Delaware Chemicals is considering the installation of a computer process con- trol system in one of its processing plants. This plant is used about 40% of the time, or 3,500 operating hours per year, to produce a proprietary demulsifica- tion chemical; during the remaining 60% of the time, it is used to produce other specialty chemicals. The annual production of the demulsification chemical amounts to 30,000 kilograms per year, and it sells for $15 per kilogram. The proposed computer process control system will cost $65,000 and is expected to provide specific benefits in the production of the demulsification chemical as follows: 9 First, the selling price of the product could be increased by $2 per kilogram because the product would be of higher purity, which translates into better demulsification performance. E Second, production volumes would increase by 4,000 kilograms per year as a result of higher reaction yields, without any increase in requirements for raw material quantities or production time. E Finally, the number of process operators could be reduced by one per shift, which represents a savings of $25 per hour. The new control system would result in additional maintenance costs of $53,000 per year and has an expected useful life of eight years. While the system is likely to provide similar benefits in the production of the other specialty chemicals manufactured in the process plant, these have not been quantificd as yet. (a) Identify the cash inflows over the life of the project. (b) Identify the cash outflows over the life of the project. (c) Determine the net cash flows over the life of the project.
Delaware Chemicals is considering the installation of a computer process con- trol system in one of its processing plants. This plant is used about 40% of the time, or 3,500 operating hours per year, to produce a proprietary demulsifica- tion chemical; during the remaining 60% of the time, it is used to produce other specialty chemicals. The annual production of the demulsification chemical amounts to 30,000 kilograms per year, and it sells for $15 per kilogram. The proposed computer process control system will cost $65,000 and is expected to provide specific benefits in the production of the demulsification chemical as follows: 9 First, the selling price of the product could be increased by $2 per kilogram because the product would be of higher purity, which translates into better demulsification performance. E Second, production volumes would increase by 4,000 kilograms per year as a result of higher reaction yields, without any increase in requirements for raw material quantities or production time. E Finally, the number of process operators could be reduced by one per shift, which represents a savings of $25 per hour. The new control system would result in additional maintenance costs of $53,000 per year and has an expected useful life of eight years. While the system is likely to provide similar benefits in the production of the other specialty chemicals manufactured in the process plant, these have not been quantificd as yet. (a) Identify the cash inflows over the life of the project. (b) Identify the cash outflows over the life of the project. (c) Determine the net cash flows over the life of the project.
Managerial Accounting
15th Edition
ISBN:9781337912020
Author:Carl Warren, Ph.d. Cma William B. Tayler
Publisher:Carl Warren, Ph.d. Cma William B. Tayler
Chapter11: Differential Analysis And Product Pricing
Section: Chapter Questions
Problem 3CMA: Aril Industries is a multiproduct company that currently manufactures 30,000 units of Part 730 each...
Related questions
Question
Refer to the problem given in answering the following questions:
(a) How long does it take to recover the investment?
(b) If the firm's interest rate is 15%, what would be the discounted-payback
period for this project?
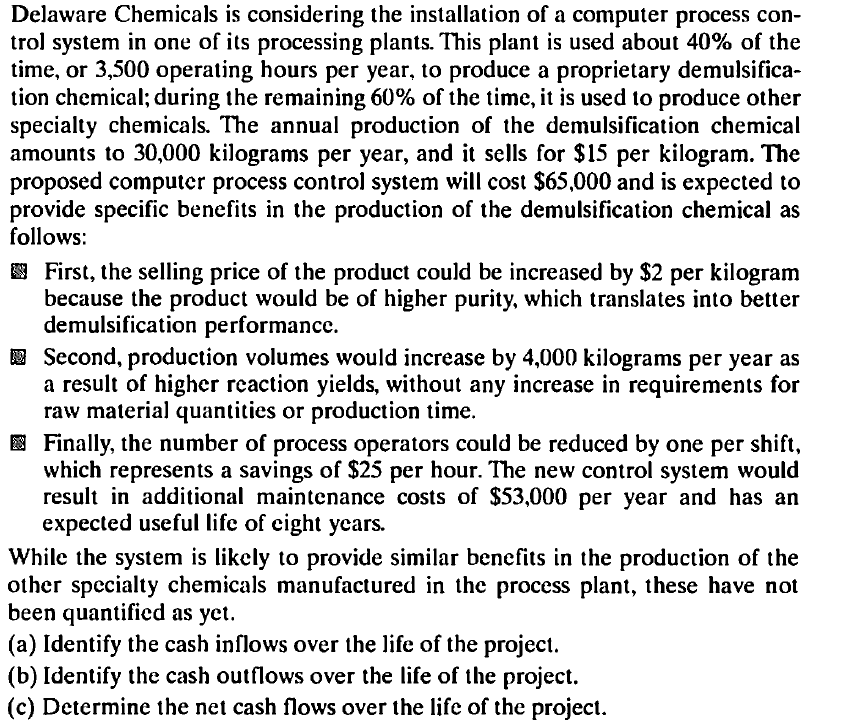
Transcribed Image Text:Delaware Chemicals is considering the installation of a computer process con-
trol system in one of its processing plants. This plant is used about 40% of the
time, or 3,500 operating hours per year, to produce a proprietary demulsifica-
tion chemical; during the remaining 60% of the time, it is used to produce other
specialty chemicals. The annual production of the demulsification chemical
amounts to 30,000 kilograms per year, and it sells for $15 per kilogram. The
proposed computer process control system will cost $65,000 and is expected to
provide specific benefits in the production of the demulsification chemical as
follows:
9 First, the selling price of the product could be increased by $2 per kilogram
because the product would be of higher purity, which translates into better
demulsification performance.
E Second, production volumes would increase by 4,000 kilograms per year as
a result of higher reaction yields, without any increase in requirements for
raw material quantities or production time.
E Finally, the number of process operators could be reduced by one per shift,
which represents a savings of $25 per hour. The new control system would
result in additional maintenance costs of $53,000 per year and has an
expected useful life of eight years.
While the system is likely to provide similar benefits in the production of the
other specialty chemicals manufactured in the process plant, these have not
been quantificd as yet.
(a) Identify the cash inflows over the life of the project.
(b) Identify the cash outflows over the life of the project.
(c) Determine the net cash flows over the life of the project.
Expert Solution

This question has been solved!
Explore an expertly crafted, step-by-step solution for a thorough understanding of key concepts.
This is a popular solution!
Trending now
This is a popular solution!
Step by step
Solved in 3 steps with 4 images

Knowledge Booster
Learn more about
Need a deep-dive on the concept behind this application? Look no further. Learn more about this topic, accounting and related others by exploring similar questions and additional content below.Recommended textbooks for you
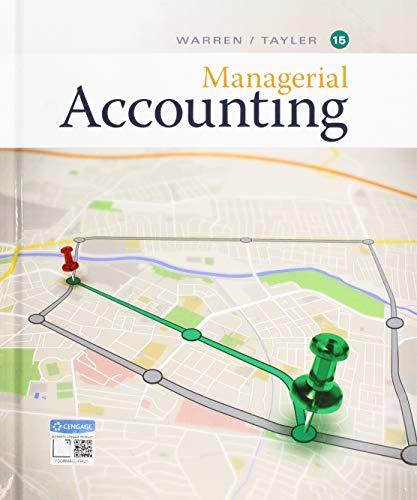
Managerial Accounting
Accounting
ISBN:
9781337912020
Author:
Carl Warren, Ph.d. Cma William B. Tayler
Publisher:
South-Western College Pub
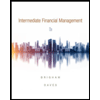
Intermediate Financial Management (MindTap Course…
Finance
ISBN:
9781337395083
Author:
Eugene F. Brigham, Phillip R. Daves
Publisher:
Cengage Learning
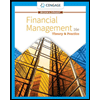
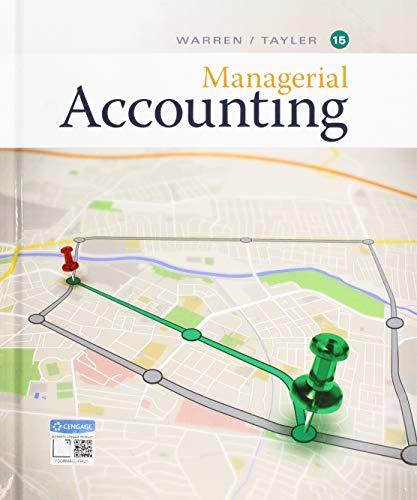
Managerial Accounting
Accounting
ISBN:
9781337912020
Author:
Carl Warren, Ph.d. Cma William B. Tayler
Publisher:
South-Western College Pub
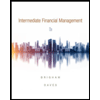
Intermediate Financial Management (MindTap Course…
Finance
ISBN:
9781337395083
Author:
Eugene F. Brigham, Phillip R. Daves
Publisher:
Cengage Learning
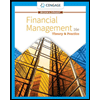
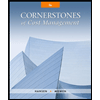
Cornerstones of Cost Management (Cornerstones Ser…
Accounting
ISBN:
9781305970663
Author:
Don R. Hansen, Maryanne M. Mowen
Publisher:
Cengage Learning
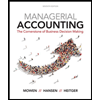
Managerial Accounting: The Cornerstone of Busines…
Accounting
ISBN:
9781337115773
Author:
Maryanne M. Mowen, Don R. Hansen, Dan L. Heitger
Publisher:
Cengage Learning