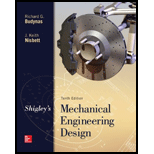
Concept explainers
(a)
The pitch diameter for gear 2.
The pitch diameter for gear 3.
The pitch diameter for gear 4.
The pitch diameter for gear 5.
(a)

Answer to Problem 36P
The pitch diameter for gear 2 is
The pitch diameter for gear 3 is
The pitch diameter for gear 4 is
The pitch diameter for gear 5 is
Explanation of Solution
Write the expression for the compound reverted gear train.
Here, the numbers of teeth on gear 3 is
Write the expression for the ratio of output speed to input speed.
Here, the ratio of output speed to input speed is
Write the expression for the ratio of output speed to input speed in terms of number of teeth.
Write the expression for the smallest number of teeth on pinion without interference.
Here, the number of teeth on pinion is
Write the expression for the number of teeth on gear 3.
Write the expression for the number of teeth on gear 5.
Substitute
Write the pitch diameter for gear 2.
Here, the pitch is
Write the pitch diameter for gear 4.
Write the pitch diameter for gear 3.
Write the pitch diameter for gear 5.
Conclusion:
Assume the output speed of the gear train is
Substitute
Substitute
Substitute
Substitute
Substitute
Substitute
Substitute
Therefore, the speed is greater than
Assume number of teeth on gear 3 and gear 5 is equal to 44 teeth.
Substitute
Therefore, the assumption is correct.
Substitute
Thus, the pitch diameter for gear 2 is
Substitute
Thus, the pitch diameter for gear 4 is
Substitute
Thus, the pitch diameter for gear 3 is
Substitute
Thus, the pitch diameter for gear 5 is
(b)
The pitch line velocity for gear 2.
The pitch line velocity for gear 3.
The pitch line velocity for gear 4.
The pitch line velocity for gear 5.
(b)

Answer to Problem 36P
The pitch line velocity for gear 2 is
The pitch line velocity for gear 3 is
The pitch line velocity for gear 4 is
The pitch line velocity for gear 5 is
Explanation of Solution
Write the pitch line velocity for gear 2.
Here, the rotational speed of gear 2 is
Write the pitch line velocity for gear 3.
Here, the rotational speed of gear 3 is
Write the pitch line velocity for gear 4.
Here, the rotational speed of gear 4 is
Write the pitch line velocity for gear 5.
Here, the rotational speed of gear 5 is
Write the rotational speed of gear 4.
Write the rotational speed of gear 5.
Conclusion:
Substitute
Thus, the pitch line velocity for gear 2 is
Substitute
Thus, the pitch line velocity for gear 3 is
Substitute
Substitute
Substitute
Thus, the pitch line velocity for gear 4 is
Substitute
Thus, the pitch line velocity for gear 5 is
(c)
The tangential force on gear 2.
The radial force on gear 2.
The total force on gear 2.
The tangential force on gear 3.
The radial force on gear 3.
The total force on gear 3.
The tangential force on gear 4.
The radial force on gear 4.
The total force on gear 4.
The tangential force on gear 5.
The radial force on gear 5.
The total force on gear 5.
(c)

Answer to Problem 36P
The tangential force on gear 2 is
The radial force on gear 2 is
The total force on gear 2 is
The tangential force on gear 3 is
The radial force on gear 3 is
The total force on gear 3 is
The tangential force on gear 4 is
The radial force on gear 4 is
The total force on gear 4 is
The tangential force on gear 5 is
The radial force on gear 5 is
The total force on gear 5 is
Explanation of Solution
Write the tangential load on the gear 2.
Here, the power in
Write the tangential load on the gear 3.
Write the tangential load on the gear 4.
Write the tangential load on the gear 5.
Write the radial load on gear 2.
Write the total load on gear 2.
Write the radial load on gear 3.
Write the total load on gear 3.
Write the radial load on gear 4.
Write the total load on gear 4.
Write the radial load on gear 5.
Write the total load on gear 5.
Conclusion:
Substitute
Thus, the tangential force on gear 2 is
Substitute
Thus, the tangential force on gear 3 is
Substitute
Thus, the tangential force on gear 4 is
Substitute
Thus, the tangential force on gear 5 is
Substitute
Thus, the radial force on gear 2 is
Substitute
Thus, the total force on gear 2 is
Substitute
Thus, the radial force on gear 3 is
Substitute
Thus, the total force on gear 3 is
Substitute
Thus, the radial force on gear 4 is
Substitute
Thus, the total force on gear 4 is
Substitute
Thus, the radial force on gear 5 is
Substitute
Thus, the total force on gear 5 is
(d)
The input torque.
(d)

Answer to Problem 36P
The input torque is
Explanation of Solution
Write the input torque.
Conclusion:
Substitute
Thus, the input torque is
(e)
The output torque.
(e)

Answer to Problem 36P
The output torque is
Explanation of Solution
Write the output torque.
Conclusion:
Substitute
Thus, the output torque is
Want to see more full solutions like this?
Chapter 13 Solutions
Shigley's Mechanical Engineering Design (McGraw-Hill Series in Mechanical Engineering)
- A set of gears is used to reduce the speed from an electric motor to a shaft driving a grocery checkout conveyor, depicted below. The gear on the motor shaft is a 10-pitch pinion, has 18 teeth, and drives at 1200 rpm clockwise. The driven gear has 72 teeth. The motor has failed and is to be replaced with the only motor available, a 600 rpm motor with an 8-pitch pinion. Specify the set of commercially available 20⁰ spur gears, by number of teeth (N3and N4), that would result in the same conveyor speed and can be used without modification to the mounting (the center distance must not change). Find the number of teeth N3 on the pinion (drive) gear (teeth): Find the number of teeth N4 on the driven gear (teeth):arrow_forward(Q.1) A compound epicyclic gear is shown in Fig. for Q.1. The shaft P is drivenat 3000 rev/min while the annulus A2 is driven at 1000 rev/min in theopposite direction. The numbers of teeth in the gears are S1, 16; S2,24; A1, 60; A2, 90. Determine the speed and direction of rotation ofshaft Q. (Q.2) A compound epicyclic gear is shown in Fig. for Q.2. C and D form acompound wheel which rotates freely on shaft G. The planet wheels B andE rotate on pins fixed in arms attached to shaft G. C and F have internalteeth: the others have external teeth with the following numbers: A, 40;B, 30; D, 50; E, 20. If A rotates at 500 rev/min and wheel F is fixed,find the speed of shaft G.arrow_forwardProvide the complete step-by-step solution, given data, conversion of units, and sketch for this problem. A turbine at 30,000 rpm is used to drive a reduction gear delivering 3 hp at 3,000rpm. The gears are 20 degrees involute herringbone gears of 28 pitch and 2 1/8 ineffective width. The pinion has 20 teeth with a helix angle of 23 deg. Determine theload normal to the tooth surface. A. 20.4 lbs B. 24.4 lbs C. 28.4 lbs D. 32.4arrow_forward
- Two mating involute spur gears of 20 pressure angle have a gear ratio of 2. The number of teeth on the pinion is 20 and its speed is 250 r.p.m. The module pitch of teeth is 10 mm. If the addendum on each wheel is such that the path of approach and the path of recess on each side are half the maximum possible length cach, find: i) the addendum for pinion and gear wheel, i) the length of arc of contact, iiithe maximum velocity of sliding during approach and recess. Assume pinion to be driver.arrow_forwarda pinion has 56.716 teeth of 5.96mm module and runs at 2.265 rev/min with a torque of 39.961N.m. it meshes with a gear wheel which has 124.409 teeth. the gears operate with a pressure angle of 27.61 degrees and a contact ratio of 31.22. If the path of recess is 1.2 times the path of approach, determine the path of recessarrow_forwardFor a pair of spur gears, one design decision is to specify the pressure angles. Please select the common values of pressure angle per textbook. 300 200 250arrow_forward
- The gears of a gear wheel with a module of 4 mm, width of 60 mm and number of 18 teeth were broken during operation. If the gear wheel is made of cast iron (GG-25), with what torque is it loaded? Given: Speed factor Kv= 1.25; kuarrow_forwardlb pair of bevel gears having 20 and 75 teeth are used on axes that intersect at a 90" angle. Determine the velocity ratio and the pitch angles. of both gears.arrow_forwardPlease solve in 30 min The teeth number of each gear is already given (e.g. Z₁ =14). If the rotation speed of gear 1 is n₁=380 r/min, calculate the rotation speed of gear carrier Harrow_forward
- Two spur gears of 24 teeth and 36 teeth of 8 mm module and 20° pressure angle are in mesh. Addendum of each gear is 7.5 mm. The teeth are of involute form. Determine : 1. the angle through which thepinion turns while any pair of teeth are in contact, and 2. the velocity of sliding between the teethwhen the contact on the pinion is at a radius of 102 mm. The speed of the pinion is 450 r.p.marrow_forward2) Two mating internal 10-pitch, spur gears have 16 and 86 teeth. Determine the center distance. 3) Two mating external 8-pitch, 20o , spur gears have 24 and 64 teeth. Determine the contact ratio. 4) Two mating 20°, 8-pitch, spur gears have 14 and 42 teeth. Will they interfere? 5) A pair of 20°, mild-steel gears are to be selected for an application where they need to transfer 5 hp. The pinion drives at 1800 rpm and the gear must rotate as close to 480 rpm as possible. Select a set of gears to accomplish this task. a) Determine a suitable diametral pitch and pressure angle. b) Use the required velocity ratio to iterate and determine appropriate number of teeth (confirm that these gears are commercially available). c) Calculate the pitch diameters and center distance.arrow_forwardTwo spur gears transmit 36kW with a velocity ratio of 2:1. The speed of the smaller driving gear is 100rpm. The centre distance between the shafts is to be as near as possible to 920mm. If m=10 and all-21MPa, determine a) Diameter of the shafts b)PCD for each wheel c)Number of teeth on each wheel d) Actual centre distance [ e) Width of the teetharrow_forward
- Elements Of ElectromagneticsMechanical EngineeringISBN:9780190698614Author:Sadiku, Matthew N. O.Publisher:Oxford University PressMechanics of Materials (10th Edition)Mechanical EngineeringISBN:9780134319650Author:Russell C. HibbelerPublisher:PEARSONThermodynamics: An Engineering ApproachMechanical EngineeringISBN:9781259822674Author:Yunus A. Cengel Dr., Michael A. BolesPublisher:McGraw-Hill Education
- Control Systems EngineeringMechanical EngineeringISBN:9781118170519Author:Norman S. NisePublisher:WILEYMechanics of Materials (MindTap Course List)Mechanical EngineeringISBN:9781337093347Author:Barry J. Goodno, James M. GerePublisher:Cengage LearningEngineering Mechanics: StaticsMechanical EngineeringISBN:9781118807330Author:James L. Meriam, L. G. Kraige, J. N. BoltonPublisher:WILEY
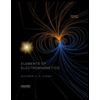
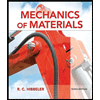
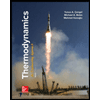
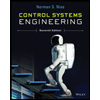
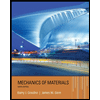
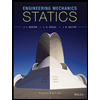