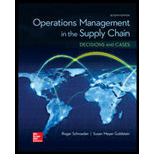
OPERATIONS MANAGEMENT IN THE SUPPLY CHAIN: DECISIONS & CASES (Mcgraw-hill Series Operations and Decision Sciences)
7th Edition
ISBN: 9780077835439
Author: Roger G Schroeder, M. Johnny Rungtusanatham, Susan Meyer Goldstein
Publisher: McGraw-Hill Education
expand_more
expand_more
format_list_bulleted
Textbook Question
Chapter 4, Problem 6DQ
A company is in the business of making souvenir spoons to customer order. The customers select the size of the spoons and may specify the design to be embossed on them. One or more spoons may be ordered. The company is considering going into the make-to-stock spoon business for souvenir spoons and everyday tableware as well. What will it have to do differently? How is the business likely to change?
Expert Solution & Answer

Want to see the full answer?
Check out a sample textbook solution
Students have asked these similar questions
The Andrews family is in the process of hiring a five-star chef who can cook a variety of food to meet customers’ tastes and wants (top quality). In addition, the restaurant is designed to provide complete privacy to customers. Therefore, tables ought to be separated by no less than 5 feet. Using Chapter 2 and the assigned videos as your theoretical foundations, please answer the following question.
What production process should the restaurant choose? Explain your answer.
In contrast to the Andrews family restaurant, the Sweet family restaurant sells burgers, burritos, and hotdogs. The restaurant relies on high school students to cook food, and customers cannot customize their food choices. The Sweet family restaurant sells 2000 burgers per restaurant each day. The average costs of burgers, burritos, and hot dogs are $2, $3, and $0.50, respectively. Using Chapters 1 and 2 as your theoretical foundations, please answer the following question:
What are the Sweet family…
A company makes parts that cost $35.00 in material and labor. 92% of the parts are produced defect
free and are sold for full price at $110 each. 2% of the parts made must be scrapped. Scrap parts are
sold for $8.00 each. The remaining 6% of the parts made must be reworked at a cost of $12.00 each.
After rework 1% still must be scrapped and the other 5% is sold at a discounted price of $90 each.
a. Draw the tree diagram showing the quality cost situation.
b. Determine the earnings per part.
c. Determine the cost of poor quality (COPQ).
d. Determine the earnings per part and COPQ if the rework operation was shut down and the parts
that required reworking were just sold for scrap instead.
Why is flexibility in the process desired? What are the two requirements?
Chapter 4 Solutions
OPERATIONS MANAGEMENT IN THE SUPPLY CHAIN: DECISIONS & CASES (Mcgraw-hill Series Operations and Decision Sciences)
Ch. 4 - Prob. 1DQCh. 4 - Why are assembly-line processes usually so much...Ch. 4 - The rate of productivity improvement in the...Ch. 4 - Several industriesincluding those that produce...Ch. 4 - Compare the expensive restaurant, fast-food...Ch. 4 - A company is in the business of making souvenir...Ch. 4 - Prob. 7DQCh. 4 - Suppose that a firm is considering moving from a...Ch. 4 - Prob. 9DQCh. 4 - Prob. 10DQ
Knowledge Booster
Learn more about
Need a deep-dive on the concept behind this application? Look no further. Learn more about this topic, operations-management and related others by exploring similar questions and additional content below.Similar questions
- Tribal Systems, Inc., is opening a new plant and has yet todecide on the type of process to employ. A labor-intensiveprocess would cost $10,000 for tools and equipment and $14 for labor and materials per item produced. A more au-tomated process costs $50,000 in plant and equipment but has a labor/material cost of $8 per item produced. A fullyautomated process costs $300,000 for plant and equipmentand $2 per item produced. If process selection were basedsolely on lowest cost, for what range of production wouldeach process be chosen?arrow_forwardTribal Systems, Inc., is opening a new plant and has yet todecide on the type of process to employ. A labor-intensiveprocess would cost $10,000 for tools and equipment and$14 for labor and materials per item produced. A more automated process costs $50,000 in plant and equipment buthas a labor/material cost of $8 per item produced. A fullyautomated process costs $300,000 for plant and equipmentand $2 per item produced. If process selection were basedsolely on lowest cost, for what range of production wouldeach process be chosen?arrow_forwardDetermine the order qualifiers and order winners for the restaurant business?arrow_forward
- A company manufactures souvenir spoons to order for customers.Customers can choose the size of the spoons as well as the design that will be embossed on them. You may order one or more spoons. The company is thinking about going into the make-to-stock spoon business for souvenir spoons as well as everyday tableware. What will it be required to do differently? What changes are likely to occur in the business?arrow_forwardIf the sales forecast estimates that 50,000 units of product will be sold during the following year, should the factory plan on manufacturing 50,000 units in the coming year? Explain.arrow_forwardThe team of ABC corp, the manufacturer of a chip processor, has a good grasp on how software giants build products around its processors. The teams at ABC design processors to feature attractive capabilities to the software giants by seeking input from researchers and designers on the ABC corp team who possess knowledge of current and upcoming trends. New processors will incorporate these trends in design. After identifying what type of problem-solving style this would be an example of, incorporate the key skills entrepreneurs must have and apply them in terms of the ABC corp team.arrow_forward
- Why is it important to make sure that the capabilities of the process are matched up with the requirements of the product?arrow_forwardWhat are some of the recommendations for number 2? And you answer them separately.arrow_forwardWhy are process selection decisions by their very essence extremely cross-functional?arrow_forward
- Lynette is interested in finding a sedan car for work. Below is the summary of her criteria and the choices that she has selected as potential cars that she may purchase. She wants you to find out the best alternative based on these data. Note: Calculate the data given below in the same way as the rating scale. There is no need to convert the data into the rating scale before the calculation. Criteria Weight Toyota Camry Volkswagen Passat Mazda 6 Hyundai Sonata Objective Drive-away price 8 $51,673 $57,399 $55,040 $55,692 Min Engine size (L) 3 2.5 2.0 2.5 2.5 Max Fuel tank capacity (L) 5 50 66 62 60 Max Power:Weight (W/kg) 5 97.3 108.3 104.8 130.2 Max Max torque (Nm) 4 221 350 420 422 Max Fuel consumption (L/100km) 7 4.7 6.9 7.6 8.1 Min Service cost (5 yr) 6 $1,940 $2,692 $2,310 $1,446 Minarrow_forwardWhat invisible biases,values or norms may have been introduced into the design,planning or intended use of the red light camera by the creators or planners, and how can this be determined?arrow_forwardWhat do the expressions order winner and order qualifiers mean? What was the order winner for your last major purchase of a product or service?arrow_forward
arrow_back_ios
SEE MORE QUESTIONS
arrow_forward_ios
Recommended textbooks for you
- Practical Management ScienceOperations ManagementISBN:9781337406659Author:WINSTON, Wayne L.Publisher:Cengage,
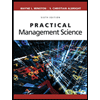
Practical Management Science
Operations Management
ISBN:9781337406659
Author:WINSTON, Wayne L.
Publisher:Cengage,
Process selection and facility layout; Author: Dr. Bharatendra Rai;https://www.youtube.com/watch?v=wjxS79880MM;License: Standard YouTube License, CC-BY