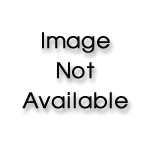
Concept explainers
a
Interpretation: Quarterly production rate which minimize the anticipatory inventory is to be determined.
Concept Introduction:
Anticipatory production is the stock kept by firms to meet uncertain demand or any increase in price of inputs or any uncertain situation.
b
Interpretation: The Anticipatory gallons that will be produced are to be specified.
Introduction:
Anticipatory production is the stock kept by firms to meet uncertain demand or any increase in price of inputs or any uncertain situation.
c
Interpretation: Level of production rate required is to be determined.
Introduction:
Anticipatory production is the stock kept by firms to meet uncertain demand or any increase in price of inputs or any uncertain situation.

Want to see the full answer?
Check out a sample textbook solution
Chapter 10 Solutions
MyLab Operations Management with Pearson eText -- Access Card -- for Operations Management: Processes and Supply Chains
- An engineering plant has developed the accompanying supply, demand, cost and inventory data. The engineering plant has a constant workforce and meets all its demands. Allocate production capacity to satisfy demand at a minimum cost. What is the cost of this plan? (Assume that back ordering is not a viable alternative for the plant) Demand forecast Period Demand (Unit) 1 650 2 700 3 900 Supply Capacity available (units) Period Regular time Overtime Subcontract 1 350 100 250 2 450 100 250 3 500 100 250 Other Data Initial Inventory 100 units Regular-time cost per unit R 50 Overtime cost per unit R 65 Subcontract cost per unit R 80 Carrying cost per unit per period R 1 Back order cost per unit per period R 4arrow_forwardThe Donald Fertilizer Company produces industrial chemi-cal fertilizers. The projected manufacturing requirements (inthousands of gallons) for the next four quarters are 90, 60,90, and 140, respectively. A level workforce is desired, relyingonly on anticipation inventory as a supply option. Stock-outs and backorders are to be avoided, as are overtime andundertime.a. Determine the quarterly production rate required to meettotal demand for the year, and minimize the anticipationinventory that would be left over at the end of the year.Beginning inventory is 0.b. Specify the anticipation inventory that will be produced.c. Suppose that the requirements for the next four quartersare revised to 60, 90, 140, and 90, respectively. If total de-mand is the same, what level of production rate is needednow, using the same strategy as part (a)?arrow_forward12. Zan Azlett and Angela Zesiger have joined forces to start A&Z Lettuce Products, a processor of packaged shredded lettuce for institutional use. Zan has years of food processing experience, and Angela has extensive commercial food preparation experience. The process will consist of opening crates of lettuce and then sorting, washing, slicing, preserving, and finally packaging the prepared lettuce. Together, with help from vendors, they think they can adequately estimate demand, fixed costs, revenues, and variable cost per bag of lettuce. They think a largely manual process will have monthly fixed costs of $36,000 and variable costs of $1.75 per bag. A more mechanized process will have fixed costs of $72,000 per month with variable costs of $1.25 per bag. They expect to sell the shredded lettuce for $2.75 per bag. Part 2 a) The break-even quantity in units for the manual process = ______ bags (round your response to the nearest whole number). b) The revenue for…arrow_forward
- Jill wants you to consider a hybrid aggregate plan, usingup to the maximum overtime per employee for any periodwhere demand cannot be satisfi ed with the current regular-timeproduction and the available inventory. Back orders can occur.(a) Show what would happen if this plan were implemented.(b) Calculate the costs associated with this plan.(c) Evaluate the plan in terms of cost, customer service,operations, and human resourcesarrow_forwardExercise 3: Daily demand for a product of a computer manufacturer is 400,000 units. The company, on average, makes $150 net profit for each computer. The current fill rate is 86%. About 70% of their incomplete orders are back-ordered, and the rests are cancelled. The company is considering to improve the fill rate to 90% whose estimated daily additional operating cost (e.g.,improving the warehousing and transportation) is $2,000,000. What should be the minimum back-order cost to make this investment reasonable?arrow_forwardThe Donald Fertilizer Company produces industrial chemical fertilizers. The projected manufacturing requirements (in thousands of gallons) for the next four quarters are 80, 50, 80, and 130, respectively. A level workforce is desired, relying only on anticipation inventory as a supply option. Stockouts and backorders are to be avoided, as are overtime and undertime.a. Determine the quarterly production rate required to meet total demand for the year, and minimize the anticipation inventory that would be left over at the end of the year. Beginning inventory is zero.b. Specify the anticipation inventory that will be produced.c. Suppose that the requirements for the next four quarters are revised to 80, 130, 50, and 80, respectively. If total demand is the same, what level of production rate is needed now, using the same strategy as part (a)?arrow_forward
- . Case: Flamingo Educational Services Flamingo Educational Services, a company located in the Tema metropolis, is a nationwide market leader in the publishing and distribution of textbooks for first and second cycle schools. Somehow, Flamingo does not use forecasts for production planning. Instead, the operations manager decides which books to produce and the batch size, based on orders and the amounts in inventory. The books that have the fewest amounts in inventory get the highest priority. Demand is uneven, and the company has experienced being overstocked on some items and out of others. Being under-stocked has occasionally created tensions with managers of the retail bookstores the company works with. Flamingo is on the verge of losing a lucrative contract with the Ghana Education Service over a complaint that the books produced over the last four months have defective binding as well as slight but noticeable variations in print quality and sizes of the…arrow_forward1. Foxie Owl’s Besty Bagel shop makes fresh bagels. She has to buy raw materials fresh every day for selling on that day. She wants to know exactly how much should she spend on raw materials. Foxie did some analysis over the past month and came back with the following numbers: Daily demand was equally likely to be 200, 225, 250, 275, or 300 bagels. What should be the number of bagels on hand to satisfy a Fill Rate requirement of 96%, rounded to next integer value? Group of answer choices 300 275 286 263 2. Suppose that instead of a discrete demand distribution, Foxie’s shop determines that the daily demand for bagels is normally distributed, with a mean of 250 and a standard deviation of 35. Foxie still wants a Fill Rate of 98%. What is the appropriate level of on-hand inventory for Foxie’s shop? Group of answer choices 263 274 257 270arrow_forwardNozone, Inc., a manufacturer of Freon recovery units (for automotive air conditioner maintenance), experiences a strongly seasonal demand pattern, driven by the summer air conditioning season. This year Nozone has put together a six-month production plan, where the monthly demands D, for recovery units are given in the table below. Each recovery unit is manufactured from one chassis assembly plus a variety of other parts. The chassis assemblies are produced in the machining center. Since there is a single chassis assembly per recovery unit, the demands in the table below also represent demands for chassis assemblies. The unit cost, fixed setup cost and monthly holding cost for chassis assemblies are also given in this table. The fixed setup cost is the firm's estimate of the cost to changeover the machining center to produce chassis assemblies, including labor and materials cost and the cost of disruption of other product lines. t D₁ C₁ A₁ h₂ 1 1,000 50 2,000 1 2 1,200 50 2,000 1 3 500…arrow_forward
- A small company produces recreational vehicles. The (in units): Mar Apr May Jun Jul Aug Sep 50 Total Month 359 Forecast 55 60 60 40 50 44 Use the following information: Regular labour cost $240 per unit Overtime labour cost $360 per unit Regular capacity 40 units per month, using 5 workers Overtime capacity 8 units per month Holding cost $30 per unit per month Back-order cost $100 per unit per month Beginning inventory Desired ending inventory 0 Hiring cost $2,000 per worker Develop the minimum cost production plan and compute its total cost.arrow_forwardThe table below contains monthly (six months) demand estimates and working days per month. Month Demand Production Days JAN 1,500 20 FEB 1,200 24 MAR 1,000 25 APR 1,600 25 MAY 1,100 20 JUN 1,300 26 For the implementation of “Level” strategy, the average demand (in units/day) over the six- month planning horizon is equal to; a. 40 b. 50 c. 55 d. 75arrow_forwardTuff-Rider, Inc., manufactures touring bikes and mountain bikes in a variety of frame sizes, colors, and component combinations. Identical bicycles are produced in lots of 110. The projected demand, lot size, and time standards are shown in the following table: i Item Demand forecast Lot size Standard processing time Standard setup time Touring 4,000 units/year 130 units 0.20 hour/unit 2 hours/lot Mountain 10,000 units/year 110 units 0.50 hour/unit 3 hours/lot The shop currently works 8 hours a day, 5 days a week, 48 weeks a year. It operates five workstations, each producing one bicycle in the time shown in the table. The shop maintains a 15 percent capacity cushion. How many workstations will be required next year to meet expected demand without using overtime and without decreasing the firm's current capacity cushion? The number of workstations required next year is. (Enter your response rounded up to the next whole number.)arrow_forward
- Practical Management ScienceOperations ManagementISBN:9781337406659Author:WINSTON, Wayne L.Publisher:Cengage,Operations ManagementOperations ManagementISBN:9781259667473Author:William J StevensonPublisher:McGraw-Hill EducationOperations and Supply Chain Management (Mcgraw-hi...Operations ManagementISBN:9781259666100Author:F. Robert Jacobs, Richard B ChasePublisher:McGraw-Hill Education
- Purchasing and Supply Chain ManagementOperations ManagementISBN:9781285869681Author:Robert M. Monczka, Robert B. Handfield, Larry C. Giunipero, James L. PattersonPublisher:Cengage LearningProduction and Operations Analysis, Seventh Editi...Operations ManagementISBN:9781478623069Author:Steven Nahmias, Tava Lennon OlsenPublisher:Waveland Press, Inc.
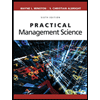
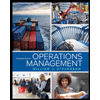
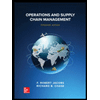
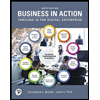
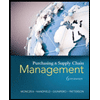
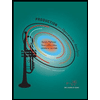