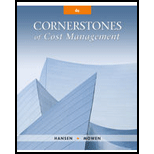
Concept explainers
Mott Company recently implemented a JIT manufacturing system. After one year of operation, Heidi Burrows, president of the company, wanted to compare product cost under the JIT system with product cost under the old system. Mott’s two products are weed eaters and lawn edgers. The unit prime costs under the old system are as follows:
Under the old manufacturing system, the company operated three service centers and two production departments. Overhead was applied using departmental overhead rates. The direct overhead costs associated with each department for the year preceding the installation of JIT are as follows:
Under the old system, the overhead costs of the service departments were allocated directly to the producing departments and then to the products passing through them. (Both products passed through each producing department.) The overhead rate for the Machining Department was based on machine hours, and the overhead rate for assembly was based on direct labor hours. During the last year of operations for the old system, the Machining Department used 80,000 machine hours, and the Assembly Department used 20,000 direct labor hours. Each weed eater required 1.0 machine hour in Machining and 0.25 direct labor hour in Assembly. Each lawn edger required 2.0 machine hours in Machining and 0.5 hour in Assembly. Bases for allocation of the service costs are as follows:
Upon implementing JIT, a manufacturing cell for each product was created to replace the departmental structure. Each cell occupied 40,000 square feet. Maintenance and materials handling were both decentralized to the cell level. Essentially, cell workers were trained to operate the machines in each cell, assemble the components, maintain the machines, and move the partially completed units from one point to the next within the cell. During the first year of the JIT system, the company produced and sold 20,000 weed eaters and 30,000 lawn edgers. This output was identical to that for the last year of operations under the old system. The following costs have been assigned to the manufacturing cells:
Required:
- 1. Compute the unit cost for each product under the old manufacturing system.
- 2. Compute the unit cost for each product under the JIT system.
- 3. Which of the unit costs is more accurate? Explain. Include in your explanation a discussion of how the computational approaches differ.
- 4. Calculate the decrease in overhead costs under JIT, and provide some possible reasons that explain the decrease.
1.

Calculate the unit cost of each product under old manufacturing system.
Explanation of Solution
Just-in-time (JIT) manufacturing system: Just-in-time (JIT) manufacturing system is an approach to manufacturing, that eliminates and reduces the non-value-added activities and it concentrates on both product quality and efficiency.
Calculate the unit cost of each product under old manufacturing system as follows:
Particulars | Eaters | Edgers |
Direct materials | $12.00 | $45.00 |
Direct labor | $4.00 | $30.00 |
Overhead (7) | $10.07 | $20.14 |
Total | $26.07 | $95.14 |
Table (1)
Working note (1):
Calculate the allocation ratios for machining and assembly.
Particulars | Machine hour | Allocation ratio | Material moves | Allocation ratio | Square feet | Allocation ratio |
Machining | 80,000 | 4/5 | 90,000 | 3/5 | 80,000 | 2/3 |
Assembly | 20,000 | 1/5 | 60,000 | 2/5 | 40,000 | 1/3 |
Total | 100,000 | 150,000 | 120,000 |
Table (2)
Note: Formula for allocation ratio is
Working note (2):
Calculate the direct overhead cost of maintenance.
For machining department:
For assembly department:
Working note (3):
Calculate the direct overhead cost of material handling.
For machining department:
For assembly department:
Working note (4):
Calculate the direct overhead cost of building and grounds.
For machining department:
For assembly department:
Working note (5):
Calculate the total direct overhead cost for each department.
Particulars | Machining | Assembly |
Direct overhead costs | $280,000 | $175,0000 |
Add: Direct overhead cost for maintenance (2) | $88,000 | $22,000 |
Add: Direct overhead cost for material handling (3) | $54,000 | $36,000 |
Add: Direct overhead cost for building and grounds (4) | $100,000 | $50,000 |
Total | $522,000 | $283,000 |
Table (3)
Working note (6):
Calculate the direct overhead cost per hour for each department.
For machining department:
For assembly department:
Working note (7):
Calculate the direct overhead cost per unit for each product.
For Eaters:
For Edgers:
2.

Calculate the unit cost of each product under JIT system.
Explanation of Solution
Calculate the unit cost of each product under JIT system as follows:
Unit cost of Eaters under JIT:
Unit cost of Edgers under JIT:
3.

Identify the unit cost which is more accurate, and explain the manner in which the computational approaches differ.
Explanation of Solution
Identify the unit cost which is more accurate, and explain the manner in which the computational approaches differ as follows:
Just in time inventory costs are more accurate because,
- The building and ground costs are assigned for activity based approach.
- All costs of company (except the building and grounds) are directly attributable to each product.
The assignment of the company should be measured at the activity based costing method, because the company traces the cost and products based on each activity of the production. Since, both cells (Eaters and Edgers) are dedicated to produce a single product, whatever causal factors that are used to allocate each cell is same as the final product.
The functional based costing system first assigns the cost to each department, and then assigns the cost to the product based on the cost drivers, but the maintenance and materials handing cost is not a unit-based activities.
4.

Ascertain the decrease in overhead costs under just in time method and given some possible reasons.
Explanation of Solution
Ascertain the decrease in overhead costs under Just in time method and given some possible reasons as follows:
In this case, the overhead cost has been decreased by $205,500 and the decrease in overhead cost is explained by the following factors:
- Usage of interdisciplinary labor,
- Total quality control,
- Decentralization of services and
- Physical organization of the manufacturing cell.
Working note (8):
Calculate the overhead cost under JIT.
Working note (9):
Calculate the Pre-JIT overhead cost.
Want to see more full solutions like this?
Chapter 11 Solutions
CengageNOWv2, 1 term Printed Access Card for Hansen/Mowen’s Cornerstones of Cost Management, 4th
- Evans, Inc., has a unit-based costing system. Evanss Miami plant produces 10 different electronic products. The demand for each product is about the same. Although they differ in complexity, each product uses about the same labor time and materials. The plant has used direct labor hours for years to assign overhead to products. To help design engineers understand the assumed cost relationships, the Cost Accounting Department developed the following cost equation. (The equation describes the relationship between total manufacturing costs and direct labor hours; the equation is supported by a coefficient of determination of 60 percent.) Y=5,000,000+30X,whereX=directlaborhours The variable rate of 30 is broken down as follows: Because of competitive pressures, product engineering was given the charge to redesign products to reduce the total cost of manufacturing. Using the above cost relationships, product engineering adopted the strategy of redesigning to reduce direct labor content. As each design was completed, an engineering change order was cut, triggering a series of events such as design approval, vendor selection, bill of materials update, redrawing of schematic, test runs, changes in setup procedures, development of new inspection procedures, and so on. After one year of design changes, the normal volume of direct labor was reduced from 250,000 hours to 200,000 hours, with the same number of products being produced. Although each product differs in its labor content, the redesign efforts reduced the labor content for all products. On average, the labor content per unit of product dropped from 1.25 hours per unit to one hour per unit. Fixed overhead, however, increased from 5,000,000 to 6,600,000 per year. Suppose that a consultant was hired to explain the increase in fixed overhead costs. The consultants study revealed that the 30 per hour rate captured the unit-level variable costs; however, the cost behavior of other activities was quite different. For example, setting up equipment is a step-fixed cost, where each step is 2,000 setup hours, costing 90,000. The study also revealed that the cost of receiving goods is a function of the number of different components. This activity has a variable cost of 2,000 per component type and a fixed cost that follows a step-cost pattern. The step is defined by 20 components with a cost of 50,000 per step. Assume also that the consultant indicated that the design adopted by the engineers increased the demand for setups from 20,000 setup hours to 40,000 setup hours and the number of different components from 100 to 250. The demand for other non-unit-level activities remained unchanged. The consultant also recommended that management take a look at a rejected design for its products. This rejected design increased direct labor content from 250,000 hours to 260,000 hours, decreased the demand for setups from 20,000 hours to 10,000 hours, and decreased the demand for purchasing from 100 component types to 75 component types, while the demand for all other activities remained unchanged. Required: 1. Using normal volume, compute the manufacturing cost per labor hour before the year of design changes. What is the cost per unit of an average product? 2. Using normal volume after the one year of design changes, compute the manufacturing cost per hour. What is the cost per unit of an average product? 3. Before considering the consultants study, what do you think is the most likely explanation for the failure of the design changes to reduce manufacturing costs? Now use the information from the consultants study to explain the increase in the average cost per unit of product. What changes would you suggest to improve Evanss efforts to reduce costs? 4. Explain why the consultant recommended a second look at a rejected design. Provide computational support. What does this tell you about the strategic importance of cost management?arrow_forwardBig Mikes, a large hardware store, has gathered data on its overhead activities and associated costs for the past 10 months. Nizam Sanjay, a member of the controllers department, believes that overhead activities and costs should be classified into groups that have the same driver. He has decided that unloading incoming goods, counting goods, and inspecting goods can be grouped together as a more general receiving activity, since these three activities are all driven by the number of receiving orders. The 10 months of data shown below have been gathered for the receiving activity. Required: 1. Prepare a scattergraph, plotting the receiving costs against the number of purchase orders. Use the vertical axis for costs and the horizontal axis for orders. 2. Select two points that make the best fit, and compute a cost formula for receiving costs. 3. Using the high-low method, prepare a cost formula for the receiving activity. 4. Using the method of least squares, prepare a cost formula for the receiving activity. What is the coefficient of determination?arrow_forwardBrees, Inc., a manufacturer of golf carts, has just received an offer from a supplier to provide 2,600 units of a component used in its main product. The component is a track assembly that is currently produced internally. The supplier has offered to sell the track assembly for 66 per unit. Brees is currently using a traditional, unit-based costing system that assigns overhead to jobs on the basis of direct labor hours. The estimated traditional full cost of producing the track assembly is as follows: Prior to making a decision, the companys CEO commissioned a special study to see whether there would be any decrease in the fixed overhead costs. The results of the study revealed the following: 3 setups1,160 each (The setups would be avoided, and total spending could be reduced by 1,160 per setup.) One half-time inspector is needed. The company already uses part-time inspectors hired through a temporary employment agency. The yearly cost of the part-time inspectors for the track assembly operation is 12,300 and could be totally avoided if the part were purchased. Engineering work: 470 hours, 45/hour. (Although the work decreases by 470 hours, the engineer assigned to the track assembly line also spends time on other products, and there would be no reduction in his salary.) 75 fewer material moves at 30 per move. Required: 1. Ignore the special study, and determine whether the track assembly should be produced internally or purchased from the supplier. 2. Now, using the special study data, repeat the analysis. 3. Discuss the qualitative factors that would affect the decision, including strategic implications. 4. After reviewing the special study, the controller made the following remark: This study ignores the additional activity demands that purchasing would cause. For example, although the demand for inspecting the part on the production floor decreases, we may need to inspect the incoming parts in the receiving area. Will we actually save any inspection costs? Is the controller right?arrow_forward
- Handbrain Inc. is considering a change to activity-based product costing. The company produces two products, cell phones and tablet PCs, in a single production department. The production department is estimated to require 2,000 direct labor hours. The total indirect labor is budgeted to be 200,000. Time records from indirect labor employees revealed that they spent 30% of their time setting up production runs and 70% of their time supporting actual production. The following information about cell phones and tablet PCs was determined from the corporate records: a. Determine the indirect labor cost per unit allocated to cell phones and tablet PCs under a single plantwide factory overhead rate system using the direct labor hours as the allocation base. b. Determine the budgeted activity costs and activity rates for the indirect labor under activity-based costing. Assume two activitiesone for setup and the other for production support. c. Determine the activity cost per unit for indirect labor allocated to each product under activity-based costing. d. Why are the per-unit allocated costs in (a) different from the per-unit activity cost assigned to the products in (c)?arrow_forwardPinter Company had the following environmental activities and product information: 1. Environmental activity costs 2. Driver data 3. Other production data Required: 1. Calculate the activity rates that will be used to assign environmental costs to products. 2. Determine the unit environmental and unit costs of each product using ABC. 3. What if the design costs increased to 360,000 and the cost of toxic waste decreased to 750,000? Assume that Solvent Y uses 6,000 out of 12,000 design hours. Also assume that waste is cut by 50 percent and that Solvent Y is responsible for 14,250 of 15,000 pounds of toxic waste. What is the new environmental cost for Solvent Y?arrow_forwardYoung Company is beginning operations and is considering three alternatives to allocate manufacturing overhead to individual units produced. Young can use a plantwide rate, departmental rates, or activity-based costing. Young will produce many types of products in its single plant, and not all products will be processed through all departments. In which one of the following independent situations would reported net income for the first year be the same regardless of which overhead allocation method had been selected? a. All production costs approach those costs that were budgeted. b. The sales mix does not vary from the mix that was budgeted. c. All manufacturing overhead is a fixed cost. d. All ending inventory balances are zero.arrow_forward
- The chief executive officer of Acadia, Inc. attended a conference in which one of the sessions was devoted to variable costing. The CEO was impressed by the presentation and has asked that the following data of Acadia, Inc. be used to prepare comparative statements using variable costing and the companys absorption costing. The data follow: The factory produced 80,000 units during the period, and 70,000 units were sold for 700,000. 1. Prepare an income statement using variable costing. 2. Prepare an income statement using absorption costing. (Round unit costs to three decimal places.)arrow_forwardIn 20x2, Choctaw Company implements a new process affecting labor and materials. The following reported data are provided to evaluate the effect on the companys productivity: Required: 1. Calculate the productivity profile for 20x1. 2. Calculate the productivity profile for 20x2, and comment on the effect of the new production and assembly process. 3. What if the labor hours used in 20x2 were 112,500? What does comparison of the 20x1 and 20x2 profiles now communicate?arrow_forwardCarsen Company produces handcrafted pottery that uses two inputs: materials and labor. During the past quarter, 24,000 units were produced, requiring 96,000 pounds of materials and 48,000 hours of labor. An engineering efficiency study commissioned by the local university revealed that Carsen can produce the same 24,000 units of output using either of the following two combinations of inputs: The cost of materials is 8 per pound; the cost of labor is 12 per hour. Required: 1. Compute the output-input ratio for each input of Combination F1. Does this represent a productivity improvement over the current use of inputs? What is the total dollar value of the improvement? Classify this as a technical or an allocative efficiency improvement. 2. Compute the output-input ratio for each input of Combination F2. Does this represent a productivity improvement over the current use of inputs? Now, compare these ratios to those of Combination F1. What has happened? 3. Compute the cost of producing 24,000 units of output using Combination F1. Compare this cost to the cost using Combination F2. Does moving from Combination F1 to Combination F2 represent a productivity improvement? Explain.arrow_forward
- Anderson Company has the following departmental manufacturing structure for one of its products: After some study, the production manager of Anderson recommended the following revised cellular manufacturing approach: Required: 1. Calculate the total time it takes to produce a batch of 20 units using Andersons traditional departmental structure. 2. Using cellular manufacturing, how much time is saved producing the same batch of 20 units? Assuming the cell operates continuously, what is the production rate? Which process controls this production rate? 3. What if the processing times of molding, welding, and assembly are all reduced to six minutes each? What is the production rate now, and how long will it take to produce a batch of 20 units?arrow_forwardCleanCom Company specializes in cleaning commercial buildings and construction sites. Each building and site is different, requiring amounts and types of supplies and labor for each job. CleanCom estimated the following for the year: During the year, the following actual amounts were experienced: If CleanCom uses a normal costing system and overhead is applied on the basis of direct labor hours, what is the cost of cleaning a construction site that takes 140 of direct materials and 21 direct labor hours? a. 455 b. 508 c. 648 d. 644arrow_forwardOtero Fibers, Inc., specializes in the manufacture of synthetic fibers that the company uses in many products such as blankets, coats, and uniforms for police and firefighters. Otero has been in business since 1985 and has been profitable every year since 1993. The company uses a standard cost system and applies overhead on the basis of direct labor hours. Otero has recently received a request to bid on the manufacture of 800,000 blankets scheduled for delivery to several military bases. The bid must be stated at full cost per unit plus a return on full cost of no more than 10 percent after income taxes. Full cost has been defined as including all variable costs of manufacturing the product, a reasonable amount of fixed overhead, and reasonable incremental administrative costs associated with the manufacture and sale of the product. The contractor has indicated that bids in excess of 30 per blanket are not likely to be considered. In order to prepare the bid for the 800,000 blankets, Andrea Lightner, cost accountant, has gathered the following information about the costs associated with the production of the blankets. Direct machine costs consist of items such as special lubricants, replacement of needles used in stitching, and maintenance costs. These costs are not included in the normal overhead rates. Otero recently developed a new blanket fiber at a cost of 750,000. In an effort to recover this cost, Otero has instituted a policy of adding a 0.50 fee to the cost of each blanket using the new fiber. To date, the company has recovered 125,000. Lightner knows that this fee does not fit within the definition of full cost, as it is not a cost of manufacturing the product. Required: 1. Calculate the minimum price per blanket that Otero Fibers could bid without reducing the companys operating income. 2. Using the full-cost criteria and the maximum allowable return specified, calculate Otero Fibers bid price per blanket. 3. Without prejudice to your answer to Requirement 2, assume that the price per blanket that Otero Fibers calculated using the cost-plus criteria specified is greater than the maximum bid of 30 per blanket allowed. Discuss the factors that Otero Fibers should consider before deciding whether or not to submit a bid at the maximum acceptable price of 30 per blanket. (CMA adapted)arrow_forward
- Cornerstones of Cost Management (Cornerstones Ser...AccountingISBN:9781305970663Author:Don R. Hansen, Maryanne M. MowenPublisher:Cengage LearningManagerial AccountingAccountingISBN:9781337912020Author:Carl Warren, Ph.d. Cma William B. TaylerPublisher:South-Western College PubFinancial And Managerial AccountingAccountingISBN:9781337902663Author:WARREN, Carl S.Publisher:Cengage Learning,
- Excel Applications for Accounting PrinciplesAccountingISBN:9781111581565Author:Gaylord N. SmithPublisher:Cengage LearningPrinciples of Cost AccountingAccountingISBN:9781305087408Author:Edward J. Vanderbeck, Maria R. MitchellPublisher:Cengage LearningPrinciples of Accounting Volume 2AccountingISBN:9781947172609Author:OpenStaxPublisher:OpenStax College
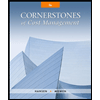
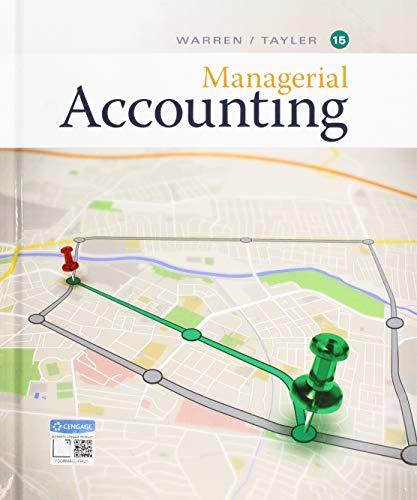
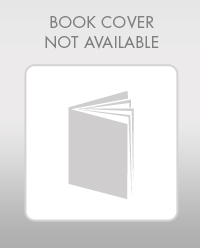
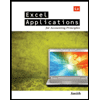
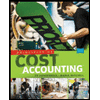