Ch.06-01 Production Master Data - S4HANA 1709 MCC V1.4
docx
keyboard_arrow_up
School
University of Central Florida *
*We aren’t endorsed by this school
Course
4205
Subject
Accounting
Date
Apr 3, 2024
Type
docx
Pages
45
Uploaded by PrivateGrasshopper4093
Chapter 06-01: Production Master Data
PREREQUISITES
1.
You should be familiar with navigation in SAP HANA
2.
Completed Exercises Chs. 02-01 through 05-02
MOTIVATION
In this exercise, you will do the following for Production Master Data:
1.
Create Materials
2.
View Inventory Balance
3.
View Material Inventory
4.
Display Requirements List
5.
Create Bills of Materials
6.
Create Product Routings
7.
Create Initial Inventory Balances PRODUCT
SAP S/4 HANA 1709
REVISED
04/06/2020
FOCUS
Production
Master Data
AUTHORS
Simha R. Magal
Jeff Word
VERSION
1.3 MCC
TESTED
Date: 04/06/2020
System: MGL
ACKNOWLEDGEMENT
These are the GBI exercises developed by Simha R. Magal and Jeff Word. These exercises include concepts discussed in the book,
Integrated Business Processes with ERP Systems
(Epistemy Press, 2012).
© 2020 Epistemy Press, LLC.
Screenshots © 2020, SAP SE
Chapter 06: Production Master Data
Page 2 of 45
© 2020 Epistemy Press, LLC.
Part 1 - Table of Contents
Table of Contents
Section 1.1: Create Materials
......................................................................................................................
3
Section 1.2: View Inventory Balance
...........................................................................................................
9
Section 1.3: View Material Inventory
........................................................................................................
10
Section 1.4: Display Requirements List
......................................................................................................
11
Section 1.5: Create Bills of Materials
.........................................................................................................
13
Section 1.6: Create Product Routings
........................................................................................................
16
Section 1.7: Create Production Versions
...................................................................................................
19
Section 1.8: Create Initial Inventory Balance
.............................................................................................
23
Chapter 06: Production Master Data
Page 3 of 45
© 2020 Epistemy Press, LLC.
Create Materials
(I)
View Inventory Balance
(II)
View Material Inventory
(III)
Display Requirements List
(IV)
Create Bills of Materials
(V)
Create Product Routings
(VI)
Create Initial Inventory Balances
(VII)
Your preview ends here
Eager to read complete document? Join bartleby learn and gain access to the full version
- Access to all documents
- Unlimited textbook solutions
- 24/7 expert homework help
In this section, you will be creating your own version of all the below raw materials, semi-finished goods,
and finished goods necessary for the production process within the material master. The following table consists of five columns: the original material description, the original material number, your material number, the material type, and your storage location where it is.
Description
Number
Your Number
Type
Your S.L.
Raw Materials
Brake Kit
BRKT1000
BRKT10##
Raw
RM##
Chain
CHAN1000
CHAN10##
Raw
RM##
Derailleur Gear Assembly
DGAM1000
DGAM10##
Raw
RM##
Hex Nut 5 mm
HXNT1000
HXNT10##
Raw
RM##
Lock Washer 5 mm
LWSH1000
LWSH10##
Raw
RM##
Packaging
PCKG1000
PCKG10##
Raw
RM##
Pedal Assembly
PEDL1000
PEDL10##
Raw
RM##
Socket Head Bolt 5x20mm
BOLT1000
BOLT10##
Raw
RM##
Chapter 06: Production Master Data
Page 4 of 45
© 2020 Epistemy Press, LLC.
Section 1.1: Create Materials
Create Materials
(I)
View Inventory Balance
(II)
View Material Inventory
(III)
Display Requirements List
(IV)
Create Bills of Materials
(V)
Create Product Routings
(VI)
Create Initial Inventory Balances
(VII)
Touring Aluminum Wheel
TRWH1000
TRWH10##
Raw
RM##
Touring Frame-Red
TRFR3000
TRFR30##
Raw
RM##
Touring Handle Bar
TRHB1000
TRHB10##
Raw
RM##
Touring Seat Kit
TRSK1000
TRSK10##
Raw
RM##
Touring Tire
TRTR1000
TRTR10##
Raw
RM##
Touring Tube
TRTB1000
TRTB10##
Raw
RM##
Warranty Document
WDOC1000
WDOC10##
Raw
RM##
Semi-Finished Materials
Touring Aluminum Wheel Assembly
TRWA1000
TRWA10##
Semi.
SF##
Finished Materials
Deluxe Touring Bike (red)
DXTR3000
DXTR30##
Fin.
FG##
Chapter 06: Production Master Data
Page 5 of 45
© 2020 Epistemy Press, LLC.
Raw Materials
Step: 1.1.1: In the “SAP Easy Access”
screen, follow the navigation path below:
Navigation
SAP Easy Access Menu
Logistics
Materials Management
Material Master
Material
Create (General)
Immediately
1: What is the Transaction Code to create a general material immediately?
2: What is the Transaction Code to change a material immediately?
3: What is the Transaction Code to display a current material?
Step: 1.1.2: In the “Create Material (Initial Screen)”
screen, enter the following information:
Attribute
Description
Data Value
Material
Key uniquely identifying the material
Your Brake Kit
Industry Sector
Specifies the branch of industry to which the material is assigned
Mechanical Engineering
Material Type
Assigns the material to a group of materials Raw Materials
Copy from…Material
Data you want the system to copy as default values
Original Brake Kit
Step: 1.1.3: Click Continue
.
Step: 1.1.4: In the “Select View(s)”
pop-up, click Deselect All
.
Chapter 06: Production Master Data
Page 6 of 45
© 2020 Epistemy Press, LLC.
Your preview ends here
Eager to read complete document? Join bartleby learn and gain access to the full version
- Access to all documents
- Unlimited textbook solutions
- 24/7 expert homework help
Step: 1.1.5: Highlight the “Basic Data 1”
row.
Step: 1.1.6: Highlight the “Purchasing”
row.
Step: 1.1.7: Highlight the “MRP 1”
row.
Step: 1.1.8: Highlight the “General Plant Data / Storage 1”
row.
Step: 1.1.9: Highlight the “Accounting 1”
row.
Step: 1.1.10: Highlight the “Costing 1”
row.
Step: 1.1.11: Click Save as Default Values .
Step: 1.1.12: Click Org. Levels .
Chapter 06: Production Master Data
Page 7 of 45
© 2020 Epistemy Press, LLC.
Step: 1.1.13: In the “Organizational Levels”
pop-up, enter the following information:
Attribute
Description
Data Value
Plant
Key uniquely identifying a plant
Your Dallas Plant
Stor. Location
Location where materials are stored
Your Raw Materials
Copy from Plant
Plant of reference Original Dallas Plant
Copy from Stor. Location
Storage location of reference
Original Raw Materials
Step: 1.1.14: Click Save As Default Values and then click continue(Enter) You will receive a message that says, “The material already exists and will extend”.
Step: 1.1.15: In the “Create Material BRKT10## (Raw materials)”
screen, enter the following information:
Attribute
Description
Data Value
Material Description
Describes the material in more detail
## Brake Kit
Purchasing Group
A buyer or group of buyers
Your GBI Buyer
Step: 1.1.16: Press Enter, until the “Last data screen reached”
pop-up opens, click Yes You will receive a message that says “Material BRKT10## created”.
Step: 1.1.17: Refer to the beginning of this section and create the rest of your RAW materials.
Chapter 06: Production Master Data
Page 8 of 45
© 2020 Epistemy Press, LLC.
Semi-Finished Goods
Step: 1.1.18: In the “Create Material (Initial Screen)”
screen, enter the following information:
Attribute
Description
Data Value
Material
Key uniquely identifying the material
TRWA10##
Industry Sector
Branch of industry to which the material is assigned.
Mechanical Engineering
Material Type
Assigns the material to a group of materials Semi-finished Product
Copy from…
Material
Material whose data you want the system to copy as default values
Original Touring Aluminum Wheel Assembly
Step: 1.1.19: Click Continue .
Step: 1.1.20: In the “Select View(s)”
pop-up, click Deselect All .
Step: 1.1.21: Highlight “Basic Data 1”
Step: 1.1.22: Highlight “Purchasing”
Step: 1.1.23: Highlight “MRP 1”
Step: 1.1.24: Highlight “Work Scheduling”
Step: 1.1.25: Highlight “General Plant Data/Storage 1”
Step: 1.1.26: Highlight “Accounting 1”
Step: 1.1.27: Highlight “Costing 1”
Step: 1.1.28: Click Save As Default Values .
Chapter 06: Production Master Data
Page 9 of 45
© 2020 Epistemy Press, LLC.
Your preview ends here
Eager to read complete document? Join bartleby learn and gain access to the full version
- Access to all documents
- Unlimited textbook solutions
- 24/7 expert homework help
Step: 1.1.29: Click Org. Levels .
Step: 1.1.30: In the “Organizational Levels”
pop-up, enter the following information:
Attribute
Description
Data Value
Plant
Key uniquely identifying a plant
Your Dallas Plant
Stor. Location
Location at which materials are stored Your Semi-Fin. Goods
Copy from Plant
Plant of reference Original Dallas Plant
Copy from Stor. Location
Storage location of reference material
Original Semi-Fin. Goods
Step: 1.1.31: Click Save As Default Values and then click continue(Enter) .
You will receive a message that says, “The materials already exists and will be extended”.
Step: 1.1.32: In the “Create Material TRWA10## (Semi-Finished Product)”
screen, enter the following information:
Attribute
Description
Data Value
Material Description
Describes the material in more detail
## Touring Aluminum Wheel Assembly
MRP Type
Determines whether and how the material is planned.
MRP
Step: 1.1.33: Press Enter, until the “Last data screen reached”
pop-up opens, click on the
icon. You will receive a message that says “Material TRWA10## created”.
Chapter 06: Production Master Data
Page 10 of 45
© 2020 Epistemy Press, LLC.
Finished Goods
Step: 1.1.34: In the “Create Material (Initial Screen)”
screen, enter the following information:
Attribute
Description
Data Value
Material Key uniquely identifying the material
DXTR30##
Industry Sector
Specifies the branch of industry to which the material
is assigned.
Mechanical Engineering Material Type
Assigns the material to a group of materials Finished Product
Copy from…
Material
Material whose data you want the system to copy as default values
Original Deluxe Touring Bike (red)
Step: 1.1.35: Click Continue .
Step: 1.1.36: In the “Select View(s)”
pop-up, click Deselect All .
Step: 1.1.37: Highlight “Basic Data 1”
Step: 1.1.38: Highlight “MRP 1”
Step: 1.1.39: Highlight “Work Scheduling”
Step: 1.1.40: Highlight “General Plant Data/Storage 1”
Step: 1.1.41: Highlight “Accounting 1”
Step: 1.1.42: Highlight “Costing 1”
Step: 1.1.43: Click Save As Default Values .
Step: 1.1.44: In the “Select View(s)”
pop-up, click Org. Levels .
Chapter 06: Production Master Data
Page 11 of 45
© 2020 Epistemy Press, LLC.
Step: 1.1.45: In the “Organizational Levels”
pop-up, enter the following information:
Attribute
Description
Data Value
Plant
Key uniquely identifying a plant
Your Dallas Plant
Stor. Location
Location at which materials are stored Your Finished Goods
Copy from Plant
Plant of reference Original Dallas Plant
Copy from Stor. Location
Storage location of reference material
Original Finished Goods
Step: 1.1.46: Click Save As Default Values and then click continue(Enter) .
You will receive a message that says, “The material already exists and will be extended”.
Step: 1.1.47: In the “Create Material DXTR30## (Finished Product)”
screen, enter the following information:
Attribute
Description
Data Value
Material Description
Describes the material in more detail.
## Deluxe Touring Bike (red)
MRP Type
Determines whether and how the material is planned
MRP
Step: 1.1.48: Press Enter, until the “Last data screen reached”
pop-up opens, click .
You will receive a message that says “Material DXTR30## created”.
Chapter 06: Production Master Data
Page 12 of 45
© 2020 Epistemy Press, LLC.
Your preview ends here
Eager to read complete document? Join bartleby learn and gain access to the full version
- Access to all documents
- Unlimited textbook solutions
- 24/7 expert homework help
In this section, you look at the inventory balance of a raw material located within Dallas.
Step: 1.1.49: In the “SAP Easy Access”
screen, follow the navigation path below:
Navigation
SAP Easy Access Menu
Logistics
Materials Management
Physical Inventory
Environment
Stock Overview
4: What is the Transaction Code to display a material’s inventory level?
Step: 1.1.50: In the “Stock Overview: Company Code/Plant/Storage Location/Batch.”
screen, enter the following information:
Attribute
Description
Data Value
Material Key uniquely identifying the material
Your Touring Frame-Red
Plant
Key uniquely identifying a plant
Your Dallas Plant
Chapter 06: Production Master Data
Page 13 of 45
© 2020 Epistemy Press, LLC.
Section 1.2: View Inventory Balance
Create Materials
(I)
View Inventory Balance
(II)
View Material Inventory
(III)
Display Requirements List
(IV)
Create Bills of Materials
(V)
Create Product Routings
(VI)
Create Initial Inventory Balances
(VII)
Storage Location
Location at which the material is stored
Your Raw Materials
Click Execute .
5: How many Touring Frames-Red are in unrestricted use?
6: How many Touring Frames-Red are in reserved stock?
7: How many Touring Frames-Red are in on-order stock?
Chapter 06: Production Master Data
Page 14 of 45
© 2020 Epistemy Press, LLC.
In this section, you view your material inventory of all your materials maintained in Dallas.
Step: 1.1.51: In the “SAP Easy Access”
screen, follow the navigation path below:
Navigation
SAP Easy Access Menu
Logistics
Materials Management
Inventory Management
Environment
Stock
Warehouse Stock
8: What is the Transaction Code to display a material’s inventory level?
Step: 1.1.52: In the “Display Warehouse Stock of Material”
screen, enter the following information:
Attribute
Description
Data Value
Material
Key uniquely identifying the material
*0##
Plant
Key uniquely identifying a plant
DL##
Chapter 06: Production Master Data
Page 15 of 45
© 2020 Epistemy Press, LLC.
Section 1.3: View Material Inventory
Create Materials
(I)
View Inventory Balance
(II)
View Material Inventory
(III)
Display Requirements List
(IV)
Create Bills of Materials
(V)
Create Product Routings
(VI)
Create Initial Inventory Balances
(VII)
Your preview ends here
Eager to read complete document? Join bartleby learn and gain access to the full version
- Access to all documents
- Unlimited textbook solutions
- 24/7 expert homework help
Storage Location
Location at which the material is stored
*##
9: What is the code for Your Raw Material Storage Location?
10: What is the code for Your Semi-Finished Goods Storage Location?
11: What is the code for Your Finished Goods Storage Location?
Step: 1.1.53: Click Execute .
12: What is the total United States dollar value of Raw Materials in your inventory?
13: How many of Your Gear Assemblies are there in inventory?
14: What is the material code for Your Warranty Document?
Chapter 06: Production Master Data
Page 16 of 45
© 2020 Epistemy Press, LLC.
In this section, you look at the stock/requirements list for the touring aluminum wheel assembly.
Step: 1.1.54: In the “SAP Easy Access”
screen, follow the navigation path below:
Navigation
SAP Easy Access Menu
Logistics
Materials Management
Inventory Management
Environment
Stock
Stock/Requirements List
15: What is the Transaction Code to display a stock/requirements list?
Step: 1.1.55: In the “Stock/Requirements List: Initial Screen”
screen, enter the following information:
Attribute
Description
Data Value
Material Key uniquely identifying the material
Your Touring Aluminum Wheel Assembly
MRP Area
Number of the MRP area for which material requirements planning should Your Dallas Plant Chapter 06: Production Master Data
Page 17 of 45
© 2020 Epistemy Press, LLC.
Section 1.4: Display Requirements List
Create Materials
(I)
View Inventory Balance
(II)
View Material Inventory
(III)
Display Requirements List
(IV)
Create Bills of Materials
(V)
Create Product Routings
(VI)
Create Initial Inventory Balances
(VII)
be carried out separately.
Plant
Key uniquely identifying a plant
Your Dallas Plant
Step: 1.1.56: Click Continue .
16: What is the material type of the Touring Wheel Assembly?
17: What is the code for the Trading Goods material type?
“Trading Goods”, NOT “Trading Goods (Planned)”
18: What is the code for the Raw Materials material type?
19: What is the code for the Finished Product material type?
In this section, you create a BOM for your wheel assembly and then create a BOM for your bike.
Chapter 06: Production Master Data
Page 18 of 45
© 2020 Epistemy Press, LLC.
Section 1.5: Create Bills of Materials
Create Materials
(I)
View Inventory Balance
(II)
View Material Inventory
(III)
Display Requirements List
(IV)
Create Bills of Materials
(V)
Create Product Routings
(VI)
Create Initial Inventory Balances
(VII)
Your preview ends here
Eager to read complete document? Join bartleby learn and gain access to the full version
- Access to all documents
- Unlimited textbook solutions
- 24/7 expert homework help
Step: 1.1.57: In the “SAP Easy Access”
screen, follow the navigation path below:
Navigation
SAP Easy Access Menu
Logistics
Production
Master Data
Bills of Material
Bill of Material
Material BOM
Create
20: What is the Transaction Code to create a bill of materials?
21: What is the Transaction Code to display a bill of materials?
22: What is the Transaction Code to change a bill of materials?
Semi-Finished Goods
Step: 1.1.58: In the “Create material BOM: Initial Screen”
screen, enter the following information:
Attribute
Description
Data Value
Material
Key uniquely identifying the material
Your Touring Aluminum Wheel Assembly
Plant
Key uniquely identifying a plant
Your Dallas Plant
BOM Usage
Defines an area where a BOM can be used
Production
Step: 1.1.59: Click Copy .
Step: 1.1.60: In the “Copy From…”
pop-up, enter the following information:
Chapter 06: Production Master Data
Page 19 of 45
© 2020 Epistemy Press, LLC.
Attribute
Description
Data Value
Material Key uniquely identifying the material
Original Touring Aluminum Wheel Assembly
Plant
Key uniquely identifying a plant
Original Dallas Plant Step: 1.1.61: Click Continue (Enter) .
Step: 1.1.62: In the “Create material BOM: Copy From”
screen, click Select All .
Step: 1.1.63: Click Copy .
Step: 1.1.64: In the “Create material BOM: Item: General Data”
screen, enter the following information:
Attribute
Description
Data Value
0010
The first component
Your Touring Tire 0020
The second component
Your Touring Tube 0030
The third component
Your Touring Aluminum Wheel 0040
The fourth component
Your Hex Nut 5 mm 0050
The fifth component
Your Lock Washer 5 mm 0060
The sixth component
Your Socket Head Bolt 5x20mm Step: 1.1.65: Press Enter.
Chapter 06: Production Master Data
Page 20 of 45
© 2020 Epistemy Press, LLC.
23: How many components make up the Touring Wheel Assembly?
24: What is the material code for Your Touring Tube?
25: What is the item category for all the components?
26: How many lock washers are needed in a Touring Wheel Assembly?
27: What is the item number for The Hex Nut?
Step: 1.1.66: Click Save .
You will receive a message that says “Creating BOM for material”.
Finished Good
Step: 1.1.67: In the “Create material BOM: Initial Screen”
screen, enter the following information:
Attribute
Description
Data Value
Material
Key uniquely identifying the material
Your Deluxe Touring Bike (red)
Plant
Key uniquely identifying a plant
Your Dallas Plant
Usage
Defines an area where a BOM can be used
Production
Step: 1.1.68: Click Copy .
Chapter 06: Production Master Data
Page 21 of 45
© 2020 Epistemy Press, LLC.
Your preview ends here
Eager to read complete document? Join bartleby learn and gain access to the full version
- Access to all documents
- Unlimited textbook solutions
- 24/7 expert homework help
Step: 1.1.69: In the “Copy From…”
pop-up, enter the following information:
Attribute
Description
Data Value
Material Key uniquely identifying the material
Original Deluxe Touring Bike (red)
Plant
Key uniquely identifying a plant
Original Dallas Plant
Step: 1.1.70: Click Continue (Enter) .
Step: 1.1.71: In the “Create material BOM: Copy From”
screen, click Select All .
Step: 1.1.72: Click Copy .
In the “Create material BOM: General Item Overview”
screen, enter the following information:
Attribute
Description
Data Value
0010
The first component
Your Touring Aluminum Wheel Assembly 0020
The second component
Your Touring Frame-Red 0030
The third component
Your Derailleur Gear Assembly 0040
The fourth component
Your Touring Seat Kit 0050
The fifth component
Your Touring Handle Bar 0060
The sixth component
Your Pedal Assembly 0070
The seventh component
Your Chain 0080
The eighth component
Your Brake Kit 0090
The ninth component
Your Warranty Document 0100
The tenth component
Your Packaging Chapter 06: Production Master Data
Page 22 of 45
© 2020 Epistemy Press, LLC.
Your preview ends here
Eager to read complete document? Join bartleby learn and gain access to the full version
- Access to all documents
- Unlimited textbook solutions
- 24/7 expert homework help
Change the component (Data Value) using their unique identifier ##.
Step: 1.1.73: Press Enter.
Step: 1.1.74: Click Save .
You will receive a message that says “Creating BOM for material”.
Chapter 06: Production Master Data
Page 23 of 45
© 2020 Epistemy Press, LLC.
Your preview ends here
Eager to read complete document? Join bartleby learn and gain access to the full version
- Access to all documents
- Unlimited textbook solutions
- 24/7 expert homework help
In this section, you copy the product routings for your wheel assembly and your touring bike.
Step: 1.1.75: In the “SAP Easy Access”
screen, follow the navigation path below:
Navigation
SAP Easy Access Menu
Logistics
Production
Master Data
Routings
Routings
Standard Routings
Create
28: What is the Transaction Code to create routings?
29: What is the Transaction Code to change routings?
30: What is the Transaction Code to display routings?
Semi-Finished Good
Chapter 06: Production Master Data
Page 24 of 45
© 2020 Epistemy Press, LLC.
Section 1.6: Create Product Routings
Create Materials
(I)
View Inventory Balance
(II)
View Material Inventory
(III)
Display Requirements List
(IV)
Create Bills of Materials
(V)
Create Product Routings
(VI)
Create Initial Inventory Balances
(VII)
Your preview ends here
Eager to read complete document? Join bartleby learn and gain access to the full version
- Access to all documents
- Unlimited textbook solutions
- 24/7 expert homework help
Step: 1.1.76: In the “Create Routing: Initial Screen”
screen, enter the following information:
Attribute
Description
Data Value
Material Key uniquely identifying the material
Your Touring Aluminum Wheel Assembly
Plant
Key uniquely identifying a plant
Your Dallas Plant
Group
Key identifying a group.
CLEAR OUT (Make sure nothing is in this field)
Ensure the Group Field is Cleared Out
Step: 1.1.77: Click Copy From .
Step: 1.1.78: In the “Select Type”
pop-up, select Routing. Step: 1.1.79: Click Continue (Enter) .
Chapter 06: Production Master Data
Page 25 of 45
© 2020 Epistemy Press, LLC.
Your preview ends here
Eager to read complete document? Join bartleby learn and gain access to the full version
- Access to all documents
- Unlimited textbook solutions
- 24/7 expert homework help
Step: 1.1.80: In the “Create Using Copy Function: Select Object to be Copied”
pop-up, enter the following information:
Attribute
Description
Data Value
Material Key uniquely identifying the material
Original Touring Aluminum Wheel Assembly
Plant
Key uniquely identifying a plant
Original Dallas Plant
Step: 1.1.81: Click Continue (Enter) .
Step: 1.1.82: In the “Create Routing: Header Data Check”
screen, enter the following information:
Attribute
Description
Data Value
Description
Routing description
## Touring Aluminum Wheel Assembly
Overall Status Indicates the processing status of a task list
Released (general)
Step: 1.1.83: Press Enter.
Step: 1.1.84: In the “Create Routing: Operation – Check”
screen, Press Enter to dismiss the “Enter Standard Value Setup”
warning message
Step: 1.1.85: Press Enter to dismiss the “Activity type LABOR is not set up for cost center NA## NAPR10## in the current year”
warning message
Step: 1.1.86: Press Enter to dismiss the “
Activity type LABOR is not set up for cost center NA## NAPR10## in the current year”
warning message
Chapter 06: Production Master Data
Page 26 of 45
© 2020 Epistemy Press, LLC.
Your preview ends here
Eager to read complete document? Join bartleby learn and gain access to the full version
- Access to all documents
- Unlimited textbook solutions
- 24/7 expert homework help
Step: 1.1.87: Continue to Press Enter though the warning messages until you reach the “Create Routing: Operation Overview”
screen.
Step: 1.1.88: In the “Create Routing: Operation Overview”
screen click Save .
You will receive a message that says, “Routing was saved with group”.
Finished Good
Step: 1.1.89: In the “Create Routing: Initial Screen”
screen, enter the following information:
Attribute
Description
Data Value
Material Key uniquely identifying the material
Your Deluxe Touring Bike (red)
Plant
Key uniquely identifying a plant
Your Dallas Plant
Group
Key identifying a group.
CLEAR OUT (Make sure nothing is in this field)
Ensure that the Group Field is cleared out.
Step: 1.1.90: Click Copy From .
Step: 1.1.91: In the “Select Type”
pop-up, select Routing. Step: 1.1.92: Click Continue (Enter)
.
Step: 1.1.93: In the “Create Using Copy Function: Select Object to be Copied”
pop-up, enter the following information:
Chapter 06: Production Master Data
Page 27 of 45
© 2020 Epistemy Press, LLC.
Your preview ends here
Eager to read complete document? Join bartleby learn and gain access to the full version
- Access to all documents
- Unlimited textbook solutions
- 24/7 expert homework help
Attribute
Description
Data Value
Material Key uniquely identifying the material
Original Deluxe Touring Bike (red)
Plant
Key uniquely identifying a plant
Original Dallas Plant
Step: 1.1.94: Click Continue (Enter) .
Step: 1.1.95: In the “Create Routing: Header Data Check”
screen, enter the following information:
Attribute
Description
Data Value
Overall Status Indicates the processing status of a task list
Released (general)
Step: 1.1.96: Press Enter.
Step: 1.1.97: In the “Create Routing: Operation – Check”
screen, Press Enter to dismiss the “Enter Standard Value Setup”
warning message
You will receive this message every time you press enter for every material in the BOM.
Step: 1.1.98: Press Enter to dismiss the “Activity type LABOR is not set up for cost center NA## NAPR10## in the current year”
warning message
Step: 1.1.99: Press Enter to dismiss the “Activity type LABOR is not set up for cost center NA## NAPR10## in the current year”
warning message
Step: 1.1.100: Continue to Press Enter though the warning messages until you reach the “Create Routing: Operation Overview”
screen.
Chapter 06: Production Master Data
Page 28 of 45
© 2020 Epistemy Press, LLC.
Your preview ends here
Eager to read complete document? Join bartleby learn and gain access to the full version
- Access to all documents
- Unlimited textbook solutions
- 24/7 expert homework help
Step: 1.1.101: In the “Create Routing: Operation Overview”
screen, click Save .
You will receive a message that says, “Routing was saved with group”.
31: What is the importance of routings?
Chapter 06: Production Master Data
Page 29 of 45
© 2020 Epistemy Press, LLC.
Your preview ends here
Eager to read complete document? Join bartleby learn and gain access to the full version
- Access to all documents
- Unlimited textbook solutions
- 24/7 expert homework help
In this section, you will create Production Versions for your Touring Wheel Assembly (TRWA10##) and your Deluxe Touring Bike (red) (DXTR30##). Manufacturing BOM determination is only possible with the creation of Production Version master data. You will need to reference your material’s routing to find the group and group counter values.
Step: 1.1.102: In the “SAP Easy Access”
screen, follow the navigation path below:
Navigation
SAP Easy Access Menu
Logistics
Production
Master Data
Routings
Routings
Standard Routings
Display
Step: 1.1.103: In the “Display Routing: Initial Screen”
screen, enter the following information:
Attribute
Description
Data Value
Material
Key identifying your material
Your Touring Wheel Assembly Plant
Key uniquely identifying a plant.
Your Dallas Plant
Group
Groups together several task lists.
CLEARED OUT
Step: 1.1.104: Click Continue .
Step: 1.1.105: In the “Display Routing: Operation Overview”
screen, select Header Data .
Chapter 06: Production Master Data
Page 30 of 45
© 2020 Epistemy Press, LLC.
Section 1.7: Create Production Versions
Your preview ends here
Eager to read complete document? Join bartleby learn and gain access to the full version
- Access to all documents
- Unlimited textbook solutions
- 24/7 expert homework help
32: What is your Touring Wheel Assembly group?
33: What is your Touring Wheel Assembly group counter?
Step: 1.1.106: In the “Display Routing: Header Details” screen, click back two times.
Step: 1.1.107: In the “Display Routing: Initial Screen” enter the following information:
Attribute
Description
Data Value
Material
Key identifying your material
Your Deluxe Touring Bike (red)
Plant
Key uniquely identifying a plant.
Your Dallas Plant
Group
Groups together several task lists
CLEARED OUT
Step: 1.1.108: Click Continue .
Step: 1.1.109: In the “Display Routing: Operation Overview”
screen, select Header Data .
34: What is your Deluxe Touring Bike (red) group?
35: What is your Deluxe Touring Bike (red) group counter?
Step: 1.1.110: In the “SAP Easy Access”
screen
, follow the navigation path below:
Navigation
SAP Easy Access Menu
Logistics
Production
Master Data
Production Versions 36: What is the transaction code to create a production version?
Step: 1.1.111: In the “Production Version: Mass Processing” screen, enter the following information:
Attribute
Description
Data Value
Chapter 06: Production Master Data
Page 31 of 45
© 2020 Epistemy Press, LLC.
Your preview ends here
Eager to read complete document? Join bartleby learn and gain access to the full version
- Access to all documents
- Unlimited textbook solutions
- 24/7 expert homework help
Plant
Key uniquely identifying a plant.
Your Plant Dallas
Material
Key identifying your material
Your Touring Wheel Assembly
Step: 1.1.112: Click Continue .
Step: 1.1.113: In the “Production Version: Mass Processing” screen, in the “
Production Versions”
section
of the screen enter the following information:
Attribute
Description
Data Value
Material
Key identifying your material
Your Touring Wheel Assembly
Production Version
Key identifying your production version
01
Production Version Text
Text describing your Production Version
Touring Wheel Assembly PV
BOM Usage
Key defining the area (such as engineering/design or production) where a BOM can be used
1 Group
Key for task list group found in material routing
Your Touring Wheel Assembly routing group
Group Counter
Helps uniquely identify the task list for the production version of a material
Your Touring Wheel Assembly Group Counter
Type
Key which classifies task lists according to their functionality
Routing
Step: 1.1.114: Click Continue Step: 1.1.115: You will receive a warning message “valid from date is set to current date and valid to date will be set to maximum”
Click Continue .
Step: 1.1.116: Click Continue through the warning message “Check default alternative BOM”
Step: 1.1.117: Click Save .
Chapter 06: Production Master Data
Page 32 of 45
© 2020 Epistemy Press, LLC.
Your preview ends here
Eager to read complete document? Join bartleby learn and gain access to the full version
- Access to all documents
- Unlimited textbook solutions
- 24/7 expert homework help
You will not receive a confirmation message; however, you will now be able to perform the production process for your Touring Wheel Assembly.
Step: 1.1.118: In the “Production Version: Mass Processing” screen, enter the following information:
Attribute
Description
Data Value
Plant
Key uniquely identifying a plant.
Your Plant Dallas
Material
Key identifying your material
Your Deluxe Touring Bike (red)
MRP Controller
MRP Controller responsible for material planning for the material.
Your DL Controller
Step: 1.1.119: Click Continue .
Step: 1.1.120: In the “Production Version: Mass Processing” screen in the “
Production Version”
section of the screen enter the following information:
Attribute
Description
Data Value
Material
Key identifying your material
Your Deluxe Touring Bike (red)
Production Version
Key identifying your production version
01
Production Version Short Text
Text describing your Production Version
Deluxe Touring Bike (red) PV
BOM Usage
Key defining the area (such as engineering/design or production) where a BOM can be used
1 Group
Key for task list group found in material routing
Your Deluxe Touring Bike (red) routing group
Group Counter
Helps uniquely identify the task list for the production
version of a material
Your Deluxe Touring Bike Red group counter
Type
Key which classifies task lists according to their functionality
Routing
Chapter 06: Production Master Data
Page 33 of 45
© 2020 Epistemy Press, LLC.
Your preview ends here
Eager to read complete document? Join bartleby learn and gain access to the full version
- Access to all documents
- Unlimited textbook solutions
- 24/7 expert homework help
Step: 1.1.121: Click Continue Step: 1.1.122: You will receive a warning message “valid from date is set to current date and valid to date will be set to maximum”
click Continue .
Step: 1.1.123: Click Continue through the warning message “Check default alternative BOM”
.
Step: 1.1.124: Click Save .
You will not receive a confirmation message; however, you will now be able to perform the production process for your Deluxe Touring Bike (red).
Chapter 06: Production Master Data
Page 34 of 45
© 2020 Epistemy Press, LLC.
Your preview ends here
Eager to read complete document? Join bartleby learn and gain access to the full version
- Access to all documents
- Unlimited textbook solutions
- 24/7 expert homework help
Normally, the material planning process would create purchase requisitions for the necessary raw materials. You would then execute the procurement process and obtain these materials. For this exercise (and simplicity reasons), we will take a shortcut and create “inventory from heaven”.
Use the table below to calculate how many of the different materials are needed to make ten bikes. The first three columns include the material description, material number, and the quantity needed for one bike. Complete the remaining columns as follows:
Item
Description
Number
Quantity for 1 Bike
Qty. Needed for 10 Bikes
1
Brake Kit
BRKT10##
1
2
Chain
CHAN10##
1
3
Derailleur Gear Assembly
DGAM10##
1
4
Hex Nut 5 mm
HXNT10##
2
5
Lock Washer 5 mm
LWSH10##
4
6
Packaging
PCKG10##
1
7
Pedal Assembly
PEDL10##
1
Chapter 06: Production Master Data
Page 35 of 45
© 2020 Epistemy Press, LLC.
Section 1.8: Create Initial Inventory Balance
Create Materials
(I)
View Inventory Balance
(II)
View Material Inventory
(III)
Display Requirements List
(IV)
Create Bills of Materials
(V)
Create Product Routings
(VI)
Create Initial Inventory Balances
(VII)
Your preview ends here
Eager to read complete document? Join bartleby learn and gain access to the full version
- Access to all documents
- Unlimited textbook solutions
- 24/7 expert homework help
8
Socket Head Bolt 5x20mm
BOLT10##
2
9
Touring Aluminum Wheel
TRWH10##
2
10
Touring Frame-Red
TRFR30##
1
11
Touring Handlebar
TRHB10##
1
12
Touring Seat Kit
TRSK10##
1
13
Touring Tire
TRTR10##
2
14
Touring Tube
TRTB10##
2
15
Warranty Document
WDOC10##
1
Chapter 06: Production Master Data
Page 36 of 45
© 2020 Epistemy Press, LLC.
Your preview ends here
Eager to read complete document? Join bartleby learn and gain access to the full version
- Access to all documents
- Unlimited textbook solutions
- 24/7 expert homework help
Step: 1.1.125: In the “SAP Easy Access”
screen, follow the navigation path below:
Navigation
SAP Menu
Logistics
Materials Management
Inventory Management
Goods Movement
Goods Movement
37: What is the T-code to create “inventory from heaven”?
Step: 1.1.126: In the “Goods Receipt Purchase Order”
screen, enter the following information:
Attribute
Description
Data Value
Trans/Event
Drop-down menu
Goods Receipt
Reference Document
Indicates the document you want to reference when you enter the transaction
Other
Receipt w/o PO (Movement Type )
Specifies a key for the type of goods movement
561
Step: 1.1.127: Press Enter. Step: 1.1.128: In the “Tip” pop-up, click Continue (Enter) .
Chapter 06: Production Master Data
Page 37 of 45
© 2020 Epistemy Press, LLC.
Your preview ends here
Eager to read complete document? Join bartleby learn and gain access to the full version
- Access to all documents
- Unlimited textbook solutions
- 24/7 expert homework help
Step: 1.1.129: In the “Goods Receipt Other”
screen, enter the following information:
Mat. Short Text
Quantity in UnE
E
SLoc
Plnt
BOLT10##
20
EA
Raw Materials Your Plant Dallas BRKT10##
10
EA
Raw Materials
Your Plant Dallas CHAN10##
10
EA
Raw Materials
Your Plant Dallas DGAM10##
10
EA
Raw Materials
Your Plant Dallas HXNT10##
20
EA
Raw Materials
Your Plant Dallas LWSH10##
40
EA
Raw Materials
Your Plant Dallas PCKG10##
10
EA
Raw Materials
Your Plant Dallas PEDL10##
10
EA
Raw Materials
Your Plant Dallas TRFR30##
10
EA
Raw Materials
Your Plant Dallas TRHB10##
10
EA
Raw Materials
Your Plant Dallas TRSK10##
10
EA
Raw Materials
Your Plant Dallas TRTB10##
20
EA
Raw Materials
Your Plant Dallas TRTR10##
20
EA
Raw Materials
Your Plant Dallas TRWH10##
20
EA
Raw Materials
Your Plant Dallas WDOC10##
10
EA
Raw Materials
Your Plant Dallas Step: 1.1.130: Press Enter.
Step: 1.1.131: Click Post . You will receive a message that says, “Material document 49………… posted”.
Chapter 06: Production Master Data
Page 38 of 45
© 2020 Epistemy Press, LLC.
Your preview ends here
Eager to read complete document? Join bartleby learn and gain access to the full version
- Access to all documents
- Unlimited textbook solutions
- 24/7 expert homework help
Step: 1.1.132: Refer to a previous step for instructions on how to view your material inventory. Make
sure you have the correct amount of inventory for each item.
38: How many of Your Touring Frames-Red are in inventory after the movement?
39: What is the total United States dollar value of Touring Frames-Red in inventory?
Chapter 06: Production Master Data
Page 39 of 45
© 2020 Epistemy Press, LLC.
Your preview ends here
Eager to read complete document? Join bartleby learn and gain access to the full version
- Access to all documents
- Unlimited textbook solutions
- 24/7 expert homework help
Part 2 - Exercise Deliverables
Name:
Course and Section:
Identifier:
Client:
Chapter 06: Production Master Data
Page 40 of 45
© 2020 Epistemy Press, LLC.
Your preview ends here
Eager to read complete document? Join bartleby learn and gain access to the full version
- Access to all documents
- Unlimited textbook solutions
- 24/7 expert homework help
1: What is the Transaction Code to create a general material immediately?
2: What is the Transaction Code to change a material immediately?
3: What is the Transaction Code to display a current material?
4: What is the Transaction Code to display a material’s inventory level?
5: How many Touring Frames-Red are in unrestricted use?
6: How many Touring Frames-Red are in reserved stock?
7: How many Touring Frames-Red are in on-order stock?
8: What is the Transaction Code to display a material’s inventory level?
9: What is the code for Your Raw Material Storage Location?
10: What is the code for Your Semi-Finished Goods Storage Location?
11: What is the code for Your Finished Goods Storage Location?
12: What is the total United States dollar value of Raw Materials in your inventory?
13: How many of Your Gear Assemblies are there in inventory?
14: What is the material code for Your Warranty Document?
Chapter 06: Production Master Data
Page 41 of 45
© 2020 Epistemy Press, LLC.
Your preview ends here
Eager to read complete document? Join bartleby learn and gain access to the full version
- Access to all documents
- Unlimited textbook solutions
- 24/7 expert homework help
15: What is the Transaction Code to display a stock/requirements list?
16: What is the material type of the Touring Wheel Assembly?
17: What is the code for the Trading Goods material type?
18: What is the code for the Raw materials material type?
19: What is the code for the Finished Product material type?
20: What is the Transaction Code to create a bill of materials?
21: What is the Transaction Code to display a bill of materials?
22: What is the Transaction Code to change a bill of materials?
23: How many components make up the Touring Wheel Assembly?
24: What is the material code for Your Touring Tube?
25: What is the item category for all the components?
26: How many Lock Washers are needed in a Touring Wheel Assembly?
27: What is the item number for the Hex Nut?
28: What is the Transaction Code to create routings?
29: What is the Transaction Code to change routings?
30: What is the Transaction Code to display routings?
Chapter 06: Production Master Data
Page 42 of 45
© 2020 Epistemy Press, LLC.
Your preview ends here
Eager to read complete document? Join bartleby learn and gain access to the full version
- Access to all documents
- Unlimited textbook solutions
- 24/7 expert homework help
31: What is the importance of routings?
32: What is your Touring Wheel Assembly group?
33: What is your Touring Wheel Assembly group counter?
34: What is your Deluxe Touring Bike (red) group?
35: What is your Deluxe Touring Bike (red) group counter?
36: What is the transaction code to create a production version?
37: What is the Transaction Code to create inventory from heaven?
38: How many of Your Touring Frames-Red are in inventory after the movement?
39: What is the total United States dollar value of Touring Frames-Red in inventory?
Chapter 06: Production Master Data
Page 43 of 45
© 2020 Epistemy Press, LLC.
Your preview ends here
Eager to read complete document? Join bartleby learn and gain access to the full version
- Access to all documents
- Unlimited textbook solutions
- 24/7 expert homework help
Description
Number
Your Number
Type
Your S.L.
Brake Kit
BRKT1000
BRKT10##
Raw
RM##
Chain
CHAN1000
CHAN10##
Raw
RM##
Derailleur Gear Assembly
DGAM1000
DGAM10##
Raw
RM##
Hex Nut 5 mm
HXNT1000
HXNT10##
Raw
RM##
Lock Washer 5 mm
LWSH1000
LWSH10##
Raw
RM##
Packaging
PCKG1000
PCKG10##
Raw
RM##
Pedal Assembly
PEDL1000
PEDL10##
Raw
RM##
Socket Head Bolt 5x20mm
BOLT1000
BOLT10##
Raw
RM##
Touring Aluminum Wheel
TRWH1000
TRWH10##
Raw
RM##
Touring Frame-Red
TRFR3000
TRFR30##
Raw
RM##
Touring Handle Bar
TRHB1000
TRHB10##
Raw
RM##
Touring Seat Kit
TRSK1000
TRSK10##
Raw
RM##
Touring Tire
TRTR1000
TRTR10##
Raw
RM##
Touring Tube
TRTB1000
TRTB10##
Raw
RM##
Warranty Document
WDOC1000
WDOC10##
Raw
RM##
Chapter 06: Production Master Data
Page 44 of 45
© 2020 Epistemy Press, LLC.
Your preview ends here
Eager to read complete document? Join bartleby learn and gain access to the full version
- Access to all documents
- Unlimited textbook solutions
- 24/7 expert homework help
Touring Aluminum Wheel Assembly
TRWA1000
TRWA10##
Semi.
SF##
Deluxe Touring Bike (red)
DXTR3000
DXTR30##
Fin.
FG##
Chapter 06: Production Master Data
Page 45 of 45
© 2020 Epistemy Press, LLC.
Your preview ends here
Eager to read complete document? Join bartleby learn and gain access to the full version
- Access to all documents
- Unlimited textbook solutions
- 24/7 expert homework help
Related Documents
Related Questions
DOCUMENT FLOWCHARTPrepare a flowchart that illustrates the sequence in which the followingsource documents are prepared.a. Bill of materialsb. Sales forecastc. Materials requisitiond. More tickete. Production schedulef. Route sheetg. Work orde
arrow_forward
1. DOCUMENT FLOWCHART Prepare a flowchart that illustrates the sequence in which the following source documents are prepared.
a. Bill of materials
b. Work order
c. Sales forecast
d. Materials requisition
e. Move ticket
f. Production schedule
g. Route sheet
arrow_forward
Help question 6
arrow_forward
Question#5
Match the items in the two columns below by entering the appropriate code letter in the space provided.A. Managerial accounting F. Work in process inventoryB. Financial accounting G. Direct materialsC. Planning H. Manufacturing overheadD. Directing I. Period costsE. Controlling J. Value chain1. The cost of products that are partially complete.2. The function of keeping activities in accordance with plans. 3. Primarily concerned with internal users and reports pertain to subunits of the entity.4. Materials that can be physically and directly associated with manufacturing a product. 5. The function of setting goals and objectives.6. Indirect costs of manufacturing a product.7. Primarily concerned with external users and reports pertain to the entity as a whole.8. Costs that are noninventoriable.9. All business processes…
arrow_forward
DESIGN AND DOCUMENT MANUFACTURING PROCESSESDesign and document with a system flowchart a computer-based manufacturingprocess that possesses the information flows of the manual systems depicted inFigures 7-9 and 7-13. Assume that the manufacturing process is triggered by amonthly sales forecast, which is received periodically from the marketing departmentin digital form. Further assume that all functional areas (work centers, storekeeping,inventory control, etc.) employ terminals that are networked to a centralized dataprocessing function. Your system design should minimize hard-copy documents
arrow_forward
Please dont provide solution image based thanks
arrow_forward
Upload Assignment: Module 4 Ex
* CengageNOwv2 | Online teachin x
un/takeAssignment/takeAssignmentMain.do?invoker =&takeAssignmentSessionLocator &inprogress-false
O eBook
Cost of Units Completed and in Process
The charges to Work in Process-Assembly Department for a period, together with information concerning production, are as follows. All direct materials are placed in process at the
beginning of production.
Work in Process-Assembly Department
Bal., 2,000 units, 35% completed
5,440
To Finished Goods, 46,000 units
Direct materials, 47,000 units @ $1.6
75,200
Direct labor
114,200
Factory overhead
44,410
Bal. 2 units, 45% completed
a. Based on the above data, determine the different costs listed below.
If required, round your interim calculations to two decimal places.
1. Cost of beginning work in process inventory completed this period.
2. Cost of units transferred to finished goods during the period.
24
3. Cost of ending work in process inventory.
4. Cost per unit of the completed…
arrow_forward
X
Paste
Clipboard
FILE
H5
1. Compute a predetermined overhead rate.
2. Prepare schedules of cost of goods manufactured and cost of goods sold.
15
56
HOME
A
Calibri
의
INSERT
BI U ▾
11
12
13
14 Inventories:
1
9 Actual costs for the year:
10
READY
▾
Font
6 Estimated total direct labor hours
7 Actual total direct labor hours
8
Raw materials (all direct)
16
Work in process
17 Finished goods
18
11
B
с
1 Stanford Enterprises uses job-order costing.
2 The allocation base for overhead is direct labor hours.
3
4
Data for the year just ended:
5 Estimated total manufacturing overhead cost
PAGE LAYOUT
Cost of Goods Manufactured and Cost of Goods Sold - Excel
DATA REVIEW VIEW
A A
Purchase of raw materials (all direct)
Direct labor cost
Manufacturing overhead costs
fx
19 Use the data to answer the following.
20
Predetermined overhead rate
Actual direct labor hours
Sheet1
G
FORMULAS
%
Alignment Number
D
Beginning
$
$
$
Conditional Format as Cell
Formatting Table Styles
Styles
E
T
$ 275,000
25,000…
arrow_forward
Chapter 20, Question 2. Part 1. Attached are possible answers for second part.
arrow_forward
choose correct ans
arrow_forward
I want last three requirement with detail working
I want last three requirement with detail working
I want last three requirement with detail working
please answer within the format by providing formula the detailed workingPlease provide answer in text (Without image)Please provide answer in text (Without image)Please provide answer in text (Without image)
arrow_forward
To make changes to inventory levels, you click on
O materials buffer icon
O customer orders icon
O job completion icon
Ostation queues icon
?
arrow_forward
Describe the step-by-step processes that are occurring in the flowchart. Describe using bullet points.
arrow_forward
Multiple choice
arrow_forward
Cost of Materials Issuances Under the FIFO Method
An incomplete subsidiary ledger of materials inventory for May is as follows:
a. Complete the materials isuances and balances for the materials subsidiary ledger under FIFO.
Received
Issued
Balance
Receiving
Materials
Unit
Unit
Report
Quantity
Requisition
Quantity
Amount
Date
Quantity
Amount
Price
price
Number
Number
May 1
260
$8
$2,080
25
$10
260 V
2,080 V
180
May 4
180 V
10 V
1,800
103
290
May 10
10 V
31
120
12
May 21
10 V
12 V
116
170
May 27
12
Feedback
V Check My Work
a. Calculate the amount of each materials issue, using FIFO. In the Balance section, separate each different unit price and its quantity.
b. Determine the materials inventory balance at the end of May.
Feedback
V Check My Work
b. Calculate the amount of each materials issue, using FIFO. In the Balance section, separate each different unit price and its quantity.
arrow_forward
help please answer in text form with proper workings and explanation for each and every part and steps with concept and introduction no AI no copy paste remember answer must be in proper format with all working
arrow_forward
Question 14
Sarah would like to create a new custom management report for her
client.
How would she accomplish this?
Create a new template under Custom reports and save to Management
reports
O Copy an existing template under Management reports
Create a new template under Management reports
Copy an existing template under Custom reports and save to Management
reports
arrow_forward
Do not use chatgpt
arrow_forward
Pares
arrow_forward
Please do not give solution in image format thanku
arrow_forward
Exercise 16-44 (Algo) (Appendix used in requirement [b]) Variable Cost Variances (LO 16-5, 7)
Rankin Fabrication reports the following information with respect to its direct materials:
Actual quantities of direct materials used
Actual costs of direct materials used.
Standard price per unit of direct materials.
Flexible budget for direct materials.
Rankin Fabrication holds no materials inventories.
35,500 gallons
$ 201,680
$ 5.79
$ 213,100
Required:
a. Compute the direct material price and efficiency variances.
b. (Appendix) Prepare the journal entries to record the purchase and use of the direct materials using standard costing.
Direct materials price variance
Direct materials efficiency variance
Complete this question by entering your answers in the tabs below.
Required A Required B
Compute the direct material price and efficiency variances.
Note: Indicate the effect of each variance by selecting "F" for favorable, or "U" for unfavorable. If there is no effect, do not
select either…
arrow_forward
SEE MORE QUESTIONS
Recommended textbooks for you
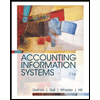
Accounting Information Systems
Finance
ISBN:9781337552127
Author:Ulric J. Gelinas, Richard B. Dull, Patrick Wheeler, Mary Callahan Hill
Publisher:Cengage Learning
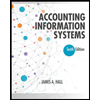
Accounting Information Systems
Accounting
ISBN:9781337619202
Author:Hall, James A.
Publisher:Cengage Learning,
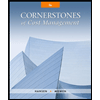
Cornerstones of Cost Management (Cornerstones Ser...
Accounting
ISBN:9781305970663
Author:Don R. Hansen, Maryanne M. Mowen
Publisher:Cengage Learning
Related Questions
- DOCUMENT FLOWCHARTPrepare a flowchart that illustrates the sequence in which the followingsource documents are prepared.a. Bill of materialsb. Sales forecastc. Materials requisitiond. More tickete. Production schedulef. Route sheetg. Work ordearrow_forward1. DOCUMENT FLOWCHART Prepare a flowchart that illustrates the sequence in which the following source documents are prepared. a. Bill of materials b. Work order c. Sales forecast d. Materials requisition e. Move ticket f. Production schedule g. Route sheetarrow_forwardHelp question 6arrow_forward
- Question#5 Match the items in the two columns below by entering the appropriate code letter in the space provided.A. Managerial accounting F. Work in process inventoryB. Financial accounting G. Direct materialsC. Planning H. Manufacturing overheadD. Directing I. Period costsE. Controlling J. Value chain1. The cost of products that are partially complete.2. The function of keeping activities in accordance with plans. 3. Primarily concerned with internal users and reports pertain to subunits of the entity.4. Materials that can be physically and directly associated with manufacturing a product. 5. The function of setting goals and objectives.6. Indirect costs of manufacturing a product.7. Primarily concerned with external users and reports pertain to the entity as a whole.8. Costs that are noninventoriable.9. All business processes…arrow_forwardDESIGN AND DOCUMENT MANUFACTURING PROCESSESDesign and document with a system flowchart a computer-based manufacturingprocess that possesses the information flows of the manual systems depicted inFigures 7-9 and 7-13. Assume that the manufacturing process is triggered by amonthly sales forecast, which is received periodically from the marketing departmentin digital form. Further assume that all functional areas (work centers, storekeeping,inventory control, etc.) employ terminals that are networked to a centralized dataprocessing function. Your system design should minimize hard-copy documentsarrow_forwardPlease dont provide solution image based thanksarrow_forward
- Upload Assignment: Module 4 Ex * CengageNOwv2 | Online teachin x un/takeAssignment/takeAssignmentMain.do?invoker =&takeAssignmentSessionLocator &inprogress-false O eBook Cost of Units Completed and in Process The charges to Work in Process-Assembly Department for a period, together with information concerning production, are as follows. All direct materials are placed in process at the beginning of production. Work in Process-Assembly Department Bal., 2,000 units, 35% completed 5,440 To Finished Goods, 46,000 units Direct materials, 47,000 units @ $1.6 75,200 Direct labor 114,200 Factory overhead 44,410 Bal. 2 units, 45% completed a. Based on the above data, determine the different costs listed below. If required, round your interim calculations to two decimal places. 1. Cost of beginning work in process inventory completed this period. 2. Cost of units transferred to finished goods during the period. 24 3. Cost of ending work in process inventory. 4. Cost per unit of the completed…arrow_forwardX Paste Clipboard FILE H5 1. Compute a predetermined overhead rate. 2. Prepare schedules of cost of goods manufactured and cost of goods sold. 15 56 HOME A Calibri 의 INSERT BI U ▾ 11 12 13 14 Inventories: 1 9 Actual costs for the year: 10 READY ▾ Font 6 Estimated total direct labor hours 7 Actual total direct labor hours 8 Raw materials (all direct) 16 Work in process 17 Finished goods 18 11 B с 1 Stanford Enterprises uses job-order costing. 2 The allocation base for overhead is direct labor hours. 3 4 Data for the year just ended: 5 Estimated total manufacturing overhead cost PAGE LAYOUT Cost of Goods Manufactured and Cost of Goods Sold - Excel DATA REVIEW VIEW A A Purchase of raw materials (all direct) Direct labor cost Manufacturing overhead costs fx 19 Use the data to answer the following. 20 Predetermined overhead rate Actual direct labor hours Sheet1 G FORMULAS % Alignment Number D Beginning $ $ $ Conditional Format as Cell Formatting Table Styles Styles E T $ 275,000 25,000…arrow_forwardChapter 20, Question 2. Part 1. Attached are possible answers for second part.arrow_forward
- choose correct ansarrow_forwardI want last three requirement with detail working I want last three requirement with detail working I want last three requirement with detail working please answer within the format by providing formula the detailed workingPlease provide answer in text (Without image)Please provide answer in text (Without image)Please provide answer in text (Without image)arrow_forwardTo make changes to inventory levels, you click on O materials buffer icon O customer orders icon O job completion icon Ostation queues icon ?arrow_forward
arrow_back_ios
SEE MORE QUESTIONS
arrow_forward_ios
Recommended textbooks for you
- Accounting Information SystemsFinanceISBN:9781337552127Author:Ulric J. Gelinas, Richard B. Dull, Patrick Wheeler, Mary Callahan HillPublisher:Cengage LearningAccounting Information SystemsAccountingISBN:9781337619202Author:Hall, James A.Publisher:Cengage Learning,Cornerstones of Cost Management (Cornerstones Ser...AccountingISBN:9781305970663Author:Don R. Hansen, Maryanne M. MowenPublisher:Cengage Learning
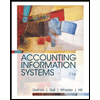
Accounting Information Systems
Finance
ISBN:9781337552127
Author:Ulric J. Gelinas, Richard B. Dull, Patrick Wheeler, Mary Callahan Hill
Publisher:Cengage Learning
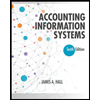
Accounting Information Systems
Accounting
ISBN:9781337619202
Author:Hall, James A.
Publisher:Cengage Learning,
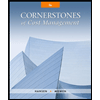
Cornerstones of Cost Management (Cornerstones Ser...
Accounting
ISBN:9781305970663
Author:Don R. Hansen, Maryanne M. Mowen
Publisher:Cengage Learning