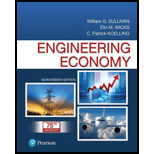
Engineering Economy (17th Edition)
17th Edition
ISBN: 9780134870069
Author: William G. Sullivan, Elin M. Wicks, C. Patrick Koelling
Publisher: PEARSON
expand_more
expand_more
format_list_bulleted
Question
Chapter 11, Problem 42FE
To determine
Calculate the minimum value of X.
Expert Solution & Answer

Want to see the full answer?
Check out a sample textbook solution
Students have asked these similar questions
A manufacturing engineer is considering whether to repair or replace a broken machine. The first alternative (Alternative “A”) is to repair the machine with an initial cost of $15,000, an annual maintenance of $700 per year, with no salvage value at the end of its five-year useful life. The second alternative (Alternative “B”) is to replace the machine for $30,000. The maintenance cost starts in the second year at $200 and increases $200 per year in all subsequent years. There is an anticipated salvage value of $5,000 at the end of 20 years. Assuming interest rate is 6% and an analysis period of 20 years, what would be the preferable alternative ?
. A construction company is considering two possibilities for warehouse operations. Proposal 1 would require the purchase of a forklift for $5,000 and 500 pallets that cost $5 each. The average life of a pallet is assumed to be 2 years. If the forklift is purchased, the company must hire an operator for $9,000 annually and spend $600 per year on maintenance and operation. The life of the forklift is expected to be 12 years with a $700 salvage value. Alternatively, proposal 2 requires that the company hire 2 men to operate power driven hand trucks at a cost of $7,500 per man. One hand truck will be required at a cost of $900. The hand truck will have a life of 6 years with no salvage value. If the company's minimum attractive rate of return is 12%, which alternative should be selected? Use the annual equivalent method.
A piece of new equipment has been proposed by engineers to increase the productivity of a certain manual welding operation. The investment cost is $25,000, and the equipment will have a market value of $5,000 at the end of a study period of five years. Increased productivity attributable to the equipment will amount to $8,000 per year after extra operating costs have been subtracted from the revenue generated by the additional production. If the firm’s MARR is 20% per year, is this proposal a sound one? Use the PW method.
Chapter 11 Solutions
Engineering Economy (17th Edition)
Ch. 11 - Prob. 1PCh. 11 - Refer to Example 11-2. Assuming gasoline costs...Ch. 11 - Prob. 3PCh. 11 - Prob. 4PCh. 11 - Prob. 5PCh. 11 - Prob. 6PCh. 11 - Prob. 7PCh. 11 - Prob. 8PCh. 11 - Prob. 9PCh. 11 - Prob. 10P
Ch. 11 - Prob. 11PCh. 11 - Prob. 12PCh. 11 - Prob. 13PCh. 11 - Prob. 14PCh. 11 - Prob. 15PCh. 11 - Prob. 16PCh. 11 - Prob. 17PCh. 11 - Prob. 18PCh. 11 - Prob. 19PCh. 11 - A bridge is to be constructed now as part of a new...Ch. 11 - An aerodynamic three-wheeled automobile (the Dart)...Ch. 11 - Prob. 23PCh. 11 - Prob. 24SECh. 11 - Prob. 25SECh. 11 - Prob. 26SECh. 11 - Prob. 27SECh. 11 - Prob. 28SECh. 11 - Prob. 29SECh. 11 - Prob. 30FECh. 11 - Prob. 31FECh. 11 - A supermarket chain buys loaves of bread from its...Ch. 11 - A supermarket chain buys loaves of bread from its...Ch. 11 - Prob. 34FECh. 11 - Prob. 35FECh. 11 - Prob. 36FECh. 11 - Prob. 37FECh. 11 - Prob. 38FECh. 11 - Prob. 39FECh. 11 - Prob. 40FECh. 11 - Prob. 41FECh. 11 - Prob. 42FE
Knowledge Booster
Similar questions
- A recent graduate who wants to start an excavation/ earth-moving business is trying to determine which size of used dump truck to buy. He knows that as the bed size increases, the net income increases, but he is uncertain whether the incremental expenditure required for the larger trucks is justified. The cash flows associated with each size truck are estimated below. The contractor has established a MARR of 18% per year, and all trucks are expected to have a remaining economic life of 5 years. (a) Determine which size truck he should purchase. (b) If two trucks are to be purchased, what should be the size of the second truck? (Note: Problem 8.44 requests a spreadsheet solution of these alternatives.) Truck Bed Size, m3 Initial Investment, $ M&O, $/Year Salvage Value, $ Annual Revenue, $/Year 8 −30,000 −14,000 +2,000 +26,500 10 −34,000 −15,500 +2,500 +30,000 15 −38,000 −18,000 +3,000 +33,500 20 −48,000 −21,000 +3,500 +40,500 25 −57,000 −26,000 +4,600 +49,000arrow_forwardThe owner of a downtown parking lot has employed a civil engineering consultingfirm to advise her on the economic feasibility of constructing an office building onthe site. The project engineer has assembled the following data: The analysis period is to be 15 years. At the end of that time the salvage value is expected to be equal to the initial investment.MARR is 10%. What should the engineer recommend?arrow_forwardThree mutually exclusive alternatives are being considered for the production equipment at a tissue paper factory. The estimated cash flows for each alternative are given here. (All cash flows are in thousands.)Which equipment alternative, if any, should be selected? The firm’s MARR is 20% per year. Please state your assumptions.arrow_forward
- A bridge design firm is performing an economic analysis of two mutually exclusive designs for a highway overpass. The steel girder option has an initial cost of $2.26 million, and the concrete option has an initial cost of $2.33 million. Every 25 years, the steel bridge must be painted at a cost of $560,000, and all other maintenance costs are the same for both options. The steel bridge is expected to last 50 years, and concrete bridge is expected to last 75 years. Based on the shortest acceptable analysis period, determine the present worth of costs for the best option using an interest rate of 7%. Express your answer in $ to the nearest $10,000.arrow_forwardThere are two alternative machines for a manufacturing process. Both machines have the same output rate, but they differ in costs. Machine A costs $20,000 to set up and $8,000 per year to operate. It must be completely replaced every 3 years, and it has no salvage value. Machine B costs $50,000 to set up and $2,160 per year to operate. It should last for 5 years and has no salvage value. The costs of two machines are shown below. 0 1 2 3 4 5 Machine A 20,000 8,000 8,000 8,000 Machine B 50,000 2,160 2,160 2,160 2,160 2,160 Assuming the cost of capital is 10%,1. find the equivalent annual cost of Machine A in Box 1. Round it to a whole dollar, and no comma or the dollar sign.2. find the EAC of Machine B in Box 2. The same format as box 1.3. Based on the equivalent annual cost method, type in Box 3 which machine do you recommend, Machine A or Machine B. Question 20 options: Blank # 1 Blank # 2 Blank #…arrow_forwardThe Adams Construction Company is bidding on a project to install a large flood drainage culvert from Dandridge to a distant lake. If they bid $2,000,000 for the job, what is the benefit-cost ratio in view of the following data? The MARR is 6% per year, and the project’s life is 30 years.arrow_forward
- The International Parcel Service has installed a new radio frequency identification system to help reduce the number of packages that are incorrectly delivered. The capital investment in the system is $65,000, and the projected annual savings are tabled below. The system’s market value at the EOY five is negligible, and the MARR is 18% per year. Calculate the payback period of the project.arrow_forwardAn automobile leasing company has a contract with a new car dealer to do major repairs for $720 per car. The leasing company estimates that for $400,000, it could buy equipment to service their own cars at a cost of $300 per car. If the equipment will have a salvage value of 10% of its first cost after 15 years, the minimum number of cars that must require major servicing each year to justify the equipment at a MARR of 10% per year is closest to: (a) 88 (b) 122 (c) 128 (d) 143arrow_forwardA potential project is currently under review. An initial investment of $87,000 would be necessary for equipment. The annual revenues and expenses are expected to be $40,000 and $19,000 each year, respectively, over the 6-year project period. The salvage value of the equipment at the end of the project period is projected to be $17,000. Assume a MARR of 9%. Find the AW (directly - do not convert from either FW or PW - to the nearest cent).arrow_forward
- Bawal gumamit ng excel( Don't use Excel) A small company has P20,000 in surplus capital that it wishes to invest in new revenue producing projects. Three independent sets of mutually exclusive projects have been developed. The useful life of each is five years and all market values are zero. You have been asked to perform an IRR analysis to select the best combination of projects. If the MARR is 12% per year, which combination of projects would you recommend?arrow_forwardAre the investment decisions based solely on an estimate of a project's profitability?arrow_forwardDupont is considering licensing a low liquid discharge (LLD) water treatment system from a small company that developed the process and owns the license. Dupont can purchase a 1-year option for $100,000 that will provide time to pilot test the LLD process or Dupont can acquire the license now at a cost of $1.8 million plus 25% of sales paid annually to the license owner. If they wait 1 year, the cost will increase to $1.9 million plus 30% of sales paid annually. If sales are estimated to be $1,000,000 per year over the 5-year license period, should Dupont purchase the license now or purchase the option now and possibly license it after the 1-year test period? Assume the MARR is 15% per year.arrow_forward
arrow_back_ios
SEE MORE QUESTIONS
arrow_forward_ios
Recommended textbooks for you
- Principles of Economics (12th Edition)EconomicsISBN:9780134078779Author:Karl E. Case, Ray C. Fair, Sharon E. OsterPublisher:PEARSONEngineering Economy (17th Edition)EconomicsISBN:9780134870069Author:William G. Sullivan, Elin M. Wicks, C. Patrick KoellingPublisher:PEARSON
- Principles of Economics (MindTap Course List)EconomicsISBN:9781305585126Author:N. Gregory MankiwPublisher:Cengage LearningManagerial Economics: A Problem Solving ApproachEconomicsISBN:9781337106665Author:Luke M. Froeb, Brian T. McCann, Michael R. Ward, Mike ShorPublisher:Cengage LearningManagerial Economics & Business Strategy (Mcgraw-...EconomicsISBN:9781259290619Author:Michael Baye, Jeff PrincePublisher:McGraw-Hill Education
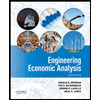
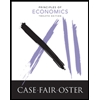
Principles of Economics (12th Edition)
Economics
ISBN:9780134078779
Author:Karl E. Case, Ray C. Fair, Sharon E. Oster
Publisher:PEARSON
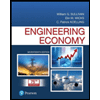
Engineering Economy (17th Edition)
Economics
ISBN:9780134870069
Author:William G. Sullivan, Elin M. Wicks, C. Patrick Koelling
Publisher:PEARSON
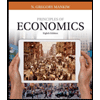
Principles of Economics (MindTap Course List)
Economics
ISBN:9781305585126
Author:N. Gregory Mankiw
Publisher:Cengage Learning
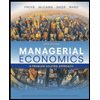
Managerial Economics: A Problem Solving Approach
Economics
ISBN:9781337106665
Author:Luke M. Froeb, Brian T. McCann, Michael R. Ward, Mike Shor
Publisher:Cengage Learning
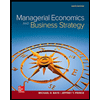
Managerial Economics & Business Strategy (Mcgraw-...
Economics
ISBN:9781259290619
Author:Michael Baye, Jeff Prince
Publisher:McGraw-Hill Education