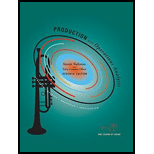
Concept explainers
(a)
To determine: The optimal rotational cycle time.
Introduction:Economic order quantity refers to the approach which is used to evaluate flow and volume of order needed to fulfill consumers demand while reducing the cost per order.Such tool is used by the organization to handle andmanage operations and logistic operations.
(a)

Explanation of Solution
Optimal cycle time of the fiber store is as follows.
Apply variables of each type of items and determine optimal cycle time by the following formula.
Similarly, the modified holding cost for each of the item should be calculated by the following method.
Item | Annual Sales | Cost | |||||
A | 25,900 | 1125000 | .003 | .00063 | .000615 | 120 | 15.9285 |
B | 42,000 | 1375000 | .002 | .00042 | .000407 | 80 | 17.094 |
C | 14,400 | 825000 | .008 | .00168 | .00165 | 160 | 23.76 |
D | 46,000 | 800000 | .002 | .00042 | .000395 | 80 | 18.17 |
E | 12,500 | 450000 | .001 | .0021 | .002041 | 60 | 25.5125 |
F | 75,000 | 975000 | .005 | .00105 | .000969 | 120 | 72.675 |
G | 30,000 | 725000 | .004 | .00084 | .000805 | 20 | 24.15 |
H | 18,900 | 300000 | .007 | .00147 | .001377 | 60 | 26.0253 |
SUM | 0.008259 | 700 | 223.315 |
Put the value of each item to determine the optimal cycle time.
Hence, the optimal rotation cycle time is 2.50 per year
(b)
To determine:TheSize of the lots.
Introduction: Economic order quantity sometimes EOQ refers to the technique used by the organizations to determine the volume and frequency or order needed to fulfill the customer demand while minimizing the cost of the item.
(b)

Explanation of Solution
Determine the optimal quantity of each item by the following formula.
Same procedure will be followed to calculate optimal quantity for each item
Item | Demand | Time | Quantity (Q) |
A | 25,900 | 2.5 | 64750 |
B | 42,000 | 2.5 | 105000 |
C | 14,400 | 2.5 | 36000 |
D | 46,000 | 2.5 | 115000 |
E | 12,500 | 2.5 | 31250 |
F | 75,000 | 2.5 | 187500 |
G | 30,000 | 2.5 | 75000 |
H | 18,900 | 2.5 | 47250 |
(C)
To determine:Average annual cost of holding and setup cost at the optimal solution.
Introduction: Economic order quantity sometimes EOQ refers to the technique used by the organizations to determine the volume and frequency or order needed to fulfill the customer demand while minimizing the cost of the item.
(C)

Explanation of Solution
Procedure to find average annual cost of holding and setup cost is discussed below.
Determine the annual holding and setup cost by the following formula.
Determine the values to calculate annual holding cost for the item A by the following method
Same procedure will be followed to calculate optimal quantity for each item
Item | Setup cost (K*D/Q) | Holding Cost (H*Q/2) | Total |
A | 48 | 19.91 | 67.91 |
B | 32 | 21.37 | 53.37 |
C | 64 | 29.70 | 93.70 |
D | 32 | 22.71 | 54.71 |
E | 24 | 31.89 | 55.89 |
F | 48 | 90.84 | 138.84 |
G | 8 | 30.19 | 38.19 |
H | 24 | 32.53 | 56.53 |
SUM | 559.14 |
Hence, annual cost of holding and setup is $559.14
(d)
To determine: Contractual obligation that G might have with the fabrics that would stop them from implementing the policy mention in part (a) and (b).
Introduction:Economic order quantity sometimes EOQ refers to the technique used by the organizations to determine the volume and frequency or order needed to fulfill the customer demand while minimizing the cost of the item.
(d)

Explanation of Solution
With the responsibility or obligation, the time required to supply 3 shipments will be 4 times in a year instead of 2.5. Hence, the size of the optimal quantity will vary as the cycle time being changed to 4 times in a year.
Hence, to make shipment thrice in a year it is very much important for the firm to change its cycle time and optimal quantity of every item to remain focused in their commitment.
Want to see more full solutions like this?
Chapter 4 Solutions
Production and Operations Analysis, Seventh Edition
- Assume the demand for a companys drug Wozac during the current year is 50,000, and assume demand will grow at 5% a year. If the company builds a plant that can produce x units of Wozac per year, it will cost 16x. Each unit of Wozac is sold for 3. Each unit of Wozac produced incurs a variable production cost of 0.20. It costs 0.40 per year to operate a unit of capacity. Determine how large a Wozac plant the company should build to maximize its expected profit over the next 10 years.arrow_forwardThe Western Jeans Company purchases denim from Cumberlend Texille Mills. The Westen Jeuns Company uses 35,000 yards of denim per yenr to make jeans. The cost of ordering denim Tron the textile company is $500 per order. It costs Western $0.35 per yard nnnually to hold a yard of denim in Inventory. Determine the optimal number of yards of denim the Western leans Company should order, the minimum total annual inventory cost, the optimal umber of ueden per yeur, and the optimal time between orders.arrow_forwardRam Roy's firm has developed the following supply, demand, cost, and inventory data. Supply Available Period Regular Time Overtime Subcontract Demand Forecast 1 30 15 5 40 2 30 15 5 45 3 30 20 5 50 Initial inventory 20 units Regular-time cost per unit $100 Overtime cost per unit $160 Subcontract cost per unit $200 Carrying cost per unit per month $4 Assume that the initial inventory has no holding cost in the first period and backorders are not permitted. Part 2 Allocating production capacity to meet demand at a minimum cost using the transportation method, the total cost is $enter your response here (enter your response as a whole number).arrow_forward
- The TransCanada Lumber Company and Mill processes 10,000 logs annually, operating 250 days per year. Imme-diately upon receiving an order, the logging company’s supplier begins delivery to the lumber mill at the rate of 60 logs per day. The lumber mill has determined that the or-dering cost is $1600 per order, and the cost of carrying logs in inventory before they are processed is $15 per log on anannual basis. Determine the following:a. The optimal order sizeb. The total inventory cost associated with the optimalorder quantityc. The number of operating days between ordersd. The number of operating days required to receive anorderarrow_forwardThe Olde Town Microbrewery makes Townside beer,which it bottles and sells in its adjoining restaurant and bythe case. It costs $1700 to set up, brew, and bottle a batchof the beer. The annual cost to store the beer in inventory is$1.25 per bottle. The annual demand for the beer is 21,000bottles and the brewery has the capacity to produce 30,000bottles annually.a. Determine the optimal order quantity, total annual inventory cost, the number of production runs per year, andthe maximum inventory level.b. If the microbrewery has only enough storage space tohold a maximum of 2500 bottles of beer in inventory,how will that affect total inventory costs?arrow_forwardANT Infra orders two kinds of precast items: A and B for use in its projects from two different suppliers. The precasts are needed throughout the entire 52-week year. Precast A are used at a relatively constant rate and are ordered whenever the remaining quantity drops to the reorder level. While, precast B is ordered from a supplier who delivers by every three weeks. Data for both precast items are as follows:Item Precast A Precast BAnnual demand 10,000 5,000Holding cost (% of item cost)20% 20%Order cost $150 $25Lead time 4 weeks 1 weekSafety stock 55 units 5 unitsItem cost $10.00 $2.00 a. Employ Q system for precast A and calculate the EOQ, the reorder point, total inventory cost? b. Employ P system for precast B and estimate the target level inventory and total inventory cost?arrow_forward
- A medical facility’s demand for N95 respirators and disposable gloves is deterministic and stable at a rate of 20 respirators per day and 100 gloves per day. The distributor charges $20 per pack of 20 respirators and $10 for a pack of 25 gloves. The distributor offered the healthcare facility the following plan: whenever the medical facility places a single order for both N95 respirators and gloves, the distributor will package one pack of respirators together with two packs of gloves to minimize shipping volume. The remainder of the order of gloves will be sent in the second shipment (without any extra shipping cost), which will be timed so that the healthcare facility receives the second shipment just before it runs out of gloves inventory. The shortages are not allowed. The fixed cost of placing an order is $10 and the holding cost rate is a 20% annual interest rate (assume 365 days per year). Calculate the average annual cost for this inventory system. If the lead time from the…arrow_forwardThree suppliers A, B and C, each produce road grit which has to be delivered to council depots W, X, Y and Z. The stock held at each supplier and the demand from each depot is known. The cost, in pounds, of transporting one lorry load of grit from each supplier to each depot is also known. This information is given in the table. Suppliers Depot W Depot X Depot Y Depot Z Stock (Lorry Loads) Supplier A 180 110 130 290 14 Supplier B 190 250 150 280 16 Supplier C 240 270 190 120 20 Demand (Lorry Loads) 11 15 14 10 50 Use VAT method to supply out all the stocksarrow_forwardCatlea Merchandising is engaged in selling school shoesfor both boys and girls in their teenage years. Catlea needs 32,000 pairs of shoes in a year in order to satisfy the market demand. It costs ₱ 48 to place an order while ₱ 8 is needed to hold each quantity of shoe in Catlea's inventory. Upon checking on Catlea's supplier, it takes 8 days in between placing an order and eventually receiving it. a. Determine the Economic Order Quantityb. Determine the number of order per monthc. Determine the reorder pointarrow_forward
- Happy Pet, Inc., is a large pet store located in LongBeach Mall. Although the store specializes in dogs, it a lso sellsfish, turtle, and bird supplies. The Everlast Leader, a leather leadfor dogs, costs Happy Pet $7 each. There is an annual demand for6,000 Everlast Leaders. The manager, Stephan Wagner, has determinedthat the ordering cost is $20 per order and the carrying cost,as a percentage of unit cost, is 15%. Happy Pet is now consideringa new supplier of Everlast Leaders. Each lead would cost only$6.65, but, in order to get this discount, Happy Pet would have tobuy shipments of 3,000 at a time. Should Happy Pet use the newsupplier and take this discount for quantity buying?arrow_forwardMetaverse LLP is a laptop manufacturing company located at Bengaluru, India. One of the main components of the laptop is the Hard Disk Drive (HDD). The inventory of this item is controlled by the EOQ model. Presently the company imports 40 GB HDD from Micron Components and Devices at a unit price of $60 and a 15 day delivery time. Metaverse needs to determine the amount to order each time an order is placed. They also need to determine when to place the order. The forecasted demand for the coming year for the 40GB HDD is 3,000 units. The company incurs a high ordering cost of $225 per order. The average annual inventory holding cost is estimated to be 25% of the item cost and a safety stock of 25 HDDs is maintained. The company operates for 300 days a year. However, Micron wants to drastically increase prices of HDDs which is not acceptable to Metaverse. The purchase officer of Metaverse has identified another supplier Minnesota Data Products. This supplier is willing to supply at…arrow_forward3. Cynthia Knott’s oyster bar buys fresh Louisiana oysters for $5 per pound and sells them for $12 per pound. Any oysters not sold that day are sold to her cousin, who has a nearby grocery store, for $1 per pound. Cynthia believes that demand follows the normal distribution, with a mean of 100 pounds and a standard deviation of 15 pounds. a) What is the cost of underestimating demand for each pound? b) What is the overage cost per pound? c) How many pounds of oyster should she order each day? d) What is the stockout risk for this order size?arrow_forward
- Practical Management ScienceOperations ManagementISBN:9781337406659Author:WINSTON, Wayne L.Publisher:Cengage,
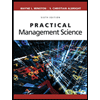