The drive is required to operate continuously with periodic lubrication and driven machine is such that load can be regarded as fairly constant with jerk and impact. Design the chain drive by calculating leading dimensions, number of teeth on the sprocket and specify the breaking strength of the chain. Assume a factor ofarrow_forwardcampute the bending stress number for the goer pair described by the given data beLow. KS= 1, Km= 1,21, F= 2.00 in, DP= 3,33 in, NG= 70, Np=20 hp = 1750v. p.m, Av=11, Pd =6, Tp= 900ib V1= 1527 ft/min The matarial used for pinion a gear is cast ironarrow_forwardA pair of straight teeth spur gear is to transmit 20kw when the pinion at 300rpm.the velocity ratio is 1:3.the allowable static stresses for the pinion and the gear material are 12MPa and 100MPa respectively.the service factor is 1.the pinion has 15 teeth and it's face width is 14 times the module.from the standpoint of strength only and taking into consideration the effect of the dynamic loading Determine; (A) module (B) face width (C) pitch circle diameter for pinion (D) pitch circle diameter for gear Tooth form factor;y=0.153_0.912÷no.of teeth Velocity factor;Cv= 3÷3+varrow_forward
- Provide the complete step-by-step solution, given data, conversion of units, and sketch for this problem. A turbine at 30,000 rpm is used to drive a reduction gear delivering 3 hp at 3,000rpm. The gears are 20 degrees involute herringbone gears of 28 pitch and 2 1/8 ineffective width. The pinion has 20 teeth with a helix angle of 23 deg. Determine theload normal to the tooth surface. A. 20.4 lbs B. 24.4 lbs C. 28.4 lbs D. 32.4arrow_forwardb) Design a self-aligning ball bearing with basic dynamic load rating of 69.5 KN to be used in the automobile industry to carry a thrust load of 1184 N. The expected life of the bearing is 5201 hours at 628 rpm. Take k=3 for all types of ball bearings. Take the value of the shock load factor as 1.7 and radial and axial load factors are 1.4 and 2.2 respectively, the rotational factor is 1. Calculate: i) Expected life of bearings in millions of revolutions ii) Design equivalent dynamic load in N iii) Basic equivalent dynamic load in N iv) Radial load acting on the bearing in Narrow_forwardA drilling machine is capable of drilling 30 holes of 20mm diameter per minute in a 16mm thick steel plate.Theplate has an ultimate shear strentgh as 360 N/mm2. The calculated energy for this process is 2895.2 Nm.Actual drilling process continues during the 36° rotation period of the crank shaft. This crank shaft is driven by a flywheel through a reductionn gear with a ratio of 1:8.In this case the rotation speed is 240 rpm related to the given cycle ratio. Mechanic gain is 80%. Speed fluctuation coefficient is 0.01and flywheel diameter is 0.75m.(a) Find the required power?(b) Find the energy change ΔEk? (c) Find the mass of the flywheel?arrow_forward
- Determine the power capacity of a uniform wear cone cutch having a major diameter of 280 mm minor diameter of 210 mm, length of contact of 120 mm, f=0.28, speed of 850 rpm and has anoperating force of 600 N.arrow_forwardpinion having 20 involute teeth of module pitch 6 mm rotates at 200 r.p.m. and transmits 1.5 kW to a gear wheel having 50 teeth. The addendum on both the wheels is 1/4 of the circular pitch. The angle of obliquity is 20°. Find (a) the length of the path of approach ; (b) the length of the arc of approach; (c) the normal force between the teeth at an instant where there is only pair of teeth in contact.arrow_forwardThe module and the number of teeth on the pinion of a spur gear are 12mm and 15teeth respectively.A power of 400kW is to be transmitted at 1700rpm of width.if the involute teeth are of standard proportions (addendum=m) with the pressure angle of 22.5° determine (A) torque due to power delivered (B) tangential load (C) teeth width (E)load on the bearingsarrow_forward
- Elements Of ElectromagneticsMechanical EngineeringISBN:9780190698614Author:Sadiku, Matthew N. O.Publisher:Oxford University PressMechanics of Materials (10th Edition)Mechanical EngineeringISBN:9780134319650Author:Russell C. HibbelerPublisher:PEARSONThermodynamics: An Engineering ApproachMechanical EngineeringISBN:9781259822674Author:Yunus A. Cengel Dr., Michael A. BolesPublisher:McGraw-Hill Education
- Control Systems EngineeringMechanical EngineeringISBN:9781118170519Author:Norman S. NisePublisher:WILEYMechanics of Materials (MindTap Course List)Mechanical EngineeringISBN:9781337093347Author:Barry J. Goodno, James M. GerePublisher:Cengage LearningEngineering Mechanics: StaticsMechanical EngineeringISBN:9781118807330Author:James L. Meriam, L. G. Kraige, J. N. BoltonPublisher:WILEY
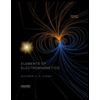
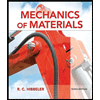
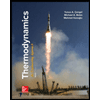
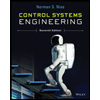
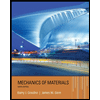
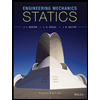