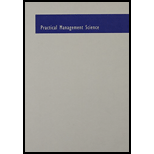
Practical Management Science, Loose-leaf Version
5th Edition
ISBN: 9781305631540
Author: WINSTON, Wayne L.; Albright, S. Christian
Publisher: Cengage Learning
expand_more
expand_more
format_list_bulleted
Concept explainers
Question
Chapter 12, Problem 35P
Summary Introduction
To determine: The optimal ordering policy and the maximum shortage that will occur.
Inventory and supply chain models:
The functions of inventory and supply chain are one of the most important business decision areas for an organization. The first important aspect of these concepts is to have adequate inventory on hand. The second important aspect is to carry a little amount of inventory as possible.
Expert Solution & Answer

Want to see the full answer?
Check out a sample textbook solution
Students have asked these similar questions
The Bosch factory in New Bern, NC uses dishwasher motors at a steady rate of 17308 units per year. Bosch procures
these units from a supplier at a purchase cost of $58 per unit. Bosch receives an order 26 days after it is placed.
Regardless of the number of units ordered, Bosch incurs a fixed cost of $2988 for placing, shipping, and receiving the
order. The holding cost per unit per year is 30% of the purchase cost per unit. Assume Bosch operates 364 days, 52
weeks, or 12 months per year.
Calculate the average time a unit spends in inventory between orders in DAYS for the optimal order quantity from the
problem above.
Rounding instructions
• Carry your calculations to at least 3 decimal places.
• Enter your answer rounded to one decimal place (nearest tenth).
A Mercedes dealer purchases vehicles for $20,000. The annual holding cost is estimated to be 25% of the dollar value of inventory. The dealer sells an average of 500 cars per year. He believes that demand is backlogged, but estimates that if he is short one car for one year, he will lose $20,000 in future profits. Each time the dealer places an order for cars, the ordering cost amounts to $10,000.
Determine the Mercedes dealer's optimal (?,?) ordering policy.
The purchasing manager for the Atlantic Steel Company must determine a policy for orderingcoal to operate 12 converters. Each converter requires exactly 5 tons of coal per day to operate,and the firm operates 360 days per year. The purchasing manager has determined that the orderingcost is $80 per order and the cost of holding coal is 20% of the average dollar value of inventoryheld. The purchasing manager has negotiated a contract to obtain the coal for $12 per ton forthe coming year. If 5 days of lead time are required to receive an order of coal, how much coal should be on hand when an order is placed?
Chapter 12 Solutions
Practical Management Science, Loose-leaf Version
Ch. 12.4 - Prob. 1PCh. 12.4 - Prob. 2PCh. 12.4 - Prob. 3PCh. 12.4 - Prob. 4PCh. 12.4 - Prob. 5PCh. 12.4 - Prob. 6PCh. 12.4 - Prob. 7PCh. 12.4 - Prob. 8PCh. 12.4 - Prob. 9PCh. 12.4 - Prob. 10P
Ch. 12.4 - Prob. 11PCh. 12.5 - Prob. 12PCh. 12.5 - Prob. 13PCh. 12.5 - Prob. 14PCh. 12.5 - Prob. 15PCh. 12.5 - Prob. 16PCh. 12.5 - Prob. 17PCh. 12.5 - Prob. 18PCh. 12.5 - Prob. 19PCh. 12.5 - Prob. 20PCh. 12.5 - Prob. 21PCh. 12 - Prob. 27PCh. 12 - Prob. 28PCh. 12 - Prob. 29PCh. 12 - Prob. 30PCh. 12 - Prob. 31PCh. 12 - Prob. 32PCh. 12 - Prob. 33PCh. 12 - Prob. 34PCh. 12 - Prob. 35PCh. 12 - Prob. 36PCh. 12 - Prob. 38PCh. 12 - Prob. 39PCh. 12 - Prob. 40PCh. 12 - Prob. 42PCh. 12 - Prob. 43PCh. 12 - Prob. 44PCh. 12 - Prob. 45PCh. 12 - Prob. 46PCh. 12 - Prob. 47PCh. 12 - Prob. 48PCh. 12 - Prob. 49PCh. 12 - Prob. 53PCh. 12 - Prob. 54PCh. 12 - In terms of K, D, and h, what is the average...Ch. 12 - Prob. 56PCh. 12 - Prob. 57PCh. 12 - Prob. 58PCh. 12 - Prob. 59PCh. 12 - Prob. 60PCh. 12 - Prob. 61PCh. 12 - Prob. 62PCh. 12 - Prob. 63PCh. 12 - Prob. 64PCh. 12 - Prob. 65PCh. 12 - Prob. 66PCh. 12 - Prob. 67PCh. 12 - Prob. 68PCh. 12 - Prob. 69PCh. 12 - Prob. 70PCh. 12 - Prob. 71PCh. 12 - Prob. 1.1CCh. 12 - Prob. 1.2CCh. 12 - Prob. 1.3C
Knowledge Booster
Learn more about
Need a deep-dive on the concept behind this application? Look no further. Learn more about this topic, operations-management and related others by exploring similar questions and additional content below.Similar questions
- The purchasing manager for the Atlantic Steel Company must determine a policy for orderingcoal to operate 12 converters. Each converter requires exactly 5 tons of coal per day to operate,and the firm operates 360 days per year. The purchasing manager has determined that the orderingcost is $80 per order and the cost of holding coal is 20% of the average dollar value of inventoryheld. The purchasing manager has negotiated a contract to obtain the coal for $12 per ton forthe coming year. Determine the total inventory-related costs associated with the optimal ordering policy (do not include the cost of the coal).arrow_forwardThe purchasing manager for the Atlantic Steel Company must determine a policy for orderingcoal to operate 12 converters. Each converter requires exactly 5 tons of coal per day to operate,and the firm operates 360 days per year. The purchasing manager has determined that the orderingcost is $80 per order and the cost of holding coal is 20% of the average dollar value of inventoryheld. The purchasing manager has negotiated a contract to obtain the coal for $12 per ton forthe coming year. Determine the optimal quantity of coal to receive in each order.arrow_forwardA Mercedes dealer pays $40,000 for each car purchased (wholesale price). The annual holding cost is estimated to be 30% of the dollar value of inventory. The dealer sells an average of 1200 cars per year. They believe that demand is backlogged but estimate that if they are short one car for one year, the loss in future profits is about 10% of the wholesale price. Each time the dealer places an order for cars, ordering costs amount to $1600. Assume there are 360 work days per year. Question: What percent of the time do shortages occur? I've deduced the percent of shortage time to be 25%, but am not sure I've set up my formulas correctly.arrow_forward
- A Mercedes dealer purchases vehicles for $20,000. The annual holding cost is estimated to be 25% of the dollar value of inventory. The dealer sells an average of 500 cars per year. He believes that demand is backlogged, but estimates that if he is short one car for one year, he will lose $20,000 in future profits. Each time the dealer places an order for cars, the ordering cost amounts to $10,000. What is the (s, Q) ordering policy that results in a 90% CSL?arrow_forwardA Mercedes dealer pays $40,000 for each car purchased (wholesale price). The annual holding cost is estimated to be 30% of the dollar value of inventory. The dealer sells an average of 1200 cars per year. They believe that demand is backlogged but estimate that if they are short one car for one year, the loss in future profits is about 10% of the wholesale price. Each time the dealer places an order for cars, ordering costs amount to $1600. Assume there are 360 work days per year. Question: If the Mercedes dealer wants to limit backorders so that they occur 20% of the time, what is the maximum number of backorders that should be allowed (assuming the optimal order quantity doesn't change)?arrow_forwardA retailer has two stores selling the same product. Weekly demand at store 1 is normally distributed with a mean of 100 and a standard deviation of 10, while weekly demand at store 2 is normally distributed with a mean of 150 and a standard deviation of 25. Demand at the two stores is independent. The retailer orders from a supplier with a 1 week lead time using a periodic review policy with a review period of 1 week, and targets a 95% service level. If the retailer wants to centralize inventory across the two stores, i.e., hold just one stock of inventory to serve demand from both stores, what should the order-up-to level be? PLEASE SHOW CALCULATIONarrow_forward
- Consider the following single-period inventory model (probabilistic demand). The Smith shoe company is currently selling an athletic shoe for the spring and summer months. It does not expect to sell any shoes in the fall, thus it will not sell after July 31. The shoes cost Smith $110 per pair and Smith will sell them retail at a price of $140. During the August sale, the shoes will sell for $70 a pair. The demand for shoes is assumed to be uniformly distributed with the range of demand going from 2,000 pairs to 3,800 pairs. Answer these questions Question 7. What is the value of co? (b) (a) Question 8. What is the value of cu?arrow_forwardA company incurs an ordering cost of $232 each time it places an order, regardless of the order size. The item's cost is $5, and the annual carrying charge for the item is 30%. If the annual demand for this item is 2,880 and the company's order quantity (Q) is 944, calculate its total annualized cost of inventory. The total annualized inventory costs are $.arrow_forwardA restaurant uses 5,000 quart bottles of ketchup each year. The ketchup costs $3.00 per bottle and is served only in whole bottles because its taste quickly deteriorates. The restaurant figures that it costs $10.00 each time an order is placed, and holding costs are 20 percent of the purchase price. It takes 3 weeks for an order to arrive. The restaurant operates 50 weeks per year. The restaurant would like to use an inventory system that minimizes inventory cost. The restaurant has figured that the most economical order size or EOQ is approx. 409 (rounding up the decimals). Suppose that things have become uncertain and that customer demand is no more constant. Customer demand is now normally distributed with mean being the same as given in the problem description and standard deviation = 30 units per week. The supply source is still very reliable and as a result the lead time is constant. Find out the safety stock needed to achieve 95% customer service level. O 55 65 075 85 None of…arrow_forward
- I need a detailed explanation on how to solve this problem: A paint shop implements an inventory policy on its stock of white paint, which costs the store $6 per can. Monthly demand for cans of white paint is normal with mean 28 and standard deviation 8. The replenishment lead time is 14 weeks. Excess demand is backordered, but costs $10 per back ordered can in labor and loss of goodwill. There is a fixed cost of $15 per order, and the holding cost is based on 30% interest rate per annum. In your computations, assume 4 weeks per month. - Write down the model name and parameters. - What are the optimal lot size and reorder points for white paint (include the formulas)? - What is the optimal safety stock (include the formula)? *** Suppose the paint shop from the above problem adopts a service level policy. - What are the optimal lot size and reorder points for white paint, such that 90% of the cycles are filled without backordering (include all formulas)? - What is the fill rate…arrow_forwardSuppose that the owner of the campus bar, Nick’s, has determined that demand for beer during leadtime averages 5000 bottles. Nick, the owner, believes the demand during lead time can be describedby a normal distribution with a mean of 5000 bottles and a standard deviation of 300 bottles. Nick iswilling to accept a stockout risk of approximately 4 percent. Determine the appropriate z value to use.Calculate how much safety stock Nick should hold. Also determine the reorder point.arrow_forwardChris usually sells 120 copies of newspaper each day and believe that sale are normally distributed, with a standard deviation of 15 papers. He pays 70 cents for each paper, which sells $1.25. For each unsold paper, he receives 30-cent credit. a) determine how many papers he should order each day b) calculate the stockout risk for that quantity.arrow_forward
arrow_back_ios
SEE MORE QUESTIONS
arrow_forward_ios
Recommended textbooks for you
- Practical Management ScienceOperations ManagementISBN:9781337406659Author:WINSTON, Wayne L.Publisher:Cengage,
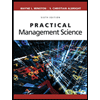
Practical Management Science
Operations Management
ISBN:9781337406659
Author:WINSTON, Wayne L.
Publisher:Cengage,
Inventory Management | Concepts, Examples and Solved Problems; Author: Dr. Bharatendra Rai;https://www.youtube.com/watch?v=2n9NLZTIlz8;License: Standard YouTube License, CC-BY