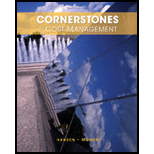
Concept explainers
1 a.
Ascertain the productivity profile for 2014 using actual inputs.
1 a.

Explanation of Solution
Productivity measurement: The productivity measurement refers to the quantitative assessment of the changes in the productivity.
Profile measurement and analysis: The profile measurement and analysis refers to the computation of a set of operational partial productivity measures and their comparison to the corresponding set of base period, for the assessment of the nature of changes in productivity.
Compute the productivity profile for 2014:
Compute the Material Productivity Profile for 2014:
Compute the Labor Productivity Profile for 2014:
The Material Productivity Profile is 1.67 and Labor Productivity Profile is 0.83.
1 b.
Ascertain the productivity profile for 2015 for the proposed process changes.
1 b.

Explanation of Solution
Compute the productivity profile for 2015 Change 1:
Compute the Material Productivity Profile for 2015 Change 1:
Compute the Labor Productivity Profile for 2015 Change 1:
The Material Productivity Profile is 1.43 and Labor Productivity Profile is 1.25.
Compute the productivity profile for 2015 Change 2:
Compute the Material Productivity Profile for 2015 Change 2:
Compute the Labor Productivity Profile for 2015 Change 2:
The Material Productivity Profile is 2.00 and Labor Productivity Profile is 1.00.
There is an overall improvement in the output input ratio from 2014 to 2015.
1 c.
Ascertain the productivity profile for optimal input combination and recommend the most productive profile.
1 c.

Explanation of Solution
Compute the productivity profile for optimal input combination:
Compute the Material Productivity Profile for optimal input combination:
Compute the Labor Productivity Profile for optimal input combination:
The Material Productivity Profile is 2.50 and Labor Productivity Profile is 1.25.
There is an overall improvement in the output input ratio from 2014 to 2015. The change 1 in 2015 has the optimum labor productivity, however the material productivity is very low. In the Change 2 of 2015, both material and labor productivity are good. Now for the decision regarding the implementation of the productivity profile, this depends on the productivity trade-offs of the inputs.
2.
Ascertain the productive inefficiency among the given combinations and compare the improvement along with the changes in the technical and
2.

Explanation of Solution
Total productive efficiency: The total productive efficiency refers to the point where the maximum technical and allocative efficiency is achieved. This is the point where the production of a new product may compromise the production of another product, as the optimum quantity of inputs is being used to get the desired output.
The technical efficiency ensures no more units of input than the required number is used for any mix of inputs.
The allocative efficiency ensures the use of an inexpensive and most technically efficient mix.
Compute the total cost of productive efficiency:
Particulars | Number of Units (A) | Cost per Unit (B) | |
2014 | |||
Cost of materials | 33,000 | $ 60 | $ 1,980,000 |
Cost of labor | 66,000 | $ 15 | $ 990,000 |
Total Cost | $ 2,970,000 | ||
2015 Change 1 | |||
Cost of materials | 38,500 | $ 60 | $ 2,310,000 |
Cost of labor | 44,000 | $ 15 | $ 660,000 |
Total Cost | $ 2,970,000 | ||
2015 Change 2 | |||
Cost of materials | 27,500 | $ 60 | $ 1,650,000 |
Cost of labor | 55,000 | $ 15 | $ 825,000 |
Total Cost | $ 2,475,000 | ||
Optimal Input | |||
Cost of materials | 22,000 | $ 60 | $ 1,320,000 |
Cost of labor | 44,000 | $ 15 | $ 660,000 |
Total Cost | $ 1,980,000 |
Table (1)
Compute the total cost of productive inefficiency:
Compute the cost of productive inefficiency for 2014:
Compute the cost of productive inefficiency for 2015 Change 1:
Compute the cost of productive inefficiency for 2015 Change 2:
Compute the potential improvement:
Compute the potential improvement for 2015 Change 1:
Compute the potential improvement for 2015 Change 2:
The Change 1 has greater technical efficiency but the allocative efficiency is reduced, on the other hand Change 2 is able to attain both technical and allocative efficiency.
3.
Compute and describe the price recovery component.
3.

Explanation of Solution
Profit-linked productivity measurement and analysis: The profit-linked productivity measurement and analysis is the ascertainment of the amount of change in profit, from the base period to the current period, due to the various changes in the productivity.
Compute the profit-linked productivity measurement:
Compute the profit-linked productivity measurement for 2015 Change 1:
Compute the profit-linked productivity measurement for 2015 Change 2:
The profit-linked productivity measurement takes into consideration only the changes in the input with no regards to the base or optimal combination.
Want to see more full solutions like this?
Chapter 15 Solutions
Cornerstones of Cost Management (Cornerstones Series)
- Mabbut Company has the following departmental manufacturing layout for one of its plants: A consulting firm recommended a value stream with the following manufacturing cell: Required: 1. Calculate the total time it takes to produce a batch of 10 units using the traditional departmental manufacturing layout. 2. Using cellular manufacturing, how much time is saved producing the same batch of 10 units? Assuming the cell operates continuously, what is the production rate? Which process controls this production rate? 3. Assume the processing time of Welding is reduced to 6 minutes, while the times of the other processes stay the same. What is the production rate now, and how long will it take to produce a batch of 10 units if the cell is in a continuous production mode?arrow_forwardMaterials used by the Instrument Division of Ziegler Inc. are currently purchased from outside suppliers at a cost of 1,350 per unit. However, the same materials are available from the Components Division. The Components Division has unused capacity and can produce the materials needed by the Instrument Division at a variable cost of 900 per unit. a. If a transfer price of 1,000 per unit is established and 75,000 units of materials are transferred, with no reduction in the Components Divisions current sales, how much would Ziegler Inc.s total operating income increase? b. How much would the Instrument Divisions operating income increase? c. How much would the Components Divisions operating income increase?arrow_forwardAnderson Company has the following departmental manufacturing structure for one of its products: After some study, the production manager of Anderson recommended the following revised cellular manufacturing approach: Required: 1. Calculate the total time it takes to produce a batch of 20 units using Andersons traditional departmental structure. 2. Using cellular manufacturing, how much time is saved producing the same batch of 20 units? Assuming the cell operates continuously, what is the production rate? Which process controls this production rate? 3. What if the processing times of molding, welding, and assembly are all reduced to six minutes each? What is the production rate now, and how long will it take to produce a batch of 20 units?arrow_forward
- A process control manager is considering two robots to improve materials handling capacity in the production of rigid shaft couplings that mate dissimilar drive components. Robot X has a first cost of $84,000, an annual M&O cost of $31,000, a $40,000 salvage value, and will improve revenues by $96,000 per year. Robot Y has a first cost of $146,000, an annual M&O cost of $28,000, a $47,000 salvage value, and will increase revenues by $119,000 per year. The company’s MARR is 15% per year and it uses a 3-year study period for economic evaluations. Which one should the manager select (a) on the basis of ROR values, and (b) on the basis of the incremental ROR value? (c) Which is the correct selection basis? Perform the analysis by hand or spreadsheet, as instructed.arrow_forwardIf 60,000 machine hours are available, and management desires to follow an optimal strategy, how many units of each product should the firm manufacture? How many units of each product should be purchased? With all other things constant, if management is able to reduce the direct material for an electric mixer to $23 per unit, how many units of each product should be manufactured? Purchased?arrow_forwardMSI is considering outsourcing the production of the handheld control module used with some of its products. The company has received a bid from Monte Legend Co. (MLC) to produce 10,000 units of the module per year for $16 each. The following information pertains to MSI’s production of the control modules: Direct materials $ 9 Direct labor 4 Variable manufacturing overhead 2 Fixed manufacturing overhead 3 Total cost per unit $ 18 MSI has determined that it could eliminate all variable costs if the control modules were produced externally, but none of the fixed overhead is avoidable. At this time, MSI has no specific use in mind for the space that is currently dedicated to the control module production. Suppose that the MSI space currently used for the modules could be utilized by a new product line that would generate $35,000 in annual profit. Recompute the difference in cost between making and buying under this scenario.arrow_forward
- Wilmington Chemical Company produces three products: ethylene, butane, and ester. Each of these products has high demand in the market, and Wilmington Chemical is able to sell as much as it can produce of all three. The reaction operation is a bottleneck in the process and is running at 100% of capacity. Wilmington wants to improve chemical operation profitability. The variable conversion cost is $10 per process hour. The fixed cost is $400,000. In addition, the cost analyst was able to determine the following information about the three products: Ethylene Butane Ester Budgeted units produced 9,000 9,000 9,000 Total process hours per unit 4.0 4.0 3.0 Reactor hours per unit 1.5 1.0 0.5 Unit selling price $170 $155 $130 Direct materials cost per unit $115 $88 $85 The reaction operation is part of the total process for each of these three products. Thus, for example, 1.5 of the 4.0 hours required to…arrow_forwardWoodruff Company is currently producing a snowmobile that uses five specialized parts. Engineering has proposed replacing these specialized parts with commodity parts, which will cost less and can be purchased in larger order quantities. Current activity capacity and demand (with specialized parts required) and expected activity demand (with only commodity parts required) are provided. Activities Activity Driver ActivityCapacity Current ActivityDemand Expected ActivityDemand Material usage Number of parts 270,000 270,000 270,000 Installing parts Direct labor hours 17,000 17,000 13,600 Purchasing parts Number of orders 13,600 11,628 7,140 Additionally, the following activity cost data are provided: Material usage: $23 per specialized part used; $15 per commodity part; no fixed activity cost. Installing parts: $22 per direct labor hour; no fixed activity cost. Purchasing parts: Four salaried clerks, each earning a $48,000 annual salary; each clerk is capable of processing…arrow_forwardAMD is contemplating a decision to either continue producing a unique line of microprocessors, or discontinue production. • The AMD factory manufactures approximately 100,000 of such processors and generates $3,000,000 in revenues and incurs $2,000,000 in variable costs. • AMD estimates that if the product is discontinued ADM would save $ 1,500,000 in fixed manufacturing costs in engineering support and depreciation costs of production equipment. • Should AMD keep or discontinue production of this product line?arrow_forward
- During the first calendar quarter of 2016, Clinton Corporation is planning to manufacture a new product and introduce it in two regions. Market research indicates that sales will be 10,000 units in the urban region at a unit price of $53 and 9,000 units in the rural region at $48 each. Because the sales manager expects the product to catch on, he has asked for production sufficient to generate a 8,000-unit ending inventory. The production manager has furnished the following estimates related to manufacturing costs and operating expenses: Variable Fixed (per unit) (total) Manufacturing costs: Direct materials A (4 lb. @ $3.15/lb.) $12.60 - B (2 lb. @ $4.65/lb.) 9.30 - Direct labor (0.5 hours per unit) 7.50 - Manufacturing overhead: Depreciation - $7,650 Factory supplies 0.90 4,500 Supervisory salaries - 28,800 Other 0.75 22,950 Operating expenses:…arrow_forwardWoodruff Company is currently producing a snowmobile that uses five specialized parts. Engineering has proposed replacing these specialized parts with commodity parts, which will cost less and can be purchased in larger order quantities. Current activity capacity and demand (with specialized parts required) and expected activity demand (with only commodity parts required) are provided. Activities Activity Driver ActivityCapacity Current ActivityDemand Expected ActivityDemand Material usage Number of parts 200,000 200,000 200,000 Installing parts Direct labor hours 20,000 20,000 16,000 Purchasing parts Number of orders 7,600 6,498 3,990 Additionally, the following activity cost data are provided: Material usage: $11 per specialized part used; $27 per commodity part; no fixed activity cost. Installing parts: $21 per direct labor hour; no fixed activity cost. Purchasing parts: Four salaried clerks, each earning a $47,000 annual salary; each clerk is capable of processing 1,900…arrow_forwardThunder Bolt, Inc., is a manufacturer of the very popular G36 motorcycles. The management at Thunder Bolt has recently adopted absorption costing and is debating which denominatorlevel concept to use. The G36 motorcycles sell for an average price of $8,200. Budgeted fixed manufacturing overhead costs for 2017 are estimated at $6,480,000. Thunder Bolt, Inc., uses subassembly operators that provide component parts. The following are the denominator-level options that management has been considering: a. Theoretical capacity—based on three shifts, completion of five motorcycles per shift, and a 360-day year—3 * 5 * 360 = 5,400. b. Practical capacity—theoretical capacity adjusted for unavoidable interruptions, breakdowns, and so forth—3 * 4 * 320 = 3,840. c. Normal capacity utilization—estimated at 3,240 units. d. Master-budget capacity utilization—the strengthening stock market and the growing popularity of motorcycles have prompted the marketing department to issue an estimate for 2017 of…arrow_forward
- Cornerstones of Cost Management (Cornerstones Ser...AccountingISBN:9781305970663Author:Don R. Hansen, Maryanne M. MowenPublisher:Cengage LearningManagerial Accounting: The Cornerstone of Busines...AccountingISBN:9781337115773Author:Maryanne M. Mowen, Don R. Hansen, Dan L. HeitgerPublisher:Cengage LearningManagerial AccountingAccountingISBN:9781337912020Author:Carl Warren, Ph.d. Cma William B. TaylerPublisher:South-Western College Pub
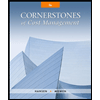
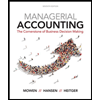
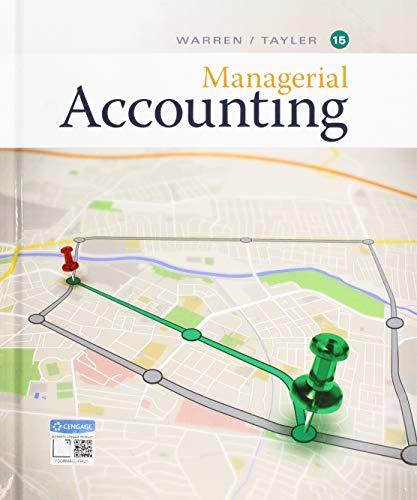