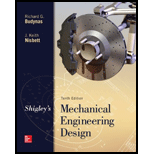
Shigley's Mechanical Engineering Design (McGraw-Hill Series in Mechanical Engineering)
10th Edition
ISBN: 9780073398204
Author: Richard G Budynas, Keith J Nisbett
Publisher: McGraw-Hill Education
expand_more
expand_more
format_list_bulleted
Concept explainers
Textbook Question
Chapter 7, Problem 2P
The section of shaft shown in the figure is to be designed to approximate relative sizes of d = 0.75D and r = D/20 with diameter d conforming to that of standard rolling-bearing bore sizes. The shaft is to be made of SAE 2340 steel, heat-treated to obtain minimum strengths in the shoulder area of 175 kpsi ultimate tensile strength and 160 kpsi yield strength with a Brinell hardness not less than 370. At the shoulder the shaft is subjected to a completely reversed bending moment of 600 lbf · in, accompanied by a steady torsion of 400 lbf · in. Use a design factor of 2.5 and size the shaft for an infinite life using the DE-ASME Elliptic criterion.
Expert Solution & Answer

Want to see the full answer?
Check out a sample textbook solution
Students have asked these similar questions
A short stub shaft, made of SAE 1035, as rolled, receivers 30 hp at 300 rpm via a 12-in. spur gear, the power being delivered to another shaft through a flexible coupling. The gear is keyed (profile keyway) midway between the bearings. The pressure angle of the gear teeth 20o, N = 1.5 based on the octahedral shear stress theory with varying stresses. (a) Neglecting the radial component R of the tooth load W , determine the shaft diameter. (b) Considering both the tangential and the radial components, compute the shaft diameters. (c) Is the difference in the results of the parts (a) and (b) enough to change your choice of the shaft size?
A turbine shaft transmits 500 kW power at 900 rpm. The permissible shear stress is 80N/mm² while twist is limited to 0.5º in a length of 2.5 m. Take G = 0.8x10⁵ N/mm², on thebasis of torsional rigidity;i.Determine diameter of shaft if solid shaft is used.ii.If hollow shaft is chosen with di/do = 0.6, determine the suitable diameters of theshaft.
please write with ball pen.. thank you
(2) A diesel engine developing 1,850 hp at 105 rpm is used on a ship to drive the propeller. The shaft of
the propeller is to be made of 3.5% per cent nickel steel, heat-treated, with an ultimate strength in
tension of 130,000 psi, and an ultimate in shear about 70% of the ultimate in tension. Angular twist
is limited to 1° in 20 diameters.
(a) Using a design factor of 2, find the diameter of solid shaft required.
(b) Using the same data, find the diameter of hollow shaft required if the outside diameter is twice
the inside diameter.
(c) What is the percentage of saving in weight by using the hollow shaft?
Chapter 7 Solutions
Shigley's Mechanical Engineering Design (McGraw-Hill Series in Mechanical Engineering)
Ch. 7 - A shaft is loaded in bending and torsion such that...Ch. 7 - The section of shaft shown in the figure is to be...Ch. 7 - The rotating solid steel shaft is simply supported...Ch. 7 - A geared industrial roll shown in the figure is...Ch. 7 - Design a shaft for the situation of the industrial...Ch. 7 - The figure shows a proposed design for the...Ch. 7 - For the problem specified in the table, build upon...Ch. 7 - Prob. 8PCh. 7 - For the problem specified in the table, build upon...Ch. 7 - For the problem specified in the table, build upon...
Ch. 7 - In the figure is a proposed shaft design to be...Ch. 7 - The shaft shown in the figure is proposed for the...Ch. 7 - Prob. 20PCh. 7 - The shaft shown in the figure is proposed for the...Ch. 7 - Prob. 25PCh. 7 - Prob. 26PCh. 7 - Prob. 27PCh. 7 - A 25-mm-diameter uniform steel shaft is 600 mm...Ch. 7 - Prob. 29PCh. 7 - Compare Eq. (727) for the angular frequency of a...Ch. 7 - Prob. 31PCh. 7 - The steel shaft shown in the figure carries a...Ch. 7 - A transverse drilled and reamed hole can be used...Ch. 7 - Prob. 34PCh. 7 - The shaft shown in Prob. 721 is proposed for the...Ch. 7 - A guide pin is required to align the assembly of a...Ch. 7 - Prob. 37PCh. 7 - Prob. 38PCh. 7 - Prob. 39PCh. 7 - A ball bearing has been selected with the bore...Ch. 7 - Prob. 41PCh. 7 - A gear and shaft with nominal diameter of 35 mm...
Knowledge Booster
Learn more about
Need a deep-dive on the concept behind this application? Look no further. Learn more about this topic, mechanical-engineering and related others by exploring similar questions and additional content below.Similar questions
- The stepped shaft shown in the figure is required to transmit 600 kW of power at 400 rpm. The shaft has a full quarter-circular fillet, and the smaller diameter D1= 100 mm. If the allowable shear stress at the stress concentration is 100 MPa, at what diameter will this stress be reached? Is this diameter an upper or a lower limit on the value of D2?arrow_forwardA motor driving a solid circular steel shaft with diameter d = 1.5 in, transmits 50 hp to a gear at B, The allowable shear stress in the steel is 6000 psi. Calculate the required speed of rotation (number of revolutions per minute) so that the shear stress in the shaft does not exceed the allowable limit.arrow_forwardA full quarter-circular fillet is used at the shoulder of a stepped shaft having diameter D2= 1.0 in. (see figure), A torque T = 500 lb-in. acts on the shaft. Determine the shear stress at the stress concentration for values as follows: D1= 0.7,0.8, and 0.9 in. Plot a graph showing versus D?arrow_forward
- Two designs for a shaft are being considered. Both have an outside diameter of 70 m and are 900 mm long. One is solid but the other is hollow with an internal diameter of 50 mm. Both are made from steel (G=120 GPa). Compare the torsional shear stress, angle of twist of the two designs if they are subjected to a torque of 722 N. m.arrow_forwardSteel shaft can be produced as solid body or circular tube with circular tube. The shaft must bear a torque of 1200 Nm. Since the shear strength for the shaft material is 40 MPa, the maximum allowable unit torsion angle of the bar is 0.75 ^ 0 / m and the shear modulus of steel is G = 78 GPa;a) Find the required diameter d0 for a solid circle shaft.b) Find the required outside diameter d2 for a ring-section shaft whose thickness is one tenth of the outer diameter.c) Find the diameter ratio (d2 / d0 ratio) and weight ratio for ring cross section and solid section shaftsarrow_forwardA 1.5-inch Monel shaft is used in a torsional application. Based on the operating speed of 100 rpm and factor of safety of 12. How much horsepower can it transmit? Assume the shearing stress is ¾ of the ultimate tensile stress which is 100 ksi.arrow_forward
- Bearing stress 5. Please provide proper discussion and illustration also complete solution and clear solution please thank you A solid shaft is designed to transmit 50kN @ 1800 rpm to a gear by means of 156 mm long key with square cross-section. The shaft diameter is 35.6mm. What should the cross-section be in mm2 to resist shearing, if the allowable shear stress on the key is 20 MPa?arrow_forwardThe figure shows an inboard engine, 8-ft long steel drive shaft, and propeller for a motor boat. The shaft is to be designed to safely transmit 200 hp at 3500 rev/ min. Determine the diameter of the smallest shaft that can be used and its corresponding angle of twist. For the steel, use a working shear stress of 12 000 psi and G = 12 x 106 psifind, a) diameter b) angle of twistarrow_forwardThe motor shown in Fig. P6-47 develops 100 hp at a speed of 360 rpm. Gears A and B deliver 40 hp and 60 hp, respectively, to operating units in a factory. If the maximum shearing stress in the shafts must be limited to 12 ksi, determine a. The minimum satisfactory diameter for the motor shaft. b. The minimum satisfactory diameter for the power shaft. (1 hp=745,7 watts); (1 ksi=6,89 MPa); (1 ft=0,30 m)arrow_forward
- A hollow shaft has to be designed for a marine engine delivering 1200 kW when running at 120 r/min. The maximum allowable shear stress is 50 MPa and the maximum torque to be transmitted by the shaft is 30 % greater than the mean torque. The internal diameter of the shaft is 50 % that of the external diameter. Calculate the shaft dimensions and the angle of twist of the shaft over 3 m when transmitting the above torque (G = 80 GPa).arrow_forwardA solid and a hollow shaft, connected by a coupling, transmit power. The outside diameters of the shafts are the same and the inside diameter of the hollow shaft is 75 % of its outside diameter. The solid shaft is three times as long as the hollow shaft. Take the modulus of rigidity for both shafts as 80 GPa. (a) If the angle of twist for the solid shaft is 1°, find the angle of twist for the hollow shaft. (b) If the maximum shear stress in the solid shaft is 30 MPa, find the maximum stress in the hollow shaft.arrow_forwardTorsion in circular shafts From the figure as shown, the maximum shearing stress is 30 MPa and the angle of twist is 1.25°. Determine the maximum permissible torque? Use G = 80 GPa.arrow_forward
arrow_back_ios
SEE MORE QUESTIONS
arrow_forward_ios
Recommended textbooks for you
- Mechanics of Materials (MindTap Course List)Mechanical EngineeringISBN:9781337093347Author:Barry J. Goodno, James M. GerePublisher:Cengage Learning
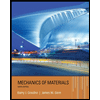
Mechanics of Materials (MindTap Course List)
Mechanical Engineering
ISBN:9781337093347
Author:Barry J. Goodno, James M. Gere
Publisher:Cengage Learning
Understanding Torsion; Author: The Efficient Engineer;https://www.youtube.com/watch?v=1YTKedLQOa0;License: Standard YouTube License, CC-BY