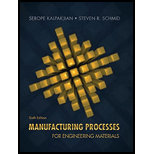
(a)
The force vs. reduction in height curve in open die forging of cylinder for
(a)

Explanation of Solution
Given:
The initial thickness of the specimen is
The initial diameter of the specimen is
The friction coefficient is
The velocity of the hydraulic press is
Formula used:
The expression for the flow stress is given as,
Here,
The expression for the true strain is given as,
Here,
The expression for the final radius by equating the volume is given as,
The expression for the forging force is given as,
Here,
The expression for the average pressure is given as,
The expression for final height for
The expression for final height for
The expression for final height for
The expression for final height for
The expression for final height for
Calculation:
For
The final height can be calculated as,
The final radius can be calculated as,
The true strain can be calculated as,
The flow stress can be calculated as,
Refer to table 2.2 “Typical values of strength coefficient
The average pressure can be calculated as,
The forging force can be calculated as,
For
The final height can be calculated as,
The final radius can be calculated as,
The true strain can be calculated as,
The flow stress can be calculated as,
Refer to table 2.2 “Typical values of strength coefficient
The average pressure can be calculated as,
The forging force can be calculated as,
For
The final height can be calculated as,
The final radius can be calculated as,
The true strain can be calculated as,
The flow stress can be calculated as,
Refer to table 2.2 “Typical values of strength coefficient
The average pressure can be calculated as,
The forging force can be calculated as,
For
The final height can be calculated as,
The final radius can be calculated as,
The true strain can be calculated as,
The flow stress can be calculated as,
Refer to table 2.2 “Typical values of strength coefficient
The average pressure can be calculated as,
The forging force can be calculated as,
For
The final height can be calculated as,
The final radius can be calculated as,
The true strain can be calculated as,
The flow stress can be calculated as,
Refer to table 2.2 “Typical values of strength coefficient
The average pressure can be calculated as,
The forging force can be calculated as,
For
Reduction (in | Forging force (in |
The plot between forging force and reduction in height is shown in figure (1) below,
Figure (1)
(b)
The force vs. reduction in height curve in open die forging of cylinder for
(b)

Explanation of Solution
Given:
The initial thickness of the specimen is
The initial diameter of the specimen is
The friction coefficient is
The velocity of the hydraulic press is
Formula used:
The expression for the flow stress is given as,
Here,
The expression for the true strain is given as,
Here,
The expression for the final radius by equating the volume is given as,
The expression for the forging force is given as,
Here,
The expression for the average pressure is given as,
The expression for final height for
The expression for final height for
The expression for final height for
The expression for final height for
The expression for final height for
Calculation:
For
The final height can be calculated as,
The final radius can be calculated as,
The true strain can be calculated as,
The flow stress can be calculated as,
Refer to table 2.2 “Typical values of strength coefficient
The average pressure can be calculated as,
The forging force can be calculated as,
For
The final height can be calculated as,
The final radius can be calculated as,
The true strain can be calculated as,
The flow stress can be calculated as,
Refer to table 2.2 “Typical values of strength coefficient
The average pressure can be calculated as,
The forging force can be calculated as,
For
The final height can be calculated as,
The final radius can be calculated as,
The true strain can be calculated as,
The flow stress can be calculated as,
Refer to table 2.2 “Typical values of strength coefficient
The average pressure can be calculated as,
The forging force can be calculated as,
For
The final height can be calculated as,
The final radius can be calculated as,
The true strain can be calculated as,
The flow stress can be calculated as,
Refer to table 2.2 “Typical values of strength coefficient
The average pressure can be calculated as,
The forging force can be calculated as,
For
The final height can be calculated as,
The final radius can be calculated as,
The true strain can be calculated as,
The flow stress can be calculated as,
Refer to table 2.2 “Typical values of strength coefficient
The average pressure can be calculated as,
The forging force can be calculated as,
For
Reduction (in | Forging force (in |
The plot between forging force and reduction in height is shown in figure (2) below,
Figure (2)
Want to see more full solutions like this?
Chapter 6 Solutions
Manufacturing Processes for Engineering Materials (6th Edition)
- In open-die forging, disc of diameter 200 mm and height 60 mm is compressed without any barreling effect. The final diameter of the disc is 400 mm. The true strain isarrow_forwardIn a rolling operation using rolls of diameter 500 mm, if a 25 mm thick plate cannot be reduced to less than 20 mm in one Pass, Estimate the coefficient of friction between the roll and the plate.arrow_forwardDescribe the effect that extrusion has on material properties with examplesarrow_forward
- 1. A round wire made from 1020 carbon steel is being drawn from a diameter of 12.5 mm to 9.5 mm in a draw die of 10°. For a coefficient of friction of 0.15, calculate required drawing force. 2. How would the extrusion process be effected if the die angle is increased?arrow_forwardA solid cylindrical work piece is reduced in height by an open die forging process using flat dies on a mechanical press, powered by a 20 kW motor which operates at 35 strokes per minute with a stroke length of 160 mm. The work piece is 60 mm high and 100 mm in diameter and is to be reduced in height by 15%. The coefficient of friction during the operation is 0,18. Calculate the flow stress of work piece material if the press is set to operate at 90% of its maximum capacity.arrow_forwardA solid cylindrical slug made of 304 stainless steel is 150 mm in diameter and 100 mm high. It is reduced in height by 50% at room temperature by opendie forging with flat dies. Assuming that the coefficient of friction is 0.2 and the flow stress of this material is 1000 MPa, calculate the forging force at the end of the stroke. Manufacturing processesarrow_forward
- A 40 mm thick plate made from 410 grade stainless steel is to be reduced to 34 mm in one pass in a rolling operation. As the thickness is reduced, the plate widens by 3%. The entrance speed of the plate is 13 m/min and the roll radius is 310 mm with a rotational speed of 30 rpm. To do 5.1 If the final width of the sheet is 200 mm, calculate the required roll force. 5.2. Explain what is roll flattening, its effects and how it can be reduced.arrow_forwardAn austenitic stainless steel plate with a width of 100 mm, a length of 150 mm and a thickness of 50 mm is to be hot forged in a hydraulic press so that the width remains constant. If it is to be reduced in one step to a thickness of 40 mm, calculatea) the actual load that needs to be applied at the end of the forging, as well as b) the corresponding deformation energy. In previous plane strain compression tests, it was found that the material exhibits an average plane strain yield stress of 80 MPa at the forging temperature. Assume that the efficiency of the process is 0.6 Answer: Pfr= 2.5 MN ; WTr= 25 kJarrow_forwardWrite a detailed note on "Hydrostatic Extrusion". Also draw diagrams to explain the process of hydrostatic extrusion.arrow_forward
- A 300mm thick slab is being cold rolled using roll of 600mm diameter.If the coefficient of friction is 0.08. Determine the maximum possible reduction.arrow_forwardA spool of wire has a starting diameter of 2.5 mm. It is drawn through a die with an opening that is 2.1 mm at a speed of 0.3 m/s. The worked metal has a strength coefficient of 450 MPa and a strain-hardening coefficient of 0.26. Assume the drawing is performed at room temperature and that the frictional and redundant work together constitute 35% of the ideal work of deformation. Calculate the power required to carry out the operationarrow_forwardA 3in long and 1in diameter billet is extruded in a direct extrusion operation with an rx = 4.0. The extrusion has a cross section. The angle of the die (half angle) is 90o. The work metal has a resistance coefficient of 60ksi and a strain hardening exponent of 0.18. Use Johnston's formula with a = 0.8 and b = 1.5 to estimate the extrusion stress. Determine the pressure applied to the end of the billet when the piston moves forward.arrow_forward
- Elements Of ElectromagneticsMechanical EngineeringISBN:9780190698614Author:Sadiku, Matthew N. O.Publisher:Oxford University PressMechanics of Materials (10th Edition)Mechanical EngineeringISBN:9780134319650Author:Russell C. HibbelerPublisher:PEARSONThermodynamics: An Engineering ApproachMechanical EngineeringISBN:9781259822674Author:Yunus A. Cengel Dr., Michael A. BolesPublisher:McGraw-Hill Education
- Control Systems EngineeringMechanical EngineeringISBN:9781118170519Author:Norman S. NisePublisher:WILEYMechanics of Materials (MindTap Course List)Mechanical EngineeringISBN:9781337093347Author:Barry J. Goodno, James M. GerePublisher:Cengage LearningEngineering Mechanics: StaticsMechanical EngineeringISBN:9781118807330Author:James L. Meriam, L. G. Kraige, J. N. BoltonPublisher:WILEY
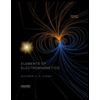
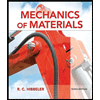
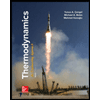
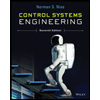
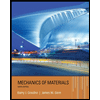
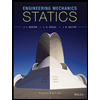