Concept explainers
Problem 6-26A Effects of the level of production on an outsourcing decision
Townsend Chemical Company makes a variety of cosmetic products, one of which is a skin cream designed to reduce the signs of aging. Townsend produces a relatively small amount (15,000 units) of the cream and is considering the purchase of the product from an outside supplier for $9 each. If Townsend purchases from the outside supplier, it would continue to sell and distribute the cream under its own brand name. Townsend’s accountant constructed the following profitability analysis:
Revenue (15,000 units × $20) | $300,000 |
Unit-level materials costs (15,000 units × $2.50) | (37,500) |
Unit-level labor costs (15,000 units × $1,80) | (27,000) |
Unit-level overhead costs (15,000 × $0.70) | (10,500) |
Unit-level selling expenses (15,000 × $1,00) | (15,000) |
Contribution margin | 210,000 |
Skin cream production supervisor’s salary | (75,000) |
Allocated portion of facility-level costs | (45,000) |
Product-level advertising cost | (50,000) |
Contribution to companywide income | $ 40,000 |
Required
- a. Identify the cost items relevant to the make-or-outsource decision.
- b. Should Townsend continue to make the product or buy it from the supplier? Support your answer by determining the change in net income if Townsend buys the cream instead of making it.
- c. Suppose that Townsend is able to increase sales by 10,000 units (sales will increase to 25,000 units). At this level of production, should Townsend make or buy the cream? Support your answer by explaining how the increase in production affects the cost per unit.
- d. Discuss the qualitative factors that Townsend should consider before deciding to outsource the skin cream. How can Townsend minimize the risk of establishing a relationship with an unreliable supplier?
a.

The cost items that is relevant to make-or-outsource decision.
Explanation of Solution
Special order decisions: Special order decisions include circumstances in which the board must choose whether to acknowledge abnormal customer orders. These requests or orders normally necessitate special dispensation or include a demand for lesser price.
Decision making: It is a vital capacity in the management, since decision making is identified with issue, a compelling decision making accomplishes the preferred objectives or goals by taking care of such issues.
The cost items that are relevant to make-or-outsource decision are as follows:
The unit-level costs of creation can be avoided if the Product X is bought. Likewise, it is sensible to accept that the cost the salary of production supervisor can be avoided if the manufacturing development is rejected. Since Company TC will keep on promoting the item, the selling costs, product-level advertising cost, and facility-sustaining costs will proceed irrespective whether Product X is made or bought.
These costs may not be avoided by obtaining Product X. Thus, the below items would be relevant to the make-or-outsource decision. The items that is relevant to make-or-outsource decision is mentioned in the below part.
Determine the total avoidable costs
Therefore the total avoidable cost is $150,000.
b.

Whether Company TC continue to make the product or buy from the supplier by determining the change in net income.
Explanation of Solution
Determine the cost per unit
Therefore the cost per unit is $10.
Determine the increase in net income
Therefore the increase in net income is $15,000.
The reason on whether Company TC would continue to make the product or buy from the supplier is as follows:
The avoidable cost of producing Product X is $10 per unit. Since the cost to buy is just $9, Company TC can lessen its costs by acquiring instead of manufacturing Product X. By outsourcing Product X would expand income by $15,000.
c.

Whether Company TC should buy Product X if sales increase by 10,000 units.
Explanation of Solution
Determine the avoidable costs
Therefore the avoidable cost is $200,000.
Determine the cost per unit
Therefore the cost per unit is $8.
The reasons on whether Company TC should buy Product X if sales increase by 10,000 units is as follows:
The cost of the chief's pay is fixed with respect to the number of units Product X is manufactured and sold. Consequently, the cost per unit will drop and there is an increase in sales. The manufacturing cost per unit is $8.
The avoidable cost per unit at the current level of production is lower to produce than to purchase. Company TC should continue making Product X. The decision to outsource should think about future development in addition to the present creation.
d.

The qualitative factors that Company TC should consider before deciding to outsource Product X.
Explanation of Solution
The qualitative factors that Company TC should consider before deciding to outsource Product X is as follows:
Before focusing on the outsourcing decision, Company TC must think about the capacity of the provider to furnish Product X as per the organization's quality norms. Likewise, Company TC must guarantee itself that the item will be conveyed on an appropriate premise. By outsourcing, Company TC is losing the advantages of vertical integration. The organization is subject to the provider's execution.
The loss of control should be weighed in contradiction of the advantages of cost reduction. Company TC can shield itself from inconsistent providers by keeping up a rundown of licensed providers. Company TC should furnish these providers with hikes or incentives for providing exceptional services, for example, amount buys and quick invoice payment so as to increase the favored customer standing.
Want to see more full solutions like this?
Chapter 13 Solutions
SURVEY OF ACCOUNTING 360DAY CONNECT CAR
- Refer to Exercise 12.14. Suppose that for 20x2, Sanford, Inc., has chosen suppliers that provide higher-quality parts and redesigned its plant layout to reduce material movement. Additionally, Sanford implemented a new setup procedure and provided training for its purchasing agents. As a consequence, less setup time is required and fewer purchasing mistakes are made. At the end of 20x2, the information shown on page 680 is provided. Required: 1. Prepare a report that compares the non-value-added costs for 20x2 with those of 20x1. 2. What is the role of activity reduction for non-value-added activities? For value-added activities? 3. Comment on the value of a trend report.arrow_forwardCase 2 Ethics and a Cost-Volume-Profit Application Danna Lumus, the marketing manager for a division that produces a variety of paper products, is considering the divisional manager's request for a sales forecast for a new line of paper napkins. The divisional manager has been gathering data so that he can choose between two different production processes. The first process would have a variable cost of $10 per case produced and total fixed cost of $100,000. The second process would have a variable cost of $6 per case and total fixed cost of $200,000. The selling price would be $30 per case. Danna had just completed a marketing analysis that projects annual sales of 30,000 cases. Danna is reluctant to report the 30,000 forecast to the divisional manager. She knows that the first process would be labor intensive, whereas the second would be largely automated with little labor and no requirement for an additional production supervisor. If the first process is chosen, Jerry Johnson, a…arrow_forwardSegment variable costing income statement and effect on income of change in operations Valdespin Company manufactures three sizes of camping tentssmall (S), medium (M), and large (L). The income statement has consistently indicated a net loss for the M size, and management is considering three proposals: (1) continue Size M, (2) discontinue Size M and reduce total output accordingly, or (3) discontinue Size M and conduct an advertising campaign to expand the sales of Size S so that the entire plant capacity can continue to be used. If Proposal 2 is selected and Size M is discontinued and production curtailed, the annual fixed production costs and fixed operating expenses could be reduced by 46,080 and 532,240. respectively. If Proposal 3 is selected, it is anticipated that an additional annual expenditure of 34,560 for the rental of additional warehouse space would yield an additional 130% in Size S sales volume. It is also assumed that the increased production of Size S would utilize the plant facilities released by the discontinuance of Size M. The sales and costs have been relatively stable over the past few years, and they are expected to remain so for the foreseeable future. The income statement for the past year ended June 30, 20Y9, is as follows: Instructions 1. Prepare an income statement for the past year in the variable costing: format. Use the following headings: Data for each style should be reported through contribution margin. The fixed costs should be deducted from the total contribution margin, as reported in the Total column, to determine income from operations. 2. Based on the income statement prepared in (1) and the other data presented, determine the amount by which total annual income from operations would be reduced below its present level if Proposal 2 is accepted. 3. Prepare an income statement in the variable costing format, indicating the projected annual income from operations if Proposal 3 is accepted. Use the following headings: Data for each style should be reported through contribution margin. The fixed costs should be deducted from the total contribution margin as reported in the Total column. For purposes of this problem, the expenditure of 34,560 for the rental of additional warehouse space can be added to the fixed operating expenses. 4. By how much would total annual income increase above its present level if Proposal 3 is accepted? Explain.arrow_forward
- AccountingAccountingISBN:9781337272094Author:WARREN, Carl S., Reeve, James M., Duchac, Jonathan E.Publisher:Cengage Learning,Financial & Managerial AccountingAccountingISBN:9781337119207Author:Carl Warren, James M. Reeve, Jonathan DuchacPublisher:Cengage LearningCornerstones of Cost Management (Cornerstones Ser...AccountingISBN:9781305970663Author:Don R. Hansen, Maryanne M. MowenPublisher:Cengage Learning
- Accounting (Text Only)AccountingISBN:9781285743615Author:Carl Warren, James M. Reeve, Jonathan DuchacPublisher:Cengage LearningFinancial & Managerial AccountingAccountingISBN:9781285866307Author:Carl Warren, James M. Reeve, Jonathan DuchacPublisher:Cengage Learning
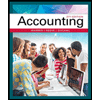
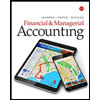
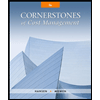
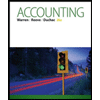
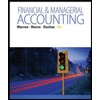