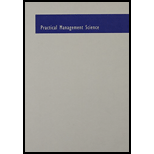
Practical Management Science, Loose-leaf Version
5th Edition
ISBN: 9781305631540
Author: WINSTON, Wayne L.; Albright, S. Christian
Publisher: Cengage Learning
expand_more
expand_more
format_list_bulleted
Concept explainers
Question
Chapter 5, Problem 80P
Summary Introduction
To determine: The way to maximize the profit of Company K.
Introduction: In linear programming, unbounded solution would occur when the objective function is infinite. If no solution satisfied the constraints then it is said to be unfeasible solution.
Expert Solution & Answer

Want to see the full answer?
Check out a sample textbook solution
Students have asked these similar questions
Company ZWZ manufactures three products in a serial system; Product XA is manufactured in Stage 1, Product XB in Stage 2, and XC in Stage 3. Product XB has a sales potential in the market; hence, some of it can be sold at the end of Stage 2, and
the remaining can be moved to Stage 3. The third stage produces Product XC, and then delivers it to customers. Two units of Product XA produced in Stage 1 are required for each unit of Product XB in Stage 2. In addition, four units of Product XB
produced in Stage 2 are required for each unit of Product XC in Stage 3.
Stage 1 can only use regular time; however, Stage 2 has the options of using regular time and overtime in manufacturing. On the other hand, Stage 3 has only one alternative, which is subcontracting. The pertinent data are provided below:
Stage 2
Stage 1
11
No overtime
No
subcontracting
No sales
0.07
Unit regular time cost (TL)
Unit overtime cost (TL)
Unit subcontracting cost (TL)
Unit selling price (TL)
Unit processing time (hrs)…
During an eight-hour shift, 750 non-defective parts are desired as a result of a manufacturing operation. The default operation time is 15 minutes. As the operators of machine are inexperienced, the actual time they take to perform the operation is 20 minutes, and, on average, a fifth of the parts that start to be manufactured are lost. Assuming that each one of the machines used in this operation will not be available for one hour in each shift, determine the number of machines needed.
Design capacity is the ability of the company to produce the quantity of goods and services within a particular period of time when the company have best condition to produce and when the company have unlimited resources. These resource's includes- Men, Machinery, Material etc. It shows the maximum capacity of the company to produce.
Effective capacity refers to the ability of the company to produce maximum quantity within a particular period of time to achieve in current production condition and current resources. It shows the real outcome capacity of the firm when the company produce within their own current condition of their production.
Question
Why is the capacity design important?
Chapter 5 Solutions
Practical Management Science, Loose-leaf Version
Ch. 5.2 - Prob. 1PCh. 5.2 - Prob. 2PCh. 5.2 - Prob. 3PCh. 5.2 - Prob. 4PCh. 5.2 - Prob. 5PCh. 5.2 - Prob. 6PCh. 5.2 - Prob. 7PCh. 5.2 - Prob. 8PCh. 5.2 - Prob. 9PCh. 5.3 - Prob. 10P
Ch. 5.3 - Prob. 11PCh. 5.3 - Prob. 12PCh. 5.3 - Prob. 13PCh. 5.3 - Prob. 14PCh. 5.3 - Prob. 15PCh. 5.3 - Prob. 16PCh. 5.3 - Prob. 17PCh. 5.3 - Prob. 18PCh. 5.4 - Prob. 19PCh. 5.4 - Prob. 20PCh. 5.4 - Prob. 21PCh. 5.4 - Prob. 22PCh. 5.4 - Prob. 23PCh. 5.4 - Prob. 24PCh. 5.4 - Prob. 25PCh. 5.4 - Prob. 26PCh. 5.4 - Prob. 27PCh. 5.4 - Prob. 28PCh. 5.4 - Prob. 29PCh. 5.5 - Prob. 30PCh. 5.5 - Prob. 31PCh. 5.5 - Prob. 32PCh. 5.5 - Prob. 33PCh. 5.5 - Prob. 34PCh. 5.5 - Prob. 35PCh. 5.5 - Prob. 36PCh. 5.5 - Prob. 37PCh. 5.5 - Prob. 38PCh. 5 - Prob. 42PCh. 5 - Prob. 43PCh. 5 - Prob. 44PCh. 5 - Prob. 45PCh. 5 - Prob. 46PCh. 5 - Prob. 47PCh. 5 - Prob. 48PCh. 5 - Prob. 49PCh. 5 - Prob. 50PCh. 5 - Prob. 51PCh. 5 - Prob. 52PCh. 5 - Prob. 53PCh. 5 - Prob. 54PCh. 5 - Prob. 55PCh. 5 - Prob. 56PCh. 5 - Prob. 57PCh. 5 - Prob. 58PCh. 5 - Prob. 59PCh. 5 - Prob. 60PCh. 5 - Prob. 61PCh. 5 - Prob. 62PCh. 5 - Prob. 63PCh. 5 - Prob. 64PCh. 5 - Prob. 65PCh. 5 - Prob. 66PCh. 5 - Prob. 67PCh. 5 - Prob. 68PCh. 5 - Prob. 69PCh. 5 - Prob. 70PCh. 5 - Prob. 71PCh. 5 - Prob. 72PCh. 5 - Prob. 73PCh. 5 - Prob. 74PCh. 5 - Prob. 75PCh. 5 - Prob. 76PCh. 5 - Prob. 77PCh. 5 - Prob. 80PCh. 5 - Prob. 81PCh. 5 - Prob. 82PCh. 5 - Prob. 83PCh. 5 - Prob. 85PCh. 5 - Prob. 86PCh. 5 - Prob. 87PCh. 5 - Prob. 2C
Knowledge Booster
Learn more about
Need a deep-dive on the concept behind this application? Look no further. Learn more about this topic, operations-management and related others by exploring similar questions and additional content below.Similar questions
- The Tinkan Company produces one-pound cans for the Canadian salmon industry. Each year the salmon spawn during a 24-hour period and must be canned immediately. Tinkan has the following agreement with the salmon industry. The company can deliver as many cans as it chooses. Then the salmon are caught. For each can by which Tinkan falls short of the salmon industrys needs, the company pays the industry a 2 penalty. Cans cost Tinkan 1 to produce and are sold by Tinkan for 2 per can. If any cans are left over, they are returned to Tinkan and the company reimburses the industry 2 for each extra can. These extra cans are put in storage for next year. Each year a can is held in storage, a carrying cost equal to 20% of the cans production cost is incurred. It is well known that the number of salmon harvested during a year is strongly related to the number of salmon harvested the previous year. In fact, using past data, Tinkan estimates that the harvest size in year t, Ht (measured in the number of cans required), is related to the harvest size in the previous year, Ht1, by the equation Ht = Ht1et where et is normally distributed with mean 1.02 and standard deviation 0.10. Tinkan plans to use the following production strategy. For some value of x, it produces enough cans at the beginning of year t to bring its inventory up to x+Ht, where Ht is the predicted harvest size in year t. Then it delivers these cans to the salmon industry. For example, if it uses x = 100,000, the predicted harvest size is 500,000 cans, and 80,000 cans are already in inventory, then Tinkan produces and delivers 520,000 cans. Given that the harvest size for the previous year was 550,000 cans, use simulation to help Tinkan develop a production strategy that maximizes its expected profit over the next 20 years. Assume that the company begins year 1 with an initial inventory of 300,000 cans.arrow_forwardIt costs a pharmaceutical company 75,000 to produce a 1000-pound batch of a drug. The average yield from a batch is unknown but the best case is 90% yield (that is, 900 pounds of good drug will be produced), the most likely case is 85% yield, and the worst case is 70% yield. The annual demand for the drug is unknown, with the best case being 20,000 pounds, the most likely case 17,500 pounds, and the worst case 10,000 pounds. The drug sells for 125 per pound and leftover amounts of the drug can be sold for 30 per pound. To maximize annual expected profit, how many batches of the drug should the company produce? You can assume that it will produce the batches only once, before demand for the drug is known.arrow_forwardAssume the demand for a companys drug Wozac during the current year is 50,000, and assume demand will grow at 5% a year. If the company builds a plant that can produce x units of Wozac per year, it will cost 16x. Each unit of Wozac is sold for 3. Each unit of Wozac produced incurs a variable production cost of 0.20. It costs 0.40 per year to operate a unit of capacity. Determine how large a Wozac plant the company should build to maximize its expected profit over the next 10 years.arrow_forward
- Design capacity is the ability of the company to produce the quantity of goods and services within a particular period of time when the company have best condition to produce and when the company have unlimited resources. These resource's includes- Men, Machinery, Material etc. It shows the maximum capacity of the company to produce. Effective capacity refers to the ability of the company to produce maximum quantity within a particular period of time to achieve in current production condition and current resources. It shows the real outcome capacity of the firm when the company produce within their own current condition of their production. In design capacity it is assume that the company will produce in best and ideal condition to produce goods and services while in Effective capacity it is assume that company will produce in current operating conditions. In design capacity it is assume that the company have unlimited resource's. It means these resource's include:- Men,…arrow_forwardJoan has a small design and tailoring shop making custom outfits for women. She has two employees. Each employee only begins working on a dress when a customer order has been received and then she makes the dress from beginning to end. The average production time of a dress is 1.8 days, with a standard deviation of 2.1 days. Historically, Joan has been receiving orders with interarrival times of one day on average. The interarrival times of orders have a coefficient of variation of one. (Carry at least 4 decimal places in all intermediate calculations. Round your final answer to 2 decimal places.) What is the expected waiting time, in days, between when an order is received and when production begins on the dress? A. 9.12 days B. 6.50 days C. 1.23 days D.3.41 daysarrow_forwardSolve the question below using the attached excel templates with formulas for renting both slow and fast copies (labeled in the excel tabs). Question: The Decision Sciences Department is trying to determine whether to rent a slow or a fast copier. The department believes that an employee’s time is worth $15 per hour. The slow copier rents for $4 per hour, and it takes an employee an average of 10 minutes to complete copying. The fast copier rents for $15 per hour, and it takes an employee an average of six minutes to complete copying. On average, four employees per hour need to use the copying machine. (Assume the copying times and interarrival times to the copying machine are exponentially distributed.) Which machine should the department rent to minimize expected total cost per hour?arrow_forward
- A manufacturing plant produces a product 'A' that requires one unit of 'B' and ½ unit of 'C'. Each unit of 'B' is comprised of one unit of 'D', two units of 'E', and one unit of 'F'. Each unit of 'C' requires ½ unit of 'G' and three units of 'H'. The manufacturing lead times for the components are as follows: 'A' - two weeks, 'B' - one week, 'C' - two weeks, 'D' - two weeks, 'E' - three weeks, 'F' - one week, 'G' - two weeks, 'H' - one week. There are 20 units in stock for each of these components. 100 units of 'A' are needed for delivery in seven weeks: a) Develop the product structure and indexed bill of materials for the product. b) Create a gross and net requirements plan for the manufacturer of the product.arrow_forwardA manufacturing firm has four plants and wants to find the most efficient means of meeting the requirements of its four customers. The relevant information for the plants and customers, along with shipping costs in dollars per unit, are shown in the table below: Customer (requirement) Factory (capacity) Customer 1 (125) Customer 2 (150) Customer 3 (175) Customer 4 (75) A (100) $ 15 $ 10 $ 20 $ 17 B (75) $ 20 $ 12 $ 19 $ 20 C (100) $ 22 $ 20 $ 25 $ 14 D (250) $ 21 $ 15 $ 28 $ 12 How many supply nodes are present in this problem? Multiple Choice: 4 3 1 8 16arrow_forwardThe College of Business and Public Administration at Benton University has a copy machine on each floor for faculty use. Heavy use of the five copy machines causes frequent failures. Maintenance records show that a machine fails every 2.5 days (or l = 0.40 failure/day). The college has a maintenance contract with the authorized dealer of the copy machines. Because the copy machines fail so frequently, the dealer has assigned one person to the college to repair them. The person can repair an average of 2.5 machines per day. Using the finite-source model, answer the followingquestions: a. What is the average utilization of the maintenance person?b. On average, how many copy machines are being repaired or waiting to be repaired?c. What is the average time spent by a copy machine in the repair system (waiting and being repaired)?arrow_forward
arrow_back_ios
arrow_forward_ios
Recommended textbooks for you
- Practical Management ScienceOperations ManagementISBN:9781337406659Author:WINSTON, Wayne L.Publisher:Cengage,
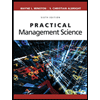
Practical Management Science
Operations Management
ISBN:9781337406659
Author:WINSTON, Wayne L.
Publisher:Cengage,