Make-or-Buy, Traditional and ABC Analysis Brees, Inc., a manufacturer of golf carts, has just received an offer from a supplier to provide 2,600 units of a component used in its main product. The component is a track assembly that is currently produced internally. The supplier has offered to sell the track assembly for $70 per unit. Brees is currently using a traditional, unit-based costing system that assigns overhead to jobs on the basis of direct labor hours. The estimated traditional full cost of producing the track assembly is as follows: Direct materials $45.00 Direct labor 16.00 Variable overhead 4.00 Fixed overhead 40.00 Prior to making a decision, the company’s CEO commissioned a special study to see whether there would be any decrease in the fixed overhead costs. The results of the study revealed the following: 3 setups—$1,180 each (The setups would be avoided, and total spending could be reduced by $1,180 per setup.) One half-time inspector is needed. The company already uses part-time inspectors hired through a temporary employment agency. The yearly cost of the part-time inspectors for the track assembly operation is $12,290 and could be totally avoided if the part were purchased. Engineering work: 450 hours, $45/hour. (Although the work decreases by 450 hours, the engineer assigned to the track assembly line also spends time on other products, and there would be no reduction in his salary.) 75 fewer material moves at $30 per move. Required: 1. Ignore the special study, and determine whether the track assembly should be produced internally or purchased from the supplier. 2. Now, using the special study data, repeat the analysis. It is $fill in the blank 2 expensive to buy outside. 3. Which of the listed items is not a qualitative factor that would affect the decision? 4. After reviewing the special study, the controller made the following remark: "This study ignores the additional activity demands that purchasing would cause. For example, although the demand for inspecting the part on the production floor decreases, we may need to inspect the incoming parts in the receiving area. Will we actually save any inspection costs?" Is the controller right?
Process Costing
Process costing is a sort of operation costing which is employed to determine the value of a product at each process or stage of producing process, applicable where goods produced from a series of continuous operations or procedure.
Job Costing
Job costing is adhesive costs of each and every job involved in the production processes. It is an accounting measure. It is a method which determines the cost of specific jobs, which are performed according to the consumer’s specifications. Job costing is possible only in businesses where the production is done as per the customer’s requirement. For example, some customers order to manufacture furniture as per their needs.
ABC Costing
Cost Accounting is a form of managerial accounting that helps the company in assessing the total variable cost so as to compute the cost of production. Cost accounting is generally used by the management so as to ensure better decision-making. In comparison to financial accounting, cost accounting has to follow a set standard ad can be used flexibly by the management as per their needs. The types of Cost Accounting include – Lean Accounting, Standard Costing, Marginal Costing and Activity Based Costing.
6. Make-or-Buy, Traditional and ABC Analysis
Brees, Inc., a manufacturer of golf carts, has just received an offer from a supplier to provide 2,600 units of a component used in its main product. The component is a track assembly that is currently produced internally. The supplier has offered to sell the track assembly for $70 per unit. Brees is currently using a traditional, unit-based costing system that assigns overhead to jobs on the basis of direct labor hours. The estimated traditional full cost of producing the track assembly is as follows:
Direct materials | $45.00 |
Direct labor | 16.00 |
Variable overhead | 4.00 |
Fixed overhead | 40.00 |
Prior to making a decision, the company’s CEO commissioned a special study to see whether there would be any decrease in the fixed overhead costs. The results of the study revealed the following:
3 setups—$1,180 each (The setups would be avoided, and total spending could be reduced by $1,180 per setup.)
One half-time inspector is needed. The company already uses part-time inspectors hired through a temporary employment agency. The yearly cost of the part-time inspectors for the track assembly operation is $12,290 and could be totally avoided if the part were purchased.
Engineering work: 450 hours, $45/hour. (Although the work decreases by 450 hours, the engineer assigned to the track assembly line also spends time on other products, and there would be no reduction in his salary.)
75 fewer material moves at $30 per move.
Required:
1. Ignore the special study, and determine whether the track assembly should be produced internally or purchased from the supplier.
2. Now, using the special study data, repeat the analysis.
It is $fill in the blank 2
expensive to buy outside.
3. Which of the listed items is not a qualitative factor that would affect the decision?
4. After reviewing the special study, the controller made the following remark: "This study ignores the additional activity demands that purchasing would cause. For example, although the demand for inspecting the part on the production floor decreases, we may need to inspect the incoming parts in the receiving area. Will we actually save any inspection costs?" Is the controller right?

Trending now
This is a popular solution!
Step by step
Solved in 4 steps

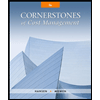
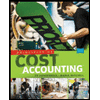
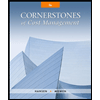
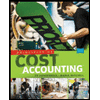
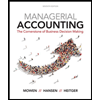
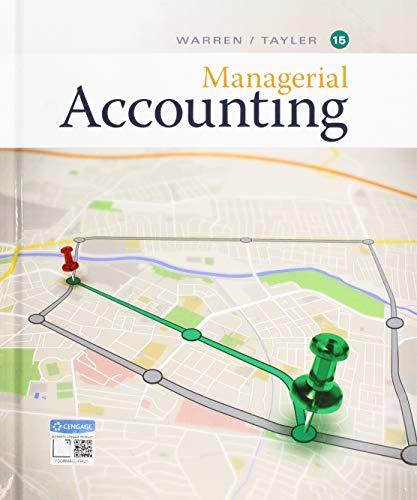
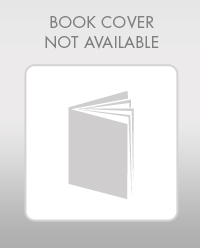