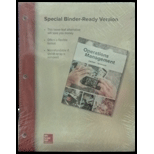
Concept explainers
CASE WARKWORTH FURNITURE1
Warkworth Furniture specializes in environmentally friendly and sustainable furniture. One of its products, the TePaki desk, uses bamboo for the surface and recycled aluminum for the supports. The desk is made in its factory in Vietnam and shipped to all of its 30 stores throughout the United States, primarily in the large urban areas on either coast. Karen Williamson, the owner of Warkworth Furniture, is struggling with how it should organize its supply chain.
Currently, it ships the desks from Vietnam to the United States via ocean carrier. Once they arrive in the United States, they are shipped via a third-party carrier to each store. It usually takes 10 weeks between when an order is placed with the factory and when the product is received in a store.
The TePaki desk may be eco-friendly, but it isn’t wallet friendly: Each desk costs Warkworth $325 to make and it sells the desk for $850. Nevertheless, Warkworth has been able to identify a market segment of customers that value the look of the desk and what it represents. Across its stores, it sells six desks per week, or 0.2 desk per week per store.
Given the upscale nature of its business, Warkworth’s stores are located in nice areas that unfortunately have high rents. Consequently, between the opportunity cost of capital and the cost of physical space, Karen estimates that it costs Warkworth $150 to hold each TePaki desk in one of its stores for one year. It would be a financial disaster if each desk actually spent the entire year in inventory in a store, but the $150 does represent the true cost of holding a desk in a store for that period of time.
Shipping a TePaki desk from Vietnam to a store costs Warkworth $80 per desk, about $40 for the ocean portion of the journey and $40 for the land portion within the United States.
Andy Philpot, Warkworth’s director of operations, has been arguing for some time that Warkworth should set up a distribution center in southern California to receive products from Asia, and from there distribute them to its various stores. Warehouse space is much cheaper than prime retail space. Hence, the holding cost per TePaki desk per year in a warehouse would only be $60. The only problem with this approach, according to Andy, is that the total shipping cost from factory to store could increase by $8 per desk due to the extra handling and shipping distance once all of the desks are routed through a distribution center.
Karen understands why the distribution center approach could make sense, but she worries about getting all of the execution done right. Instead, she suggests that it ship all of the desks directly to the stores as it currently does, but then ship product between stores as needed. The only problem with that approach is that it probably will cost it about $40 per desk to ship from one store to another.
To add to the discussion, Kathy White, Warkworth’s marketing director, is concerned with how these ideas will affect the desks’ instore availability. She proudly reminds everyone that Warkworth currently has a .99 in-stock probability for the TePaki desk. Andy, a typical ops guy, quips that it could save a ton if it were willing to make its customers wait a week or so to get their desk delivered to the store from a distribution center.
Say Warkworth listened to Andy and didn’t hold inventory at die stores. Instead, inventory would be held in a distribution center and shipped to the stores as needed. How much would it save in inventory holding costs with this strategy?

Case summary:
Company WF specializes in furniture that are environmental friendly and sustainable in nature. The new desk TePaki is eco-friendly but it is costlier than conventional desks. Person AP is the director of operations looking to setup a distribution channel in the southern part of City C to receive products Asia. But, they are many points to consider before the move is actually made.
To determine: The inventory holding costs saved with the strategy.
Explanation of Solution
Given information:
Number of stores (N) = 30
Lead time (L) = 10 weeks
Production cost (P) = $325 per desk
Selling price (S) = $850 per desk
Weekly sales (d) = 6 desks or 0.2 desk per week per store
Holding cost (H) = $150 per desk per year
Shipping cost (C) = $80 per desk
Ocean part cost (OC) = $40
Land part cost (LC) = $40
New system:
Lead time (L) = 1 week
Holding cost (H) = $60 per desk per year
Increase in shipping cost (IC) = $8 per desk
Cost of shipping from store to another (SC) = $40
In-stock probability (IP) = 0.99
New system:
Calculation of demand over (L+1) weeks:
The in-stock probability is 0.99, therefore, the base stock level must be selected so that the in-stock probability is satisfied. The desired probability lies in the base stock level of 2.
With a base stock level of 1, and the probability of 0.99 the average inventory from the Poisson table is 1.61. The total holding costs are calculated as shown below:
The average inventory is 48.3.
Holding cost per desk:
Every year they operate for 52 weeks, and 6 desks are sold per week. Therefore, the holding cost per desk will be:
Distribution center:
Apart from this, the distribution center must also hold inventory. The lead time is 10 weeks. The average weekly demand over the lead time would be:
The demand distribution is centered with a mean of 66 desks. The standard deviation (SD) is calculated as shown below:
The mean is substantially greater than 20, and so the demand can be approximated with normal distribution. From the distribution table, to achieve an in-stock probability of 0.99, the z-value is 2.4. The base stock level is:
The average inventory for a z-value of 2.4 is calculated by using the I (2.4) value from the distribution table. Therefore, the average inventory is
The holding cost of the distribution center is calculated as shown below:
Holding cost per desk:
Every year they operate for 52 weeks, and 6 desks are sold per week. Therefore, the holding cost per desk will be:
The cost per desk at the distribution center is $3.75. While, the cost per desk at the stores is $23.22. If the customers are willing to wait, the Company can save an additional cost of $23.22 per desk.
The inventory holding costs saved with the strategy is $23.22.
Want to see more full solutions like this?
Chapter 14 Solutions
OPERATIONS MANAGEMENT (LL)-W/ACCESS
Additional Business Textbook Solutions
Operations Management
Business in Action
Operations Management
Principles of Operations Management: Sustainability and Supply Chain Management (10th Edition)
Operations Management: Processes and Supply Chains (12th Edition) (What's New in Operations Management)
Principles Of Operations Management
- UPD Manufacturing produces a range of health care appliances for hospital as well as for home use. The company has experienced a steady demand for its products, which are highly regarded in the health care field. Recently the company has undertaken a review of its inventory ordering procedures as part of a larger effort to reduce costs. One of the company's products is a blood pressure testing kit. UPD manufactures all of the components for the kit in-house except for the digital display unit. The display units are ordered at six-week intervals from the supplier. This ordering system began about five years ago, because the supplier insisted on it. However, that supplier was bought out by another supplier about a year ago, and the six-week ordering requirement is no longer in place. Nonetheless, UPD has continued to use the six-week ordering policy. According to purchasing manager Tom Chambers, “Unless somebody can give me a reason for changing, I'm going to stick with what we've been…arrow_forwardAn item has normally distributed demand with a mean of 100 and a standard deviation of 50. They order a week with one week lead time. Backorders are allowed. A) With an order-up-to level of 300, on-hand inventory of 200, and on-order inventory of 60, how much will be ordered this week? B) What is the standard deviation of demand over 2 weeks?arrow_forwardKen Ramsing has been in the lumber business for most of his life. Ken’s biggest competitor is Pacific Woods. Through many years of experience, Ken knows that the ordering cost for an order of plywood is $25 and that the carrying cost is 25% of the unit cost. Both Ken and Pacific Woods receive plywood in loads that cost $100 per load. Furthermore, Ken and Pacific Woods use the same supplier of plywood, and Ken was able to find out that Pacific Woods orders in quantities of 4,000 loads at a time. Ken also knows that 4,000 loads is the EOQ for Pacific Woods. What is the annual demand in loads of plywood for Pacific Woods?arrow_forward
- The Western Jeans Company purchases denim from Cumberland Textile Mills. The Western Jeans Company uses 35,000 yards of denim per year to make jeans. The cost of ordering denim from the textile company is $500 per order. It costs Western $0.35 per yard annually to hold a yard of denim in inventory. Determine the optimal number of yards of denim the Western Jeans Company should order, the minimum total annual inventory cost, the optimal number of orders per year, and the optimal time between orders.arrow_forward6. Leaky Pipe, a local retailer of plumbing supplies, faces demand for one of its SKUs at a constant rate of 17,000 units per year. It costs Leaky Pipe $5 to process an order to replenish stock and $2.00 per unit per year to carry the item in stock. Stock is received 12 working days after an order is placed. No backordering is allowed. Assume 365 working days a year. a. Leaky Pipe's optimal order quantity is ______ units. (Enter your response rounded to the nearest whole number.) Part 3 b. The optimal number of orders per year is _____ orders. (Enter your response rounded to the nearest whole number.) Part 4 c. The optimal interval (in working days) between orders is ______ days. (Enter your response rounded to one decimal place.)arrow_forwardA pharmacist is trying to determine the inventory order and stock levels for a particular drug. The following information is available about the drug. Demand (D) 85 tablets/week Working weeks per year 52 weeks Unit holding cost per year (H) $6 Order cost (S) $44/order Standard deviation of weekly demand (sd) 15 tablets Lead time (L) 2 weeks Desired cycle service level 95% If the pharmacist uses the continuous review (Q) system to control the inventory of the drug, what would be the order quantity and reorder point? If the pharmacist uses the periodic review (P) system to control the inventory of the drug, what would be the review interval and target inventory level? (Hint: Use the EOQ model to derive the review interval P)arrow_forward
- Daily demand of a chemical at an oil refinery is normally distributed with a mean of 60 litres and a standard deviation of 7. The supplier reliably delivers the chemical by maintaining a constant lead time of 1 week. There are no delivery charges from the supplier. Sales occur throughout the year. An order placement requires one hour of an administrative employee who is paid $20 per hour. Receiving and storing a chemical shipment requires two workers to work for half an hour. Workers are paid $12 per hour each. Chemical’s purchase price is $500 per litre. Annual cost of capital is 5%. Other holding costs are estimated to be $0.5 per litre. Find the order quantity and the reorder point to satisfy a 95% service level during the lead time. (Round answers to 2 decimal places.)arrow_forwardConsider the EOQ model. The optimal order quantity (Q*) is 500. What is the average inventory carried (I*)? Group of answer choices Cannot be determined 3,600 units 500 units 250 units 0 unitsarrow_forwardSam's Pet Hotel operates 52 weeks per year, 6 days per week, and uses a continuous review inventory system. It purchases kitty litter for $13.00 per bag. The following information is available about these bags: ≻Demand=75 bags/week ≻Order cost=$55.00/order ≻Annual holding cost=25 percent of cost ≻Desired cycle-service level=80 percent ≻Lead time=4 weeks (24 working days) ≻Standard deviation of weekly demand=15 bags ≻Current on-hand inventory is 320 bags, with no open orders or backorders. Part 2 a. Suppose that the weekly demand forecast of 75 bags is incorrect and actual demand averages only 50 bags per week. How much higher will total costs be, owing to the distorted EOQ caused by this forecast error? The costs will be $enter your response here higher owing to the error in EOQ. (Enter your response rounded to two decimal places.) a. What is the EOQ? What would the average time between orders (in weeks)? b. What should R be? c. An inventory withdraw…arrow_forward
- The amount of denim used daily by the Southwest ApparelCompany in its manufacturing process to make jeans isnormally distributed with an average of 4000 yards ofdenim and a standard deviation of 600 yards. The lead timerequired to receive an order of denim from the textile mill is a constant 7 days. Determine the safety stock and re-order point if the company wants to limit the probability of a stockout and work stoppage to 5%.arrow_forwardSouthern Markets, Inc., is considering the use of ABC analysis to focus on the most critical SKUs in its inventory. Currently, there are approximately 20,000 different SKUs with a total dollar usage of $10,000,000 per year.a. What would you expect to be the number of SKUs and the total annual dollar usage for A items, B items, and C items at Southern Markets, Inc.?350 PART 2 Managing Customer Demandb. The following table provides a random sample of the unit values and annual demands of eight SKUs. Categorize these SKUs as A, B, and C items.SKU Code Unit Value Demand (Units)A104 $2.10 2,500D205 $2.50 30X104 $0.85 350U404 $0.25 250L205 $4.75 20S104…arrow_forwardSuppose the following item is being managed using a fixed-order quantity model with safety stock. Annual Demand = 100,000 units Order quantity = 30,000 units Safety stock = 4000 units What are the average inventory level and inventory turnover for this item?arrow_forward
- Practical Management ScienceOperations ManagementISBN:9781337406659Author:WINSTON, Wayne L.Publisher:Cengage,Operations ManagementOperations ManagementISBN:9781259667473Author:William J StevensonPublisher:McGraw-Hill EducationOperations and Supply Chain Management (Mcgraw-hi...Operations ManagementISBN:9781259666100Author:F. Robert Jacobs, Richard B ChasePublisher:McGraw-Hill Education
- Purchasing and Supply Chain ManagementOperations ManagementISBN:9781285869681Author:Robert M. Monczka, Robert B. Handfield, Larry C. Giunipero, James L. PattersonPublisher:Cengage LearningProduction and Operations Analysis, Seventh Editi...Operations ManagementISBN:9781478623069Author:Steven Nahmias, Tava Lennon OlsenPublisher:Waveland Press, Inc.
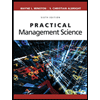
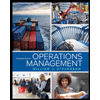
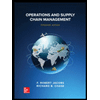
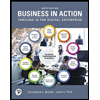
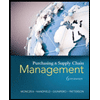
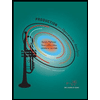