Lab 4_TemperatureCal
.pdf
keyboard_arrow_up
School
Boston University *
*We aren’t endorsed by this school
Course
310
Subject
Mechanical Engineering
Date
Apr 3, 2024
Type
Pages
8
Uploaded by ChancellorMuleMaster163
Temperature Calibration Lab - 1 - ME310 – Instrumentation and Theory of Experiments Lab 4: Temperature Calibration and Measurement CONCEPTS: temperature measurements, RTDs, thermistors, digital data acquisition, LabVIEW GUIs DELIVERABLES: Full lab report (
with
full uncertainty analysis) document, due in 2 weeks, in lab. 1.
Introduction Two important aspects of temperature measurement are choosing the measurement device and obtaining an accurate calibration. Different devices, such as thermistors and resistance temperature detectors each offer advantages and disadvantages in measuring temperature, in the response time and the response function, as well as variations between the many different types of each device that are available. Choosing the appropriate instrument can be a significant factor in obtaining valid results. Equally important is the ability to accurately determine the temperature being measured. Each of the devices mentioned above measures changes in properties other than temperature that can in turn be related to a change in temperature. To measure temperature effectively, an accurate calibration is necessary between the change in properties actually measured and the associated change in temperature. In this lab you will use constant temperature baths to investigate variations in the capabilities and properties of two different temperature measurement devices. You will also calibrate each of the three devices using physical ice points. 2.
Theory Thermistors and resistance temperature detectors (RTDs) measure properties that can be used to determine the temperature of a substance. Whereas thermocouples (discussed in class) use as their thermometric property the voltage that is created between two different metals when two bimetal junctions are at different temperatures, RTDs and thermistors use the fact that as temperature changes, the electrical resistance of materials change (thermistor = thermal + resistor…). In the sections that follow each of these devices is explained briefly.
Temperature Calibration Lab - 2 - 2.1.
Thermistors & RTDs As mentioned above, thermistors and RTDs rely on the fact that the resistivity of a substance changes as its temperature does. The main difference between thermistors and RTD’s is the material from which they are made. Another difference (actually a function of the material and the implementation) is that the response of an RTD is more linear than a thermistor, while the thermistor is more sensitive. RTDs are generally made of a conductive metal. In a conductor the atoms can be thought of being in a regular lattice. The metal’s conduction properties are a result of the lattice: an irregular lattice is a poor conductor compared to a more regular one. As temperature increases the atoms in the lattice shake more, making it more irregular, thus scattering more of the conduction electrons, not allowing them to conduct current. The decrease in the ability to conduct current is seen as an increase in the metal’s resistivity. The response of the resistance R
to the sensed temperature T
can be approximated to be a function of the empirical fit coefficients a
, R
0
, and T
0
:
R ≈
R
0
[1 + a
(
T-T
0
)] Thermistors are generally made from a semi-conducting material, such as a ceramic material. Semiconductors are characterized by having two energy bands (in their electron cloud) separated by an energy gap. The band with a lower energy is called the valence band, while the band with higher energy is called the conduction band. The population of the conduction band of a semi-conductor determines its resistivity. Electrons from the valence band can jump to the conduction band, across the energy gap, if they acquire enough energy. Energy can be added to electrons in the valence band by increasing the temperature. As temperature increases, resistivity goes down, because the population of the conduction band increases. The response of the resistance R
to the sensed temperature T
can be approximated to be a function of the empirical fit coefficients b
, R
0
, and T
0
:
R
≈
R
0
exp[ b
(1/
T-1/T
0
) ] RTDs have a relatively slow response time. With this in mind, they are not usually used for applications in which the temperature varies quickly. Thermistors have a relatively quick response time, and are not as delicate as RTDs, so they can be used in applications that have harsh environmental conditions. Thermistors can be easily packaged in a manner that will allow them to be flat mounted to a device. The use of these devices relies on a calibration of the device, usually obtained by measuring the output of the system as the temperature is varied in a known controlled fashion. Note that the data sheets for the RTD and thermistor that you’ll use in lab isn’t
available because the goal of this lab is to determine the entire sensing system’s response through its calibration. Prelab question
: Research and summarize two commercial systems that incorporate each device (4 systems total).
Temperature Calibration Lab - 3 - 3.
Procedure NOTE: Each student should transfer the data files from the computer, either via transfer to the cloud or your own USB drive. Before beginning the lab, be certain you can identify thermistor and RTD devices. A pdf of both instruments can be found on the course website, since they look similar in appearance. Spot check thought questions: Read through & think about the questions in Section 5. 3.1.
Data Acquisition This lab uses a National Instruments BNC-2090 breakout box connected to the National Instruments PCI-6221 data acquisition board (the same board as lab 3 and the design project) using a 64-pin I/O cable. The input range that the board is set via the LabView VI. Double-check with the GST that it is set to ±10 V.
Constant Temperature Baths Portions of this section may already be in progress at the time you start your lab. Check with the GST to determine the state of each temperature bath. Set the temperature of the five temperature baths as follows: 1. Fill the 0ºC bath approximately 50% full from a cold water tap and add ice as necessary. 2. Fill the 15ºC bath to approximately 70% of capacity from a cold water tap and add ice as necessary until the temperature drops slightly below 15ºC. Allow the temperature to slowly rise to 15ºC. Once at 15ºC, continue to monitor the temperature and add ice as necessary to maintain that temperature. 3. Fill the 30ºC bath from a cold water tap. Allow 30-45 min. for the water to reach 30ºC with the aid of the immersion heaters. 4.
Fill the 45ºC and 60ºC from a hot water tap. Allow 30-45 min. for the water to reach the proper temperature with the aid of the immersion heaters. The immersion heaters draw a lot of current and may cause a ground loop in the form of the 60-Hz AC voltage in conjunction with the rest of the measurement devices. Since the water isn’t deionized, the sensors (thermistors and RTDs), which act as antennas, can pick up this signal and disrupt their voltage output that you’re seeking to measure. Observe the signals on an oscilloscope to identify the different types of noise in the signals. Identify the different noise sources in the system if possible. Employ instrument level filtering provided in the lab such as the Krohn-Hite Model 3940 filter to remove the noise. A DC-coupled lowpass filter with a cutoff frequency of 50 Hz should be sufficient. Use Input & Output Channel 2.
Your preview ends here
Eager to read complete document? Join bartleby learn and gain access to the full version
- Access to all documents
- Unlimited textbook solutions
- 24/7 expert homework help
Related Questions
Pls show step by step solution thank you
arrow_forward
2:45
ull 4G
A moodle1.du.edu.om
1-
A J-Type thermocouple
referenced to 80°F has a
measured output emf of 2.878
mV. What is the temperature of
the measuring junction?
2- Assume that the measured
temperature is 250° F, what
should be the output voltage if
the reference temperature is 90
°F.
RK: if the temperature values are
not in the table, you have to use
interpolation.
Response to question 2: The
measured output voltage (mV)
Select one:
O a. 2.764
b. 4.769
c. 5.762
O d. 3.768
arrow_forward
A. A customer asked you to explain your choice of a temperature sensor that you used for his PCB.
Initially, there were two sensor options. To compare between them, you decided to test their accuracy
and precision. Accuracy of a sensor is a measure of how near its reading is to the real value, the nearer
the measured value to the real value the better. While precision is a measure of how widely spread the
readings of a sensor are [relative to each other] when measuring the same variable, the narrower the
spread the better. So, you tested the two sensors by measuring the same temperature, which was 100
C of boiling water, and you recorder the following 10 measurements of each sensor. Which Sensor has
higher accuracy, and which one has higher precision.
Sensor
Sensor readings when measuring 100 C
99.65
100.05
103
102
99.3
s1
100.1
99.1
100.5
99
98.8
98.78
96.9
101.4
98.88
99
S2
99.12
98.9
99
98.69
99.2
arrow_forward
QUESTION 2
Thermocouples are devices used to measure temperature of a given sample or the surrounding
medium. These devices feature a "bead", which has a spherical shape, and produces voltage upon change
in temperature. For an engineering application at a pharmaceutical company, thermocouple devices are
being tested for their responsiveness, i.e. how fast it can detect temperature changes in the environment
(surrounding air). The engineers at this company have specified design constraints for an ideal
thermocouple: it must detect temperature changes no later than 1.5 minute, and the reported
temperature value must be reasonably correct: at most %3 difference between measured and actual
temperature values is allowed.
Four thermocouples from different vendors are being tested. Relevant properties of these devices are
listed below:
Thermal conductivity Density
36 W/m*K
36 W/m*K
42 W/m*K
33 W/m*K
Specific Heat
140 kJ/kg*K
120 kJ/kg*K
150 kJ/kg*K
160 kJ/kg*K
Device
Bead Diameter…
arrow_forward
Record the dimensions of the known (calibration) block using the caliper and dial gauge on the table below. Indicate the
units of each measurement. Calculate the average length of each side of the block.
Dimension
Caliper (Units)
0.995
1.455
0.985
Ruler(in) A: 0.9
B: 1.5
C: 0.9
A
B
C
Dimension
A
B
Instrument
Use the average dimensions (see Problem 2a) of the known block to calibrate the LVDT at your workstation. Record the
voltage on the table below:
LVDT Offset: 0.556 (Do not include the offset value in your average dimensions)
C
Ave Dimension (Units)
(Dial Gauge)
0.997
1.659
0.949
0.964 in
1.538 in
0.945 in
oltage
Average Dimension
1.244 volt
1.994
1.28
0.964 in
1.538 in
0.945 in
arrow_forward
Truncation errors are increased as the round-off errors are decreased.Group of answer choices True False
Say, you have a thermometer and you are checking the temperature of a body that has a temperature of 36o Using your thermometer five times, it gives you the following measurements: 29oC, 29.2oC, 29.3oC, 28.9oC, and 29.1oC. What can we conclude about the accuracy and the precision of the thermometer?Group of answer choices The thermometer is not accurate and not precise The thermometer is faulty. The thermometer is accurate and precise The thermometer is not accurate but precise.
Say, you have a thermometer and you are checking the temperature of a body that has a temperature of 36o Using your thermometer five times, it gives you the following measurements: 36oC, 35.6oC, 36oC, 37oC, and 36.2oC. What can we conclude about the accuracy and the precision of the thermometer?Group of answer choices The thermometer is accurate and precise. The thermometer is accurate but not precise. The…
arrow_forward
Task 3-a:
If you have four instruments used to measure a temperature of 50.02 C inside the factory. However, the
instruments gave different readings for different trials as follows:
Instrument 1 20
30
40
50
60
70
80
51
49
Instrument 2 49
49
49
49
49
49
49
49
49
Instrument 3 48.01
48.03
49.02
49.01
50.00
48.02
47.09
47.05
47.80
Instrument 4 17.01
17.02
17.09
17.03
17.01
17.03
15.09
19.02
17.00
1. Define the resolution of an instrument.
2. Define the sensitivity of an instrument, then explain how the sensitivity of an instrument can
be calculated.
3. Define the accuracy of an instrument system and explain using your own words how the
accuracies of different instruments are compared.
4. Define the precision of an instrument system and explain using your own words how the
precisions for different instruments are compared.
arrow_forward
Chapter 3:
13. What type of geometric tolerance has no datum features?
14. A theoretically exact dimension is called a
15. The
feature symbol specifies that a group of two or more interrupted features of size are to be considered one single feature of size.
16. For an individual regular feature of size, no element of the feature shall extend beyond the maximum material condition boundary (envelope) of perfect form. This statement is the essence of
17. What is the name of the symbol used to identify physical features of a part as a datum feature and must not be applied to centerlines, center planes, or axes?
18. The
is the condition in which a feature of size contains the maximum amount of material within the stated limits of size.
19. The total positional tolerance equals the sum of the
tolerance and the
tolerance.
arrow_forward
A chamber of unknown volume is filled with an unknown amount of ideal gas. A cylinder with an open bottom and calibrated volume is connected to the chamber and is closed with a movable piston. A gas pressure sensor is also mounted on the chamber as shown in the figure. The whole experimental setup is kept at a constant temperature of 300 K. Doris moves the piston from mark 0 to mark 200 mL in steps of 50 mL and records the corresponding pressure in the chamber (see the table below). She moves the piston very slowly and waits several minutes before recording the pressure values.
VCyl(mL)
P(105N/m2))
0
4.35
50
3.85
100
3.50
150
3.15
200
2.90
Determine the volume of the chamber using Doris's data in the table. (Note: This is a problem that requires linearization of data.)
Determine the number of moles of gas. (Note: This is a problem that requires linearization of data.)
arrow_forward
Lab 2-Measurement Asynch - Tagged.pdf
Page 4 of 7
?
Part I: Taking Measurements & Estimating Uncertainties for a single measurement
www.stefanelli.eng.br
The mass of the object is_
0
i
Parts on a tripie peam palance
0
0
10 20 30
1
100
2 3
40
200
4
+/-
50 60 70
5
300
7
400
80
Qv Search
8
90
9
500
100
9
10 g
www.stefanelli.eng.br
arrow_forward
ISOBARIC PROCESS / ISOMETRIC PROCESS
answer D please fast. Thank you!!!
arrow_forward
e IY: %VY OLD ?
د ميکانيك شهري 2021.pdf
UNIVERSITY OF BASRAH - COLLEGE OF ENGINEERING
DEPARTMENT OF CIVIL ENGINEERING
Subject: Engineering Mechanics-Static
Class: 1st year, 1st term
Exam. : Semester
Date: 16/3/2021
Examiner: Dr. Mazin, Dr. Aqeel, Dr.Ahid and Dr.Jaffar
Time: 1.5Hours
Q1] (10 Marks)
A- In Fig.A , If the resultant force acting on the bracket is to be 642 N directed
along the positive x axis, determine the magnitude of F.
B- In Fig.B , Determine the magnitude of the resultant force acting on the screw
eye and its direction measured clockwise from the x axis.
C- In Fig.C , Resolve the 100N force into components along the u and v axes, and
determine the magnitude of each of these components.
D- In Fig.D, Determine the moment of the force about point O.
300 N
60N
25°
32
45°
60°
505 N
50°
40N
Fig. A
50 N
Fig. B
400 N
100N
28°
18
2.12 m
Fig. C
2.12 m
Fig.D
Q2] (10 Marks)
A- In Fig.A , Replace the loading system by an equivalent resultant force and
specify where the resultant's…
arrow_forward
Datum dimension the isometric view
arrow_forward
b) A linear variable displacement transducer (LVDT) senses displacement and indicates a
voltage output, which is linear to the input. Figure 1 shows an LVDT setup used for static
calibration. It uses a micrometre to apply the known displacement and a voltmeter for the
output.
i) Suggest the independent, dependent and extraneous variables in this calibration.
ii) Indicate the basic functional elements of the device in Figure 1 in the form of block
diagram.
10
Micrometer
Fixed mounts
Connector
Excitation
voltage
in
Figure 1
Primary coil
xx_w_
LVDT
E
Output
voltage
10.135
Voltmeter
Secondary coil
Core
arrow_forward
Newton's Law of cooling states that the rate at which heat is lost by a heated body is
proportional to the difference in temperature between the body and the surrounding
medium. Match the following statements/phrases with the corresponding item in the
drop down box. Choices in the box
1. In accordance with the stated law obove, we have the equation?
2. If a thermometer is taken outdoors where the temperoture is 5 deg C, from a
room in which the temperature is 20 deg C and the reading drops 10 deg C in one
minute, the working equation is?
3. In the obove problem, separoting the variables and integrating will result to?
4. In the obove problem, how long, in minutes, after its removal from the room will
the reading be 6 deg C?
5. In the obove problem, ofter 30 seconds, whot will be the thermometer reading?
5.2
dT(body temp)/dt = k(Temp of medium - 5)
dr(body temp)/dt = k(Temp of body - Temp of medium)
Temp of body = Cenkt +5
2.5
13.7
dr(body temp)/dt = k(Temp of medium - Temp of body)…
arrow_forward
Q (2): A laboratory experiment has been executed to calculate the thermal conductivity of a specimen.
The specimen is a bar with (Diameter= 0.04 m) and (length = 0.06 m). At steady state condition, the
following data have been recorded:
Voltage(V) Current(A)
8
0.8
T₁ (°C)
46.8
T₂ (°C) T3 (°C)
42.2
34.6
T. (°C)
31.4
By taking into consideration that the temperature changes linearly
with position, refer to the figure aside, and calculate
he thermal conductivity for the specimen (intermediate section).
T₂
T₂
The face
Told face
T₂
T₂
6 cm
4 cm
6 cm
4 cm
6 cm
Hot section
Int. section
Cold section
arrow_forward
2) A device used in a ground radar system has age to failure that is described approximately by a
Weibull distribution with mean life 83 h, shape parameter 1.5, and location parameter zero.
When it fails it takes on average 3.5 h to repair:
a) Calculate the reliability over a 25 h period, and the 'steady state' availability of the device.
b) Calculate the reliability over 25 h, and the ‘steady state' availability of a subsystem that
consists of two of these devices in active parallel redundancy.
arrow_forward
6.
Determine the correct statement
Mark only one oval.
It is preferable to have a temperature sensor or pressure sensor with non-linear
response to the measured property
Density is an extensive property
Sum of the macroscopic energies of the pure substances is called internal energy
Work transfer out of the system is taken to be negative as convention
None of the given
7. Tyre pressure is 2 bar of gage pressure and it has volume of 14 litres. Determine the
density inside the tyre if the tyre is in thermal equilibrium with the environment at 25
arrow_forward
a) Describe static sensitivity and time constant of instrument?b) A thermometer having a time constant of 1 min is initially at 50 oC. It is immersedin a bath maintained at 100 oC at time = 0. Express temperature in oC at time = 1.2min
arrow_forward
Berserk - Chapter 2- Read Berserk
compressor.
reggienet.illinoisstate.edu
https://reggienet.illinoisstate.edu/access/content/attachment/f6b18576-acf9-...
Hint. Both power-sizing and indexing will be used.
Ć
+
Question 3. The purchase price of a natural gas-fired commercial boiler (capacity X) was $181,000 eight years
ago. Another boiler of the same basic design, except with the capacity 1.42X, is currently being considered for
purchase. If it is purchased, some optional features presently costing $28,000 would be added for your
application. If the cost index was 162 for this type of equipment when the capacity X boiler was purchased and
is 221 now, and the applicable cost capacity factor is 0.8, what is your estimate of the purchase price for the
new boiler?
Hint: Use both indexing and power-sizing methods.
88
Illinois State University: TEC 330 001 FA2022 - Applied Economic Analysis For...
arrow_forward
EXPERIMENT -1- TEMPERATURE MEASUREMENT AND
CALIBRATION
Discussion
4-State any possible error source in the experiment?
5-State any suggestions to improve the experiment?
arrow_forward
4:07
3G l.
Moodle
A bbb2.du.edu.om
EE
...Session (15-3-
Said Grami O
College of Engineering
Vision for the Future
Question 3
During a step function calibration, a first-order instrument
is exposed to a step change of 200 units.
1- If after 1.5 s the instrument indicates 140 units, find the
instrument time constant.
2- find the error in the indicated value after 2 s
S.
3- Find the raise time at 90 % of the system.
y(0)=0 units; K=1 unit/unit.
Question 4
A first order instrument with a time constant of 2 seconds is to
be used to measure a periodic input. If a dynamic error of
±2% can be tolerated,
1- determine the maximum frequency of periodic input that
can be measured.
2- What is the associated time lag (in seconds) at that
frequency?
MECH374: Instrumentation and Measurement
Said Grami
Practice
arrow_forward
The rate of infections with respect to time t (measured in days) within a population is
seen to be rising exponentially according to the relation:
I = e(k–1)t (Infections per day)
This occurs over a period of 20 days from time t =
[0, 20], where k = 1.4.
a)
What is the period of time t required for the initial infection rate I(t = 0) to double
in number? State answer to within 3 decimal places.
arrow_forward
E and 5 v X
O file:///C:/Users/Hp/Desktop/mm/OUTCOME%20NO.2%20and%205%20with%20Problems.pdf
+
O Fit to page
D Page view
A Read aloud
1 Add notes
Problems
1. A brass rod of diameter 25 mm and length 250 mm is
subjected to a tensile load of 50 kN and the extension of
the rod is equal to 0.3 mm. Find the Young's Modulus or
Modulus of Elasticity.
99+
to search
hp
delete
prt sc
14 DI
backs
&
7
8
24
4
P
EJR
-0
J
K
H
D.
F
arrow_forward
THERMODYNAMICS 2 SUBJECT
Pleaseee answer with complete handwritten solution, Schematic and TS diagram with correct dimension analysis. Thankssss! I'll give a thumbs up. ❤️
arrow_forward
Discussion:
1) discuss the methods of temperature measurement.
2) What is the reference of thermometers calibration tool?
3) What is the meaning of the temperature? What its units?
4) What is the faster method of temperature measurement?
4) Do you have another method or appearance that may be used temperature measurement?
arrow_forward
Q:02
Write Down the application of manufacturing processes in the field of mechanical Engineering?
arrow_forward
The left side of this equation tells how much energy Q the cylinder gives to the water while it cools. The right
side of this equation tells how much energy Q the water and aluminum cup absorb from the cylinder to warm
up. Because it is the same energy, they are equal.
What is known in this equation?
Mcyl
411.7 g, malum
46.5 g, malum+water
= 175 g
Can you find: mwater =? g
Twater = Talum = 20°C (water and cup of room temperature)
90°C, T; = 35°C (hot cylinder and cool "cylinder+cup+water" temperatures)
Tcyl
kCal
Calum = 0.22, Cwater
1 (specific heat of water and aluminum, measured in units
kg-°C
What are we looking for is Ccul - How we find it? Plug all the numbers into the equation (1), Ccul will be one
unknown which you can calculate from the equation. Important, convert all the masses from grams to kilograms!
After
you find Ccyl, compare it to known value for the copper 0.093(our cylinder is made out of copper).
|Ceyl -0.093|
% :
· 100%
0.093
arrow_forward
Read each statement carefully and answer by True or False (if False then, correct
the statement).
1- Process control combines how physics, chemistry, and biology work in
operating equipment and an understanding of dynamic systems.
2- When a second letter is used in instrumentation symbols, e.g., Pressure
Indicator Controller (PIC), it defines the measured or initiating variables.
3- P&ID contains the sensor details such as physical principle and
measurement range.
4- FRC 82516: Flow Recording Controller, area no 825, process unit 8, loop
number 16.
5- P&ID excludes equipment identification.
arrow_forward
b) Figure 1 shows the calibration data of a sensor. Determine the static sensitivity at the
input of X= 0, X= 5 and X= 10. For which input values is the system more sensitive?
Calibration Data
300
250
y = 0.875x1.055
200
150
100
50
20
40
60
80
100
120
Input value, cm
Figure 1
c) Suppose you found a dial thermometer in a stockroom. Discuss several methods by
which you might estimate random and systematic error in the thermometer? How
would you estimate its uncertainty?
Output value, V
arrow_forward
3. a) With neat diagram, State the principle of RTD sensor
b) A platinum resistance thermometer has a resistance of 100 ohm at 25°C. The Resistance temperature
coefficient of platinum is 0.00392 ohm/ohm°C.
(i) Find its resistance at 700C
(ii) Let the thermometer has a resistance of 400 ohm, calculate the value of temperature.
arrow_forward
SEE MORE QUESTIONS
Recommended textbooks for you
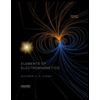
Elements Of Electromagnetics
Mechanical Engineering
ISBN:9780190698614
Author:Sadiku, Matthew N. O.
Publisher:Oxford University Press
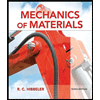
Mechanics of Materials (10th Edition)
Mechanical Engineering
ISBN:9780134319650
Author:Russell C. Hibbeler
Publisher:PEARSON
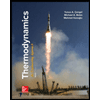
Thermodynamics: An Engineering Approach
Mechanical Engineering
ISBN:9781259822674
Author:Yunus A. Cengel Dr., Michael A. Boles
Publisher:McGraw-Hill Education
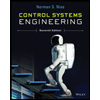
Control Systems Engineering
Mechanical Engineering
ISBN:9781118170519
Author:Norman S. Nise
Publisher:WILEY
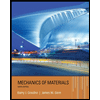
Mechanics of Materials (MindTap Course List)
Mechanical Engineering
ISBN:9781337093347
Author:Barry J. Goodno, James M. Gere
Publisher:Cengage Learning
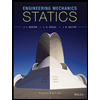
Engineering Mechanics: Statics
Mechanical Engineering
ISBN:9781118807330
Author:James L. Meriam, L. G. Kraige, J. N. Bolton
Publisher:WILEY
Related Questions
- Pls show step by step solution thank youarrow_forward2:45 ull 4G A moodle1.du.edu.om 1- A J-Type thermocouple referenced to 80°F has a measured output emf of 2.878 mV. What is the temperature of the measuring junction? 2- Assume that the measured temperature is 250° F, what should be the output voltage if the reference temperature is 90 °F. RK: if the temperature values are not in the table, you have to use interpolation. Response to question 2: The measured output voltage (mV) Select one: O a. 2.764 b. 4.769 c. 5.762 O d. 3.768arrow_forwardA. A customer asked you to explain your choice of a temperature sensor that you used for his PCB. Initially, there were two sensor options. To compare between them, you decided to test their accuracy and precision. Accuracy of a sensor is a measure of how near its reading is to the real value, the nearer the measured value to the real value the better. While precision is a measure of how widely spread the readings of a sensor are [relative to each other] when measuring the same variable, the narrower the spread the better. So, you tested the two sensors by measuring the same temperature, which was 100 C of boiling water, and you recorder the following 10 measurements of each sensor. Which Sensor has higher accuracy, and which one has higher precision. Sensor Sensor readings when measuring 100 C 99.65 100.05 103 102 99.3 s1 100.1 99.1 100.5 99 98.8 98.78 96.9 101.4 98.88 99 S2 99.12 98.9 99 98.69 99.2arrow_forward
- QUESTION 2 Thermocouples are devices used to measure temperature of a given sample or the surrounding medium. These devices feature a "bead", which has a spherical shape, and produces voltage upon change in temperature. For an engineering application at a pharmaceutical company, thermocouple devices are being tested for their responsiveness, i.e. how fast it can detect temperature changes in the environment (surrounding air). The engineers at this company have specified design constraints for an ideal thermocouple: it must detect temperature changes no later than 1.5 minute, and the reported temperature value must be reasonably correct: at most %3 difference between measured and actual temperature values is allowed. Four thermocouples from different vendors are being tested. Relevant properties of these devices are listed below: Thermal conductivity Density 36 W/m*K 36 W/m*K 42 W/m*K 33 W/m*K Specific Heat 140 kJ/kg*K 120 kJ/kg*K 150 kJ/kg*K 160 kJ/kg*K Device Bead Diameter…arrow_forwardRecord the dimensions of the known (calibration) block using the caliper and dial gauge on the table below. Indicate the units of each measurement. Calculate the average length of each side of the block. Dimension Caliper (Units) 0.995 1.455 0.985 Ruler(in) A: 0.9 B: 1.5 C: 0.9 A B C Dimension A B Instrument Use the average dimensions (see Problem 2a) of the known block to calibrate the LVDT at your workstation. Record the voltage on the table below: LVDT Offset: 0.556 (Do not include the offset value in your average dimensions) C Ave Dimension (Units) (Dial Gauge) 0.997 1.659 0.949 0.964 in 1.538 in 0.945 in oltage Average Dimension 1.244 volt 1.994 1.28 0.964 in 1.538 in 0.945 inarrow_forwardTruncation errors are increased as the round-off errors are decreased.Group of answer choices True False Say, you have a thermometer and you are checking the temperature of a body that has a temperature of 36o Using your thermometer five times, it gives you the following measurements: 29oC, 29.2oC, 29.3oC, 28.9oC, and 29.1oC. What can we conclude about the accuracy and the precision of the thermometer?Group of answer choices The thermometer is not accurate and not precise The thermometer is faulty. The thermometer is accurate and precise The thermometer is not accurate but precise. Say, you have a thermometer and you are checking the temperature of a body that has a temperature of 36o Using your thermometer five times, it gives you the following measurements: 36oC, 35.6oC, 36oC, 37oC, and 36.2oC. What can we conclude about the accuracy and the precision of the thermometer?Group of answer choices The thermometer is accurate and precise. The thermometer is accurate but not precise. The…arrow_forward
- Task 3-a: If you have four instruments used to measure a temperature of 50.02 C inside the factory. However, the instruments gave different readings for different trials as follows: Instrument 1 20 30 40 50 60 70 80 51 49 Instrument 2 49 49 49 49 49 49 49 49 49 Instrument 3 48.01 48.03 49.02 49.01 50.00 48.02 47.09 47.05 47.80 Instrument 4 17.01 17.02 17.09 17.03 17.01 17.03 15.09 19.02 17.00 1. Define the resolution of an instrument. 2. Define the sensitivity of an instrument, then explain how the sensitivity of an instrument can be calculated. 3. Define the accuracy of an instrument system and explain using your own words how the accuracies of different instruments are compared. 4. Define the precision of an instrument system and explain using your own words how the precisions for different instruments are compared.arrow_forwardChapter 3: 13. What type of geometric tolerance has no datum features? 14. A theoretically exact dimension is called a 15. The feature symbol specifies that a group of two or more interrupted features of size are to be considered one single feature of size. 16. For an individual regular feature of size, no element of the feature shall extend beyond the maximum material condition boundary (envelope) of perfect form. This statement is the essence of 17. What is the name of the symbol used to identify physical features of a part as a datum feature and must not be applied to centerlines, center planes, or axes? 18. The is the condition in which a feature of size contains the maximum amount of material within the stated limits of size. 19. The total positional tolerance equals the sum of the tolerance and the tolerance.arrow_forwardA chamber of unknown volume is filled with an unknown amount of ideal gas. A cylinder with an open bottom and calibrated volume is connected to the chamber and is closed with a movable piston. A gas pressure sensor is also mounted on the chamber as shown in the figure. The whole experimental setup is kept at a constant temperature of 300 K. Doris moves the piston from mark 0 to mark 200 mL in steps of 50 mL and records the corresponding pressure in the chamber (see the table below). She moves the piston very slowly and waits several minutes before recording the pressure values. VCyl(mL) P(105N/m2)) 0 4.35 50 3.85 100 3.50 150 3.15 200 2.90 Determine the volume of the chamber using Doris's data in the table. (Note: This is a problem that requires linearization of data.) Determine the number of moles of gas. (Note: This is a problem that requires linearization of data.)arrow_forward
- Lab 2-Measurement Asynch - Tagged.pdf Page 4 of 7 ? Part I: Taking Measurements & Estimating Uncertainties for a single measurement www.stefanelli.eng.br The mass of the object is_ 0 i Parts on a tripie peam palance 0 0 10 20 30 1 100 2 3 40 200 4 +/- 50 60 70 5 300 7 400 80 Qv Search 8 90 9 500 100 9 10 g www.stefanelli.eng.brarrow_forwardISOBARIC PROCESS / ISOMETRIC PROCESS answer D please fast. Thank you!!!arrow_forwarde IY: %VY OLD ? د ميکانيك شهري 2021.pdf UNIVERSITY OF BASRAH - COLLEGE OF ENGINEERING DEPARTMENT OF CIVIL ENGINEERING Subject: Engineering Mechanics-Static Class: 1st year, 1st term Exam. : Semester Date: 16/3/2021 Examiner: Dr. Mazin, Dr. Aqeel, Dr.Ahid and Dr.Jaffar Time: 1.5Hours Q1] (10 Marks) A- In Fig.A , If the resultant force acting on the bracket is to be 642 N directed along the positive x axis, determine the magnitude of F. B- In Fig.B , Determine the magnitude of the resultant force acting on the screw eye and its direction measured clockwise from the x axis. C- In Fig.C , Resolve the 100N force into components along the u and v axes, and determine the magnitude of each of these components. D- In Fig.D, Determine the moment of the force about point O. 300 N 60N 25° 32 45° 60° 505 N 50° 40N Fig. A 50 N Fig. B 400 N 100N 28° 18 2.12 m Fig. C 2.12 m Fig.D Q2] (10 Marks) A- In Fig.A , Replace the loading system by an equivalent resultant force and specify where the resultant's…arrow_forward
arrow_back_ios
SEE MORE QUESTIONS
arrow_forward_ios
Recommended textbooks for you
- Elements Of ElectromagneticsMechanical EngineeringISBN:9780190698614Author:Sadiku, Matthew N. O.Publisher:Oxford University PressMechanics of Materials (10th Edition)Mechanical EngineeringISBN:9780134319650Author:Russell C. HibbelerPublisher:PEARSONThermodynamics: An Engineering ApproachMechanical EngineeringISBN:9781259822674Author:Yunus A. Cengel Dr., Michael A. BolesPublisher:McGraw-Hill Education
- Control Systems EngineeringMechanical EngineeringISBN:9781118170519Author:Norman S. NisePublisher:WILEYMechanics of Materials (MindTap Course List)Mechanical EngineeringISBN:9781337093347Author:Barry J. Goodno, James M. GerePublisher:Cengage LearningEngineering Mechanics: StaticsMechanical EngineeringISBN:9781118807330Author:James L. Meriam, L. G. Kraige, J. N. BoltonPublisher:WILEY
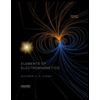
Elements Of Electromagnetics
Mechanical Engineering
ISBN:9780190698614
Author:Sadiku, Matthew N. O.
Publisher:Oxford University Press
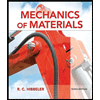
Mechanics of Materials (10th Edition)
Mechanical Engineering
ISBN:9780134319650
Author:Russell C. Hibbeler
Publisher:PEARSON
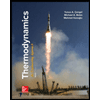
Thermodynamics: An Engineering Approach
Mechanical Engineering
ISBN:9781259822674
Author:Yunus A. Cengel Dr., Michael A. Boles
Publisher:McGraw-Hill Education
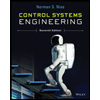
Control Systems Engineering
Mechanical Engineering
ISBN:9781118170519
Author:Norman S. Nise
Publisher:WILEY
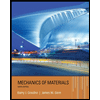
Mechanics of Materials (MindTap Course List)
Mechanical Engineering
ISBN:9781337093347
Author:Barry J. Goodno, James M. Gere
Publisher:Cengage Learning
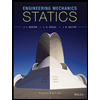
Engineering Mechanics: Statics
Mechanical Engineering
ISBN:9781118807330
Author:James L. Meriam, L. G. Kraige, J. N. Bolton
Publisher:WILEY