Concept explainers
eXcel The Chewy Candy Company would like to determine an aggregate production plan for the next six months. The company makes many different types of candy but feels it can plan its total production in pounds provided that the mix of candy sold does not change too drastically. At the present time, the Chewy Company has 70 workers and 9000 pounds of candy in inventory. Each worker can produce 100 pounds of candy a month and is paid S 19 an hour (use 160 hours of regular time per month). Overtime, at a pay rate of 150 percent of regular time, can be used up to a maximum of 20 percent in addition to regular time in any month. It costs so cents to store a pound of candy for a year, $1,200 to hire a worker, and $1,500 to lay off a worker. The
- a. Determine the costs of a level production strategy for the next six months, with an ending inventory of 8000 pounds.
- b. Determine the costs of a chase strategy for the next six months.
- c. Calculate the costs of using the maximum overtime for the two months of highest demand.

Want to see the full answer?
Check out a sample textbook solution
Chapter 11 Solutions
Operations Management In The Supply Chain Decisions And Cases 7th
- evelop a production plan and calculate the annual cost for a firm whose demand forecast is fall, 9,700; winter, 8,000; spring, 7,000; summer, 11,700. Inventory at the beginning of fall is 485 units. At the beginning of fall you currently have 35 workers, but you plan to hire temporary workers at the beginning of summer and lay them off at the end of summer. In addition, you have negotiated with the union an option to use the regular workforce on overtime during winter or spring only if overtime is necessary to prevent stockouts at the end of those quarters. Overtime is not available during the fall. Relevant costs are hiring, $80 for each temp; layoff, $160 for each worker laid off; inventory holding, $5 per unit-quarter; backorder, $10 per unit; straight time, $5 per hour; overtime, $8 per hour. Assume that the productivity is 0.5 unit per worker hour, with eight hours per day and 60 days per season. In each quarter, produce to the full output of your regular workforce, even if that…arrow_forwardThe president of Hill Enterprises, Terri Hill, projects the firm's aggregate demand requirements over the next 8 months as follows: January 1,400 May 2,200 February 1,600 June 2,200 March 1,800 July 1,800 April 1,800 August 1,400 Her operations manager is considering a new plan, which begins in January with 200 units of inventory on hand. Stockout cost of lost sales is $100 per unit. Inventory holding cost is $20 per unit per month. Ignore any idle-time costs. The plan is called plan C. Plan C: Keep a stable workforce by maintaining a constant production rate equal to the average gross requirements excluding initial inventory and allow varying inventory levels. Conduct your analysis for January through August. Part 2 The average monthly demand requirement=17751775 units. (Enter your response as a whole number.) Part 3 In order to arrive at the costs, first compute the ending inventory and stockout units for each month…arrow_forwardThe president of Hill Enterprises, Terri Hill, projects the firm's aggregate demand requirements over the next 8 months as follows: January 1,400 May 2,200 February 1,600 June 2,200 March 1,800 July 1,800 April 1,800 August 1,400 Her operations manager is considering a new plan, which begins in January with 200 units of inventory on hand. Stockout cost of lost sales is $100 per unit. Inventory holding cost is $20 per unit per month. Ignore any idle-time costs. The plan is called plan C. Plan C: Keep a stable workforce by maintaining a constant production rate equal to the average gross requirements excluding initial inventory and allow varying inventory levels. Conduct your analysis for January through August. Part 2 The average monthly demand requirement=1775 units. (Enter your response as a whole number.) Part 3 In order to arrive at the costs, first compute the ending inventory and stockout units for each month by…arrow_forward
- The president of Hill Enterprises, Terri Hill, projects the firm's aggregate demand requirements over the next 8 months as follows: January 1,400 May 2,200 February 1,600 June 2,200 March 1,800 July 1,800 April 1,800 August 1,400 Her operations manager is considering a new plan, which begins in January with 200 units of inventory on hand. Stockout cost of lost sales is $100 per unit. Inventory holding cost is $20 per unit per month. Ignore any idle-time costs. The plan is called plan C. Plan C: Keep a stable workforce by maintaining a constant production rate equal to the average gross requirements excluding initial inventory and allow varying inventory levels. Conduct your analysis for January through August. Part 2 The average monthly demand requirement=1775 units. (Enter your response as a whole number.) Part 3 In order to arrive at the costs, first compute the ending inventory and stockout units for each month by…arrow_forwardThe planner at a company that makes garden tractors is about to prepare an aggregate production plan that will cover the next 6 months. She has collected the following information: Month Demand Forecast Above the available capacity through permanent workforce 1 1,000 2 1,000 3 2,000 4 3,000 5 4,000 6 1,000 Total: 12,000 Production per month = 20 units per worker Initial inventory = 500 units Desired ending inventory (at the end of month 6) = 0 units Cost: Hire cost = $500 per temporary worker Inventory = $10 per tractor per month Backorder = $150 per tractor per month The optimum aggregate plan is: Month 1 2 3 4 5 6 Total Forecast Demand above regular capacity 1,000 1,000 2,000 3,000 4,000 1,000 12,000 # of temporary workers required 50 50 100 150 200 50 Temp. Workers hired 25 25 50 75 0 0 Temp. workers laid off 0…arrow_forwardPlanners for a company that makes several models of skateboards are about to prepare the aggregate plan that will cover six periods. They have assembled the following information. Period 1 2 3 4 5 6 Total Forecast 200 200 300 400 500 200 1,800 Costs Output Regular time=$2 per skateboard Overtime =$3 per skateboard Subcontract =$6 per skateboard Inventory =$1 per skateboard per period on average inventory Back orders =$5 per skateboard per period They now want to evaluate a plan that calls for a steady rate of regular-time output, mainly using inventory to absorb the uneven demand but allowing some backlog. Prepare an aggregate plan and determine its cost using the preceding information.arrow_forward
- The president of Hill Enterprises, Terri Hill, projects the firm's aggregate demand requirements over the next 8 months as follows: January 1,400 May 2,100 February 1,700 June 2,100 March 1,600 July 1,700 April 1,900 August 1,500 Her operations manager is considering a new plan, which begins in January with 200 units of inventory on hand. Stockout cost of lost sales is $60 per unit. Inventory holding cost is $20 per unit per month. Ignore any idle-time costs. Evaluate the following plans D and E. Plan D: Keep the current workforce stable at producing 1,600 units per month. In addition to the regular production, another 20% of the normal production units can be produced in overtime at an additional cost of $50 per unit. A warehouse now constrains the maximum allowable inventory on hand to 600 units or less. Note: Do not produce in overtime if production or inventory are adequate to cover demand.…arrow_forwardThe president of Hill Enterprises, Terri Hill, projects the firm's aggregate demand requirements over the next 8 months as follows: January 1,500 May 2,300 February 1,700 June 2,100 March 1,700 July 1,900 April 1,700 August 1,500 Her operations manager is considering a new plan, which begins in January with 200 units of inventory on hand. Stockout cost of lost sales is $125 per unit. Inventory holding cost is $20 per unit per month. Ignore any idle-time costs. The plan is called plan C. Plan C: Keep a stable workforce by maintaining a constant production rate equal to the average gross requirements excluding initial inventory and allow varying inventory levels. Conduct your analysis for January through August. The average monthly demand requirement=18001800 units. (Enter your response as a whole number.) In order to arrive at the costs, first compute the ending inventory and stockout units for each month by filling in…arrow_forwardAt Taste of Thyme coffee shop a dirty chai latte creates a profit point of $2.85 for a small and $3.80 for a large. In a month, 200 small lattes were sold and 285 large lattes. As a fast growing demand item with fall approaching, the demand is estimated at 400 and 420 per month. The amount of machine time needed to produce the lattes is 5 minutes and 7 minutes each or for a month, 16.67 hours a month for a small and 33.25 hours a month for a large. What is the maximization function for profit? A. Profit = 400x1 + 420x2 B. Profit = 2.85x1 + 3.80x2 C. Profit = 16.67x1 + 33.25x2 D. Profit = 2.50x1 + 3.50x2arrow_forward
- Formulate a chase sales and operations plan for a company with the following predicted demand: Month 1 2 3 4 5 6 Total Demand 55,200 49,600 12,800 24,800 50,400 25,600 218,400 The beginning workforce is 160 employees. The monthly output per employee is 400 units. The cost to hire and lay off a worker are $2,500 and $3,500, respectively. The cost to carry an item in inventory for one month is estimated at $14, and the stockout cost is $25 per unit. Show the production schedule, the inventory levels, and the changes in the workforce…arrow_forward. Botany weaving was established in 1934 in Dublin Ireland and it is now an approvedsupplier of fabrics for both Boeing and Airbus. They operate 3 plants in Europe to supplytheir 2 major airline customers and these plants are located in Ireland, UK and Italy. Theyhave to decide where to manufacture the two newest high-tech fabrics: Nano Seat Fabricsand Ultra Curtains. Each plant has a different variable cost structure and capacity formanufacturing the different products. Also, each product has an expected demand. CostPlan Plant Capacity Nano Seat Fabrics Ultra curtains Ireland 6000 31€ 28.5€UK 5300 32.5€ 30.5€Italy 5000 35€ 29.5€Demand…arrow_forward3) Gang Aft Agley, a manufacturing company, faces the aggregate planning problem shown in the table below. Cost of regular production is $5 per unit, the cost of producing the same unit on overtime is $7, the cost of subcontracting is $8 per unit, and the cost of carrying a unit in inventory from one month to the next is $2. January February March April May Forecast 500 750 1200 650 300 Beginning Inventory 100 Regular Time Overtime Subcontracting Ending Inventory The labor contract at the plant prohibits both overtime and subcontracting output to exceed 300 units in any five month window. The plant capacity is 500 units per month produced using two shifts, regardless of the number of days in a month. By policy, management wants to avoid stockouts. Formulate the aggregate plan using linear programming and solve it using Solver.arrow_forward
- Practical Management ScienceOperations ManagementISBN:9781337406659Author:WINSTON, Wayne L.Publisher:Cengage,Operations ManagementOperations ManagementISBN:9781259667473Author:William J StevensonPublisher:McGraw-Hill EducationOperations and Supply Chain Management (Mcgraw-hi...Operations ManagementISBN:9781259666100Author:F. Robert Jacobs, Richard B ChasePublisher:McGraw-Hill Education
- Purchasing and Supply Chain ManagementOperations ManagementISBN:9781285869681Author:Robert M. Monczka, Robert B. Handfield, Larry C. Giunipero, James L. PattersonPublisher:Cengage LearningProduction and Operations Analysis, Seventh Editi...Operations ManagementISBN:9781478623069Author:Steven Nahmias, Tava Lennon OlsenPublisher:Waveland Press, Inc.
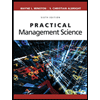
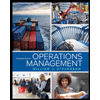
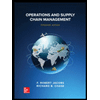
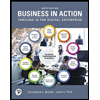
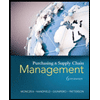
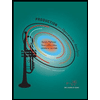