Lab 2 AME 324L
pdf
School
University Of Arizona *
*We arenβt endorsed by this school
Course
324L
Subject
Mechanical Engineering
Date
Jan 9, 2024
Type
Pages
8
Uploaded by MagistrateStrawJellyfish60
Beam Bending
Aditya Kannan
AME 324L
9/18/2023
NOTE TO GRADER: I spoke with the TA in class today and he
allowed me to submit the report before midnight instead
of 5 PM. Thank you!
Introduction
In this experimental investigation, our focus will be on beam stress and bending. We will employ strain
gauges strategically positioned along an I-beam and vary their distances from a fixed clamp as well as a
dial gage to measure the deflection of the beam in a simple manner. Subsequently, we will subject the
beam to diverse loads applied at two different points near its extremity. By collecting data pertaining to
strain, load magnitudes, and distances, we will apply Hooke's law and the flexure formula, accompanied
by moment diagrams/equations, to determine the strain response of the beam to a load.
Discussion of relevant concepts
The primary objective of this experiment is to understand the behavior of a beam when subject to
bending by loading a cantilevered I-beam and gathering data on its response. In the following
paragraphs, we will go over the equations that govern the response of beams to bending moments. The
first among them is the flexure formula, as depicted below, where
?
represents the bending moment,
?
signifies the location for stress assessment, and
πΌ
stands for the second moment of area.
π = β
??
πΌ
Now, below is the equation for shear stress due to bending.
π
is the shear stress due to applied loads,
?
is the first moment of area and
πΌ
is the second moment of area.
π =
π?
ππΌ
The distribution of normal stress is linear, where the max stress is at the top and bottom of the beam
pointing in opposite directions. The distribution of shear stress is a parabola with the focus located at the
central axis of the beam.
Deflection is a useful piece of data gathered from this experiment using a dial gauge, and the theoretical
deflection can be calculated as below.
πΏ =
??
2
6?πΌ
β (3? β ?)
Now, here are drawn shear force and bending moment diagrams for cantilever and 3-point bending
configuration beams.
Figure 1: Shear and moment diagrams for different configurations of a loaded beam
Experimental Procedure
A 6061 Aluminum I-Beam, firmly attached to the testing table, is used as the cantilever beam for
experimentation. Two strain gauges each are attached at 3 locations on the beam. The measurements
were recorded using LabView and a dial gage.
After configuring the LabView software and ensuring that the strain gage connections were in good
condition, the dial gauge was placed on the beam at a measured location. Then, the position of the
beam was adjusted in order to locate the testing machine head above a specified location. The LabView
recording was started and the load was applied up to specific values (
100, 200, 250 ?ππ
) and a photo of
the strain and load data from LabView and the dial gage deflection was recorded. This process was
performed again with the beam moved to a different position in order to understand how the deflection
changed by varying the distance of the load from the cantilever.
Results & Calculations
Now we calculate the moment of inertia of the I-beam based on measurements taken during the
experiment using the following formula:
πΌ
π₯
=
1
3
πβ
3
β
1
12
π
1
β
1
3
β
1
12
π
2
β
2
3
Where:
Your preview ends here
Eager to read complete document? Join bartleby learn and gain access to the full version
- Access to all documents
- Unlimited textbook solutions
- 24/7 expert homework help
β’
πΌ?
is the moment of inertia about the x-axis.
β’
π
is the width of the entire I-beam cross-section.
β’
β
is the height of the entire I-beam cross-section.
β’
π
1
and
β
1
are the width and height of the smaller rectangular section (the web) of the I-beam.
β’
π
2
and
β
2
are the width and height of each of the larger rectangular sections (the flanges) of the
I-beam.
Therefore:
πΌ
π₯
=
1
3
(0.0258)(0.2532)
3
β
1
12
(0.0357)(0.127)
3
β
1
12
(0.0258)(0.063)
3
= ?. ?? β ??
β?
?π ?
?
= ?. ???? ?π π?
?
The area is calculated to be
12.15 π?
2
We take the Youngβs Modulus (
?
) to be
10
6
ππ π
.
Raw Data from Strain Gauges
Table 2: Measured load vs strain at location 1 (0.0131m from cantilever)
Load
Location
1 (lb)
White
Red
Green
Blue
Yellow
Purple
Orange
100
-0.00013
-0.0005
9.93E-06
1.14E-05
0.002114
0.000291
1.22E-05
200
-0.00027
-0.00102
8.29E-06
1.9E-05
0.000459
0.000624
9.6E-06
250
-0.00034
-0.00128
8.53E-06
2.42E-05
0.000595
0.000793
1.82E-05
Load
Location
1 (lb)
White
Red
Green
Blue
Yellow
Purple
Orange
100
-1.30E-04
-0.0005
8.78E-06
1.04E-05
2.10E-03
2.92E-04
1.06E-05
200
-2.70E-04
-2.70E-03
5.94E-06
1.95E-05
4.57E-04
6.25E-04
1.02E-05
250
-3.30E-04
-0.00127
7.64E-06
2.34E-05
5.96E-04
7.92E-04
1.07E-05
Load
Location
1 (lb)
White
Red
Green
Blue
Yellow
Purple
Orange
100
-1.32E-04
-0.0005
8.62E-06
9.59E-06
2.07E-03
2.91E-04
8.27E-06
200
-2.70E-04
-0.00102
6.86E-06
1.97E-05
4.60E-04
6.26E-04
1.02E-05
250
-3.35E-04
-0.00128
6.68E-06
2.49E-05
5.96E-04
7.91E-04
1.15E-05
Table 3: Measured load vs strain at location 2 (0.0115m from cantilever)
Load
Location
2 (lb)
White
Red
Green
Blue
Yellow
Purple
Orange
100
4.24E-06
-0.00022
-1.69E-05
-1.74E-06
9.71E-05
-5.80E-05
2.08E-05
200
1.50E-06
-0.00044
-1.65E-05
-3.50E-06
1.83E-04
-2.22E-05
1.67E-05
250
2.12E-06
-0.00055
-1.74E-05
2.06E-06
2.35E-04
-8.33E-07
2.02E-05
Load
Location
2 (lb)
White
Red
Green
Blue
Yellow
Purple
Orange
100
2.99E-06
-0.00022
-1.69E-05
-1.64E-06
9.56E-05
-5.69E-05
1.96E-05
200
2.02E-06
-0.00044
-1.77E-05
-2.94E-06
1.84E-04
-2.18E-05
1.83E-05
250
1.24E-06
-0.00055
-1.73E-05
1.36E-07
2.34E-04
-9.94E-07
2.03E-05
Load
Location
2 (lb)
White
Red
Green
Blue
Yellow
Purple
Orange
100
2.41E-06
-0.00022
-1.74E-05
4.61E-08
9.45E-05
-5.92E-05
2.03E-05
200
-2.32E-07
-0.00044
-1.57E-05
-5.49E-07
1.84E-04
-2.13E-05
2.10E-05
250
3.05E-06
-0.00055
-1.65E-05
9.64E-07
2.35E-04
-9.04E-08
1.92E-05
Averaged Trials from Strain Gauges
Table 3: Measured load vs average strain at location 1 (0.0131m from cantilever)
Load
Location
1 (lb)
White
Red
Green
Blue
Yellow
Purple
Orange
100
-1.31E-04
-5.00E-04
9.11E-06
1.05E-05
2.09E-03
2.91E-04
1.04E-05
200
-2.70E-04
-1.58E-03
7.03E-06
1.94E-05
4.59E-04
6.25E-04
9.99E-06
250
-3.35E-04
-1.28E-03
7.61E-06
2.42E-05
5.96E-04
7.92E-04
1.35E-05
Table 3: Measured load vs average strain at location 2 (0.0115m from cantilever)
Load
Location
2 (lb)
White
Red
Green
Blue
Yellow
Purple
Orange
100
3.21E-06
-2.18E-04
-1.71E-05
-1.11E-06
9.57E-05
-5.80E-05
2.02E-05
200
1.10E-06
-4.40E-04
-1.66E-05
-2.33E-06
1.84E-04
-2.18E-05
1.87E-05
250
2.14E-06
-5.50E-04
-1.71E-05
1.05E-06
2.35E-04
-6.39E-07
1.99E-05
Data from Dial Gauge
Relevant constants used for calculations:
1.
? = 10.276 π?
2.
?
1
= 5.12 π?
3.
?
2
= 5.74 π?
4.
? = 10
6
ππ π
5.
π΄ = 12.15 π?
2
Table 4: Strain gauge data at location 1 (x = 5.12 in)
Load (lb)
Dial gauge deflection (in)
Theoretical deflection (in)
100
0.17
0.410394
200
0.39
0.820787
250
0.54
1.025984
The Youngs Modulus is calculated using the following formula, where
?
is the slope of the graph.
? = ? β
?
π΄
= 409.05 β
10.276
12.15
= 345.95 ππ π
Table 5: Strain gauge data at location 2 (x = 5.74 in)
Load (lb)
Dial gauge deflection (in)
Theoretical deflection (in)
100
0.56
0.324028
200
0.96
0.648056
250
1.14
0.81007
y = 409.05x + 33.349
RΒ² = 0.9934
0
50
100
150
200
250
300
0
0.1
0.2
0.3
0.4
0.5
0.6
Load (lb)
Deflection (in)
Load vs Deflection
Your preview ends here
Eager to read complete document? Join bartleby learn and gain access to the full version
- Access to all documents
- Unlimited textbook solutions
- 24/7 expert homework help
? = ? β
?
π΄
= 257.19 β
10.276
12.15
= 217.52 ππ π
Error Analysis
The hypothesis that the deflection increased as we moved away from the fixed end towards the applied
point force was proven by the fact that the deflection increased progressively. Some sources of error
include:
1.
Zero error from the strain gauges
2.
High random error/sensitivity of the strain gauges
3.
System not properly insulated from outside disturbances.
The effects of the said sources of error were minimized by performing three trials for each
measurement. It is important to mention that the huge discrepancy in the theoretical and calculated
Youngs Modulus value can be explained by a calculation error.
Lab Report Questions
Describe the stresses distribution on a cross section of a beam which is subjected to
bending moment. Both of normal stress and shear stress.
When a beam experiences a bending moment, stress distribution across its cross-section includes
normal stress (tension and compression) and shear stress. Normal stress is linear, reaching its maximum
on the outermost fibers of the convex and concave sides, while shear stress is parabolic, peaking at the
neutral axis with zero values at the top and bottom surfaces.
Draw the shear force and bending moment diagrams for cantilever and 3-point bending
configuration (Assume you apply load F at the free end of cantilever beam and at the
center of a 3-point bending beam. Both of the beams have length L).
Answered in previous section.
y = 257.19x - 44.705
RΒ² = 0.9994
0
50
100
150
200
250
300
0
0.2
0.4
0.6
0.8
1
1.2
Load (lb)
Deflection (in)
Load vs Deflection
Plot Deflection Vs Force. From the slope evaluate the Youngβs Modulus. Compare the
value of Youngβs modulus with published value.
Answered in previous section.
A load of 100 lbf is applied to the center of a rectangular beam made of Aluminum that is
ΒΎ inch wide and 1 ΒΌ inch tall (Fig.3). What will the stress and deflection be at the center
of the beam?
Assuming that the beam is fixed on both ends and the force is applied on the center, we begin by
defining constants:
π = 0.75 π?
β = 1.25 π?
? = 7.5 π?
? = 10
6
ππ π
Now, we find the equation for the bending moment:
? =
1
2
? (
1
2
?) =
1
4
??
Therefore:
π = β
??
πΌ
=
β
1
4
?? (
1
2
β)
1
12
πβ
3
= 960 ππ π
Now, we find the deflection with the following formula:
πΏ =
??
3
48?πΌ
= 7.2 β 10
β3
?
Give some real life examples where beam bending analysis would be useful.
1.
Building construction: Analyzing beams in structural design to ensure the stability and safety of
buildings.
2.
Bridge engineering: Assessing the behavior of bridge beams under various loads and conditions.
3.
Aerospace industry: Analyzing aircraft wings and fuselage beams to ensure they can withstand
loads during flight.
4.
Automotive design: Evaluating the strength and performance of vehicle chassis and suspension
beams.
5.
Civil infrastructure: Studying the behavior of beams in dams, tunnels, and pipelines for safety
and longevity.
Related Documents
Related Questions
A metallic strain gauge produces an electrical resistance change when subjected to
mechanical strain. However, engineers don't measure this voltage drop directly using
a voltmeter. Why don't we directly measure the voltage drop across the strain gauge,
and instead, use a Wheatstone Bridge?
Damgraph
>
arrow_forward
Hi can you please help me with the attached question?
arrow_forward
For my assigment, I was asked to design a electric motorbike that has a peformance equal to Honda CBR1000 Fireblade which has a petrol engine. A part of the the assignment is to calculate " An estimate of maximum Power your new motor will need to generate to match the Hondaβs performance." I can make the assumption, apart from changing the motor, everything else is going to stay the same so the fairing,the rider and etc they're gonna be the same for the two bikes. So can you please tell me how I can calculate that which information would I need ?
arrow_forward
i. If you know that any strain gauge has a sensitivity towards temperature.In other words, any change in the temperature could also affect theresistance value. How can we get a correct reading from strain gaugesand get rid of the temperature effect?ii. In an AC LVDT system, measuring the output voltage alone gives anindication of the displacement from the center, but not the direction ofdisplacement. Explain why, and also explain a method for solving thisproblem.iii. In a vortex flow meter, there are many methods that could be used tomeasure the effect of vortices and measure the flow rate. Explain howvortices could occur in this flow meter, and explain three methods thatcould be used for measuring the effects of vortices in a vortex flowmeter.iv. Explain in details how can we use a capacitor to indicate the lever ofwater in a tank (use drawings and electrical diagram to elaborate on yourexplanation).Page 5 of 63v. Bimetallic strip could be used as a temperature detector. Explainβ¦
arrow_forward
Big and clear handwriting with all the steps. Make sure calculations and answers are accurate please. THANK YOU
arrow_forward
1
arrow_forward
Please show work for practice problem 12
arrow_forward
A long steel rod is placed horizontally between two supports, one at each end. The rod bends a little in the center. Which property of this rod can be used to estimate how much the rod should bend at the center?
1.
Its Shear Modulus
2.
Its Young's Modulus
3.
All of these Moduli can be used to compute how much it bends.
4.
Its Bulk Modulus.
arrow_forward
Show work
Part 1 website: https://ophysics.com/r5.html
PArt 2 website: https://ophysics.com/r3.html
arrow_forward
Please can you assist me with the attached question. Many thanks.
arrow_forward
Can anyone help me with this question
arrow_forward
Which of these statements are correct?
arrow_forward
Force applied to a circular cantilever beam is estimated from the strain-gage read-out and
measurements of beam dimensions. The readout of the strain-gage sensor is 3.40V. The length and
diameter of beam were measured by a caliper which has a resolution of 0.01 in. Five measurements
were made for both the length (mean=11.96", STD=0.05") and diameter (mean=1.05, STD=0.02"),
respectively. The caliper has a resolution of 0.01 in. The measurements took place at a room
temperature (20 Β°C). (a) What is the sensitivity of the sensor? (b) Find the uncertainty of the
applied force (o = 32FI/3, c=95%) (c) Which measurement contributes the largest
uncertainty?
Voltmeter
Strain-gage
Resolution
0.01V
Input
0-100ksi
Excitation
15VDC
Output
0-5V
Linearity
+4mv/ksi
Hysteresis
+0.4% of FS
Thermal
+0.3mv/Β°C
arrow_forward
these are shot questions please answer the all questions it's important for me
arrow_forward
explain the strain here? include the minimum and the max .
arrow_forward
Pls donβt use ai and fast :)
arrow_forward
The purpose of this problem is to
show the relationship between material constants typically used in engineering practice. This
is useful because you may often have access to measurements of or tabulated values of some
constants (e.g., Young's modulus and Poisson's ratio) but need another constant (e.g., shear
modulus) for a calculation. Use the expression Cijkl = Β΅(dildjk + dikdjl) + AdΒΏjdkl to derive
the following:
(a) Young's modulus, E = Β΅(3X+2Β΅)/(X+ΞΌ), from the definition 11 = Ee11 in a unconfined
(022 = 0,033 = 0) uniaxial tension test.
(b) Poisson's ratio, v = \/(2(X + ΞΌ)), from the definition v = β¬22/11 in the same test as
in (a).
(c) Shear modulus, ΞΌ = G = 012/(2β¬12) = E/(2(1 + v)).
Use the results to show that C can also be written Cijkl
Ev/((1+v)(1 β 2v))dijΒ§kl.
=
E/(2(1 + v))(duΓ°jk + dikdjl) +
arrow_forward
SEE MORE QUESTIONS
Recommended textbooks for you
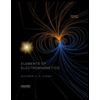
Elements Of Electromagnetics
Mechanical Engineering
ISBN:9780190698614
Author:Sadiku, Matthew N. O.
Publisher:Oxford University Press
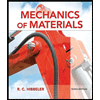
Mechanics of Materials (10th Edition)
Mechanical Engineering
ISBN:9780134319650
Author:Russell C. Hibbeler
Publisher:PEARSON
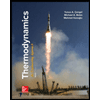
Thermodynamics: An Engineering Approach
Mechanical Engineering
ISBN:9781259822674
Author:Yunus A. Cengel Dr., Michael A. Boles
Publisher:McGraw-Hill Education
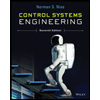
Control Systems Engineering
Mechanical Engineering
ISBN:9781118170519
Author:Norman S. Nise
Publisher:WILEY
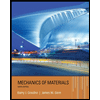
Mechanics of Materials (MindTap Course List)
Mechanical Engineering
ISBN:9781337093347
Author:Barry J. Goodno, James M. Gere
Publisher:Cengage Learning
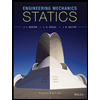
Engineering Mechanics: Statics
Mechanical Engineering
ISBN:9781118807330
Author:James L. Meriam, L. G. Kraige, J. N. Bolton
Publisher:WILEY
Related Questions
- A metallic strain gauge produces an electrical resistance change when subjected to mechanical strain. However, engineers don't measure this voltage drop directly using a voltmeter. Why don't we directly measure the voltage drop across the strain gauge, and instead, use a Wheatstone Bridge? Damgraph >arrow_forwardHi can you please help me with the attached question?arrow_forwardFor my assigment, I was asked to design a electric motorbike that has a peformance equal to Honda CBR1000 Fireblade which has a petrol engine. A part of the the assignment is to calculate " An estimate of maximum Power your new motor will need to generate to match the Hondaβs performance." I can make the assumption, apart from changing the motor, everything else is going to stay the same so the fairing,the rider and etc they're gonna be the same for the two bikes. So can you please tell me how I can calculate that which information would I need ?arrow_forward
- i. If you know that any strain gauge has a sensitivity towards temperature.In other words, any change in the temperature could also affect theresistance value. How can we get a correct reading from strain gaugesand get rid of the temperature effect?ii. In an AC LVDT system, measuring the output voltage alone gives anindication of the displacement from the center, but not the direction ofdisplacement. Explain why, and also explain a method for solving thisproblem.iii. In a vortex flow meter, there are many methods that could be used tomeasure the effect of vortices and measure the flow rate. Explain howvortices could occur in this flow meter, and explain three methods thatcould be used for measuring the effects of vortices in a vortex flowmeter.iv. Explain in details how can we use a capacitor to indicate the lever ofwater in a tank (use drawings and electrical diagram to elaborate on yourexplanation).Page 5 of 63v. Bimetallic strip could be used as a temperature detector. Explainβ¦arrow_forwardBig and clear handwriting with all the steps. Make sure calculations and answers are accurate please. THANK YOUarrow_forward1arrow_forward
- Please show work for practice problem 12arrow_forwardA long steel rod is placed horizontally between two supports, one at each end. The rod bends a little in the center. Which property of this rod can be used to estimate how much the rod should bend at the center? 1. Its Shear Modulus 2. Its Young's Modulus 3. All of these Moduli can be used to compute how much it bends. 4. Its Bulk Modulus.arrow_forwardShow work Part 1 website: https://ophysics.com/r5.html PArt 2 website: https://ophysics.com/r3.htmlarrow_forward
arrow_back_ios
SEE MORE QUESTIONS
arrow_forward_ios
Recommended textbooks for you
- Elements Of ElectromagneticsMechanical EngineeringISBN:9780190698614Author:Sadiku, Matthew N. O.Publisher:Oxford University PressMechanics of Materials (10th Edition)Mechanical EngineeringISBN:9780134319650Author:Russell C. HibbelerPublisher:PEARSONThermodynamics: An Engineering ApproachMechanical EngineeringISBN:9781259822674Author:Yunus A. Cengel Dr., Michael A. BolesPublisher:McGraw-Hill Education
- Control Systems EngineeringMechanical EngineeringISBN:9781118170519Author:Norman S. NisePublisher:WILEYMechanics of Materials (MindTap Course List)Mechanical EngineeringISBN:9781337093347Author:Barry J. Goodno, James M. GerePublisher:Cengage LearningEngineering Mechanics: StaticsMechanical EngineeringISBN:9781118807330Author:James L. Meriam, L. G. Kraige, J. N. BoltonPublisher:WILEY
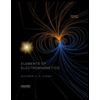
Elements Of Electromagnetics
Mechanical Engineering
ISBN:9780190698614
Author:Sadiku, Matthew N. O.
Publisher:Oxford University Press
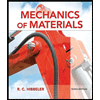
Mechanics of Materials (10th Edition)
Mechanical Engineering
ISBN:9780134319650
Author:Russell C. Hibbeler
Publisher:PEARSON
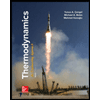
Thermodynamics: An Engineering Approach
Mechanical Engineering
ISBN:9781259822674
Author:Yunus A. Cengel Dr., Michael A. Boles
Publisher:McGraw-Hill Education
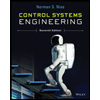
Control Systems Engineering
Mechanical Engineering
ISBN:9781118170519
Author:Norman S. Nise
Publisher:WILEY
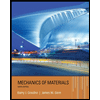
Mechanics of Materials (MindTap Course List)
Mechanical Engineering
ISBN:9781337093347
Author:Barry J. Goodno, James M. Gere
Publisher:Cengage Learning
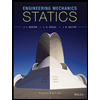
Engineering Mechanics: Statics
Mechanical Engineering
ISBN:9781118807330
Author:James L. Meriam, L. G. Kraige, J. N. Bolton
Publisher:WILEY