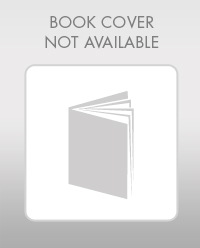
Concept explainers
a)
To develop: A gross requirements plan for all the items.
Introduction:
Gross requirements plan:
The gross requirements plan is the plan where the independent and dependent demand for a product or a component before the on-hand inventory and the scheduled receipts are netted with.
a)

Explanation of Solution
Given information:
Product structure:
Master production
MPS for X1 | ||||||
Period | 7 | 8 | 9 | 10 | 11 | 12 |
Gross requirements | 50 | 20 | 100 |
Inventory and lead time:
Item | X1 | B1 | B2 | A1 | C | D | E |
Lead time | 1 | 2 | 2 | 1 | 1 | 1 | 3 |
On hand | 50 | 20 | 20 | 5 | 0 | 0 | 10 |
Item X1:
Week | ||||||||||||
Item X1 | 1 | 2 | 3 | 4 | 5 | 6 | 7 | 8 | 9 | 10 | 11 | 12 |
Gross requirements | 50 | 20 | 100 | |||||||||
Order release | 50 | 20 | 100 |
The gross requirements are 50, 20 and 100 (1 assembly of X1) in weeks 8, 10 and 12 respectively derived from the master production schedule of X1. The lead time is 1 week. Therefore, the order release will be 50, 20 and 100 in weeks 7, 9 and 11 respectively.
Item B1:
Week | ||||||||||||
Item B1 | 1 | 2 | 3 | 4 | 5 | 6 | 7 | 8 | 9 | 10 | 11 | 12 |
Gross requirements | 50 | 20 | 100 | |||||||||
Order release | 50 | 20 | 100 |
The order release of X1 will become the gross requirements of B1. The gross requirements are 50, 20 and 100 (1 assembly of B1) in weeks 7, 9 and 11 respectively. The lead time is 2 weeks. Therefore, the order release will be 50, 20 and 100 in weeks 5, 7 and 9 respectively.
Item B2:
Week | ||||||||||||
Item B2 | 1 | 2 | 3 | 4 | 5 | 6 | 7 | 8 | 9 | 10 | 11 | 12 |
Gross requirements | 100 | 40 | 200 | |||||||||
Order release | 100 | 40 | 200 |
The order release of X1 will become the gross requirements of B2. The gross requirements are 100, 40 and 200 (2 assemblies of B2) in weeks 7, 9 and 11 respectively. The lead time is 2 weeks. Therefore, the order release will be 100, 40 and 200 in weeks 5, 7 and 9 respectively.
Item A1:
Week | ||||||||||||
Item A1 | 1 | 2 | 3 | 4 | 5 | 6 | 7 | 8 | 9 | 10 | 11 | 12 |
Gross requirements | 50 | 20 | 100 | |||||||||
Order release | 50 | 20 | 100 |
The order release of B1 will become the gross requirements of A1. The gross requirements are 50, 20 and 100 (1 assembly of A1) in weeks 5, 7 and 9 respectively. The lead time is 1 week. Therefore, the order release will be 50, 20 and 100 in weeks 4, 6 and 8 respectively.
Item C:
Week | ||||||||||||
Item C | 1 | 2 | 3 | 4 | 5 | 6 | 7 | 8 | 9 | 10 | 11 | 12 |
Gross requirements | 200 | 80 | 400 | |||||||||
Order release | 200 | 80 | 400 |
The order release of B2 will become the gross requirements of C. The gross requirements are 200, 80 and 400 (2 assemblies of C) in weeks 5, 7 and 9 respectively. The lead time is 1 week. Therefore, the order release will be 200, 80 and 400 in weeks 4, 6 and 8 respectively.
Item D:
Week | ||||||||||||
Item D | 1 | 2 | 3 | 4 | 5 | 6 | 7 | 8 | 9 | 10 | 11 | 12 |
Gross requirements | 100 | 40 | 200 | |||||||||
Order release | 100 | 40 | 200 |
The order release of B2 will become the gross requirements of D. The gross requirements are 100, 40 and 200 (2 assemblies of C) in weeks 5, 7 and 9 respectively. The lead time is 1 week. Therefore, the order release will be 100, 40 and 200 in weeks 4, 6 and 8 respectively.
Item E:
Week | ||||||||||||
Item E | 1 | 2 | 3 | 4 | 5 | 6 | 7 | 8 | 9 | 10 | 11 | 12 |
Gross requirements | 200 | 50 | 80 | 20 | 400 | 100 | ||||||
Order release | 200 | 50 | 80 | 20 | 400 | 100 |
The order release of B1 and D will become the gross requirements of E. The gross requirements are 50, 20 and 100 (1 assembly of E) in weeks 5, 7 and 9 respectively. The lead time is 3 weeks. Therefore, the order release will be 50, 20 and 100 in weeks 2, 4 and 6 respectively.
The gross requirements are 200, 80 and 400 (2 assembly of E) in weeks 4, 6 and 8 respectively. The lead time is 3 weeks. Therefore, the order release will be 200, 80 and 400 in weeks 1, 3 and 5 respectively.
b)
To develop: A net requirements plan for all the items.
Introduction:
Net requirements plan:
The net requirements plan is the plan which is established on the gross requirements plan formed by deducting the stock on and the scheduled receipts. If the total requirement is below the safety stock levels, a planned order is made based on the given lot sizing technique.
b)

Explanation of Solution
Given information:
Product structure:
Master production schedule for X1:
MPS for X1 | ||||||
Period | 7 | 8 | 9 | 10 | 11 | 12 |
Gross requirements | 50 | 20 | 100 |
Inventory and lead time:
Item | X1 | B1 | B2 | A1 | C | D | E |
Lead time | 1 | 2 | 2 | 1 | 1 | 1 | 3 |
On hand | 50 | 20 | 20 | 5 | 0 | 0 | 10 |
Item X1:
Week | ||||||||||||
Item X1 | 1 | 2 | 3 | 4 | 5 | 6 | 7 | 8 | 9 | 10 | 11 | 12 |
Gross requirements | 50 | 20 | 100 | |||||||||
Scheduled receipt | ||||||||||||
On hand (50) | 50 | 0 | 0 | |||||||||
Net requirement | 0 | 20 | 100 | |||||||||
Planned order receipt | 20 | 100 | ||||||||||
Planned order release | 20 | 100 |
Week 8:
The gross requirement is 50 (1 assembly)derived from the master production schedule of X1. The on hand inventory is 50. Hence, the net requirement is 0. The lead time is 1 week. Therefore, there will be no planned order release.
Week 10:
The gross requirement is 20 (1 assembly) derived from the master production schedule of X1. The on hand inventory is 0. Hence, the net requirement is 20. The lead time is 1 week. Therefore, the planned order release will be 20 in week 9 which will be the planned order receipt in week 10.
Week 12:
The gross requirement is 100 (1 assembly) derived from the master production schedule of X1. The on hand inventory is 0. Hence, the net requirement is 100. The lead time is 1 week. Therefore, the planned order release will be 100 in week 11 which will be the planned order receipt in week 12.
Item B1:
Week | ||||||||||||
Item B1 | 1 | 2 | 3 | 4 | 5 | 6 | 7 | 8 | 9 | 10 | 11 | 12 |
Gross requirements | 20 | 100 | ||||||||||
Scheduled receipt | ||||||||||||
On hand (20) | 20 | 0 | ||||||||||
Net requirement | 0 | 100 | ||||||||||
Planned order receipt | 100 | |||||||||||
Planned order release | 100 |
Week 9:
The gross requirement is 20 (1 assembly) derived from the planned order release of X1. The on hand inventory is 20. Hence, the net requirement is 0. The lead time is 2 weeks. Therefore, there will be no planned order release.
Week 11:
The gross requirement is 100 (1 assembly) derived from planned order release of X1. The on hand inventory is 0. Hence, the net requirement is 100. The lead time is 2 weeks. Therefore, the planned order release will be 100 in week 9 which will be the planned order receipt in week 11.
Item B2:
Week | ||||||||||||
Item B2 | 1 | 2 | 3 | 4 | 5 | 6 | 7 | 8 | 9 | 10 | 11 | 12 |
Gross requirements | 40 | 200 | ||||||||||
Scheduled receipt | ||||||||||||
On hand (20) | 20 | 0 | ||||||||||
Net requirement | 20 | 200 | ||||||||||
Planned order receipt | 20 | 200 | ||||||||||
Planned order release | 20 | 200 |
Week 9:
The gross requirement is 40 (2 assembly) derived from the planned order release of X1. The on hand inventory is 20. Hence, the net requirement is 20. The lead time is 2 weeks. Therefore, the planned order release will be 20 in week 7 which will be the planned order receipt in week 9.
Week 11:
The gross requirement is 200 (2 assembly) derived from planned order release of X1. The on hand inventory is 0. Hence, the net requirement is 200. The lead time is 2 weeks. Therefore, the planned order release will be 200 in week 9 which will be the planned order receipt in week 11.
Item A1:
Week | ||||||||||||
Item A1 | 1 | 2 | 3 | 4 | 5 | 6 | 7 | 8 | 9 | 10 | 11 | 12 |
Gross requirements | 100 | |||||||||||
Scheduled receipt | ||||||||||||
On hand (5) | 5 | |||||||||||
Net requirement | 95 | |||||||||||
Planned order receipt | 95 | |||||||||||
Planned order release | 95 |
Week 9:
The gross requirement is 100 (1 assembly) derived from the planned order release of B1. The on hand inventory is 5. Hence, the net requirement is 95. The lead time is 1 week. Therefore, the planned order release will be 95 in week 8 which will be the planned order receipt in week 9.
Item C:
Week | ||||||||||||
Item C | 1 | 2 | 3 | 4 | 5 | 6 | 7 | 8 | 9 | 10 | 11 | 12 |
Gross requirements | 40 | 400 | ||||||||||
Scheduled receipt | ||||||||||||
On hand (0) | 0 | 0 | ||||||||||
Net requirement | 40 | 400 | ||||||||||
Planned order receipt | 40 | 400 | ||||||||||
Planned order release | 40 | 400 |
Week 7:
The gross requirement is 40 (2 assembly) derived from the planned order release of B2. The on hand inventory is 0. Hence, the net requirement is 40. The lead time is 1 week. Therefore, the planned order release will be 40 in week 6 which will be the planned order receipt in week 7.
Week 9:
The gross requirement is 400 (2 assembly) derived from planned order release of B2. The on hand inventory is 0. Hence, the net requirement is 400. The lead time is 1 week. Therefore, the planned order release will be 400 in week 8 which will be the planned order receipt in week 9.
Item D:
Week | ||||||||||||
Item D | 1 | 2 | 3 | 4 | 5 | 6 | 7 | 8 | 9 | 10 | 11 | 12 |
Gross requirements | 20 | 200 | ||||||||||
Scheduled receipt | ||||||||||||
On hand (0) | 0 | 0 | ||||||||||
Net requirement | 20 | 200 | ||||||||||
Planned order receipt | 20 | 200 | ||||||||||
Planned order release | 20 | 200 |
Week 7:
The gross requirement is 20 (1 assembly) derived from the planned order release of B2. The on hand inventory is 0. Hence, the net requirement is 20. The lead time is 1 week. Therefore, the planned order release will be 20 in week 6 which will be the planned order receipt in week 7.
Week 9:
The gross requirement is 200 (1 assembly) derived from planned order release of B2. The on hand inventory is 0. Hence, the net requirement is 200. The lead time is 1 week. Therefore, the planned order release will be 200 in week 8 which will be the planned order receipt in week 9.
Item E:
Week | ||||||||||||
Item E | 1 | 2 | 3 | 4 | 5 | 6 | 7 | 8 | 9 | 10 | 11 | 12 |
Gross requirements | 40 | 400 | 100 | |||||||||
Scheduled receipt | ||||||||||||
On hand (10) | 10 | 0 | 0 | |||||||||
Net requirement | 30 | 400 | 100 | |||||||||
Planned order receipt | ||||||||||||
Planned order release | 30 | 400 | 100 |
Week 6:
The gross requirement is 40 (2 assembly) derived from the planned order release of B2. The on hand inventory is 10. Hence, the net requirement is 30. The lead time is 3 weeks. Therefore, the planned order release will be 30 in week 3 which will be the planned order receipt in week 6.
Week 8:
The gross requirement is 400 (2 assembly) derived from the planned order release of B2. The on hand inventory is 0. Hence, the net requirement is 400. The lead time is 3 weeks. Therefore, the planned order release will be 400 in week 5 which will be the planned order receipt in week 8.
Week 9:
The gross requirement is 100 (1 assembly) derived from the master production schedule of B1. The on hand inventory is 0. Hence, the net requirement is 100. The lead time is 3 weeks. Therefore, the planned order release will be 100 in week 6 which will be the planned order receipt in week 9.
Want to see more full solutions like this?
Chapter 14 Solutions
Principles Of Operations Management
- What are examples of three tasks involved in the requirements-gathering and analysis phase?arrow_forwardNote:- Do not provide handwritten solution. Maintain accuracy and quality in your answer. Take care of plagiarism. Answer completely. 14.) A part structure, lead time (weeks), and on-hand quantities for product A are shown in Figure 14. From the information shown, generate: a) An indented bell of material for product A. b) Net requirements for each part to produce 10 As in week 8 using lot-for-lot. Figure 14:arrow_forwardWhat will be projected on hand inventory of item S in week6?arrow_forward
- Product A is assembled from two units of S1 and threeunits of S2. S1 is made of one unit of C1, four units of C2,and one unit of C3. S2 is made of three units of C2 and twounits of C3.a. Draw a product structure diagram for product A.b. How many C3’s are needed to fill an order for 100 A’s?c. Assume no inventory on hand, products take one day to assemble, subassemblies take two days and compo-nents take three days. When should an order be re-leased for C3 if the 100 A’s are needed by day 7?arrow_forwardDevelop a material requirements plan for component H. Lead times for the end item and each component except B are one week. The lead time for B is three weeks. Sixty units of A are needed at the startof week 8. There are currently 15 units of B on hand and 130 of E on hand, and 50 units of H are inproduction and will be completed by the start of week 2. Lot-for-lot ordering will be used for all items.arrow_forwardProduct X is made of 2 units of Y and 3 of Z. Y is made of 1 unit of A and 2 units of B. Z is made of 2 units of A and 4 units of C. Lead Time of X is 1 week: Y - 2 weeks; Z – 3 weeks; A – 2 weeks; B – 1 week; and C – 3 weeks. Scheduled receipt on week 5 are: A = 250 and Z = 135. If 150 units of X are needed in week 10 & 100 units in week 12, develop a planning schedule showing when each item should be ordered and in what quantity. Use lot for lot except for Y & C which requires minimum of 400 units. Determine the timing of planned release of component Z for the order of 150 units.arrow_forward
- Product X is made of 2 units of Y and 3 of Z. Y is made of 1 unit of A and 2 units of B. Z is made of 2 units of A and 4 units of C. Lead Time of X is 1 week: Y - 2 weeks; Z – 3 weeks; A – 2 weeks; B – 1 week; and C – 3 weeks. Scheduled receipt on week 5 are: A = 250 and Z = 135. If 150 units of X are needed in week 10 & 100 units in week 12, develop a planning schedule showing when each item should be ordered and in what quantity. Use lot for lot except for Y & C which requires minimum of 400 units. Determine the total gross requirement of “A”arrow_forwardWhat are the other managerial applications that might be found once the material requirements plan technique is established ?arrow_forwardFigure shows the BOMs for two products, A and B. Table 1 shows the MPS quantity start date for each one. Table 2 contains data from inventory records for items C, D, and E. There are no safety stock requirements for any of the items.a. Determine the material requirements plan for items C, D, and E for the next 8 weeks.b. What specific managerial actions are required in week 1?c. Suppose that a very important customer places an emergency order for a quantity of product A. To satisfy this order, a new MPS of 200 units of product A is now required in week 5. Determine the changes to the material requirements plan if this order is accepted and note any problems that you detect. MPS Quantity Start Dates Date Product 1 2 3 4 5 6 7 8 A 125 95 150 130 B 80 70 Inventory Record Data Item Data Category C D E Lot-sizing rule L4L POQ 1P = 32 FOQ = 800 Lead time 3 weeks 2 weeks 1 weeks Scheduled receipts 200 (week 2) None 800 (week 1) Beginning…arrow_forward
- Consider the following product structure (bill of material). One hundred and fifty (150) units of Product A are needed in week 10. Assuming no on-hand inventory of A exists, explode the bill of material, and use the following information to construct a net requirements plan for all the items. You must use the template provided by the instructor and provide all the information needed on the template. There are no scheduled receipts for all the items. Item On-hand Inventory Lead time (weeks) A 0 2 B 20 2 C 10 1 D 0 3 E 5 1 F 10 3 Item: LT= 1 2 3 4 5 6 7 8 9 10 11 12 Gross Requirements Scheduled Receipts Projected on Hand Net Requirements…arrow_forwardProduct A consists of subassemblies B and C. Subassembly B requires two parts of D and one part of E. Subassembly C requires one part of D and one part of F.a. Draw a product structure tree (BOM) for this product.b. How many parts are needed to make 300 units of finishedproduct?arrow_forwardExplain the significance of a Requirements Management Plan (RMP) in complex projects. How does it ensure requirements are well-defined and properly managed?arrow_forward
- Practical Management ScienceOperations ManagementISBN:9781337406659Author:WINSTON, Wayne L.Publisher:Cengage,Operations ManagementOperations ManagementISBN:9781259667473Author:William J StevensonPublisher:McGraw-Hill EducationOperations and Supply Chain Management (Mcgraw-hi...Operations ManagementISBN:9781259666100Author:F. Robert Jacobs, Richard B ChasePublisher:McGraw-Hill Education
- Purchasing and Supply Chain ManagementOperations ManagementISBN:9781285869681Author:Robert M. Monczka, Robert B. Handfield, Larry C. Giunipero, James L. PattersonPublisher:Cengage LearningProduction and Operations Analysis, Seventh Editi...Operations ManagementISBN:9781478623069Author:Steven Nahmias, Tava Lennon OlsenPublisher:Waveland Press, Inc.
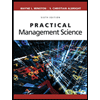
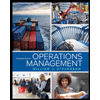
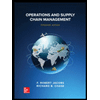
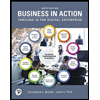
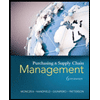
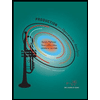