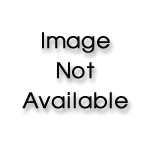
Concept explainers
The Barberton Municipal Division of Road Maintenance is charged with road repair in the city of Barberton and the surrounding area. Cindy Kramer, road maintenance director, must submit a staffing plan for the next year based on a set
- Find a level staffing plan that relies just on overtime and tile minimum amount of undertime possible. Overtime can be used to its limits in any quarter. What is the total cost of the plan and how many under time hours does it call for?
- Use a chase strategy that varies the workforce level without using overtime or undertime. What is the total cost of this plan?
- Propose a plan of your own. Compare your plan with those in parts (a) and (b), and discuss its comparative merits.

Want to see the full answer?
Check out a sample textbook solution
Chapter 10 Solutions
MyLab Operations Management with Pearson eText -- Access Card -- for Operations Management: Processes and Supply Chains
Additional Business Textbook Solutions
Operations Management: Sustainability and Supply Chain Management (12th Edition)
Operations and Supply Chain Management 9th edition
Principles of Operations Management: Sustainability and Supply Chain Management (10th Edition)
Business in Action
Operations Management
Operations Management, Binder Ready Version: An Integrated Approach
- XYZ Company produces and sells 2 products, Lambda and Gamma, and the production process goes through two departments. Traditionally Manufacturing Overhead (M/O) cost is applied on the basis of direct labor hours (DLH); estimated M/O cost is $ 5,757,500 and the estimated DLH is $12,250 for the most recent period.The team decided to replace traditional plantwide costing system to activity-based costing system. There are 3 activity cost pools which represent 3 activity areas at the plant. Direct Labor wage rate is $ 30 per hour. Compute total cost per unit (for lambda and gamma) using activity-based approach. (round your numbers).arrow_forwardThe Sun River beverage company is a regional producer of teas, exotic juices, and energy drinks. With an interest in healthier lifestyles, there has been an increase in demand for its sugar-free formulation. The final packing operation requires 13 tasks. Sun River bottles its sugar-free product 5 hours a day, 5 days a week. Each week, there is a demand for 2,500 bottles of this product. TASK 1 4 6 8 9 10 11 12 13 PERFORMANCE TIME TASK MUST (MINUTES) FOLLOW 0.1 0.2 Efficiency 0.2 0.2 0.1 0.3 0.3 0.1 0.3 0.2 0.1 0.1 0.1 2 7 B 9 6 10, 11 12 Using the above data, solve the assembly-line balancing problem and calculate the efficiency of your solution. Use the longest task time for your decision criteria. (Enter your answer as a percentage rounded to 1 decimal place.)arrow_forwardEmployees Layoffs at the University Medical Center The University Medical Center is medium-sized, 300-bed capacity hospital at Dasmarinas Cavites. The facilities have grown gradually over the years and are now the 2nd largest in the town of Dasmarinas. It is entirely nonunion and has never experienced an employee layoff since its inception. Sister Veronica Cornista, the Chief Executive Officer of the hospital for 8 years presented a rather bleak financial of the BOD. This according to her is the result of the declining occupancy rate which has affected the hospital’s revenues to such an extent that it ran a deficit for the first time last 1998. Such declines have not been unusual for this industry because of increasing competition. So far, the only response to these changes has been tightening of requirements for equipment or supply purchases. The projected deficit for the coming year is around 1,300,000 unless some additional revenues were identified or some additional savings…arrow_forward
- Tailwind, Inc., produces high-quality but expensive training shoes for runners. The Tailwind shoe, which sells for $210, contains both gas- and liquid-filled compartments to provide more stability and better protection against knee, foot, and back injuries. Manufacturing the shoes requires 10 separate tasks. There are 400minutes available for manufacturing the shoes in the plant each day. Daily demand is 62.The information for the tasks is as follows: Task Performance Time (mins) Predecessors A 1 − B 3 A C 1 B D 4 B E 1 C, D F 3 A G 2 F H 5 G I 3 E, H J 2 I a-b) The correct precedence relationship with one of the possible assignments of tasks using the "ranked positionedweight" to workstations is shown in Fig 1, 2 or 3 c) The efficiency of the assembly line with 5 workstations shown in the figure…arrow_forwardThe director of social services of a county has learned that the state has mandated additional information requirements. This will place an additional burden on the agency. The director has identified three acceptable alternatives to handle the increased workload. One alternative is to reassign present staff members, the second is to hire and train two new workers, and the third is to redesign current practice so that workers can readily collect the information with little additional effort. An unknown factor is the caseload for the coming year when the new data will be collected on a trial basis. The estimated costs for various options and caseloads are shown in the following table: CASELOAD Moderate High Very High Reassign staff $ 80 * 90 95 New staff 70 70 70 Redesign collection 90 80 70 *Cost in $ thousands. After contemplating the caseload question, the director of social services has decided that reasonable caseload probabilities are 0.30 for…arrow_forwardIn reference to an Human Resource Management course 4th year college course at Malone University using the following textbook: Gomez-Mejia, L. R., Balkin, D. B., Cardy, R. L., & Carson, K. P. (2020). Managing human resources. (9th ed.). Boston: Pearson Education. Which one of the following functions is typically not a human resource management responsibility? a. Analysis and design of work b. Demand forecasting c. Performance management and development d. Exit interviewsarrow_forward
- Medical Solutions, Inc. has the following claims it must complete in the next week (40 hours). The jobs are as follows: Claim Type Spinal injury Number of Claims Setup (Changeover) to Process (Work Time per Claim Type (hours) Cancer treatment 15 Hip replacement Order Quantity) 14 10 SI Claims Workload: hours Processing Time per Claim (hours) HR Claims Workload: hours 3.0 1.1 2.5 0.9 1.5 All claims of the same type are processed together. Is 40 hours enough capacity? (Hint: use Equation 10.3.) Round your answers to one decimal place. CT Claims Workload: hours 0.5 Total workload is hours while capacity is 40 hours. The work -Select-cancannotItem 5 be completed using regular time hours.arrow_forwardA small-size cargo company in Dubai has been operating since the year 2000. The total workforce comprises ten employees, out of which five are in sales, three are in operations, one is handling legal and accounts matters, and one manager is also the owner of the company. Total annual turnover is enough to run the company smoothly. Recently another director has joined who brought large investment to the company. The Board of directors has decided to expand the business in other cities and establish offices overseas in potential locations. This expansion policy will directly be linked to the new manpower needs. Therefore, the board has decided to open an HR department with one HR manager and three staff to look after HR operations. The new HR manager has noticed that the company has a very convenient way of recording the data, where all transactions are recorded on excel documents. “this may not work in the new setup with many branches around the world”, he mentioned in the BOD meeting.…arrow_forwardManufacturing Company uses FIFO method of accumulating costs in a two-department process. Materials are introduced at the inception of the process except for a special material which is added in department 2 at 60% completion as to overhead. Inspection is done at the end of the process in both departments. Production data for Department 2 are given below: In process, beginning, (80% labor, 70% overhead)2,000 Transferred in 14,900 In process, ending (40% labor, 20% overhead) 3,000 Normal spoilage 200 Abnormal spoilage (found at 30% completion as to laborand 15% as to overhead due to internal failure) 400 Cost data for the month:In process beginning:Transferred in 15,020 Special materials 1,900 Direct labor 4,388 Overhead 11,044 Current costs:Transferred in 137,080 Special materials 14,030 Direct labor 46,000 Overhead 113,564 The cost of units transferred to finished goods is?The cost of spoilage charged to revenue is?arrow_forward
- Fast Burger Inc. is building a new restaurant near a college football stadium. The restaurant will be open 16 hours per day, 360 days per year. Managers have concluded that the restaurant should have the capacity to handle a peak hour demand of 120 customers. Assume front-counter service personnel can take and assemble orders at the service rate of 14 customers per hour and the target labor utilization rate for this job is 70 percent. According to the information, determine the the number of front-service counter people that should be assigned to this peak demand period. Only for non-integer results, round your answer UP to the nearest integer. For example, if your answer is 5.05, type 6; if your answer is 5, type 5. Your Answer: Answerarrow_forwardSue Helms Appliances wants to establish an assem-bly line to manufacture its new product, the Micro Popcorn Popper. The goal is to produce five poppers per hour. The tasks,task times, and immediate predecessors for producing one MicroPopcorn Popper are as follows:TASK TIME (min) IMMEDIATEPREDECESSORSA 10 —B 12 AC 8 A, BD 6 B, CE 6 CF 6 D, Ea) What is the theoretical minimum for the smallest number ofworkstations that Helms can achieve in this assembly line?b) Graph the assembly line, and assign workers to workstations.Can you assign them with the theoretical minimum?c) What is the efficiency of your assignment?arrow_forwardTailwind, Inc., produces high-quality but expensive training shoes for runners. The Tailwind shoe, which sells for $210, contains both gas- and liquid-filled compartments to provide more stability and better protection against knee, foot, and back injuries. Manufacturing the shoes requires 10 separate tasks. There are 400 minutes available for manufacturing the shoes in the plant each day. Daily demand is 60. The information for the tasks is as follows: Performance Time Task (in minutes) 1 Н ABCDEFGH Task Must Follow This Task C, D ABB GAFG 324-325- E, H 25 312 | Required: a. Draw the precedence diagram showing the task precedence and their times b. Determine the cycle time associated with the rate of output required. c. What is the theoretical minimum number of work stations required to satisfy this output rate? d. Allocate the tasks to work stations taking into consideration the precedence requirements and using the LOT rule to break ties between feasible tasks. e. What is the…arrow_forward
- Practical Management ScienceOperations ManagementISBN:9781337406659Author:WINSTON, Wayne L.Publisher:Cengage,
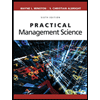