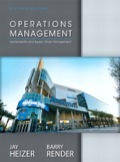
EBK OPERATIONS MANAGEMENT
11th Edition
ISBN: 8220103630726
Author: RENDER
Publisher: PEARSON
expand_more
expand_more
format_list_bulleted
Concept explainers
Question
Chapter 13, Problem 10DQ
Summary Introduction
To determine: Thedifference between aggregate planning in service and aggregate planning in manufacturing
Introduction: The aggregate plan is the output of sales and operations planning. The major concern of aggregate planning is the production time and quantity for the intermediate future. Aggregate planning would encompass a time prospect of approximately 3 to 18 months.
Expert Solution & Answer

Want to see the full answer?
Check out a sample textbook solution
Students have asked these similar questions
Question 4) APP Linear Programming
Given the following information:
Quarter Demand
Regular Prod. Capacity = 3,000 units/gt
8,000 Overtime Prod. Capacity = 800 units/gtg
4,000 Subcontracting Capacity = 1,800 units/gt
Regular Prod. Cost = $20/unit
Overtime Prod. Cost = $25/unit
1
2
2,000 Inventory Capacity
= 6,000 untis/atr
Subcontracting Cost = $35/unit
Inventory Cost
3
Beginning Inventory
= 500 units
= $4/unit/gtr
Linear programming is to be used to determine a production plan strategy of Level Production,
Overtime, and Subcontracting.
a. Formulate the Objective Function (note that there are 3 quarters).
b. Formulate all Constraints (standardized).
c. How many decision variables are in the model?
d. How many constraints are in the model? (do not include non-negativity constraints)
QUESTION 1
A master production schedule shows the following information
MPS
Week
Week
Week
Week
Beginning inventory =
300
31
Forecast
1.000
1,200
1,300
1.200
800
700
Actual customer orders
Projected on-hand
inventory
Available to promise
800
1,000
MPS
Based on the information in the MPS, what is the amount that is available to promise in week 4?
O a. 1,200
Ob.700
Oc. 1.500
O d. 500
Question 3
Regular output capacity is 130 units per month. Regular cost per unit = K600. Overtime cost per unit =
K900. Beginning inventory is 0 units. We have the forecast of engine demand shown below:
a) Develop a chase plan that matches the forecast. Calculate the cost of the plan.
b) Develop a level plan that uses inventory to absorb fluctuations. Compare the costs of the level
plan to the costs of the chase plan from Part (a). Inventory carrying cost per unit per month = 20.
Backlog cost per unit per month = K900. There should be no backlog in the final month.
Month
Forecast
1
120
2
135
3
140
4
120
5
125
6
125
7
140
8 Total
135
1,040
Chapter 13 Solutions
EBK OPERATIONS MANAGEMENT
Ch. 13 - Prob. 1DQCh. 13 - Why are SOP teams typically cross-functional?Ch. 13 - Prob. 3DQCh. 13 - Prob. 4DQCh. 13 - Prob. 5DQCh. 13 - Prob. 6DQCh. 13 - Question: 7. What is level scheduling? What is the...Ch. 13 - Question: 8. Define mixed strategy. Why would a...Ch. 13 - Prob. 9DQCh. 13 - Prob. 10DQ
Ch. 13 - Question: 11. What is the relationship between the...Ch. 13 - Prob. 12DQCh. 13 - Question: 13. What are major limitations of using...Ch. 13 - Prob. 14DQCh. 13 - Question: 13.1 Prepare a graph of the monthly...Ch. 13 - Prob. 2PCh. 13 - The president of Hill Enterprises, Terri Hill,...Ch. 13 - Prob. 4PCh. 13 - Prob. 5PCh. 13 - Prob. 6PCh. 13 - Prob. 7PCh. 13 - Prob. 8PCh. 13 - Prob. 9PCh. 13 - Question: 13.10 The SOP team (see Problem 13.9)...Ch. 13 - Prob. 11PCh. 13 - Prob. 12PCh. 13 - Prob. 13PCh. 13 - Question: 13.14 Jerusalem Medical Ltd., an...Ch. 13 - Prob. 15PCh. 13 - Prob. 16PCh. 13 - Prob. 17PCh. 13 - Question: 13.18 Jose Martinez of El Paso has...Ch. 13 - Prob. 19PCh. 13 - Prob. 20PCh. 13 - Prob. 21PCh. 13 - Prob. 22PCh. 13 - Prob. 1CSCh. 13 - Prob. 2CSCh. 13 - Prob. 1VCCh. 13 - Prob. 2VCCh. 13 - Question: 3. What are some concerns the team needs...
Knowledge Booster
Learn more about
Need a deep-dive on the concept behind this application? Look no further. Learn more about this topic, operations-management and related others by exploring similar questions and additional content below.Similar questions
- Question 4 b) Company ABC wishes to evaluate whether to produce a component internally or purchase from a vendor. The firm has the following options: Internal Production Process 1 Process 2 Purchase from Vendor Vendor 1 Vendor 2 Vendor 3 Variable cost of $17 per unit; annual fixed cost of $200,000 Variable cost of $14 per unit; annual fixed cost of $240,000 Offers a price of $20 per unit for any volume up to 30,000 units Offers a price of $22 per unit for 1,000 units or less, and $18 per unit for large quantities Offers a price of $21 per unit for the first 1,000 units and $19 per unit for additional units If the annual demand is 10,000 units, which alternative would be best from a cost standpoint? For 20,000 units, which alternative would be best?arrow_forwardQuestion 3 List any five (5) costs prevalent in aggregate planning in the motor car industry.arrow_forwardQuestion 3 Regular output capacity is 130 units per month. Regular cost per unit = K600. Overtime cost per unit K900. Beginning inventory is 0 units. We have the forecast of engine demand shown below: a) Develop a chase plan that matches the forecast. Calculate the cost of the plan. b) Develop a level plan that uses inventory to absorb fluctuations. Compare the costs of the level plan to the costs of the chase plan from Part (a). Inventory carrying cost per unit per month = 20. Backlog cost per unit per month = K900. There should be no backlog in the final month. Month Forecast 1 120 2 3 135 140 4 120 End of assignment 1 5 125 6 125 7 140 = 8 135 Total 1,040arrow_forward
- Question 1. Hoverboards and the Factory Market Area: Suppose there is a single shoe factory in the region. The factory competes with homemade shoes and will sell shoes to any household for which the net price of factory shoes is less than the cost of homemade shoes. The cost of a homemade shoe is the opportunity cost of the time required to make the shoe at home, that is, the one gallon of milk that could be produced instead. Suppose the higher cost of living and commuting requires compensation of 0.80 gallons of milk per hour. Each worker produces 10 shoes per hour, so the average labor and capital cost are 0.18 gallons of milk and 0.12 gallons of milk respectively. The factory price of shoe (equal to the average production cost, sum of the average labor cost and the average capital cost) is 0.30 gallons of milk. A round-trip mile involves one mile of travel to a location and one mile back, for a total distance of two miles. Linear travel cost 20 miles /hour. Therefore, the…arrow_forwardQuestion 4.4 Montreal Hardware Co. is making a make-or-buy decision. The market feedback shows that the optimal price for this item is $10 each. If the item is outsourced to Laval Hardware Co, there is virtually no cost other than the $6 per unit that they would pay Laval Hardware Co. Internally, they have two choices. Process A requires an investment of $120,000 for design and equipment, but it results in a $4 per unit cost. Process B requires only a $100,000 investment, but its per unit cost is $5. Regardless of whether the item is subcontracted or produced internally, there is a 50% chance that they will sell 50,000 units, and a 50% chance that they will sell 100,000 units. Draw the decision tree appropriate to the alternatives and outcomes stated. Using the decision tree and EMV, what is their best choice?arrow_forwardQuestion 4 An alternative will have fixed costs of $10,000 per month, variable costs of $50 per unit, and revenue of $70 per unit. The break-even point volume is:arrow_forward
- question 1 Terminator, Inc., manufactures a motorcycle part in lots of 250 units. The raw materials cost for the part is $150, and the value added in manufacturing 1 unit from its components is $280, for a total cost per completed unit of $430. The lead time to make the part is 3 weeks, and the annual demand is 4,200 units. Assume 50 working weeks per year. a. How many units of the part are held, on average, as cycle inventory? nothing units. (Enter your response as an integer.) What is its value? $_______.(Enter your response as an integer.) b. How many units of the part are held, on average, as pipeline inventory? nothing units. (Enter your response as an integer.) What is its value? $________________ (Enter your response as an integer.)arrow_forwardQuestion 5 Terminator, Inc., manufactures a motorcycle part in lots of 150 units. The raw materials cost for the part is $150, and the value added in manufacturing 1 unit from its components is $320, for a total cost per completed unit of $470. The lead time to make the part is 2 weeks, and the annual demand is 3,800 units. Assume 50 working weeks per year. a. How many units of the part are held, on average, as cycle inventory? __________________ units. (Enter your response as an integer.) What is its value? $___________________ (Enter your response as an integer.) b. How many units of the part are held, on average, as pipeline inventory? ________________ units. (Enter your response as an integer.) What is its value? $__________________________ (Enter your response as an integer.)arrow_forwardQUESTION #1 Mrs. Johnson, the owner of a small manufacturing business has patented a new device for kitchen appliance. Before trying to commercialize the device and add it to her existing product line, the she wants reasonable assurance of success. Variable costs are estimated at $8 per unit produced and sold. Fixed costs are about $60,000 per year. a. Forecasted sales for the first year are 15,000 units if the price is reduced to $20. With this pricing strategy, what would be the product's total contribution to profits in the first year? b. If the selling price is set at $30, how many units must be produced and sold to break even? Use both algebraic and graphic approachesarrow_forward
- QUESTION 2 ID11 What is an information system for identifying and planning the enterprise-wide resources needed to take, make, ship, and account for customer orders? BOM MRP CIM ⒸERParrow_forwardProblem 1 The following information applies to the City View Restaurant. May 1 Food inventory value: $73,480 bnl de May 31 Food inventory value: $77,550 bonen Cost of food used during May $386,410 1. What is the inventory turnover rate for food products for the City View Restaurant? 2. What does the answer (inventory turnover ratio) in question 1 mean?arrow_forwardQUESTION 9 Consider a SKU with 276 picks forecasted during the planning horizon and an annual flow of 2000 ft. Suppose that: • the cost of picking from the forward fast-pick area is 1 minute per pick • the cost of picking from the reserve area is 4 minutes per pick • the cost of restocking the fast-pick area from reserve is 5 minutes per restock What is the labor efficiency of this SKU? Provide your answer to the nearest single decimal point.arrow_forward
arrow_back_ios
SEE MORE QUESTIONS
arrow_forward_ios
Recommended textbooks for you
- Practical Management ScienceOperations ManagementISBN:9781337406659Author:WINSTON, Wayne L.Publisher:Cengage,Operations ManagementOperations ManagementISBN:9781259667473Author:William J StevensonPublisher:McGraw-Hill EducationOperations and Supply Chain Management (Mcgraw-hi...Operations ManagementISBN:9781259666100Author:F. Robert Jacobs, Richard B ChasePublisher:McGraw-Hill Education
- Purchasing and Supply Chain ManagementOperations ManagementISBN:9781285869681Author:Robert M. Monczka, Robert B. Handfield, Larry C. Giunipero, James L. PattersonPublisher:Cengage LearningProduction and Operations Analysis, Seventh Editi...Operations ManagementISBN:9781478623069Author:Steven Nahmias, Tava Lennon OlsenPublisher:Waveland Press, Inc.
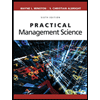
Practical Management Science
Operations Management
ISBN:9781337406659
Author:WINSTON, Wayne L.
Publisher:Cengage,
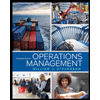
Operations Management
Operations Management
ISBN:9781259667473
Author:William J Stevenson
Publisher:McGraw-Hill Education
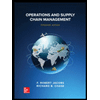
Operations and Supply Chain Management (Mcgraw-hi...
Operations Management
ISBN:9781259666100
Author:F. Robert Jacobs, Richard B Chase
Publisher:McGraw-Hill Education
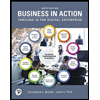
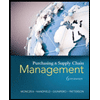
Purchasing and Supply Chain Management
Operations Management
ISBN:9781285869681
Author:Robert M. Monczka, Robert B. Handfield, Larry C. Giunipero, James L. Patterson
Publisher:Cengage Learning
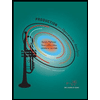
Production and Operations Analysis, Seventh Editi...
Operations Management
ISBN:9781478623069
Author:Steven Nahmias, Tava Lennon Olsen
Publisher:Waveland Press, Inc.