midterm_practice_solution
pdf
School
University of Washington *
*We aren’t endorsed by this school
Course
301
Subject
Economics
Date
Feb 20, 2024
Type
Pages
12
Uploaded by BaronHippopotamusPerson1484
Midterm Exam Practice Solution - 1 - OpMgt 301: Principles of Operations Management Yong-Pin Zhou 1.
Problem 10 in Chapter 19 of the textbook. Decision Variables: x
1
= number of containers of orange juice x
2
= number of containers of grapefruit juice x
3
= number of containers of pineapple juice x
4
= number of containers of All-in-One Parameters: Orange Juice Grapefruit Juice Pineapple Juice All-in-One Revenue per qt. $1.00 $.90 $.80 $1.10 Cost per qt. $.50 $.40 $.35 $.417 Profit per qt. $.50 $.50 $.45 $.683 Objective Function and Constraints: Maximize .50 x
1
+ .50 x
2
+ .45 x
3
+ .683 x
4
s.t. Orange juice: 1 x
1 + .33 x
4
≤
1600 (qt.) Grapefr. juice: 1x
2 +
.33 x
4
≤
1200 (qt.) Pineapple juice: 1x
3
+ .33 x
4
≤
800 (qt.) Grapefr.: -.30 x
1 +.70 x
2 -.30 x
3 +.70 x
4
≤
0 Ratio: -5 x
1 +7 x
3
≤
0 Non-negativity: x
1
, x
2
, x
3
, x
4
≥
0 Note that originally the “Grapefr” constraint is written as “
x
2
+x
4
≤
0.3(x
1
+x
2+
x
3
+x
4
)”
, which can be simplified to “
-.30 x
1 +.70 x
2
-.30 x
3
+.70 x
4
≤
0”. Similarly, the “Ratio” constraint is originally written as “
x
1
/x
3
≥
7/5”.
But this is not linear as the left-hand-side is a division of two decision variables. You can simplify it to “x
1
≥
1.4x
3
,”
“5x
1
≥
7x
3
,” or “-5x
1
+7x
3
≤
0.” 2.
Problem 14 in Chapter 19 of the textbook. Decision Variables: x
1
= boxes of regular mix x
2
= " " deluxe " x
3
= " " cashews x
4
= " " raisins x
5
= " " caramels x
6
= " " chocolates Objective Function and Constraints: Maximize .80 x
1
+ .90 x
2
+ .70 x
3
+ .60 x
4
+ .50 x
5
+ .75 x
6
s.t.
Midterm Exam Practice Solution - 2 - OpMgt 301: Principles of Operations Management Yong-Pin Zhou cashews: .25 x
1 +.50 x
2 +x
3
≤
120 (lb./day) raisins: .25 x
1 +x
4 ≤
200 (lb./day) caramels: .25 x
1 +x
5 ≤
100 (lb./day) chocolate: .25 x
1 +.50 x
2 +x
6 ≤
160 (lb./day) Boxes regular: x
1 ≥
20 deluxe: x
2 ≥
20 cashews: x
3 ≥
20 raisins: x
4 ≥
20 caramels: x
5 ≥
20 chocolates: x
6
≥
20 Non-negativity: x
1
,
x
2
, x
3
, x
4
, x
5
, x
6
≥
0 (Note that the non-negativity constraints are redundant due to the “boxes” constraints). 3.
A farmer is raising pigs for market, and he wishes to determine the quantities of the available types of feed that should be given to each pig to meet certain nutritional requirements at a minimum cost. The number of units of each type of basic nutritional ingredients contained within a kilogram of each feed type is given in the following table along with the daily nutritional requirements and feed costs. Nutritional Ingredient Corn (Kg) Tankage (Kg) Alfalfa (Kg) Minimum Daily Requirement Carbohydrates 90 20 40 200 Protein 30 80 60 180 Vitamins 10 20 60 150 Cost (cents) 42 36 30 In addition, for weight control reasons, the farmer would like each pig to be fed no more than a total of six kilograms of feed. Finally, no more than 40% of the total diet (by weight) should consist of Alfalfa. Formulate this problem as a linear program. Decision Variables: c:
kilograms of corn t:
kilograms of tankage a: kilograms of alfalfa Objective Function and Constraints:
Midterm Exam Practice Solution - 3 - OpMgt 301: Principles of Operations Management Yong-Pin Zhou 0
,
0
,
0
:
0
4
.
0
4
.
0
6
.
0
or )
(
4
.
0
:
6
:
150
60
20
10
:
vitamins
180
60
80
30
:
200
40
20
90
:
30
36
42
a
t
c
ity
nonnegativ
t
c
a
a
t
c
a
alfalfa
a
t
c
control
weight
a
t
c
a
t
c
protein
a
t
c
tes
carbohydra
to
subject
a
t
c
z
Cost
Minimize
4.
X-Mart is a supermarket that operates everyday from 8 a.m. to midnight. Requirement for security personnel at its Seattle store is as follows: Time Period Number of Officers Needed 8 a.m. - 12 p.m. 8 12 p.m. - 4 p.m. 15 4 p.m. - 8 p.m. 12 8 p.m. - 12 a.m. 9 Union contract requires that security officers work consecutive hours. So they can start an 8-hour shift at 8 a.m., 12 p.m., 4 p.m., or a 4-hour shift at 8 p.m. Formulate a linear program to find the minimum number of people to meet the requirement. There are four possible shifts: 8 a.m. – 4 p.m., 12 p.m. – 8 p.m., 4 p.m. – 12 a.m., (8-hour shifts) and 8 p.m. – 12 a.m. (4-hour shift). There is one decision variable for each shift. Decision Variables: x
1
: number of security officers to work 8 a.m. – 4 p.m. x
2
: number of security officers to work 12 p.m. – 8 p.m. x
3
: number of security officers to work 4 p.m. – 12 a.m. y
: number of security officers to work 8 p.m. – 12 a.m. Objective Function and Constraints: 0
,
,
,
:
9
12
15
8
Headcount
Total
3
2
1
3
3
2
2
1
1
3
2
1
y
x
x
x
ity
nonnegativ
y
x
x
x
x
x
x
to
subject
y
x
x
x
Minimize
Your preview ends here
Eager to read complete document? Join bartleby learn and gain access to the full version
- Access to all documents
- Unlimited textbook solutions
- 24/7 expert homework help
Midterm Exam Practice Solution - 4 - OpMgt 301: Principles of Operations Management Yong-Pin Zhou 5.
The personnel department of the A & M Corporation wants to know how many workers will be needed each month for the next six-month production period. The following is a monthly demand forecast for the six-month period. Month Forecasted Demand July 1,250 August 1,100 September 940 October 900 November 1,000 December 1,150 The inventory on hand at the end of June was 500 units. The company would like to have 400 units on hand at the end of December. Each unit requires 5 employee-hours to produce; there are 20 working days each month, and each employee works 8-hour days. The workforce at the end of June was 35 workers. Hiring cost is $200 per worker and firing cost is $1,000 per employee. Monthly inventory holding cost is $5 per unit and monthly backorder cost is $10 per unit. a)
Determine a chase production plan and compute its associated costs. b)
Determine a level production plan and compute its associated costs. When your plan calls for a fractional number of employees, round it up. This would result in a maximum production level that exceeds your planned production level. Assume for this problem that you don't have to produce to the maximum. That is, you can produce the amount determined by your aggregate plan, even if that amount is less than the maximum production level. Chase Plan: First, here is how to deal with initial inventory and ending inventory requirement: subtract the initial inventory from the first month’s demand and add ending inventory requirement to last month’s demand to form the production quantities. As a result, productions for July and December are 750 and 1550 units respectively. Since each unit requires 5 employee-hours to produce and each employee works 160 hours per month, the monthly production rate is 32 units per employee. For July, the demand of 750 units requires 24 (750/32, rounded up). The workforce requirements for the other months are calculated similarly. Note that the assumption here is that the production for each month does not have to be exactly the same as the potential maximum production. For example, in July, 24 people are required due to rounding up. Therefore the potential maximum production is 768, but we will produce only 750. Month Demand Production Inventory Workers Beginning Ending Average Needed Hired Fired July 1250 750 500 0 250 24 0 11 August 1,100 1,100 0 0 0 35 11 0 September 940 940 0 0 0 30 0 5 October 900 900 0 0 0 29 0 1
Midterm Exam Practice Solution - 5 - OpMgt 301: Principles of Operations Management Yong-Pin Zhou November 1,000 1,000 0 0 0 32 3 0 December 1150 1550 0 400 200 49 17 0 Total 500 400 450 31 17 Inventory holding cost = 450 *$5 = $2250. Hiring Cost = 31* $200 = $6,200 Firing Cost = 17 * $1,000 = $17,000 Total Cost = $25,450 Level Plan: Total (revised) demand over the six months is 6,240. Therefore, a level plan would produce 1,040 units each month. This requires a constant workforce of 33 (1,040/32 rounded up). Note that in the following table total demand does not equal to total production because of the initial inventory and ending inventory requirement. If you adjust for that, then they both come out to be 6,240. Month Demand Production Inventory Backorder Workers Beginning Ending Average Needed Hired Fired July 1,250 1040 500 290 395 0 33 0 2 Aug. 1,100 1040 290 230 260 0 33 0 0 Sep. 940 1040 230 330 280 0 33 0 0 Oct. 900 1040 330 470 400 0 33 0 0 Nov. 1,000 1040 470 510 490 0 33 0 0 Dec. 1,150 1040 510 400 455 0 33 0 0 Total 6,340 6240 2330 2230 2280 0 0 2 In this level plan, there are no backorder or hiring costs. Inventory Holding Cost = 2280 * $5 = $11,400 Firing Cost = 2 * $1,000 = $2,000 Total Cost = $13,400 6.
Mr. Meadows Cookie Company makes a variety of chocolate chip cookies in the plant in Spokane, WA. Based on orders received and forecasts of buying habits, it is estimated that the demand for the next four months is 850, 510, 1260, and 980, expressed in thousands of cookies. During a 46-day period when there were 120 workers, the company produced 1.7 million cookies. Assume that the numbers of workdays over the four months are respectively 26, 24, 20, and 16. There are currently 100 workers employed, and there is no starting inventory of cookies. a)
What is the minimum constant workforce required to meet demand over the next four months? b)
Assume that inventory holding cost is 10 cents per cookie per month, hiring cost is $100, and firing cost is $500. Moreover, assume that we will produce to the
Midterm Exam Practice Solution - 6 - OpMgt 301: Principles of Operations Management Yong-Pin Zhou full capacity of the workforce in each month. Evaluate the cost the plan based on the workforce derived in (a). Note that for this problem, once you determine the workforce level (you may need to round up), you always produce at the maximum. Therefore, the total production may in the end exceed the total demand by a small amount. First note that the daily production rate is about 307.97 cookies per worker (1.7mil/46/120). Because there is neither initial inventory nor ending inventory requirement, the total demand over the next four months is 3,600,000 cookies. And the total workdays over the next four months is 86 days. Therefore, a)
the minimum constant workforce required to meet demand over the next four months is 136 (3.6 mil/86/307.97, rounded up). This means 36 people must be hired before the start of the first month. b)
Note that the daily production rate of the workforce derived in (a) is 41,883.92 (=307.97*136). The monthly production will be the product of this number and the number of workdays in that month. Mon. Demand Work days Production Inventor Back-
order Beginning Ending Average 1 850,000 26 1,088,981.92 0 238,981.92 119,490.96 0 2 510,000 24 1,005,214.08 238,981.92 734,196 486,588.96 0 3 1,260,000 20 837,678.4 734,196 311,874.4 523,035.2 0 4 980,000 16 670,142.72 311,874.4 2,017.12 156,945.76 0 Total 3,600,000 3,602,017.12 1,286,060.88 0 In this plan, there are no backorder or firing costs. Inventory Holding Cost = 1,286,060.88 * $0.1 ≈
$128,606.09 Hiring Cost = 36 * $100 = $3,600 Total Cost = $132,206.09 7.
The final assembly of a product (#3001) requires 2 units of #3003, 1 unit of 3002, and 3 units of 3004. Each unit of #3004 is made of 2 units of #3003 and 1 unit of #3005; each unit of #3002 is made of 2 units of #3006 and 4 units of #3004. Each unit of #3004 is in turn made of 2 units of #3003 and 1 unit of #3005. a)
Develop a product structure tree. b)
Low-level code the product structure tree using its network representation.
Your preview ends here
Eager to read complete document? Join bartleby learn and gain access to the full version
- Access to all documents
- Unlimited textbook solutions
- 24/7 expert homework help
Midterm Exam Practice Solution - 7 - OpMgt 301: Principles of Operations Management Yong-Pin Zhou a) (b) 8.
Is there any problem with the following product tree structure? Yes. The problem is that 100 is a component of 322 (right side of the BOM explosion) and
322 is a component of 100 (left side). So we have an “infinite loop” in which we would never complete a single end product. This is easily seen when you draw the graph of the bill of materials: 3
3
2
0
1
3004
3001
3002
3005
3003
2
3006
100 322 End Product 3
3
3
3
2
3001
3003 (2)
3004 (3) 3002
3006 (2)
3004 (4)
3003 (2)
3005
3003 (2)
3005
0
2
2
1
3
Midterm Exam Practice Solution - 8 - OpMgt 301: Principles of Operations Management Yong-Pin Zhou Note the “cycle” that exists between the nodes for 100 and 322. That is, you can follow the arrows around in a closed cycle that visits nodes 100 and 322. The graph of a BOM explosion should never contain such a cycle! 9.
End item “A” has a planned lead-time of two weeks. There are currently 120 units on hand and no scheduled receipts. Week 1 2 3 4 5 6 7 8 9 10 Demand 41 44 84 42 84 86 7 18 49 30 a)
Compute the planned order releases for “A” using the “lot-for-lot” lot-sizing rule. Product A, LT = 2 weeks, LFL Week 1 2 3 4 5 6 7 8 9 10 Gross Requirements 41 44 84 42 84 86 7 18 49 30 Scheduled Receipts Projected On-hand 120
120 79 35 Net Requirements 49 42 84 86 7 18 49 30 Planned-order Receipts 49 42 84 86 7 18 49 30 Planned-order Releases 49 42 84 86 7 18 49 30 (b)
Compute the planned order releases using a 3-week, “fixed-order-period” lot sizing rule. Product A, LT = 2 weeks, FOP=3 weeks Week 1 2 3 4 5 6 7 8 9 10 Gross Requirements 41 44 84 42 84 86 7 18 49 30 Scheduled Receipts Projected On-hand 120
120 79 35 126 84 0 25 18 0 30 Net Requirements 49 86 49 Planned-order Receipts 175 111 79 Planned-order Releases 175 111 79 10.
Suppose that, in order to produce one unit of a particular end item, two units of A and one unit of B are required. In order to produce one unit of A, one unit of C and two units of D are required. In order to produce B, two units of C and three units of E are required. a)
Develop a product tree structure.
Midterm Exam Practice Solution - 9 - OpMgt 301: Principles of Operations Management Yong-Pin Zhou b) Now assume that the MPS for the end item for weeks 1 through 8 is Week
1 2 3 4 5 6 7 8 Demand
100 100 40 40 100 200 200 200 And the Inventory Records is as follows Item On Hand Lead Time Scheduled Receipts Lot Size End Product 130 1 week 50 in week 2 LFL A 60 2 weeks 70 in week 1 LFL B 30 1 weeks 10 in week 2 30 in week 5 FOP, 3 week C 500 2 weeks 300 in week 4 200 in week 6 FOP, 2 weeks D 450 1 week 150 in week 2 LFL E 480 2 weeks 200 in week 1 LFL It is also known that the production of item C has a scrap rate of 5%. Determine the planned order releases for C (be sure to show all the steps you follow to arrive at the final answer). To determine the order releases for C, we need to determine the order releases for the end product, A, and B first. For brevity, we will not consider D and E. End product, LT = 1 weeks, LFL Week 1 2 3 4 5 6 7 8 Gross Requirements 100 100 40 40 100 200 200 200 Scheduled Receipts 50 Projected On-hand 130
130 80 Net Requirements 20 40 40 100 200 200 200 Planned-order Receipts 20 40 40 100 200 200 200 Planned-order Releases 20 40 40 100 200 200 200 Item A, LT = 2 weeks, LFL End product
A (2)
B C
D (2)
C (2)
E (3)
Your preview ends here
Eager to read complete document? Join bartleby learn and gain access to the full version
- Access to all documents
- Unlimited textbook solutions
- 24/7 expert homework help
Midterm Exam Practice Solution - 10 - OpMgt 301: Principles of Operations Management Yong-Pin Zhou Week 1 2 3 4 5 6 7 8 Gross Requirements 40 80 80 200 400 400 400 Scheduled Receipts 70 Projected On-hand 60
130 90 10 Net Requirements 70 200 400 400 400 Planned-order Receipts 70 200 400 400 400 Planned-order Releases 70 200 400 400 400 Item B, LT = 1 weeks, FOP=3 week Week 1 2 3 4 5 6 7 8 Gross Requirements 20 40 40 100 200 200 200 Scheduled Receipts 10 30 Projected On-hand 30
30 20 140 100 30 400 200 0 Net Requirements 20 170 Planned-order Receipts 160 570 Planned
‐
order Releases
160 570 Item C, LT = 2 weeks, FOP=2 weeks Week 1 2 3 4 5 6 7 8 Gross Requirements from A 70 200 400 400 400 Gross Requirements from B 320 1140 Gross Requirements 390 200 400 1540 400 Scheduled Receipts 300 200 Projected On-hand 500
500 110 400 300 400 200 200 200 Net Requirements 90 1240 Planned-order Receipts 490 1640 Planned-order Receipts
§
516 1726 Planned-order Releases 516* 1726 §: here we adjust for scrap rate of 5% by dividing the previous row by 95%, and for simplicity, we have rounded the division results *: indicates a late start. Normally this would be reported in the MRP output. But for brevity we have omitted the output and simply used * to indicate a late start. 11.
Construct an AOA network diagram for the following project. Note that it may require the use of some dummy activities. Activity Follows A Start B Start C Start D A E A, B F C
Midterm Exam Practice Solution - 11 - OpMgt 301: Principles of Operations Management Yong-Pin Zhou G F H F 1. I E, G, H J H 12.
A project consists of seven activities. The precedence relationships are given in the table below. Activity Time (days) Follows A 32 Start B 21 Start C 30 Start D 45 A E 26 A, B F 28 C G 20 E, F i)
Construct an AOA network for this project. ii)
Compute the earliest and the latest starting and finishing times for each activity and identify the critical path. iii)
Which activities will have to be completed by day 60 in order to guarantee that the project will not be delayed? i) 1
2
4
3
6
5
A G E C B 1
2
4
3
8
5
6
7
A G H I F E D C B J D
Midterm Exam Practice Solution - 12 - OpMgt 301: Principles of Operations Management Yong-Pin Zhou ii) Activity ES EF LS LF Slack A 0 32 0 32 0 B 0 21 11 32 11 C 0 30 0 30 0 D 32 77 33 78 1 E 32 58 32 58 0 F 30 58 30 58 0 G 58 78 58 78 0 There are two critical paths: A-E-G and C-F-G. iii) All of the activities with LF
60 should be finished by day 60 in order to guarantee that the project will not be delayed. This includes all activities except D and G. 13.
Problem 3, Chapter 10 of the textbook. n=20, we can also calculate from the table that R
=0.45 and X
=3.10 (a)
First, we focus on the ranges. From table 10-2, D
3
=0.41 D
4
=1.59. Therefore, for the R-chart, UCL = D
4
R
= 1.59*0.45 = 0.7155, LCL=D
3
R
= 0.41*0.45 = 0.1845. All ranges are within these limits. (b)
Next, we construct the X
-Chart. From Table 10-2, A
2
=0.18. Therefore, the limits are R
A
X
2
= 3.1
0.18*0.45. That is, UCL=3.181, LCL=3.019. All means are within these limits. (c)
Therefore, the process is in control. 14.
Problem 9, Chapter 10 of the textbook. 054
.
100
*
16
87
ns
observatio
of
number total
defectives
of
number total
p
Control limits are 044
.
054
.
100
946
.
*
054
.
96
.
1
054
.
)
1
(
n
p
p
z
p
. Hence, UCL = .098 and LCL = .010 The observations must be converted to fraction defective. All points are within these limits so the process appears to be in control. Note: For 95% limits, it means an “out of limit” 5% probability. Since this is two-sided, you need to divide it by 2 to get 2.5%. 1-2.5% = 97.5%. Look in the normal table and find 0.9750. The corresponding z to that probability is 1.96. For those of you not familiar with this process, at least you should remember that z=1.96 corresponds to a 95% control limit. F
Your preview ends here
Eager to read complete document? Join bartleby learn and gain access to the full version
- Access to all documents
- Unlimited textbook solutions
- 24/7 expert homework help
Related Documents
Recommended textbooks for you
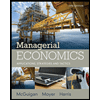
Managerial Economics: Applications, Strategies an...
Economics
ISBN:9781305506381
Author:James R. McGuigan, R. Charles Moyer, Frederick H.deB. Harris
Publisher:Cengage Learning
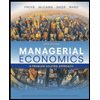
Managerial Economics: A Problem Solving Approach
Economics
ISBN:9781337106665
Author:Luke M. Froeb, Brian T. McCann, Michael R. Ward, Mike Shor
Publisher:Cengage Learning
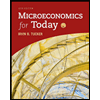
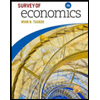
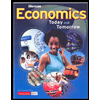
Economics Today and Tomorrow, Student Edition
Economics
ISBN:9780078747663
Author:McGraw-Hill
Publisher:Glencoe/McGraw-Hill School Pub Co
Recommended textbooks for you
- Managerial Economics: Applications, Strategies an...EconomicsISBN:9781305506381Author:James R. McGuigan, R. Charles Moyer, Frederick H.deB. HarrisPublisher:Cengage LearningManagerial Economics: A Problem Solving ApproachEconomicsISBN:9781337106665Author:Luke M. Froeb, Brian T. McCann, Michael R. Ward, Mike ShorPublisher:Cengage Learning
- Economics Today and Tomorrow, Student EditionEconomicsISBN:9780078747663Author:McGraw-HillPublisher:Glencoe/McGraw-Hill School Pub Co
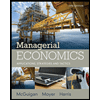
Managerial Economics: Applications, Strategies an...
Economics
ISBN:9781305506381
Author:James R. McGuigan, R. Charles Moyer, Frederick H.deB. Harris
Publisher:Cengage Learning
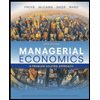
Managerial Economics: A Problem Solving Approach
Economics
ISBN:9781337106665
Author:Luke M. Froeb, Brian T. McCann, Michael R. Ward, Mike Shor
Publisher:Cengage Learning
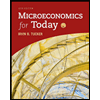
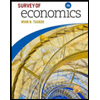
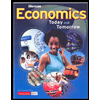
Economics Today and Tomorrow, Student Edition
Economics
ISBN:9780078747663
Author:McGraw-Hill
Publisher:Glencoe/McGraw-Hill School Pub Co