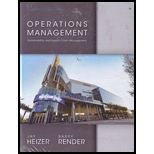
Concept explainers
New England Foundry
For more than 75 years, New England Foundry, Inc., (NEFI), has manufactured wood stoves for home use. In recent years, with increasing energy prices, President George Mathison has seen sales triple. This dramatic increase has made it difficult for George to maintain quality in all his wood stoves and related products.
Unlike other companies manufacturing wood stoves, NEFI is in the business of making only stoves and stove-related products. Its major products are the Warmglo I, the Warmglo II, the Warmglo III, and the Warmglo IV. The Warmglo I is the smallest wood stove, with a heat output of 30,000 BTUs, and the Warmglo IV is the largest, with a heat output of 60,000 BTUs.
The Warmglo III outsold all other models by a wide margin. Its heat output and available accessories were ideal for the typical home. The Warmglo III also had a number of other outstanding features that made it one of the most attractive and heat-efficient stoves on the market. These features, along with the accessories, resulted in expanding sales and prompted George to build a new factory to manufacture the Warmglo III model. An overview diagram of the factory is shown in Figure D.6.
Figure D.6 Overview of Factory
The new foundry used the latest equipment, including a new Disamatic that helped in manufacturing stove parts. Regardless of new equipment or procedures, casting operations have remained basically unchanged for hundreds of years. To begin with, a wooden pattern is made for every cast-iron piece in the stove. The wooden pattern is an exact duplicate of the cast-iron piece that is to be manufactured. All NEFI patterns are made by Precision Patterns, Inc. and are stored in the pattern shop and maintenance room. Next, a specially formulated sand is molded around the wooden pattern. There can be two or more sand molds for each pattern. The sand is mixed and the molds are made in the molding room. When the wooden pattern is removed, the resulting sand molds form a negative image of the desired casting.
Next, molds are transported to the casting room, where molten iron is poured into them and allowed to cool. When the iron has solidified, molds are moved into the cleaning, grinding, and preparation room, where they are dumped into large vibrators that shake most of the sand from the casting. The rough castings are then subjected to both sandblasting to remove the rest of the sand and grinding to finish some of their surfaces. Castings are then painted with a special heat-resistant paint, assembled into workable stoves, and inspected for manufacturing defects that may have gone undetected. Finally, finished stoves are moved to storage and shipping, where they are packaged and transported to the appropriate locations.
At present, the pattern shop and the maintenance department are located in the same room. One large counter is used by both maintenance personnel, who store tools and parts (which are mainly used by the casting department), and sand molders, who need various patterns for the molding operation. Pete Nawler and Bob Dillman, who work behind the counter, can service a total of 10 people per hour (about 5 per hour each). On average, 4 people from casting and 3 from molding arrive at the counter each hour. People from molding and casting departments arrive randomly, and to be served, 1hey form a single line.
Pete and Bob have always had a policy of first come, first served. Because of the location of the pattern shop and maintenance department, it takes an average of 3 minutes for an individual from the casting department to walk to the pattern and maintenance room, and it takes about 1 minute for an individual to walk from the molding department to the pattern and maintenance room.
After observing the operation of the pattern shop and maintenance room for several weeks, George decided to make some changes to the factory layout. An overview of these changes appears in Figure D.7.
Figure D.7 Overview of Factory after Changes
Separating the maintenance shop from the pattern shop would have a number of advantages. It would take people from the casting department only 1 minute instead of 3 to get to the new maintenance room. The time from molding to the pattern shop would be unchanged. Using motion and time studies, George was also able to determine that improving the layout of the maintenance room would allow Bob to serve 6 people from the casting department per hour; improving the layout of the pattern department would allow Pete to serve 7 people from the molding shop per hour.
3. Should George have made the change in layout?

Want to see the full answer?
Check out a sample textbook solution
Chapter D Solutions
Operations Management and Student CD
- Seas Beginning sells clothing by mail order. An important question is when to strike a customer from the companys mailing list. At present, the company strikes a customer from its mailing list if a customer fails to order from six consecutive catalogs. The company wants to know whether striking a customer from its list after a customer fails to order from four consecutive catalogs results in a higher profit per customer. The following data are available: If a customer placed an order the last time she received a catalog, then there is a 20% chance she will order from the next catalog. If a customer last placed an order one catalog ago, there is a 16% chance she will order from the next catalog she receives. If a customer last placed an order two catalogs ago, there is a 12% chance she will order from the next catalog she receives. If a customer last placed an order three catalogs ago, there is an 8% chance she will order from the next catalog she receives. If a customer last placed an order four catalogs ago, there is a 4% chance she will order from the next catalog she receives. If a customer last placed an order five catalogs ago, there is a 2% chance she will order from the next catalog she receives. It costs 2 to send a catalog, and the average profit per order is 30. Assume a customer has just placed an order. To maximize expected profit per customer, would Seas Beginning make more money canceling such a customer after six nonorders or four nonorders?arrow_forwardManagement of High Tech Services (HTS) would like to develop a model that will help allocate its technicians' time between service calls to regular contract customers and new customers. A maximum of 90 hours of technician time is available over the two-week planning period. To satisfy cash flow requirements, at least $900 in revenue (per technician) must be generated during the two-week period. Technician time for regular customers generates $30 per hour. However, technician time for new customers only generates an average of $9 per hour because in many cases a new customer contact does not provide billable services. To ensure that new customer contacts are being maintained, the technician time spent on new customer contacts must be at least 80% of the time spent on regular customer contacts. Given these revenue and policy requirements, HTS would like to determine how to allocate technician time between regular customers and new customers so that the total number of customers contacted…arrow_forwardHighline Financial Services provides three categories of service toits clients. Managing partner Freddie Mack is getting ready to preparefinancial and personnel hiring (or layoff) plans for the comingyear. He is a bit perplexed by the following printout he obtained,which seems to show oscillating demand for the three categoriesof services over the past eight quarters:Examine the demand that this company has experienced for thethree categories of service it offers over the preceding two years.Assuming nothing changes in terms of advertising or promotion,and competition doesn’t change, predict demand for the servicesthe company offers for the next four quarters. Note that there arenot enough data to develop seasonal relatives. Nonetheless, youshould be able to make reasonably good, approximate intuitiveestimates of demand. What general observations can you makeregarding demand? Should Freddie have any concerns? Explain.arrow_forward
- Primer Inc. offers plumbing and air conditioning services to customers in Brooklyn, NY. The company’s product strategy is to solve the customer’s problem irrespective of what it takes, at the time the customer needs it solved. The company provides same-day service for customers, and the aim is to make the customer happy before leaving.The services of the company are available 24 hours a day, 7 days a week for customers. There is no extra charge for requests made on holidays, odd hours of the day, or in festive seasons. The company aims to be available at the call of customers without charging a pesewa extra, even at times when rival firms won’t get out of bed.The company fixes the price of the service before it begins, and customers can be assured of no extra charges. Irrespective of the customer’s location in the city, Primer Inc. does not charge additional fees for transportation. For all services, the company provides a one-year guarantee on all parts and labor used, while rival…arrow_forwardPrimer Inc. offers plumbing and air conditioning services to customers in Brooklyn, NY. The company’s product strategy is to solve the customer’s problem irrespective of what it takes, at the time the customer needs it solved. The company provides same-day service for customers, and the aim is to make the customer happy before leaving.The services of the company are available 24 hours a day, 7 days a week for customers. There is no extra charge for requests made on holidays, odd hours of the day, or in festive seasons. The company aims to be available at the call of customers without charging a pesewa extra, even at times when rival firms won’t get out of bed.The company fixes the price of the service before it begins, and customers can be assured of no extra charges. Irrespective of the customer’s location in the city, Primer Inc. does not charge additional fees for transportation. For all services, the company provides a one-year guarantee on all parts and labor used, while rival…arrow_forwardPrimer Inc. offers plumbing and air conditioning services to customers in Brooklyn, NY. The company’s product strategy is to solve the customer’s problem irrespective of what it takes, at the time the customer needs it solved. The company provides same-day service for customers, and the aim is to make the customer happy before leaving.The services of the company are available 24 hours a day, 7 days a week for customers. There is no extra charge for requests made on holidays, odd hours of the day, or in festive seasons. The company aims to be available at the call of customers without charging a pesewa extra, even at times when rival firms won’t get out of bed.The company fixes the price of the service before it begins, and customers can be assured of no extra charges. Irrespective of the customer’s location in the city, Primer Inc. does not charge additional fees for transportation. For all services, the company provides a one-year guarantee on all parts and labor used, while rival…arrow_forward
- Primer Inc. offers plumbing and air conditioning services to customers in Brooklyn, NY. The company’s product strategy is to solve the customer’s problem irrespective of what it takes, at the time the customer needs it solved. The company provides same-day service for customers, and the aim is to make the customer happy before leaving.The services of the company are available 24 hours a day, 7 days a week for customers. There is no extra charge for requests made on holidays, odd hours of the day, or in festive seasons. The company aims to be available at the call of customers without charging a pesewa extra, even at times when rival firms won’t get out of bed.The company fixes the price of the service before it begins, and customers can be assured of no extra charges. Irrespective of the customer’s location in the city, Primer Inc. does not charge additional fees for transportation. For all services, the company provides a one-year guarantee on all parts and labor used, while rival…arrow_forward• Use this information for the question below. Low-Grade Copper Ore $571 per Ton High-Grade Copper Ore $843 per Ton Coloma Cooper Incorporated is able to produce $640 worth of copper from one ton of low-grade copper ore. Because of its higher copper content, Coloma can produce $940 worth of copper from one ton of high-grade copper ore. A mining company is offering to trade 7,250 tons of low-grade copper ore for 5,000 tons of high-grade copper ore. Assuming Coloma currently has 5,000 tons of high-grade ore, what should it do?arrow_forwardManagement of High Tech Services (HTS) would like to develop a model that will help allocate their technician’s time between service calls to regular contract customers and new customers. A maximum of 80 hours of technician time is available over the two-week planning period. To satisfy cash flow requirements, at least $800 in revenue (per technician) must be generated during the two-week period. Technician time for regular customers generates $25 per hour. However, technician time for newcustomers only generates an average of $8 per hour. To ensure that new customer contracts are being maintained, the technician time spent on new customer contracts must be at least 60% of the time spent on regular customer contracts. Given these revenue and policy requirements, HTS would like to determine how to allocate technician time between regular customers and new customers so that the total number of customers contracted during the two-week period will be maximized. Technicians require an…arrow_forward
- The Northwoods General Store in Vermont sells a variety of outdoor clothing items and equipment and several food products at its modern but rustic-looking retail store. Its food products include salmon and maple syrup. The store also runs a lucrative catalog operation. One of its most popular products is maple syrup, which is sold in metal half-gallon cans with a picture of the store on the front. Maple syrup was one of the first products the store produced and sold, and it continues to do so. Setting up the syrup-making equipment to produce a batch of syrup costs $450. Storing the syrup for sales throughout the year is a tricky process because the syrup must be kept in a temperature-controlled facility. The annual cost of carrying a gallon of the syrup is $15. Based on past sales data, the store has forecasted a demand of 7,500 gallons of maple syrup for the coming year. The store can produce approximately 100 gallons of syrup per day during the maple syrup season, which runs from…arrow_forwardWheelco, Inc., manufactures automobile and truck wheels. The company produces four basic, high-volume wheels used by each of the large automobile and pickup truck manufacturers. Wheelco also has two specialty wheel lines. These are fancy, complicated wheels used inexpensive sports cars. Lately, Wheelco's profits have been declining. Foreign competitors have been undercutting Wheelco's prices in three of its bread-and-butter product lines, and Wheelco's sales volume and market share have declined. In contrast, Wheelco's specialty wheels have been selling steadily, although in relatively small numbers, in spite of three recent price increases. At a recent staff meeting, Wheelco's president made the following remarks: "Our profits are going down the tubes, folks. It costs us 29 dollars to manufacture our A22 wheel. That's our best-seller, with a volume last year of 17,000 units. But our chief competitor is selling basically the same wheel for 27 bucks. I don't see how they can…arrow_forwardSembotix Company has several divisions including a Semiconductor Division that sells semiconductors to both internal and external customers. The company’s X-ray Division uses semiconductors as a component in its final product and is evaluating whether to purchase them from the Semiconductor Division or from an external supplier. The market price for semiconductors is $100 per 100 semiconductors. Dave Bryant is the controller of the X-ray Division, and Howard Hillman is the controller of the Semiconductor Division. The following conversation took place between Dave and Howard: Dave: I hear you are having problems selling semiconductors out of your division. Maybe I can help. Howard: You’ve got that right. We’re producing and selling at about 90% of our capacity to outsiders. Last year, we were selling 100% of capacity. Would it be possible for your division to pick up some of our excess capacity? After all, we are part of the same company. Dave: What kind of price could you give me?…arrow_forward
- Practical Management ScienceOperations ManagementISBN:9781337406659Author:WINSTON, Wayne L.Publisher:Cengage,
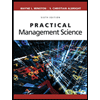