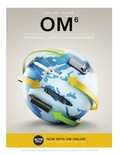
Concept explainers
(a)
Interpretation: The annual capacity with a single eight hour shift is to be calculated.
Concept Introduction:
The annual capacityis the maximum level of output that a company is able to make a product or provide a service in a year.
Output per day is calculated by,
The capacity is given by,
(a)

Explanation of Solution
Given information:
Fixed cost for one shift is $60,000.
Unit variable cost is $7.
Selling price is $12.
Number of machines is 6.
Number of working days in year is 340.
Processing time per unit is 40 minutes.
The annual capacity with a single eight hour shift calculation is shown below:
The capacity is calculated as follows:
Thus, the capacity of plant is 24480 units per year.
(b)
Interpretation: The capacity with two shifts is to be calculated.
Concept Introduction:
The annual capacityis the maximum level of output that a company is able to make a product or provide a service in a year.
The formula to calculate the output per day is given by,
(b)

Explanation of Solution
The annual capacity with a single eight hour shift is calculated as shown below:
Determine the capacity as follows.
Thus, the capacity of plant is 48960 unit per year.
(c)
Interpretation: The break-even volume with a single shift operation is to be calculated.
Concept Introduction:
Break-even point is the no profit no loss situation.
Breakevenvolumeis the amount of product that needs to be produced and sold to cover total costs of production.
(c)

Explanation of Solution
Calculate the break-even volume with one shiftas shown below.
Thus, the break-even volume with one shift is $12000 units.
(d)
Interpretation: The maximum revenue with a single shift is to be calculated.
Concept Introduction:
Revenueis defined as the income of a company that is generated from its normal business activities, such as the sale of goods and services to customers.
(d)

Explanation of Solution
The maximum revenue per shift is calculated by using the following formula:
Thus, the revenue is $297,600 units.
(e)
Interpretation: The break-even volume with a two shift operation is to be calculated.
Concept Introduction:
Break-even point is the no profit, no loss situation.
Breakevenvolumeis the amount of product that needs to be produced and sold to cover total costs of production.
(e)

Explanation of Solution
Thus, the break-even volume with two shifts is $24,000 units.
Want to see more full solutions like this?
- Given the following data for Albert’s fabricating production area:Fixed costs for one shift = $60,000Unit variable cost = $7Selling price = $12Number of machines = 6Number of working days in year = 340Processing time per unit = 40 minutes a. What is the annual capacity with a single 8-hour shift? b. What is the capacity with two shifts? c. What is the break-even volume with a single-shift operation?arrow_forward1. What factors should be considered when selecting the appropriate capacity cushion? Howdoes the choice of capacity cushion relate to other decisions in operations management?To other functional areas? 2. Capacity planning requires a demand forecast for an extended period of time into thefuture. What concerns would you have regarding an extended forecast as a capacityplanner?arrow_forwardBriefly discuss how does capacity planning interrelates with other activities of operations?arrow_forward
- MagneticCompany has made the following information available for its production facility for the current month. Fixed overhead was estimated at 19,000 machine hours for the production cycle. Actual machine hours for the period were 18,900, which generated 3,900 units. Material purchased (80,000 pieces) P314,000 Material quantity variance P6,400 U Machine hours used (18,900 hours) VOH spending variance P50 U Actual fixed overhead P60,000 Actual labor cost P40,120 Actual labor hours 5,900 Magnetic Company’s standard costs are as follows: Direct material 20 pieces @ P4 per piece Direct labor 1.5 hours @ P6 per hour Variable overhead (applied on a machine hour basis) 4.8 hours @ P2.50 per hour Fixed overhead (applied on a machine hour basis) 4.8 hours @ P3 per hour Determine the following items: h. labor efficiency variance i. actual variable overhead…arrow_forwardExplain and expand these importance of capacity planning. 1. Capacity decisions often involve long-term commitment of resources and the fact that, once they are implemented, those decision may be difficult or impossible to modify without incurring major costs. 2. Capacity decisions can affect competitiveness. 3. Capacity affects the ease of management.arrow_forwardA company has a factory that is designed so that it is most efficient (average unit cost is minimized) when producing 28,500 units of output each month. However, it has an absolute maximum output capability of 35,000 units per month, and can produce as little as 7,000 units per month without corporate headquarters shifting production to another plant. If the factory produces 22,120 units in October, what is the capacity utilization rate in October for this factory? (Round your answer to 1 decimal place.)arrow_forward
- What steps are necessary in the capacity planning? differentiate between product capacity and service capacity with proper points without plagiarism.arrow_forwardWhat do you understand by capacity planning? Explain the decision tree modeling for capacity expansionarrow_forwardmafTech is a local companv assembles smart devices parts to various manutacturersproducing smartphones and computersLast year it had cost of goods sold of RM88.700 Million, the averageproduction materials and parts are RM1.333 Million, Work in progress atRM7.555 Million, and finished goods at RM5.999 Million. Define theaverage aggregate value, and Analyze the company's inventory turnsand days of supply being held in inventory.arrow_forward
- Out of the following factors that are affecting Capacity Planning, which one is Less Controllable one?(A) Machine break-downs(B) Amount of labour employed(C) Facilities installed(D) Shifts of work per dayarrow_forwardA company has a factory that is designed so that it is most efi cient (average unit cost is minimized) when producing 15,000 units of output each month. However, it has an absolute maximum output capability of 17,250 units per month, and can produce as little as 7,000 units per month without corporate headquarters shifting production to another plant. If the factory produces 10,925 units in October, what is the capacity utilization rate in October for this factory?arrow_forwardYou have been asked to estimate the cost of 100 prefabricated structures to be sold to a local school district. Each structure provides 1,000 square feet offloor space, with 8-feet ceilings. In 1999, you produced 70 similar structures consistingof the same materials and having the same ceiling height, but each provided only 800square feet of floor space. The material cost for each structure was $25,000 in 1999, andthe cost capacity factor is 0.65. The cost index values for 1999 and 2006 are 200 and 289,respectively. The estimated manufacturing cost for the first 1,000-square-foot structureis $12,000. Assume a learning curve of 88% and use the cost of the 50th structure asyour standard time for estimating manufacturing cost. Estimate the total material costand the total manufacturing cost for the 100 prefabricated structures.arrow_forward
- Practical Management ScienceOperations ManagementISBN:9781337406659Author:WINSTON, Wayne L.Publisher:Cengage,Operations ManagementOperations ManagementISBN:9781259667473Author:William J StevensonPublisher:McGraw-Hill EducationOperations and Supply Chain Management (Mcgraw-hi...Operations ManagementISBN:9781259666100Author:F. Robert Jacobs, Richard B ChasePublisher:McGraw-Hill Education
- Purchasing and Supply Chain ManagementOperations ManagementISBN:9781285869681Author:Robert M. Monczka, Robert B. Handfield, Larry C. Giunipero, James L. PattersonPublisher:Cengage LearningProduction and Operations Analysis, Seventh Editi...Operations ManagementISBN:9781478623069Author:Steven Nahmias, Tava Lennon OlsenPublisher:Waveland Press, Inc.
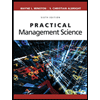
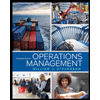
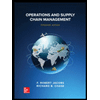
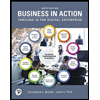
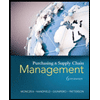
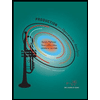