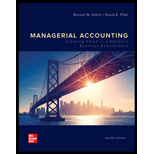
Clearview Window Company manufactures windows for the home-building industry. The window frames are produced in the Frame Division. The frames are then transferred to the Glass Division, where the glass and hardware are installed. The company’s best-selling product is a three-by-four-foot, doublepaned operable window.
The Frame Division also can sell frames directly to custom home builders, who install the glass and hardware. The sales price for a frame is $80. The Glass Division sells its finished windows for $190. The markets for both frames and finished windows exhibit
The standard variable cost of the window is detailed as follows:
*Not including the transfer price for the frame.
Required:
- 1. Assume that there is no excess capacity in the Frame Division.
- a. Use the general rule to compute the transfer price for window frames.
- b. Calculate the transfer price if it is based on standard variable cost with a 10 percent markup.
- 2. Assume that there is excess capacity in the Frame Division.
- a. Use the general rule to compute the transfer price for window frames.
- b. Explain why your answers to requirements (1a) and (2a) differ.
- c. Suppose the predetermined fixed-
overhead rate in the Frame Division is 125 percent of direct-labor cost. Calculate the transfer price if it is based onstandard full cost plus a 10 percent markup.- d. Assume the transfer price established in requirement (2c) is used. The Glass Division has been approached by the U.S. Army with a special order for 1,000 windows at $155. From the perspective of Clearview Window Company as a whole, should the special order be accepted or rejected? Why?
- e. Assume the same facts as in requirement (2d). Will an autonomous Glass Division manager accept or reject the special order? Why?
- f. Comment on any ethical issues you see in the questions raised in requirements (2d) and (2e).
- 3. Comment on the use of full cost as the basis for setting transfer prices.

Want to see the full answer?
Check out a sample textbook solution
Chapter 13 Solutions
Managerial Accounting: Creating Value in a Dynamic Business Environment
- Washington, Inc., makes three models of motorized carts for vacation resorts, X-10, X-20, and X-40. Washington manufactures the carts in two assembly departments: Department A and Department B. All three models are processed initially in Department A, where all material is assembled. The X-10 model is then transferred to finished goods. After processing in Department A, the X-20 and X-40 models are transferred to Department B for final assembly, and then transferred to finished goods.There were no beginning work-in-process inventories on April 1. Data for April are shown in the following table. Ending work in process is 20 percent complete in Department A and 60 percent complete in Department B. Conversion costs are allocated based on the number of equivalent units processed in each department. Total X-10 X-20 X-40 Units started 510 390 270 Units completed in Department A 440 250 180 Units completed in Department B 225…arrow_forwardMuffin Factory (MF) bakes and sells muffins. MF buys materials from suppliers and bakes, frosts, and packages them for resale. Currently the firm offers 2 different types of muffins to gourmet bake shops in boxes, each containing a dozen muffins. The major cost is direct materials; however, a substantial amount of factory overhead is incurred in the baking, frosting, and packing process. MF prices its muffins at full product cost, including allocated overhead, plus a markup of 40%. Data for the current budget include factory overhead of $919,400, which has been allocated by its current costing system on the basis of each product’s direct labor cost. The budgeted direct labor cost for the current year totals $300,000. The budgeted direct costs for a one-dozen box of two of the company’s most popular muffins are as follows: Costs per one dozen Blueberry Cinnamon Activity Cost Driver Budgeted Activity Budgeted Cost Direct materials $…arrow_forwardHedwig Optical makes three models of binoculars: Travel, Sport, and Pro. The models differ by the size of the casing and the quality of the optics. The binoculars are produced in two departments. The Assembly Department purchases components from vendors and assembles them into binoculars. The Travel and Sport models are complete and ready for sale after completing the assembly process. The Pro model undergoes further processing in the Calibration Department, which is actually just a small area in the same building as the Assembly Department. Conversion costs in both the Assembly Department and Calibration Department are based on the number of units produced. There are never any work-in-process inventories. Data for production in January are shown in the following table: Units produced Materials cost Conversion costs Assembly Calibration Total conversion costs Travel Sport Pro Total Cost Per Unit 36,000 $ 1,648,000 $ 440,000 44,400 $ 484,400 Travel Sport 13,500 Pro 4,500 18,000 $…arrow_forward
- O Hedwig Optical makes three models of binoculars: Travel, Sport, and Pro. The models differ by the size of the casing and the quality of the optics. The binoculars are produced in two departments. The Assembly Department purchases components from vendors and assembles them into binoculars. The Travel and Sport models are complete and ready for sale after completing the assembly process. The Pro model undergoes further processing in the Calibration Department, which is actually just a small area in the same building as the Assembly Department. Conversion costs in both the Assembly Department and Calibration Department are based on the number of units produced. There are never any work-in-process inventories. Data for production in January are shown in the following table: Units produced Materials cost Conversion costs Assembly Calibration Total conversion costs Travel Sport Pro Total 35,000 $ 1,645,000 Cost Per Unit $ 440,000 44,400 $ 484,400 Travel 17,500 Sport 13,125 4,375 $ 305,000…arrow_forwardCrane Packaging Company is a leading manufacturer of cardboard boxes and other product packaging solutions. One of the company’s major product lines is custom-printed cake boxes that are sold to some of the country’s best known bakeries at a price of $0.50 per box. To maintain its high-quality image, Crane uses a thick premium coated paper for all of its cake boxes. Based on annual production of 1,000,000 boxes, Crane’s cost for producing a box is as follows: Paper $0.15 Ink 0.05 Direct labor 0.05 Variable overhead 0.09 Fixed overhead 0.09 Total cost per box $0.43 Kimberly Young, a recent graduate of the Culinary Institute of America, is opening a new bakery in her hometown. She recently contacted Brad Lail, Crane’s top salesperson, about purchasing cake boxes for her new store. Brad described Crane’s boxes, emphasizing the high-quality paper and the unique printing process the company uses. Andrea is looking for ways to lower her operating costs, so…arrow_forwardLamothe Kitchen and Bath makes products for the home, which it sells through major retailers and remodeling (do-it-yourself, or DIY) outlets. One product that has had varying success is a ceiling fan for the kitchen. The fan comes in three sizes (36-Inch, 44-Inch, and 54-Inch), which are designed for various kitchen sizes and cooling requirements. The chief financial officer (CFO) at Lamothe has been looking at the segmented income statement for the fan and is concerned about the results for the 36-inch model. Revenues Variable costs Fixed costs allocated to products Operating profit (loss) 36 Inch $ 376,000 233,600 149, 230 $ (6,830) 44 Inch $ 578,600 287,680 227,464 $ 63,456 54 Inch $ 356,400 165,500 140, 806 $ 50,094 If the 36-Inch model is dropped, the revenue associated with it would be lost and the related variable costs saved. In addition, the company's total fixed costs would be reduced by 25 percent. Required: a. Prepare a differential cost schedule to support your…arrow_forward
- Lamothe Kitchen and Bath makes products for the home, which it sells through major retailers and remodeling (do-it-yourself, or DIY) outlets. One product that has had varying success is a ceiling fan for the kitchen. The fan comes in three sizes (36-Inch, 44-Inch, and 54-Inch), which are designed for various kitchen sizes and cooling requirements. The chief financial officer (CFO) at Lamothe has been looking at the segmented income statement for the fan and is concerned about the results for the 36-inch model. Revenues Variable costs Fixed costs allocated to products Operating profit (loss) 36 Inch $ 372,200 231,600 147,230 $ (6,630) If the 36-Inch model is dropped, the revenue associated with it would be lost and the related variable costs saved. In addition, the company's total fixed costs would be reduced by 25 percent. Required A Required B Required: a. Prepare a differential cost schedule to support your recommendation. b. Should Lamothe Kitchen and Bath should drop the 36-Inch…arrow_forwardM4 Engineering has two divisions, the Fabrication Division and the Airplane Division. The Airplane Division may purchase engine mounting clamps from the Fabrication Division or from outside suppliers. The Fabrication Division sells engine mounting clamps both internally and externally. The market price for is $5,000 per 100 mounting clamps. The following conversation took place between the controllers of the Fabrication Division and Airplane Division: • Airplane Division: I hear you are having problems selling mounting clamps out of your division. Maybe I can help. • Fabrication Division: You've got that right. We're producing and selling at about 90% of our capacity to outsiders. Last year we were selling 100% of capacity. Would it be possible for your division to pick up some of our excess capacity? After all, we are part of the same company. • Airplane Division: What kind of price could you give me? • Fabrication Division: Well, you know as well as I that we are under strict profit…arrow_forwardDogarrow_forward
- Shaw is a lumber company that also manufactures custom cabinetry. It is made up of two divisions: Lumber and Cabinetry. The Lumber Division is responsible for harvesting and preparing lumber for use; the Cabinetry Division produces custom-ordered cabinetry. The lumber produced by the Lumber Division has a variable cost of $2.10 per linear foot and full cost of $3.10. Comparable quality wood sells on the open market for $6.30 per linear foot. Required: Assume you are the manager of the Cabinetry Division. Determine the maximum amount you would pay for lumber. Assume you are the manager of the Lumber Division. Determine the minimum amount you would charge for the lumber if you have excess capacity. Repeat assuming you have no excess capacity. Assume you are the president of Shaw. Determine a mutually beneficial transfer price assuming there is excess capacity.arrow_forwardBoney Corporation processes sugar beets that it purchases from farmers. Sugar beets are processed in batches. A batch of sugar beets costs $53 to buy from farmers and $18 to crush in the company's plant. Two intermediate products, beet fiber and beet juice, emerge from the crushing process. The beet fiber can be sold as is for $25 or processed further for $18 to make the end product industrial fiber that is sold for $39. The beet juice can be sold as is for $32 or processed further for $28 to make the end product refined sugar that is sold for $79. What is the financial advantage (disadvantage) for the company from processing the intermediate product beet juice into refined sugar rather than selling it as is?arrow_forwardEyeGuard Equipment Incorporated (EEI) manufactures protective eyewear for use in commercial and home applications. The product is also used by hunters, home woodworking hobbyists, and in other applications. The firm has two main product lines—the highest-quality product is called Safe-T, and a low-cost, value version is called Safe-V. Information on the factory conversion costs for EEI is as follows: Factory Costs Salaries $ 850,000 Supplies 150,000 Factory expense 550,000 Total $ 1,550,000 EEI uses ABC to determine the unit costs of its products. The firm uses resource consumption cost drivers based on rough estimates of the amount that each activity consumes, as shown below. EEI has four activities: job setup, assembly, inspecting and finishing, and packaging. Setup Assembly Inspecting and Finishing Packaging Total Salaries 15% 55% 20% 10% 100% Supplies 20 60 20 100 Factory expense 80 20 100 The activity cost drivers for the two…arrow_forward
- AccountingAccountingISBN:9781337272094Author:WARREN, Carl S., Reeve, James M., Duchac, Jonathan E.Publisher:Cengage Learning,Accounting Information SystemsAccountingISBN:9781337619202Author:Hall, James A.Publisher:Cengage Learning,
- Horngren's Cost Accounting: A Managerial Emphasis...AccountingISBN:9780134475585Author:Srikant M. Datar, Madhav V. RajanPublisher:PEARSONIntermediate AccountingAccountingISBN:9781259722660Author:J. David Spiceland, Mark W. Nelson, Wayne M ThomasPublisher:McGraw-Hill EducationFinancial and Managerial AccountingAccountingISBN:9781259726705Author:John J Wild, Ken W. Shaw, Barbara Chiappetta Fundamental Accounting PrinciplesPublisher:McGraw-Hill Education
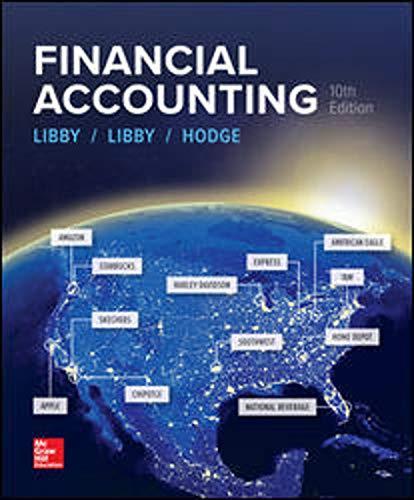
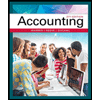
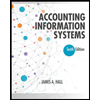
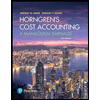
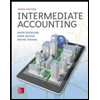
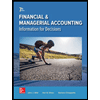