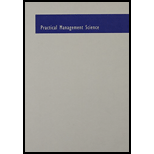
Practical Management Science, Loose-leaf Version
5th Edition
ISBN: 9781305631540
Author: WINSTON, Wayne L.; Albright, S. Christian
Publisher: Cengage Learning
expand_more
expand_more
format_list_bulleted
Concept explainers
Question
Chapter 12, Problem 63P
a)
Summary Introduction
To determine: The extra holding cost incurred by adding ‘Q’ units.
Inventory and supply chain models:
The functions of inventory and supply chain are one of the most important business decision areas for an organization. The first important aspect of these concepts is to have adequate inventory on hand. The second important aspect is to carry a little amount of inventory as possible.
b)
Summary Introduction
To determine: The save in purchase costs by ordering ‘Q’ units.
c)
Summary Introduction
To determine: The value of ‘Q’ maximizing the purchase cost saving less the extra holding costs.
d)
Summary Introduction
To determine: The order size should be made by the company before the price increases go into the effect.
Expert Solution & Answer

Want to see the full answer?
Check out a sample textbook solution
Students have asked these similar questions
The best quantity to order One of the formulas for inventorymanagement says that the average weekly cost of ordering, payingfor, and holding merchandise iswhere q is the quantity you order when things run low (shoes,TVs, brooms, or whatever the item might be); k is the cost ofplacing an order (the same, no matter how often you order); c isthe cost of one item (a constant); m is the number of items soldeach week (a constant); and h is the weekly holding cost per item(a constant that takes into account things such as space, utilities,insurance, and security). Find dA>dq and d2A>dq2.
Red Corporation uses the reorder point modelto plan its purchases. It sellsitssole productat the following daily amounts:Minimum=30,000; Average=40,000;Maximum=60,000. Its supplier takes 3 dayson average and 4 days maximum to deliverthe order. The-reorder point would be
A. 240,000B. 160,000C. 120,000D. 90,000
Torrance Refinery produces approximately 23.1 Million barrels of gasoline per
year. A California distributor sources its gasoline from the Torrance refinery.
The annual demand for gasoline at the California distributor is 5.3 Million
barrels. The cost of storing gasoline is approximately $29 per barrel (per year).
The cost of placing an order to the Torrance refinery (including shipping) is
$7300 per order. Orders will be received gradually instead of delivered all at
once (hence EPQ).
At what quantity will the total cost of procurement be the lowest?
Round your answer to the nearest whole number. Do NOT include a comma.
For example, answer like 103542 and NOT 103,542
Answer: 58845
Check
Chapter 12 Solutions
Practical Management Science, Loose-leaf Version
Ch. 12.4 - Prob. 1PCh. 12.4 - Prob. 2PCh. 12.4 - Prob. 3PCh. 12.4 - Prob. 4PCh. 12.4 - Prob. 5PCh. 12.4 - Prob. 6PCh. 12.4 - Prob. 7PCh. 12.4 - Prob. 8PCh. 12.4 - Prob. 9PCh. 12.4 - Prob. 10P
Ch. 12.4 - Prob. 11PCh. 12.5 - Prob. 12PCh. 12.5 - Prob. 13PCh. 12.5 - Prob. 14PCh. 12.5 - Prob. 15PCh. 12.5 - Prob. 16PCh. 12.5 - Prob. 17PCh. 12.5 - Prob. 18PCh. 12.5 - Prob. 19PCh. 12.5 - Prob. 20PCh. 12.5 - Prob. 21PCh. 12 - Prob. 27PCh. 12 - Prob. 28PCh. 12 - Prob. 29PCh. 12 - Prob. 30PCh. 12 - Prob. 31PCh. 12 - Prob. 32PCh. 12 - Prob. 33PCh. 12 - Prob. 34PCh. 12 - Prob. 35PCh. 12 - Prob. 36PCh. 12 - Prob. 38PCh. 12 - Prob. 39PCh. 12 - Prob. 40PCh. 12 - Prob. 42PCh. 12 - Prob. 43PCh. 12 - Prob. 44PCh. 12 - Prob. 45PCh. 12 - Prob. 46PCh. 12 - Prob. 47PCh. 12 - Prob. 48PCh. 12 - Prob. 49PCh. 12 - Prob. 53PCh. 12 - Prob. 54PCh. 12 - In terms of K, D, and h, what is the average...Ch. 12 - Prob. 56PCh. 12 - Prob. 57PCh. 12 - Prob. 58PCh. 12 - Prob. 59PCh. 12 - Prob. 60PCh. 12 - Prob. 61PCh. 12 - Prob. 62PCh. 12 - Prob. 63PCh. 12 - Prob. 64PCh. 12 - Prob. 65PCh. 12 - Prob. 66PCh. 12 - Prob. 67PCh. 12 - Prob. 68PCh. 12 - Prob. 69PCh. 12 - Prob. 70PCh. 12 - Prob. 71PCh. 12 - Prob. 1.1CCh. 12 - Prob. 1.2CCh. 12 - Prob. 1.3C
Knowledge Booster
Learn more about
Need a deep-dive on the concept behind this application? Look no further. Learn more about this topic, operations-management and related others by exploring similar questions and additional content below.Similar questions
- Assume the demand for a companys drug Wozac during the current year is 50,000, and assume demand will grow at 5% a year. If the company builds a plant that can produce x units of Wozac per year, it will cost 16x. Each unit of Wozac is sold for 3. Each unit of Wozac produced incurs a variable production cost of 0.20. It costs 0.40 per year to operate a unit of capacity. Determine how large a Wozac plant the company should build to maximize its expected profit over the next 10 years.arrow_forwarda supermarket expects to sell 1000 boxes of sugar in a year. each box costs $2 and there is a fixed delivery charge of $20 per order. if it costs $1 to store a box for a year, what is the order size and how many times a year should orders be placed to minimize inventory costs?arrow_forwardModels of inventory systems frequently consider the relationships among a beginning inventory,a production quantity, a demand or sales, and an ending inventory. For a givenproduction period j, letsj-1 = ending inventory from the previous period (beginning inventory for period j)xj = production quantity in period jdj = demand in period jsj = ending inventory for period ja. Write the mathematical relationship or model that shows ending inventory as a functionof beginning inventory, production, and demand.b. What constraint should be added if production capacity for period j is given by Cj?c. What constraint should be added if inventory requirements for period j mandate anending inventory of at least Ij?arrow_forward
- Mamma Temte bakes six pies a day that cost $2 each to produce. On 31% of the days she sells only two pies. On 39% of the days, she sells 4 pies, and on the remaining 30% of the days, she sells all six pies. If Mama Temte sells her pies for $5 each, what is her expected profit for a dayʹs worth of pies? [Assume that any leftover pies are given away.]arrow_forwardAn electronics retailer wants to develop an inventory policy to achieve 99% chance of not getting stockouts for a chip. The daily demand for the chip is estimated to be Normal with mean 200 and standard deviation of 20. They count the chip inventory every 2 weeks to place an order, and it takes 11 days for the ordered chips to be delivered. The retailer operates 7 days a week, 365 days a year. They are going to implement an order-up-to model. A) What base stock level should they choose? B) What is the number of chips they would have on order (on average)? C) When they checked their inventory of chips to place a new order, they found that they ran out of stock completely. In addition, they have 10 chips on way to be delivered, while there are five customers who paid for 20 chips in total and are waiting to receive their chips. How many chips should the retailer order?arrow_forwardTyrelle's T-shirts purchases shirts for $4. If a markup of $5 per shirt is applied, the selling price for each shirt is $9. True Falsearrow_forward
- A retailer determines that the cost of ordering and storing units of a product can be modelled by C(x)= 3x + 2000 / x, 0 < x < 200. Find the order size that will minimise ordering and storage cost.arrow_forwardThe economic order quantity of Geo Co. is determined to be 450 units and it sells its only product for P5 each. Every time the company orders, it incurs P50. Holding cost is P10. It takes 3 days to make and receive an order. How much sales should Geo Co. for this economic order quantity to be plausible? (Using 360 day per year)arrow_forwardA customer buys 1 ABC Jan 35 put for a premium of $3 and simultaneously buys 100 shares of ABC stock for $35 per share. The customer will break even when the stock is selling for what price per share at expiration?arrow_forward
- A restaurant uses 100 per week or 5,000 quart bottles of ketchup each year. The ketchup costs $3.00 per bottle and is served only in whole bottles because its taste quickly deteriorates. The restaurant figures that it costs $10.00 each time an order is placed, and holding costs are 20 percent of the purchase price. It takes 3 weeks for an order to arrive. The restaurant operates 50 weeks per year. The restaurant would like to use an inventory system that minimizes inventory cost. The restaurant has figured that the most economical order size or EOQ is approx. 409 (rounding up the decimals). Approximately, what is the time between two orders (in terms of weeks) 08 06 04 02 None of the abovearrow_forwardConsider two products A and B that have identical cost, retail price and demand parameters and the same short selling season. The newsvendor model is used to manage inventory for both products. Product A is to be discontinued at the end of the season this year, and the leftovers will be salvaged at 65% of the cost. Product B will be re-offered next summer, so any leftovers this year can be carried over to the next year while incurring a holding cost on each leftover unit equal to 20% of the product's cost. How do the stocking quantities for these products compare? Multiple Choice Stocking quantity of product A is higher. Stocking quantity of product B is higher. The answer cannot be determined from the data provided. Stocking quantities are equal.arrow_forwardChris usually sells 120 copies of newspaper each day and believe that sale are normally distributed, with a standard deviation of 15 papers. He pays 70 cents for each paper, which sells $1.25. For each unsold paper, he receives 30-cent credit. a) determine how many papers he should order each day b) calculate the stockout risk for that quantity.arrow_forward
arrow_back_ios
SEE MORE QUESTIONS
arrow_forward_ios
Recommended textbooks for you
- Practical Management ScienceOperations ManagementISBN:9781337406659Author:WINSTON, Wayne L.Publisher:Cengage,
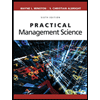
Practical Management Science
Operations Management
ISBN:9781337406659
Author:WINSTON, Wayne L.
Publisher:Cengage,