please. Mention important parts. Also, you will put your comments and ideas about the topic. Do not write item by item. Please I really need help
please. Mention important parts. Also, you will put your comments and ideas about the topic. Do not write item by item. Please I really need help
Principles Of Marketing
17th Edition
ISBN:9780134492513
Author:Kotler, Philip, Armstrong, Gary (gary M.)
Publisher:Kotler, Philip, Armstrong, Gary (gary M.)
Chapter1: Marketing: Creating Customer Value And Engagement
Section: Chapter Questions
Problem 1.1DQ
Related questions
Question
Business question
Read the pages and make a summary of them with your own words, please. Mention important parts. Also, you will put your comments and ideas about the topic. Do not write item by item. Please I really need help
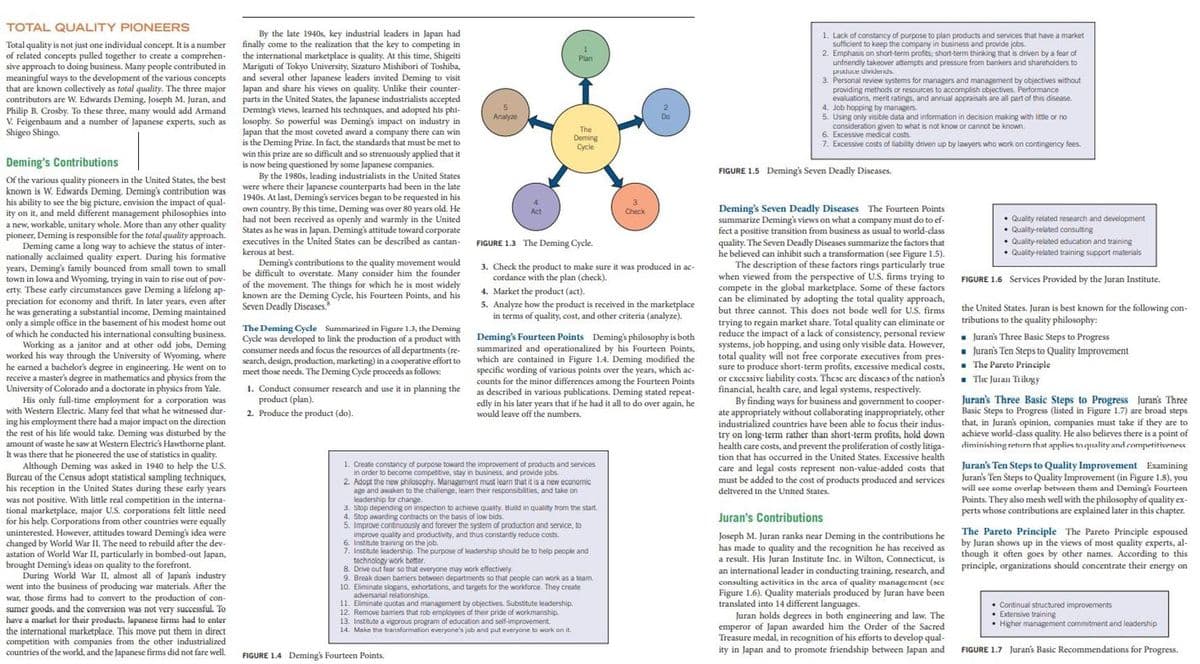
Transcribed Image Text:receive
n 1940 to neip the U.S.
TOTAL QUALITY PIONEERS
Total quality is not just one individual concept. It is a number
of related concepts pulled together to create a comprehen-
sive approach to doing business. Many people contributed in
meaningful ways to the development of the various concepts
that are known collectively as total quality. The three major
contributors are W. Edwards Deming, Joseph M. Juran, and
Philip B. Crosby. To these three, many would add Armand
V. Feigenbaum and a number of Japanese experts, such as
Shigeo Shingo.
By the late 1940s, key industrial leaders in Japan had
finally come to the realization that the key to competing in
the international marketplace is quality. At this time, Shigeiti
Mariguti of Tokyo University, Sizaturo Mishibori of Toshiba,
and several other Japanese leaders invited Deming to visit
counter-
Japanese industrialists accepted
Demings views, learned his techniques, and adopted his phi-
losophy. So powerful was Deming's impact on industry in
Japan that the most coveted award a company there can win
is the Deming Prize. In fact, the standards that must be met to
so difficult and so strenuously applied that it
1. Lack of constancy of purpose to plan products and services that have a market
sufficient to keep the company in business and provide jobs.
2. Emphasis on short-term profits; short-term thinking that is diven by a fear of
unfriendly takeover attempts and pressure from bankers and shareholders to
produce dividerds.
3. Personal review systems for managers and management by objectives without
providing methods or resources to accomplish objectives. Performance
evaluations, merit ratings, and annual appraisals are all part of this disease.
4. Job hopping by managers.
5. Using only visibie data and information in decision making with little or no
consideration given to what is not know or cannot be known.
6. Excessive medical costs.
7. Excessive costs of liability driven up by lawyers who work on contingency fees.
Plan
Japan and share his views on quality. Unlik
parts in the United States, the
Analyze
The
Deming
Cycle
win this
s prize are
Deming's Contributions
Of the various quality pioneers in the United States, the best
known is W. Edwards Deming. Deming's contribution was
his ability to see the big picture, envision the impact of qual-
ity on it, and meld different management philosophies into
a new, workable, unitary whole. More than any other
pioneer, Deming is responsible for the total quality approach.
Deming came a long way
nationally acclaimed quality
years, Deming's family bounced from small
town in lowa and Wyoming, trying in vain to rise out of pov-
is now being questioned by some Japanese companies.
FIGURE 1.5 Deming's Seven Deadly Diseases.
By the 1980s,
where their Japanese counterparts
1940s. At last, Deming's services began to be requested in his
4.
Act
own country. By this time, Deming was over 80 years old. He
had not been received as openly and warmly in the United
States as he was in Japan. Deming's attitude toward corporate
Deming's Seven Deadly Diseases The Fourteen Points
summarize Deming's views on what a company must do to ef-
fect a positive transition from business as usual to world-cdass
quality. The Seven Deadly Discases summarize the factors that
he believed can inhibit such a transformation (see Figure 1.5).
The description of these factors rings particularly true
when viewed from
Check
• Quality related research and development
• Quality-related consulting
• Quality-related education and training
• Quality-related training support materials
quality
executives in the United States can be described as cantan-
kerous at best,
Deming's contributions to the quality movement would
be difficult to overstate. Many consider him the founder
of the movement. The things for which he is most widely
known are the Deming Cycle, his Fourteen Points, and his
Seven Deadly Diseases.
FIGURE 1.3 The Deming Cycle.
to achieve the status of inter-
his formative
еxpert.
3. Check the product to make sure it was produced in ac-
cordance with the plan (check).
Itown
to small
rom the perspective of U.S. firms trying to
FIGURE 1.6 Services Provided by the Juran Institute.
erty. These
preciation for economy and thrift. In later years, even after
he was generating a substantial income, Deming maintained
only a simple office in the basement of his modest home out
of which he conducted his international consulting business.
Working as a janitor and at other odd jobs, Deming
worked his way through the University of Wyoming, where
be carned a bachelor's degree in engineering.
re a master's degree in mathematics and physics from the
compete in the global marketplace. Some of these factors
can be eliminated by adopting
but three cannot. This does not bode well for U.S. firms
trying to regain market share. Total quality can eliminate or
reduce the impact of a lack of consistency, personal review
systems, job hopping, and using only visible data. However,
total quality will not free corporate executives from pres-
sure to produce short-term profits, excessive medical costs,
carly
circumstances gave Deming a lifelong ap-
4. Market the product (act).
5. Analyze how the product is received in the marketplace
in terms of quality, cost, and other criteria (analyze).
total quality approach,
the United States. Juran is best known for the following con-
tributions to the quality philosophy:
The Deming Cycle Summarized in Figure 1.3, the Deming
Cycle was developed to link the production of a product with
consumer needs and focus the resources of all departments (re-
inere
Deming's Fourteen Points Deming's philosophy is both
summarized and operationalized by his Fourteen Points,
which are contained in Figure 1.4. Deming modified the
specific wording of various points over the years, which ac-
counts for the minor differences among the Fourteen Points
as described in various publications. Deming stated repeat-
edly in his later years that if he had it all to do over again, he
would leave off the numbers.
- Juran's Three Basic Steps to Progress
1 Juran's Ten Steps to Quality Improvement
- The Pareto Principle
- Tlhe Juran Tiilogy
search, design, production, marketing) in a cooperative effort to
meet those needs. The Deming Cycle proceeds as follows:
He
went on to
or cxccssive liability
costs. Thesc are discascs of the nation's
financial, health care, and legal systems, respectively.
By finding ways for business and government to cooper-
ate appropriately without collaborating inappropriately,
industrialized countries have been able to focus their indus-
try on long-term rather than short-term profits, hold down
health care costs, and prevent the proliferation of costly litiga-
tion that has occurred in the United States. Excessive health
care and legal costs represent non-value-added costs that
must be added to the cost of products produced and services
deltvered in the United States.
of Colorado and a doctorate in physics from Yale.
l-time employment for
1. Conduct consumer research and use it in planning the
product (plan).
2. Produce the product (do).
Juran's Three Basic Steps to Progress Juran's Three
Basic Steps to Progress (listed in Figure 1.7) are broad steps
that, in Juran's opinion, companies must take if they are to
achieve world-class quality. He also believes there is a point of
diminishing return that applies to quality and competitiveness
His only
with Western Electric. Many feel that what he
ing his employment there had a major impact on the direction
the rest of his life would take. Deming was disturbed by the
amount of waste he saw at Western Electric's Hawthorne plant.
It was there that he pioneered the use of statistics in quality.
Although
Bureau of the Census adopt
his reception in the United States during these early years
was not positive. With little real competition in the interna-
tional marketplace, major U.S. corporations felt little need
fo
full-
a corporation was
witnessed
I dur-
other
asked in 1940 to
statistical sampling
1. Create constancy of purpose toward the improvement of products and services
in order to become competitive, stay in business, and provide jobs
2. Adopt the new philosophy. Managernent must learn that it is a new economic
age and awaken to the challenge, learn their responsibiities, and take on
leadership for change.
3. Stop depending on inspection to achieve quality. Build in quality trom the start.
4. Stop awarding contracts on the basis of low bids.
5. Improve continuously and forever the system of production and service, to
improve quality and productivity, and thus constantly reduce costs.
6. Institute training on the job.
7. Institute leadership. The purpose of leadership should be to help people and
technology work better.
8. Drive out fear so that everyone may work effectively.
9. Break down bamers between departments so that people can work as a team.
10. Eliminate slogans, exhortations, and targets for the workforce. They create
adversarial relationships.
11. Eliminate quotas and management by objectives. Substitute leadership.
12. Remove bariers that rob employees of their pride of workmanship.
13. Institute a vigorous program of education and self-improvement
14. Make the transformation everyone's job and put everyone to work on it.
Juran's Ten Steps to Quality Improvement Examining
Juran's Ten Steps to Quality Improvement (in Figure 1.8), you
will see some overlap between them and Deming's Fourteen
Points. They also mesh well with the philosophy of quality ex-
perts whose contributions are explained later in this chapter.
Deming was
the US.
techniques,
Juran's Contributions
his help. Corporations from other countries were equally
uninterested. However, attitudes toward Deming's idea were
changed by World War II. The need to rebuild after the dev-
astation of World War II, particularly in bombed-out Japan,
brought Deming's ideas on quality to the forefront.
During World War II, almost all of Japan's industry
went into the business of producing war materials. After the
war, those firms had to convert to the production of con-
Joseph M. Juran ranks near Deming in the contributions he
has made to quality and the recognition he has received as
a result. His Juran Institute Inc. in Wilton, Connecticut, is
an international leader in conducting training, research, and
consulting activitics in the arca of quality management (sce
Figure 1.6). Quality materials produced by Juran have been
translated into 14 different languages.
Juran holds degrees in both engineering and law. The
emperor of Japan awarded him the Order of the Sacred
Treasure medal, in recognition of his efforts to develop qual-
ity in Japan and to promote friendship between Japan and
The Pareto Principle The Pareto Principle espoused
by Juran shows up in the views of most quality experts, al-
though it often goes by other names. According to this
principle, organizations should concentrate their energy on
• Continual structured improvements
• Extersive training
• Higher management commitment and leadership
sumer goods, and the conversion was not very successful. To
have a market tor their products, Japanese firma had to enter
the international marketplace. This move put them in direct
competition with companies from the other industrialized
countries of the world, and the Japanese firms did not fare well.
FIGURE 1.7 Juran's Basic Recommendations for Progress.
FIGURE 1.4 Deming's Fourteen Points.
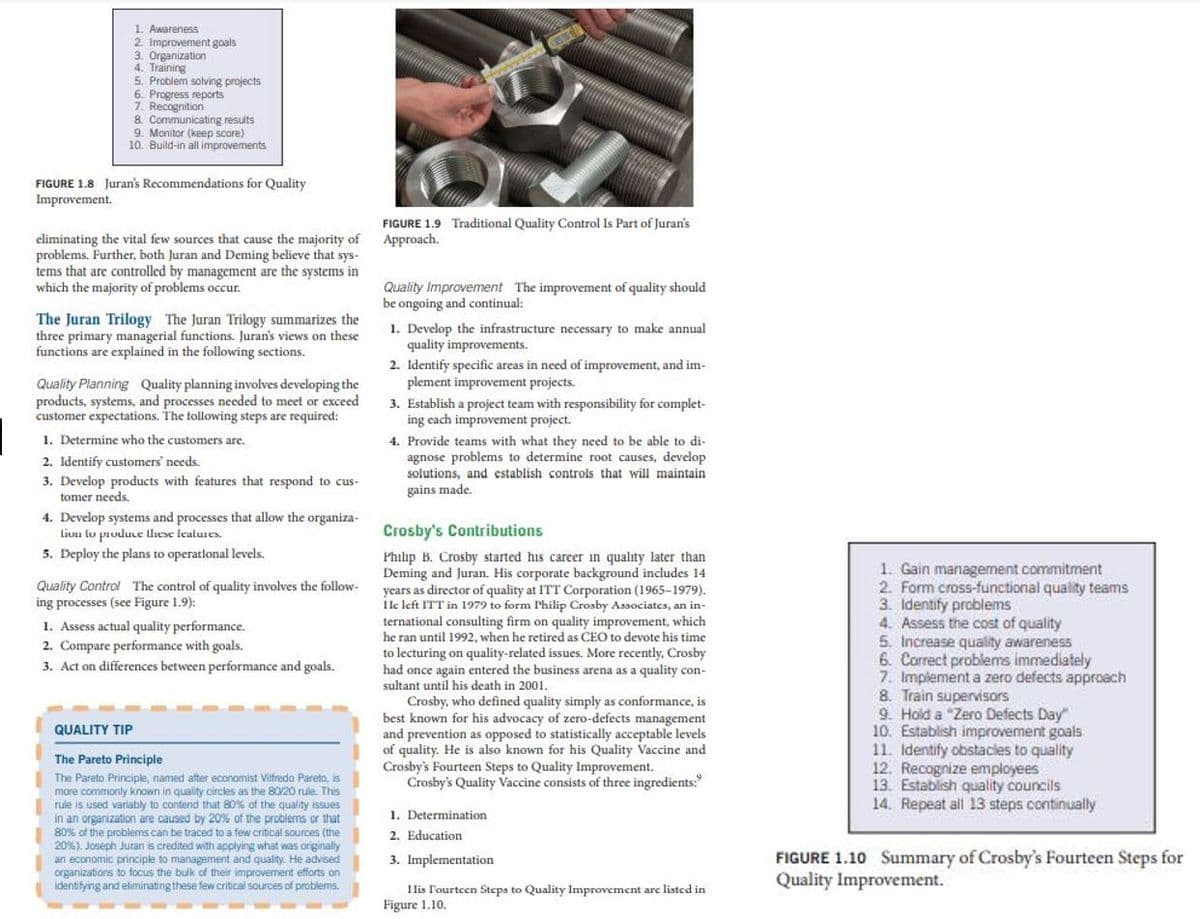
Transcribed Image Text:1. Awareness
2. Improvement goals
3. Organization
4. Training
5. Problem solving projects
6. Progress reports
7. Recognition
8. Communicating results
9. Monitor (keep score)
10. Build-in all improvements
FIGURE 1.8 Juran's Recommendations for Quality
Improvement.
FIGURE 1.9 Traditional Quality Control Is Part of Juran's
climinating the vital few sources that cause the majority of
problems. Further, both Juran and Deming believe that sys-
tems that are controlled by management are the systems in
which the majority of problems occur.
Approach.
Quality Improvement The improvement of quality should
be ongoing and continual:
The Juran Trilogy The Juran Trilogy summarizes the
three primary managerial functions. Juran's views on these
functions are explained in the following sections.
1. Develop the infrastructure necessary to make annual
quality improvenments.
2. Identify specific areas in need of improvement, and im-
plement improvement projects.
Quality Planning Quality planning involves developing the
products, systems, and processes needed to meet or exceed
customer expectations. The following steps are required:
3. Establish a project team with responsibility for complet-
ing each improvement project.
1. Determine who the customers are.
4. Provide teams with what they need to be able to di-
agnose problems to determine root causes, develop
solutions, and establish controls that will maintain
2. Identify customers' needs.
3. Develop products with features that respond to cus-
tomer needs.
gains made.
4. Develop systems and processes that allow the organiza-
Liuu lo produce lhese lealures.
5. Deploy the plans to operatlonal levels.
Crosby's Contributions
Philip B. Crosby started his career in quality later than
Deming and Juran. His corporate background includes 14
years as director of quality at ITT Corporation (1965–1979).
Ile left ITT in 1979 to form l'hilip Crosby Associatcs, an in-
ternational consulting firm on quality improvement, which
he ran until 1992, when he retired as CEO to devote his time
to lecturing on quality-related issues. More recently, Crosby
had once again entered the business arena as a quality con-
sultant until his death in 2001.
Crosby, who defined quality simply as conformance, is
best known for his advocacy of zero-defects management
and prevention as opposed to statistically acceptable levels
of quality. He is also known for his Quality Vaccine and
Crosby's Fourteen Steps to Quality Improvement.
Crosby's Quality Vaccine consists of three ingredients:"
1. Gain management commitment
2. Form cross-functional quality teams
3. Identify problems
4. Assess the cost of quality
5. Increase quality awarenes5
6. Correct problems immediately
7. Implement a zero defects approach
8. Train supervisors
9. Hold a "Zero Defects Day"
10. Establish improvement goals
11. Identify obstacles to quality
12. Recognize employees
13. Establish quality councils
14. Repeat all 13 steps continually
Quality Control The control of quality involves the follow-
ing processes (see Figure 1.9):
1. Assess actual quality performance.
2. Compare performance with goals.
3. Act on differences between performance and goals.
QUALITY TIP
The Pareto Principle
The Pareto Principle, named after economist Vilfredo Pareto, is
more commonly known in quality circles as the 80/20 rule. This
rule is used variably to contend that 80% of the quality issues
in an organization are caused by 20% of the problems or that
80% of the problems can be traced to a few critical sources (the
20%). Joseph Juran is credited with applying what was originaly
an economic principle to management and quality. He advised
organizations to focus the bulk of their improvement efforts on
identifying and eliminating these few critical sources of problems.
1. Determination
2. Education
FIGURE 1.10 Summary of Crosby's Fourteen Steps for
Quality Improvement.
3. Implementation
His Fourtcen Steps to Quality Improvement are listed in
Figure 1.10.
Expert Solution

This question has been solved!
Explore an expertly crafted, step-by-step solution for a thorough understanding of key concepts.
This is a popular solution!
Trending now
This is a popular solution!
Step by step
Solved in 3 steps

Recommended textbooks for you
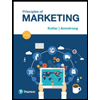
Principles Of Marketing
Marketing
ISBN:
9780134492513
Author:
Kotler, Philip, Armstrong, Gary (gary M.)
Publisher:
Pearson Higher Education,
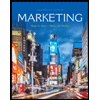
Marketing
Marketing
ISBN:
9781259924040
Author:
Roger A. Kerin, Steven W. Hartley
Publisher:
McGraw-Hill Education
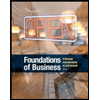
Foundations of Business (MindTap Course List)
Marketing
ISBN:
9781337386920
Author:
William M. Pride, Robert J. Hughes, Jack R. Kapoor
Publisher:
Cengage Learning
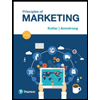
Principles Of Marketing
Marketing
ISBN:
9780134492513
Author:
Kotler, Philip, Armstrong, Gary (gary M.)
Publisher:
Pearson Higher Education,
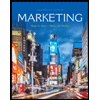
Marketing
Marketing
ISBN:
9781259924040
Author:
Roger A. Kerin, Steven W. Hartley
Publisher:
McGraw-Hill Education
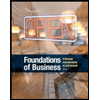
Foundations of Business (MindTap Course List)
Marketing
ISBN:
9781337386920
Author:
William M. Pride, Robert J. Hughes, Jack R. Kapoor
Publisher:
Cengage Learning
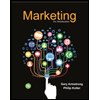
Marketing: An Introduction (13th Edition)
Marketing
ISBN:
9780134149530
Author:
Gary Armstrong, Philip Kotler
Publisher:
PEARSON
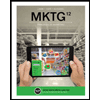
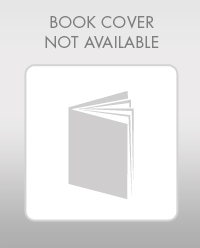
Contemporary Marketing
Marketing
ISBN:
9780357033777
Author:
Louis E. Boone, David L. Kurtz
Publisher:
Cengage Learning