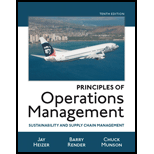
PRIN OF OPS MGMT W/MYOMLAB&ACCESS BADGE
1st Edition
ISBN: 9781323818510
Author: HEIZER
Publisher: PEARSON C
expand_more
expand_more
format_list_bulleted
Concept explainers
Question
Chapter 13, Problem 9DQ
Summary Introduction
To define: Advantages and disadvantages of varying the workforce according to the demand requirement
Introduction: The aggregate plan is the output of sales and operations planning. The major concern of aggregate planning is the production time and quantity for the intermediate future. Aggregate planning would encompass a time prospect of approximately 3 to 18 months.
Expert Solution & Answer

Want to see the full answer?
Check out a sample textbook solution
Students have asked these similar questions
The planner at a company that makes garden tractors is about to prepare an aggregate production plan that will cover the next 6 months. She has collected the following information:
Month
Demand Forecast Above the available capacity through permanent workforce
1
1,000
2
1,000
3
2,000
4
3,000
5
4,000
6
1,000
Total:
12,000
Production per month = 20 units per worker
Initial inventory = 500 units
Desired ending inventory (at the end of month 6) = 0 units
Cost:
Hire cost = $500 per temporary worker
Inventory = $10 per tractor per month
Backorder = $150 per tractor per month
The optimum aggregate plan is:
Month
1
2
3
4
5
6
Total
Forecast Demand above regular capacity
1,000
1,000
2,000
3,000
4,000
1,000
12,000
# of temporary workers required
50
50
100
150
200
50
Temp. Workers hired
25
25
50
75
0
0
Temp. workers laid off
0…
How does aggregate planning in service differ fromaggregate planning in manufacturing?
Table shows the aggregate demand requirements of a manufacturing company. The operations manager is going to use a new plan, which begins in January with 200 units on hand and ends with zero inventory in August. Assume, Inventory holding cost is $20 per unit per month and stockout cost of lost sales is $100 per unit. The plan is called plan A. Compute the cost of plan A.
Plan A: Vary the workforce level to execute a “chase” strategy by producing the quantity demanded in the prior month. The December demand and rate of production are both 1,600 units per month. The cost of hiring additional workers is $5,000 per 100 units. The cost of laying off workers is $7,500 per 100 units. Evaluate this plan.
Chapter 13 Solutions
PRIN OF OPS MGMT W/MYOMLAB&ACCESS BADGE
Ch. 13 - Make the case for, and then against, this pricing...Ch. 13 - Prob. 1DQCh. 13 - Why are SOP teams typically cross-functional?Ch. 13 - Prob. 3DQCh. 13 - Prob. 4DQCh. 13 - Prob. 5DQCh. 13 - Prob. 6DQCh. 13 - Prob. 7DQCh. 13 - Prob. 8DQCh. 13 - Prob. 9DQ
Ch. 13 - Prob. 10DQCh. 13 - Prob. 11DQCh. 13 - Prob. 12DQCh. 13 - Prob. 13DQCh. 13 - Prob. 14DQCh. 13 - Prob. 1PCh. 13 - Prob. 2PCh. 13 - The president of Hill Enterprises, Terri Hill,...Ch. 13 - Prob. 4PCh. 13 - Prob. 5PCh. 13 - Prob. 6PCh. 13 - Consuelo Chua, Inc., is a disk drive manufacturer...Ch. 13 - Prob. 8PCh. 13 - Prob. 9PCh. 13 - Prob. 10PCh. 13 - Prob. 11PCh. 13 - Southeast Soda Pop, Inc., has a new fruit drink...Ch. 13 - Ram Roys firm has developed the following supply,...Ch. 13 - Jerusalem Medical Ltd., an Israeli producer of...Ch. 13 - Prob. 15PCh. 13 - Prob. 16PCh. 13 - Prob. 17PCh. 13 - Prob. 18PCh. 13 - Dwayne Cole, owner of a Florida firm that...Ch. 13 - Prob. 24PCh. 13 - Prob. 25PCh. 13 - Prob. 26PCh. 13 - Evaluate the various configurations of operating...Ch. 13 - Prob. 2CSCh. 13 - After researching revenue (yield) management in...Ch. 13 - The Magic used its original pricing systems of...Ch. 13 - Prob. 3VC
Knowledge Booster
Learn more about
Need a deep-dive on the concept behind this application? Look no further. Learn more about this topic, operations-management and related others by exploring similar questions and additional content below.Similar questions
- . If the opening backlog is 450 units, forecast demand is 700 units, and production is800 units, what will be the ending backlog?arrow_forwardWhat are the options available for the production manager when there is a consistent lack of capacity in a particular work center ?arrow_forwardPlanners for a company that makes several models of skateboards are about toprepare the aggregate plan that will cover six periods. They now want toevaluate a plan that calls for a steady rate of regular output, mainly usinginventory to absorb the uneven demand but allowing some backlog. Overtimeand subcontracting are not used because they want a steady output. They intendto start with zero inventory on hand in the first period. Prepare an aggregate planand determine its cost using the following information. Assume a level of outputrate of 300 units per period with regular time. Note that the planned endinginventory is zero. There are 15 workers, and each can produce 20 units per Period 1 2 3 4 5 6 Total Forecast 200 200 300 400 500 200 1800 Cost Information:Regular time = $2 per skateboardOvertime = $3 per skateboardSubcontract = $6 per skateboardInventory = $1 per skateboard per period on average inventoryBack orders = $5 per skateboard per periodarrow_forward
- The XYZ Company manufactures a seasonal product. At the present time, the company uses a level labor force as a matter of company policy. The company is afraid that if it lays off workers, it will not be able to rehire them or find qualified replacements. Does this company have an aggregate planning problem? Discuss.arrow_forwardHow does demand variability affect the effectiveness of the Wilson approach? Provide examples.arrow_forwardMavis and John have joined forces to start M&J Food Products, a processor of packaged shredded lettuce for institutional use. John has years of food processing experience, and Mavis has extensive commercial food preparation experience. The process will consist of opening crates of lettuce and then sorting, washing, slicing, preserving, and finally packaging the prepared lettuce. Together, with help from vendors, they think they can adequately estimate demand, fixed costs, revenues, and variable cost per 5-pound bag of lettuce. They think a largely manual process will have monthly fixed cost of $50,000and a variable cost of $2.50 per bag. They expect to sell 75,000 bags of lettuce per month. They expect to sell the shredded lettuce for $3.25 per 5-pound bag. John and Mavis has been contacted by a vendor to consider a more mechanized process. This new process will have monthly fixed cost of $125,000 per month with a variable cost of $1.75 per bag. Based on the above scenario: Should…arrow_forward
- When creating an Event, which field reflects the current stage of the negotiating process and controls whether the rooms, space, and items will deduct from inventory?arrow_forwardExplain the different capacity based options used in aggregate planning and their implications for business ?arrow_forwardJAYB, manager of a Fabrication company, has the following aggregate demand requirements and other data for the upcoming four quarters. Table 5: Forecast and cost information [Jadual 5: Maklumat Ramalan dan kos] Quarter [Suku] Demand [Permintaan] Previous quarter's output [Keluaran suku sebelumnya] 1,500 units 1 1,400 Beginning inventory [Inventori awal] 200 units 2 1,000 Hiring workers [Pengambilan pekerja] RM6 per unit 3 1,500 Laying off workers [Pembuangan pekerja] RM11 per unit 4 1,300 Unit cost [Kos unit] RM30 per unit With the information given, JAYB wants you to calculate the total cost of using chase strategy by hiring and layoff workers.arrow_forward
- EZ-Windows, Inc. manufacturers replacement windows for the home remodeling business. In January, the company produces 15,000 windows and ended the month with 9,000 windows in inventory. EZ-Windows' management team would like to develop a production schedule for the next three months. A smooth production schedule is obviously desirable because it maintains the current workforce and provides a similar month-to-month operation. However, given the sales forecasts, the productioncapacities, and the storage capabilities as shown in Table 2, the management team does not think a smooth production schedule with the same production quantity each month possible.The company's cost accounting department estimates that increasing production by one window from one month to the next will increase total costs by $1.00 for each unit increase in the production level. In addition, decreasing production by one unit from one month to the next will increase total costs by $0.65 for each unit decrease in the…arrow_forwardJustify why aggregate planning is different when a business does not produce a tangible good.arrow_forwardPlan production for a four-month period: February through May. For February and March, you should produce to exact demand forecast. For April and May, you should use overtime and inventory with a stable workforce; stable means that the number of workers needed for March will be held constant through May. However, government constraints put a maximum of 5,000 hours of overtime labor per month in April and May (zero overtime in February and March). If demand exceeds supply, then backorders occur. There are 100 workers on January 31. You are given the following demand forecast: February, 90,000; March 65,000; April 110,000; May, 55,000. Productivity is four units per worker hour, eight hours per day, 20 days per month. Assume zero inventory on February 1. Costs are hiring, $50 per new worker; layoff, $70 per worker laid off; inventory holding, $10 per unit-month; straight-time labor, $10 per hour; overtime, $15 per hour; backorder, $20 per unit a. Find the total cost of this plan?arrow_forward
arrow_back_ios
SEE MORE QUESTIONS
arrow_forward_ios
Recommended textbooks for you
- Practical Management ScienceOperations ManagementISBN:9781337406659Author:WINSTON, Wayne L.Publisher:Cengage,Operations ManagementOperations ManagementISBN:9781259667473Author:William J StevensonPublisher:McGraw-Hill EducationOperations and Supply Chain Management (Mcgraw-hi...Operations ManagementISBN:9781259666100Author:F. Robert Jacobs, Richard B ChasePublisher:McGraw-Hill Education
- Purchasing and Supply Chain ManagementOperations ManagementISBN:9781285869681Author:Robert M. Monczka, Robert B. Handfield, Larry C. Giunipero, James L. PattersonPublisher:Cengage LearningProduction and Operations Analysis, Seventh Editi...Operations ManagementISBN:9781478623069Author:Steven Nahmias, Tava Lennon OlsenPublisher:Waveland Press, Inc.
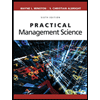
Practical Management Science
Operations Management
ISBN:9781337406659
Author:WINSTON, Wayne L.
Publisher:Cengage,
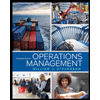
Operations Management
Operations Management
ISBN:9781259667473
Author:William J Stevenson
Publisher:McGraw-Hill Education
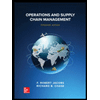
Operations and Supply Chain Management (Mcgraw-hi...
Operations Management
ISBN:9781259666100
Author:F. Robert Jacobs, Richard B Chase
Publisher:McGraw-Hill Education
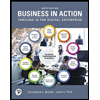
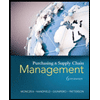
Purchasing and Supply Chain Management
Operations Management
ISBN:9781285869681
Author:Robert M. Monczka, Robert B. Handfield, Larry C. Giunipero, James L. Patterson
Publisher:Cengage Learning
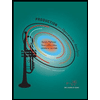
Production and Operations Analysis, Seventh Editi...
Operations Management
ISBN:9781478623069
Author:Steven Nahmias, Tava Lennon Olsen
Publisher:Waveland Press, Inc.