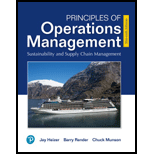
Concept explainers
Using the data for the coffee table in Problem 14.31, build a labor

To determine: The number of labor hours and employees needed each day.
Explanation of Solution
Given information:
- Table requires 1 top, 4 legs, 1/8 gallon of strain, 1/16 gallon of blue, 2 short braces, 2 long braces, and brass cap on the bottom of each leg.
- 100 gallons of glue as inventory.
- All items except brass caps, stain and glue are planned on a Lot for lot basis.
- Caps are purchased in 1000’s, stain and glue by gallon.
- Lead time = 1 (for each item).
- 640 coffee tables needed on day 5 and 6.
- 128 coffee tables needed on days 7 and 8.
- Labor standard for each top is 2 labor hours.
- Each leg with brass cap installation and each pair of braces need ¼ hour.
- Base assembly needs 1 labor hour.
- Final assembly of table requires 2 labor hours.
- Number of hours per day is 8.
Product structure:
Net requirements plan:
Table:
Period (Day) | ||||||||
Table | 1 | 2 | 3 | 4 | 5 | 6 | 7 | 8 |
Gross requirements | 640 | 640 | 128 | 128 | ||||
Scheduled receipt | ||||||||
On hand (0) | 0 | 0 | 0 | 0 | ||||
Net requirement | 640 | 640 | 128 | 128 | ||||
Planned order receipt | 640 | 640 | 128 | 128 | ||||
Planned order release | 640 | 640 | 128 | 128 |
Day 5:
The gross requirement is 640 (1 assembly) of Coffee table derived from the given information. The On hand is 0. Therefore, the net requirement is 640. The lead time is 1 week. The planned order release will be 640 in day 4 which will be the planned order receipt in day 5.
Day 6:
The gross requirement is 640 (1 assembly) of Coffee table derived from the given information. The On hand is 0. Therefore, the net requirement is 640. The lead time is 1 week. The planned order release will be 640 in day 5 which will be the planned order receipt in day 6.
Day 7:
The gross requirement is 128 (1 assembly) of Coffee table derived from the given information. The On hand is 0. Therefore, the net requirement is 128. The lead time is 1 week. The planned order release will be 128 in day 6 which will be the planned order receipt in day 7.
Day 8:
The gross requirement is 128 (1 assembly) of Coffee table derived from the given information. The On hand is 0. Therefore, the net requirement is 128. The lead time is 1 week. The planned order release will be 128 in day 7 which will be the planned order receipt in day 8.
Top:
Period (Day) | ||||||||
Top | 1 | 2 | 3 | 4 | 5 | 6 | 7 | 8 |
Gross requirements | 640 | 640 | 128 | 128 | ||||
Scheduled receipt | ||||||||
On hand (0) | 0 | 0 | 0 | 0 | ||||
Net requirement | 640 | 640 | 128 | 128 | ||||
Planned order receipt | 640 | 640 | 128 | 128 | ||||
Planned order release | 640 | 640 | 128 | 128 |
Day 4:
The gross requirement is 640 (1 assembly) of Top derived from the planned order release of Table. The On hand is 0. Therefore, the net requirement is 640. The lead time is 1 week. The planned order release will be 640 in day 3 which will be the planned order receipt in day 4.
Day 5:
The gross requirement is 640 (1 assembly) of Top derived from the planned order release of Table. The On hand is 0. Therefore, the net requirement is 640. The lead time is 1 week. The planned order release will be 640 in day 4 which will be the planned order receipt in day 5.
Day 6:
The gross requirement is 128 (1 assembly) of Top derived from the planned order release of Table. The On hand is 0. Therefore, the net requirement is 128. The lead time is 1 week. The planned order release will be 128 in day 5 which will be the planned order receipt in day 6.
Day 7:
The gross requirement is 128 (1 assembly) of Top derived from the planned order release of Table. The On hand is 0. Therefore, the net requirement is 128. The lead time is 1 week. The planned order release will be 128 in day 6 which will be the planned order receipt in day 7.
Stain:
Period (Day) | ||||||||
Stain | 1 | 2 | 3 | 4 | 5 | 6 | 7 | 8 |
Gross requirements | 80 | 80 | 16 | 16 | ||||
Scheduled receipt | ||||||||
On hand (0) | 0 | 0 | 0 | 0 | ||||
Net requirement | 80 | 80 | 16 | 16 | ||||
Planned order receipt | 80 | 80 | 16 | 16 | ||||
Planned order release | 80 | 80 | 16 | 16 |
Day 4:
The gross requirement is 80 (1 assembly) of Stain derived from the planned order release of Table. The On hand is 0. Therefore, the net requirement is 80. The lead time is 1 week. The planned order release will be 80 in day 3 which will be the planned order receipt in day 4.
Day 5:
The gross requirement is 80 (1 assembly) of Stain derived from the planned order release of Table. The On hand is 0. Therefore, the net requirement is 80. The lead time is 1 week. The planned order release will be 80 in day 4 which will be the planned order receipt in day 5.
Day 6:
The gross requirement is 16 (1 assembly) of Stain derived from the planned order release of Table. The On hand is 0. Therefore, the net requirement is 16. The lead time is 1 week. The planned order release will be 16 in day 5 which will be the planned order receipt in day 6.
Day 7:
The gross requirement is 16 (1 assembly) of Stain derived from the planned order release of Table. The On hand is 0. Therefore, the net requirement is 16. The lead time is 1 week. The planned order release will be 16 in day 6 which will be the planned order receipt in day 7.
Glue:
Period (Day) | ||||||||
Glue | 1 | 2 | 3 | 4 | 5 | 6 | 7 | 8 |
Gross requirements | 40 | 40 | 8 | 8 | ||||
Scheduled receipt | ||||||||
On hand (100) | 100 | 60 | 20 | 12 | 4 | |||
Net requirement | 0 | 0 | 0 | 0 | ||||
Planned order receipt | ||||||||
Planned order release |
Day 4:
The gross requirement is 40 (1 assembly) of Glue derived from the planned order release of Table. The On hand is 100. Therefore, the net requirement is 0. Therefore there will be no planned order release. The excess inventory 60 will be available at week 5.
Day 5:
The gross requirement is 40 (1 assembly) of Glue derived from the planned order release of Table. The On hand is 60. Therefore, the net requirement is 0. Therefore there will be no planned order release. The excess inventory 20 will be available at week 6.
Day 6:
The gross requirement is 8 (1 assembly) of Glue derived from the planned order release of Table. The On hand is 20. Therefore, the net requirement is 0. Therefore there will be no planned order release. The excess inventory 12 will be available at week 7.
Day 7:
The gross requirement is 8 (1 assembly) of Glue derived from the planned order release of Table. The On hand is 12. Therefore, the net requirement is 0. Therefore there will be no planned order release. The excess inventory 8 will be available at week 8.
Base assembly:
Period (Day) | ||||||||
Base | 1 | 2 | 3 | 4 | 5 | 6 | 7 | 8 |
Gross requirements | 640 | 640 | 128 | 128 | ||||
Scheduled receipt | ||||||||
On hand (0) | 0 | 0 | 0 | 0 | ||||
Net requirement | 640 | 640 | 128 | 128 | ||||
Planned order receipt | 640 | 640 | 128 | 128 | ||||
Planned order release | 640 | 640 | 128 | 128 |
Day 4:
The gross requirement is 640 (1 assembly) of base assembly derived from the planned order release of Table. The On hand is 0. Therefore, the net requirement is 640. The lead time is 1 week. The planned order release will be 640 in day 3 which will be the planned order receipt in day 4.
Day 5:
The gross requirement is 640 (1 assembly) of base assembly derived from the planned order release of Table. The On hand is 0. Therefore, the net requirement is 640. The lead time is 1 week. The planned order release will be 640 in day 4 which will be the planned order receipt in day 5.
Day 6:
The gross requirement is 128 (1 assembly) of base assembly derived from the planned order release of Table. The On hand is 0. Therefore, the net requirement is 128. The lead time is 1 week. The planned order release will be 128 in day 5 which will be the planned order receipt in day 6.
Day 7:
The gross requirement is 128 (1 assembly) of base assembly derived from the planned order release of Table. The On hand is 0. Therefore, the net requirement is 128. The lead time is 1 week. The planned order release will be 128 in day 6 which will be the planned order receipt in day 7.
Short brace:
Period (Day) | ||||||||
Short Brace | 1 | 2 | 3 | 4 | 5 | 6 | 7 | 8 |
Gross requirements | 1,280 | 1,280 | 256 | 256 | ||||
Scheduled receipt | ||||||||
On hand (0) | 0 | 0 | 0 | 0 | ||||
Net requirement | 1,280 | 1,280 | 256 | 256 | ||||
Planned order receipt | 1,280 | 1,280 | 256 | 256 | ||||
Planned order release | 1,280 | 1,280 | 256 | 256 |
Day 3:
The gross requirement is 1,280 (2 assembly) of short brace derived from the planned order release of base assembly. The On hand is 0. Therefore, the net requirement is 1,280. The lead time is 1 week. The planned order release will be 1,280 in day 2 which will be the planned order receipt in day 3.
Day 4:
The gross requirement is 1,280 (2 assembly) of short brace derived from the planned order release of base assembly. The On hand is 0. Therefore, the net requirement is 1,280. The lead time is 1 week. The planned order release will be 1,280 in day 3 which will be the planned order receipt in day 4.
Day 5:
The gross requirement is 256 (2 assembly) of short brace derived from the planned order release of base assembly. The On hand is 0. Therefore, the net requirement is 256. The lead time is 1 week. The planned order release will be 256 in day 4 which will be the planned order receipt in day 5.
Day 6:
The gross requirement is 256 (2 assembly) of short brace derived from the planned order release of base assembly. The On hand is 0. Therefore, the net requirement is 256. The lead time is 1 week. The planned order release will be 256 in day 5 which will be the planned order receipt in day 6.
Long brace:
Period (Day) | ||||||||
Long Brace | 1 | 2 | 3 | 4 | 5 | 6 | 7 | 8 |
Gross requirements | 1,280 | 1,280 | 256 | 256 | ||||
Scheduled receipt | ||||||||
On hand (0) | 0 | 0 | 0 | 0 | ||||
Net requirement | 1,280 | 1,280 | 256 | 256 | ||||
Planned order receipt | 1,280 | 1,280 | 256 | 256 | ||||
Planned order release | 1,280 | 1,280 | 256 | 256 |
Day 3:
The gross requirement is 1,280 (2 assembly) of long brace derived from the planned order release of base assembly. The On hand is 0. Therefore, the net requirement is 1,280. The lead time is 1 week. The planned order release will be 1,280 in day 2 which will be the planned order receipt in day 3.
Day 4:
The gross requirement is 1,280 (2 assembly) of long brace derived from the planned order release of base assembly. The On hand is 0. Therefore, the net requirement is 1,280. The lead time is 1 week. The planned order release will be 1,280 in day 3 which will be the planned order receipt in day 4.
Day 5:
The gross requirement is 256 (2 assembly) of long brace derived from the planned order release of base assembly. The On hand is 0. Therefore, the net requirement is 256. The lead time is 1 week. The planned order release will be 256 in day 4 which will be the planned order receipt in day 5.
Day 6:
The gross requirement is 256 (2 assembly) of long brace derived from the planned order release of base assembly. The On hand is 0. Therefore, the net requirement is 256. The lead time is 1 week. The planned order release will be 256 in day 5 which will be the planned order receipt in day 6.
Leg:
Period (Day) | ||||||||
Leg | 1 | 2 | 3 | 4 | 5 | 6 | 7 | 8 |
Gross requirements | 2,560 | 2,560 | 512 | 512 | ||||
Scheduled receipt | ||||||||
On hand (0) | ||||||||
Net requirement | 2,560 | 2,560 | 512 | 512 | ||||
Planned order receipt | 2,560 | 2,560 | 512 | 512 | ||||
Planned order release | 2,560 | 2,560 | 512 | 512 |
Day 3:
The gross requirement is 2,560 (4 assembly) of leg derived from the planned order release of base assembly. The On hand is 0. Therefore, the net requirement is 2,560. The lead time is 1 week. The planned order release will be 2,560 in day 2 which will be the planned order receipt in day 3.
Day 4:
The gross requirement is 2,560 (4 assembly) of leg derived from the planned order release of base assembly. The On hand is 0. Therefore, the net requirement is 2,560. The lead time is 1 week. The planned order release will be 2,560 in day 3 which will be the planned order receipt in day 4.
Day 5:
The gross requirement is 512 (4 assembly) of leg derived from the planned order release of base assembly. The On hand is 0. Therefore, the net requirement is 512. The lead time is 1 week. The planned order release will be 512 in day 4 which will be the planned order receipt in day 5.
Day 6:
The gross requirement is 512 (4 assembly) of leg derived from the planned order release of base assembly. The On hand is 0. Therefore, the net requirement is 256. The lead time is 1 week. The planned order release will be 512 in day 5 which will be the planned order receipt in day 6.
Brass caps:
Period (Day) | ||||||||
Brass caps | 1 | 2 | 3 | 4 | 5 | 6 | 7 | 8 |
Gross requirements | 2,560 | 2,560 | 512 | 512 | ||||
Scheduled receipt | ||||||||
On hand (0) | 0 | 440 | 880 | 368 | 856 | 856 | 856 | |
Net requirement | 2,560 | 2,120 | 0 | 144 | ||||
Planned order receipt | 3,000 | 3,000 | 1,000 | |||||
Planned order release | 3,000 | 3,000 | 1,000 |
Day 2:
The gross requirement is 2,560 (1 assembly) of brass caps derived from the planned order release of legs. The On hand is 0. Therefore, the net requirement is 2,560. The lead time is 1 week. The planned order release will be 3,000 (1 Lot = 1,000) in day 1 which will be the planned order receipt in day 2. The excess inventory of 440 is available at day 3.
Day 3:
The gross requirement is 2,560 (1 assembly) of brass caps derived from the planned order release of legs. The On hand is 440. Therefore, the net requirement is 2,120. The lead time is 1 week. The planned order release will be 3,000 (1 Lot = 1,000) in day 2 which will be the planned order receipt in day 3. The excess inventory of 880 is available at day 4.
Day 4:
The gross requirement is 512 (1 assembly) of brass caps derived from the planned order release of legs. The On hand is 880. Therefore, the net requirement is 0. Therefore, there will be no planned release. The excess inventory of 368 is available at day 5.
Day 5:
The gross requirement is 512 (1 assembly) of brass caps derived from the planned order release of legs. The On hand is 368. Therefore, the net requirement is 144. The lead time is 1 week. The planned order release will be 1,000 (1 Lot = 1,000) in day 4 which will be the planned order receipt in day 5. The excess inventory of 856 is available at the next day.
Calculation of labor hours / day:
Master Schedule | Hours Required | Day 1 | Day 2 | Day 3 | Day 4 | Day 5 | Day 6 | Day 7 | Day 8 |
Table assembly | 2 | 1280 | 1280 | 256 | 256 | ||||
Top preparation | 2 | 1280 | 1280 | 256 | 256 | ||||
Assemble base | 1 | 640 | 640 | 128 | 128 | ||||
Long brace (2) | 0.25 | 320 | 320 | 64 | 64 | ||||
Short brace (2) | 0.25 | 320 | 320 | 64 | 64 | ||||
Leg (4) | 0.25 | 640 | 640 | 128 | 128 | ||||
Total Hours | 0 | 1280 | 3200 | 3456 | 1920 | 640 | 256 | ||
Employees need @ 8 hours / day | 0 | 160 | 400 | 432 | 240 | 80 | 32 |
The master production schedule is derived from net requirements plan.
Formula to calculate number of hours / each day:
Formula to calculate the number of employees per 8 hour day:
Day 2:
Calculation of total hours for each day for each component:
Long brace:
Short brace:
Leg:
Calculation of total hours / day:
The total hours is calculated by summing all the hours needed for each component in a day.
Calculation of number of employees per 8 hour day:
The number of employees is calculated by dividing the total hours per day with the number of hours per day.
Day 3:
Calculation of total hours for each day for each component:
Top preparation:
Assemble base:
Long brace:
Short brace:
Leg:
Calculation of total hours / day:
The total hours is calculated by summing all the hours needed for each component in a day.
Calculation of number of employees per 8 hour day:
The number of employees is calculated by dividing the total hours per day with the number of hours per day.
Day 4:
Calculation of total hours for each day for each component:
Table assembly:
Top preparation:
Assemble base:
Long brace:
Short brace:
Leg:
Calculation of total hours / day:
The total hours is calculated by summing all the hours needed for each component in a day.
Calculation of number of employees per 8 hour day:
The number of employees is calculated by dividing the total hours per day with the number of hours per day.
Day 5:
Calculation of total hours for each day for each component:
Table assembly:
Top preparation:
Assemble base:
Long brace:
Short brace:
Leg:
Calculation of total hours / day:
The total hours is calculated by summing all the hours needed for each component in a day.
Calculation of number of employees per 8 hour day:
The number of employees is calculated by dividing the total hours per day with the number of hours per day.
Day 6:
Calculation of total hours for each day for each component:
Table assembly:
Top preparation:
Assemble base:
Calculation of total hours / day:
The total hours is calculated by summing all the hours needed for each component in a day.
Calculation of number of employees per 8 hour day:
The number of employees is calculated by dividing the total hours per day with the number of hours per day.
Day 7:
Calculation of total hours for each day for each component:
Table assembly:
Calculation of total hours / day:
The total hours is calculated by summing all the hours needed for each component in a day.
Calculation of number of employees per 8 hour day:
The number of employees is calculated by dividing the total hours per day with the number of hours per day.
Want to see more full solutions like this?
Chapter 14 Solutions
EBK PRINCIPLES OF OPERATIONS MANAGEMENT
- Francis Johnson’s plant needs to design an efficient assembly line to make a new product. The assembly line needs to produce 15 units per hour, and there is room for only four workstations. The tasks and the order in which they must be performed are shown in the following table. Tasks cannot be split, and it would be too expensive to duplicate any task. TASK TASK TIME (MINUTES) IMMEDIATE PREDECESSOR A 1 — B 2 — C 3 — D 1 A, B, C E 3 C F 2 E G 3 E What is the workstation cycle time required to produce 15 units per hour? Note: Round your answer to 1 decimal place. Balance the line to use the fewest possible workstations to meet the cycle time found in part (b). Use whatever method you feel is appropriate. What is the efficiency of your line balance, assuming the line operates at the cycle time from part (b)? Note: Round your answer to 1 decimal place.arrow_forwardYou've just been assigned the job of setting up an electric fan assembly line with the following tasks and precedence relationships The assemtly line wil be nunning 8 hours per day and 5 days per week, The demand forast is 600 Items per week. Your goal is to minimie the numbor of workstations necesary to complete enough units to satisfy the demand forecast. What is the takt time (in minutes) needed to produce the required number of units? (Integer Answer, do not put anything other than numbers.) What is the theoretical minimum number of workstations that you will need (apply the round-up rule)? (Integer Answer, do not put anything other than numbers.)arrow_forwardKlassen Toy Company, Inc., assembles two parts(parts I and 2): Part I is first processed at workstation A for15 minutes per unit and then processed at workstation B for330 PART 2 DESIGNING OPERATIONS10 minutes per unit. Part 2 is simultaneously processed at workstationC for 20 minutes per unit. Workstations B and C feed theparts to an assembler at workstation D, where the two parts areassembled. The time at workstation Dis 15 minutes.a) What is the bottleneck of this process?b) What is the hourly capacity of the process?arrow_forward
- Bill builds benches in a small shop and he plans to operate five 8-hour days perweek. Each bench has two ends and a top. It takes 5 minutes to cut and sand eachend and 2 minutes to make each top. Assembly requires 8 minutes per bench, andpainting requires 5 minutes per bench. Bill has one employee who makes the topsand ends. Bill will do the final assembly and painting. He also plans 1 hour per dayfor setup and teardown for each department.a. How many benches should he plan to build per week?b. How many hours per week are required for each person?c. Suggest ways to increase the number of benches produced per weekarrow_forwardThe desired daily output for an assembly line is 540 units. This assembly line will operate 720 minutes per day. The following table contains information on this product's task times and precedence relationships: TASK TASK TIME(SECONDS) IMMEDIATEPREDECESSOR A 35 — B 25 A C 35 A D 55 B E 5 B F 15 C G 30 E-D H 5 F-G b. What is the workstation cycle time? c. Balance this line using the largest number of following tasks. Use the longest task time as a secondary criterion. (Leave no cells blank - be certain to enter "0" wherever required.)arrow_forwardA shop works a 400-minute day. The manager of the shop wants an output of 200 units per day for the assembly line that has the elemental tasks shown in the table. Do the following: b.) Assign tasks according to the most following tasks rule. Break ties with the greatest positional weight rule. c.) Assign tasks according to the greatest positional weight rule. Break ties with the most following tasks rule. d.) Compute the efficiency level for each rule. Which one yields the better set of assignments in this instance?arrow_forward
- The following tasks are to be performed on an assembly line: TASK SECONDS TASKS THAT MUST PRECEDE A 30 — B 16 A C 21 B D 15 B E 17 C F 14 D G 20 E, F H 9 G The workday is 8 hours long. The demand for completed product is 900 per day. Find the cycle time required to meet the desired output rate. Note: Round your answer to 1 decimal place.arrow_forwardUsing the information below answer the following questionsa) What is the bottleneck in the process – show your work by demonstrating the workloadby product and station.b) Using the traditional (margin) based model what is the order of priority of the 4 products,and how many of each can they produce BY MONTH. Show your math for determiningthe order of priority and for determining the number of unitsc) Using the bottle keck based model what is the order of priority of the 4 products, andhow many of each can they produce BY MONTH. Show your math for determining theorder of priority and for determining the number of unitsd) What is the profit using the traditional method – show your mathe) What is the profit using the bottleneck method – show your mathThe factory runs one 8-hour shift per day per station, operates five days a week. The skilledemployees get paid $25 / hour. In addition, the factory has a weekly overhead of $2000. Due touncertainty in the demand planning, management has…arrow_forwardAn assembly line must be designed to produce 40 containers per hour. The following data give the necessary information Table 1 TASK IMMEDIATE PREDECESSOR TASK TIME (sec) A None 60 B A 12 C B 35 D A 55 E D 10 F E 50 G F, C 5 Draw the precedence diagram. Compute the cycle time (in seconds) to achieve the desired output rate. What is the theoretical minimum number of stations? Assign the tasks to the workstation? What is the efficiency of the line? Calculate the idle timearrow_forward
- The desired daily ouput for an assembly line is 420 units. This assembly line will operate 595 minutes per day. The following table contains information on the products task times and precedence relationships Task. Task time-seconds Immediate predecessor A. 35 - B. 40 A C 30 A D 40 B E 20 C F 70 C G 45 E-F H 30 D-G The required workstation cycle time to meet the desired output time is 85 seconds Balance this line using the largest number of following tasks. Use the longest task time as a secondary criterion The answer gives only 4 workstations as option Have to fill out following Workstation. Task Idle time 1 ?? ?? 2 ?? ?? 3…arrow_forwardAn assembly plant for the Blood Pressure RX, a portableblood pressure device, has 400 minutes available daily in theplant for the device, and the average demand is 80 units per day.Final assembly requires 6 separate tasks. Information concerningthese tasks is given in the following table. a) Draw a precedence diagram of this operationb) Given the demand, what is the cycle time for this operation?c) What is the theoretical minimum number of workstations?f d) Assign tasks to workstations.e) What is the overall actual efficiency of the assembly line?arrow_forwardThe following tasks are to be performed on an assembly line: TASK SECONDS TASKS THAT MUST PRECEDE A 20 — B 7 A C 20 B D 22 B E 15 C F 10 D G 16 E, F H 8 G The workday is seven hours long. The demand for completed product is 750 per day. Find the cycle time required to meet the desired output rate. Note: Round your answer to 1 decimal place. What is the theoretical number of workstations required to meet the desired output rate? Note: Round up your answer to the next whole number. Balance the line using sequential restrictions and the longest-operating-time rule. Determine the task under each workstation and the idle time for each such task. Note: Round your answers to 1 decimal place. What is the efficiency of the line balanced as in part (d) assuming it is running at the cycle time determined in part (a)? Note: Round your answer to 1 decimal place. Suppose that demand rose from 750 to 800 units per day. Determine the cycle time. (Use the…arrow_forward
- Practical Management ScienceOperations ManagementISBN:9781337406659Author:WINSTON, Wayne L.Publisher:Cengage,
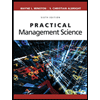