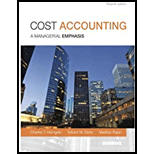
EBK COST ACCOUNTING
15th Edition
ISBN: 9780133812763
Author: Rajan
Publisher: VST
expand_more
expand_more
format_list_bulleted
Question
Chapter 16, Problem 16.35P
1.
To determine
Process costing is a method of cost accounting where cost is allocated to each activity and then it is further assigned to individual units. It is suitable for companies where alike products are produced in significant volume.
To examine: Decision of process further or sell as it.
2.
To determine
To compute: Effect on change in cost of producing raw coal on the above analysis.
3.
To determine
To compute: Effect on potential value of the coal fines on the above analysis.
Expert Solution & Answer

Want to see the full answer?
Check out a sample textbook solution
Students have asked these similar questions
Monroe Manufacturing owns a warehouse that has been used for storing finished goods for electro-pump products. As the company is phasing out the electro-pump product line, the company is considering modifying the existing structure to use for manufacturing a new product line. Monroe's production engineer feels that the warehouse could be modified to handle one of two new product lines. The cost and revenue data for the two product alternatives arc as follows:
Product A Product BInitial cash expenditure:• Warehouse modification $115,000 $189,000• Equipment $250,000 $315,000Annual revenues $215,000 $289,000Annual O&M costs $126,000 $168,000Product life 8 years 8 yearsSalvage value…
A plastic-manufacturing company owns andoperates a polypropylene production facility that converts the propylene from one of its cracking facilitiesto polypropylene plastics for outside sale. The polypropylene production facility is currently forced tooperate at less than capacity due to an insufficiencyof propylene production capacity in its hydrocarboncracking facility. The chemical engineers are considering alternatives for supplying additional propyleneto the polypropylene production facility. Two feasiblealternatives are to build a pipeline to the nearest outside supply source and to provide additional propylene by truck from an outside source. The engineersalso gathered the following projected cost estimates.• Future costs for purchased propylene excludingdelivery: $0.215 per lb.• Cost of pipeline construction: $200,000 per pipeline mile.• Estimated length of pipeline: 180 miles.• Transportation costs by tank truck: $0.05 per lb,utilizing a common carrier.• Pipeline operating…
A plastic-manufacturing company owns and operates a polypropylene-production facility that converts the propylene from one of its cracking facilities to polypropylene plastics for outside sale. The polypropylene-production facility is currently forced to operate at less than capacity due to lack of enough propylene-production capacity in its hydrocarbon-cracking facility. The chemical engineers are considering alternatives for supplying additional propylene to the polypropylene productionfacility. Some of the feasible alternatives are as follows:Option 1: Build a pipeline to the nearest outs.ide supply source.Option 2: Provide additional propylene by truck from an outside source.The engineers also gathered the following projected cost estimates:Hi Future costs for purchased propylene, excluding delivery: $0.215 per lb1. Cost of pipeline construction: $200,000 per pipeline mile2. Estimated length of pipeline: 180 miles3. Transportation costs by tank truck: $0.05 per lb, using a common…
Chapter 16 Solutions
EBK COST ACCOUNTING
Ch. 16 - Give two examples of industries in which joint...Ch. 16 - What is a joint cost? What is a separable cost?Ch. 16 - Distinguish between a joint product and a...Ch. 16 - Why might the number of products in a joint-cost...Ch. 16 - Provide three reasons for allocating joint costs...Ch. 16 - Why does the sales value at splitoff method use...Ch. 16 - Prob. 16.7QCh. 16 - Distinguish between the sales value at splitoff...Ch. 16 - Give two limitations of the physical-measure...Ch. 16 - How might a company simplify its use of the NRV...
Ch. 16 - Why is the constant gross-margin percentage NRV...Ch. 16 - Managers must decide whether a product should be...Ch. 16 - Prob. 16.13QCh. 16 - Describe two major methods to account for...Ch. 16 - Why might managers seeking a monthly bonus based...Ch. 16 - Prob. 16.16ECh. 16 - Prob. 16.17ECh. 16 - Prob. 16.18ECh. 16 - Prob. 16.19ECh. 16 - Prob. 16.20ECh. 16 - Prob. 16.21ECh. 16 - Prob. 16.22ECh. 16 - Prob. 16.23ECh. 16 - Prob. 16.24ECh. 16 - Joint costs and decision making. Jack Bibby is a...Ch. 16 - Joint costs and byproducts. (W. Crum adapted)...Ch. 16 - Prob. 16.27PCh. 16 - Prob. 16.28PCh. 16 - Prob. 16.29PCh. 16 - Prob. 16.30PCh. 16 - Prob. 16.31PCh. 16 - Prob. 16.32PCh. 16 - Prob. 16.33PCh. 16 - Prob. 16.34PCh. 16 - Prob. 16.35PCh. 16 - Prob. 16.36PCh. 16 - Methods of joint-cost allocation, comprehensive....
Knowledge Booster
Similar questions
- A plastic-manufacturing company owns and operates a polypropylene-production facility that converts the propylene from one of its cracking facilities to polypropylene plastics for outside sale. The polypropylene-production facility is currently forced to operate at less than capacity due to a lack of propylene-production capacity in its hydrocarbon-cracking facility. The chemical engineers are considering alternatives for supplying additional propylene to the polypropylene productionfacility. Some of the feasible alternatives are as follows: Option 1: Build a pipeline to the nearest outs.ide supply source.Option 2: Provide additional propylene by truck from an outside source.The engineers also gathered the following projected cost estimates:Hi Future costs for purchased propylene, excluding delivery: $0.215 per lb1. Cost of pipeline construction: $200,000 per pipeline mile2. Estimated length of pipeline: 180 miles3. Transportation costs by tank truck: $0.05 per lb, using a common…arrow_forwardKingsley Products, Ltd., is using a model 400 shaping machine to make one of its products. The companyis expecting to have a large increase in demand for the product and is anxious to expand its productivecapacity. Two possibilities are under consideration:Alternative 1. Purchase another model 400 shaping machine to operate along with the currentlyowned model 400 machine.Alternative 2. Purchase a model 800 shaping machine and use the currently owned model 400machine as standby equipment. The model 800 machine is a high-speed unit with double thecapacity of the model 400 machine.The following additional information is available on the two alternatives:a. Both the model 400 machine and the model 800 machine have a 10-year life from the time they arefirst used in production. The scrap value of both machines is negligible and can be ignored. Straightline depreciation is used.b. The cost of a new model 800 machine is $300,000.c. The model 400 machine now in use cost $160,000 three years…arrow_forwardPaper reclaim capital investment analysis The Victor Paper Company manufactures paper products from pulp. The process creates paper scrap from paper trim, off-grade, and machine errors. Presently, the scrap paper is discarded in a landfill. Management is considering a proposal for a scrap paper reclamation system. The system is designed so that paper is discarded in vacuum collection points located throughout the plant. The vacuum system would be attached to a reclaim process that would digest the scrap paper, turning it back into pulp, and then blending the reclaimed product back into the papermaking process with virgin (new) pulp. The blended stream is termed “blended pulp.” It has been determined that the quality of the final product is not adversely impacted by using blended pulp versus using 100% virgin pulp. In addition, the cost of the reclaimed pulp is considered “free” to the blended stream, and causes the amount of virgin pulp used in the blended stream to be less than would…arrow_forward
- ABC steel plant industry plans to manufacture a product. The product needs a special component. The industry has reviewed that the special component can be produced in the plant or bought in. An investment is required to start the production of the component for which two mutually exclusive projects A and B representing different production processes are available. The alternative option is to buy in from another company representing project C. The details of projects A and B are given in Table 3: (i) Using the information from table 3 and Discount Cash Flow criteria, calculate Pay Back Period (PBP), Account Rate of Return (ARR), Net Present Value (NPV) and Internal Rate Return (IRR) for project A & Project B if the industry plans to sale the unit cost of RO 350. (ii) Using the annual cost data from table 3, determine which project incurs less cost if the industry considers producing 7,500 units per year. (iii) Using the table 3, determine the Break-Even quantity and margin of…arrow_forwardAt times firms will need to decide if they want to continue to use their current equipment or replace the equipment with newer equipment. The company will need to do replacement analysis to determine which option is the best financial decision for the company. Price Co. is considering replacing an existing piece of equipment. The project involves the following: • The new equipment will have a cost of $1,800,000, and it will be depreciated on a straight-line basis over a period of six years (years 1–6). • The old machine is also being depreciated on a straight-line basis. It has a book value of $200,000 (at year 0) and four more years of depreciation left ($50,000 per year). • The new equipment will have a salvage value of $0 at the end of the project's life (year 6). The old machine has a current salvage value (at year 0) of $300,000. • Replacing the old machine will require an investment in net operating working capital (NOWC) of $50,000 that will be recovered at the end…arrow_forwardCamilia Inc. has options to acquire intangible assets either through buying the intangible asset, or through A. doing some research and develop the intangible asset internally. From what you learnt from this course explain with details the differences between these two ways of acquiring intangible assets. Camilia, Inc, a biotechnology company, developed and patented a diagnostic product called Trouvadol. Camilia purchased some research equipment to be used for Trouvadol and subsequent research projects. Camilia defeated a legal challenge to its Trouvadol patent, and began production and marketing operations for the project. Corporate headquarters B. costs were allocated to Camilia's research division as a percentage of the division's salaries. Required: 1. How the equipment purchased for Trouvadol should be reported in Camilia's income statement and statement of financial position? Explain your answer. 2. Describe the accounting treatment of research and development costs. And what is…arrow_forward
- At times firms will need to decide if they want to continue to use their current equipment or replace the equipment with newer equipment. The company will need to do replacement analysis to determine which option is the best financial decision for the company.Price Co. is considering replacing an existing piece of equipment. The project involves the following:• The new equipment will have a cost of $1,200,000, and it is eligible for 100% bonus depreciation so it will be fully depreciated at t = 0.• The old machine was purchased before the new tax law, so it is being depreciated on a straight-line basis. It has a book value of $200,000 (at year 0) and four more years of depreciation left ($50,000 per year).• The new equipment will have a salvage value of $0 at the end of the project's life (year 6). The old machine has a current salvage value (at year 0) of $300,000.• Replacing the old machine will require an investment in net operating working capital (NOWC) of $30,000 that will be…arrow_forwardCertain production equipment used by Dayton Mechanical has become obsolete relative to current technology. The company is considering whether it should keep or replace its existing equipment. To aid in this decision, the company’s controller gathered the following data: (See attached) c. What is the total dollar amount of all relevant costs to the equipment replacement decision. $______ d. What is the total dollar amount of the opportunity costs associated with the alternative of keeping the old equipment? $______arrow_forwardAt times firms will need to decide if they want to continue to use their current equipment or replace the equipment with newer equipment. The company will need to do replacement analysis to determine which option is the best financial decision for the company. Price Co. is considering replacing an existing piece of equipment. The project involves the following: • The new equipment will have a cost of $2,400,000, and it is eligible for 100% bonus depreciation so it will be fully depreciated at t = 0. • The old machine was purchased before the new tax law, so it is being depreciated on a straight-line basis. It has a book value of $200,000 (at year 0) and four more years of depreciation left ($50,000 per year). • The new equipment will have a salvage value of $0 at the end of the project's life (year 6). The old machine has a current salvage value (at year 0) of $300,000. • Replacing the old machine will require an investment in net operating working capital (NOWC) of…arrow_forward
- At times firms will need to decide if they want to continue to use their current equipment or replace the equipment with newer equipment. The company will need to do replacement analysis to determine which option is the best financial decision for the company. Price Co. is considering replacing an existing piece of equipment. The project involves the following: • The new equipment will have a cost of $2,400,000, and it is eligible for 100% bonus depreciation so it will be fully depreciated at t = 0. • The old machine was purchased before the new tax law, so it is being depreciated on a straight-line basis. It has a book value of $200,000 (at year 0) and four more years of depreciation left ($50,000 per year). • The new equipment will have a salvage value of $0 at the end of the project's life (year 6). The old machine has a current salvage value (at year 0) of $300,000. • Replacing the old machine will require an investment in net operating working capital (NOWC) of…arrow_forwardCompany XYZ extracts oil and accordingly owns a drilling platform in theArabian Gulf. By the end of the platform’s useful life, the firm is required toremove and dismantle it. Thus, the firm accounts for the removal anddismantling costs, which are depreciated over the platform’s useful life.Using the information below, you are asked to investigate whether therehas been an impairment of the platform: The carrying amount of the platform in the statement of financialposition is £5m.The company received an offer of £4.8m for the platform from aneighbouring competitor. This potential bidder would take theresponsibility of dismantling and removing the platform(including the costs) at the end of the asset’s life. The present value of the estimated cash flows from theplatform’s continued use is £5.4m, excluding any dismantlingcosts.The carrying value in XYZ’s balance sheet for the provision fordismantling and extraction is £0.8m. Describe in detail what is meant by the impairment of assets.…arrow_forwardAt times firms will need to decide if they want to continue to use their current equipment or replace the equipment with newer equipment. The company will need to do replacement analysis to determine which option is the best financial decision for the company. Johnson Co. is considering replacing an existing piece of equipment. The project involves the following: • The new equipment will have a cost of $1,200,000, and it is eligible for 100% bonus depreciation so it will be fully depreciated at t = 0. • The old machine was purchased before the new tax law, so it is being depreciated on a straight-line basis. It has a book value of $200,000 (at year 0) and four more years of depreciation left ($50,000 per year). • The new equipment will have a salvage value of $0 at the end of the project's life (year 6). The old machine has a current salvage value (at year 0) of $300,000. • Replacing the old machine will require an investment in net operating working capital (NOWC) of…arrow_forward
arrow_back_ios
SEE MORE QUESTIONS
arrow_forward_ios
Recommended textbooks for you
- Intermediate Accounting: Reporting And AnalysisAccountingISBN:9781337788281Author:James M. Wahlen, Jefferson P. Jones, Donald PagachPublisher:Cengage Learning
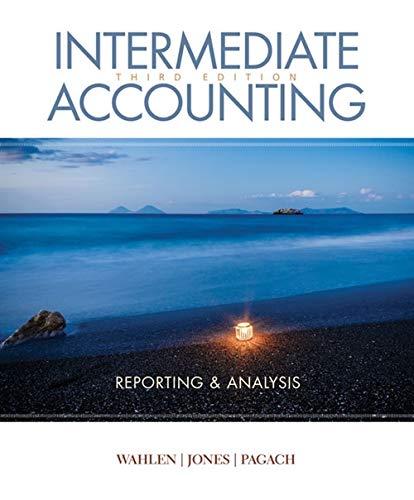
Intermediate Accounting: Reporting And Analysis
Accounting
ISBN:9781337788281
Author:James M. Wahlen, Jefferson P. Jones, Donald Pagach
Publisher:Cengage Learning