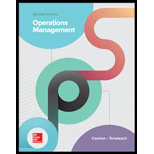
Operations Management
2nd Edition
ISBN: 9781260484687
Author: CACHON, Gerard
Publisher: MCGRAW-HILL HIGHER EDUCATION
expand_more
expand_more
format_list_bulleted
Question
Chapter 6, Problem 2C
Summary Introduction
Case summary:
The case deals with the highland plant of Company F. Initially, the workers of Company F have received $2.30 for a 9-hour shift. It is mentioned that typically 1,000 workers did not show up for the work among 13,000 workers. Employee turnover is 370 percent. Shift timing was limited to 8-hour duration and wages were increased to $5 in January 1914. In 1908, cost of Model T is $850, which is $20,763 in 2013. After 1927, the cost of the model is $260, which is $3,372 in 2013.
To determine: The average tenure of a worker.
Expert Solution & Answer

Want to see the full answer?
Check out a sample textbook solution
Students have asked these similar questions
Action Learning refers to target training which is intended to solve an actual problem.
True
False
6.
Mateo works on an assembly line in a factory. Last month the assembly line processes were overhauled. Mateo is still responsible for soldering electrical contacts on an appliance component, but now he is also expected to review each component for quality defects after he solders. If he notes any defects, he can place the component in the scrap bin. If he scraps five such pieces in succession, he is permitted to press an emergency button which stops the assembly line completely. This job redesign reflects the ___________ philosophy.
a)
job specialization
b)
job rotation
c)
job enrichment
d)
job enlargement
A startup company is considering making a part by injection molding. The part is moderately complex and the volume of the part is about 10 cubic centimeters. Assume that the part is designed for injection molding and can be made with a two part mold. The company needs to make 250,000 parts made from ABS plastic. Once the mold is made it will take a worker 1 minute to make one part using the injection molding machine. The company will use contract manufacturing to produce the parts. Estimate the cost per part and explain how you came up with the number. (If you are stuck look at the Contract Manufacturing Cost per Unit section. Also keep in mind that there is no exact right answer, the goal is to come up with a reasonable estimate.)
Contract Manufacturing Cost per Unit: It’s not uncommon to hire another company to perform some or all the manufacturing for a product. To estimate the cost use
((Cost of Parts and Materials) + (man hours) × $40)/.75
Chapter 6 Solutions
Operations Management
Ch. 6 - Prob. 1CQCh. 6 - Prob. 2CQCh. 6 - Prob. 3CQCh. 6 - Prob. 4CQCh. 6 - Prob. 5CQCh. 6 - Prob. 6CQCh. 6 - Prob. 7CQCh. 6 - A learning curve following the power law has what...Ch. 6 - Prob. 9CQCh. 6 - Prob. 10CQ
Ch. 6 - Prob. 11CQCh. 6 - The learning curve coefficient LCC(10, 0.8)...Ch. 6 - Prob. 13CQCh. 6 - Instead of using the learning curve coefficient...Ch. 6 - Prob. 15CQCh. 6 - Prob. 16CQCh. 6 - Prob. 17CQCh. 6 - Prob. 18CQCh. 6 - Prob. 19CQCh. 6 - Prob. 20CQCh. 6 - Prob. 21CQCh. 6 - Prob. 22CQCh. 6 - Prob. 23CQCh. 6 - Prob. 24CQCh. 6 - Prob. 25CQCh. 6 - Prob. 1PACh. 6 - Prob. 2PACh. 6 - Prob. 3PACh. 6 - Prob. 4PACh. 6 - Prob. 5PACh. 6 - Prob. 6PACh. 6 - Prob. 7PACh. 6 - Prob. 8PACh. 6 - Prob. 9PACh. 6 - Prob. 10PACh. 6 - A company has 2200 employees, on average, and it...Ch. 6 - Prob. 12PACh. 6 - Prob. 13PACh. 6 - Prob. 14PACh. 6 - In October 1908, just prior to the launch of his...Ch. 6 - Prob. 2CCh. 6 - Prob. 3C
Knowledge Booster
Learn more about
Need a deep-dive on the concept behind this application? Look no further. Learn more about this topic, operations-management and related others by exploring similar questions and additional content below.Similar questions
- The cumulative average labor cost per unit for the first batch (of 100 units) produced using a new process is P200. The cumulative average labor cost after the second batch is P140.Assuming that the learning curve continues, the cumulative (total) labor cost of eight batches is P80,000 P56,000 P39,200 P54,880arrow_forwardJackson and Dal both start working as "attendees" at the new full-service carwash, each starting at the same pay rate. Jackson gives the customer exactly what they request and is a friendly employee. Dal is very open and approachable and his shifts usually find the carwash selling more "extras" to the customers, such as upholstery detailing. Based on this, you could say that: Multiple Choice Dal has a higher use value than Jackson. Jackson has a higher exchange value than Dal. Jackson has a higher use value than Dal. Dal has a higher exchange value than Jackson.arrow_forwardPlease answer all parts clearly & make sure you round it if askedarrow_forward
- Employee absenteeism reduces the productivity of the work. True or Falsearrow_forwardSchumacher & Company recently introduced a new ATM system. The Company’s MoneyMatic Division assembles these systems from purchased hardware, using its in-house developed software. It just completed assembling the first batch of 15 units. The last unit (#15) produced required 50 hours of labor, and the learning rate was estimated to be 94 percent for these systems. Another order for 25 units (#16 - #40) of the same system has just arrived. 1) What is the estimated time for the 40th unit? 2) How many total labor hours will be needed to satisfy this second batch (#16 - #40) ? 3) What is the average time to produce this second batch?arrow_forwardThe first unit took 100 hours to produce. It is expected that an 80% learning curve will apply. You are required to estimate the following times: Property of and for the exclusive use of SLU. Reproduction, storing in a retrieval system, distributing, uploading or posting online, or transmitting in any form or by any means, electronic, mechanical, photocopying, recording, or otherwise of any part of this document, without the prior written permission of SLU, is strictly prohibited. 154 a. The cumulative average time per unit to produce three units. b. The total time it will take to produce three units c. The incremental time for the forth and fifth units, in totalarrow_forward
- Which of the following is true of automation? Group of answer choices The development of automation has created jobs across all industries. Automated machines make more errors. Automation discourages innovation. Automation helps to improve products and services. Automation was the earliest step in the development of machines and machine-controlling devices.arrow_forwardA learning curve of 80% assumes that direct labor costs are reduced by 25% for each doubling of output. What is the cost of the sixteenth unit produced?arrow_forwardIs there a feature in the acquisition and spending management system that would prevent a worker from generating fake vouchers to steal money?arrow_forward
- ces There is a single commonly accepted definition of "employee" used by courts, employers, and the government. True or False True Falsearrow_forwardDo you happen to be able to think of any way to increase the machine's production while simultaneously decreasing the amount of time it needs to be repaired?arrow_forwardThe Colonial Housearrow_forward
arrow_back_ios
SEE MORE QUESTIONS
arrow_forward_ios
Recommended textbooks for you
- Practical Management ScienceOperations ManagementISBN:9781337406659Author:WINSTON, Wayne L.Publisher:Cengage,Operations ManagementOperations ManagementISBN:9781259667473Author:William J StevensonPublisher:McGraw-Hill EducationOperations and Supply Chain Management (Mcgraw-hi...Operations ManagementISBN:9781259666100Author:F. Robert Jacobs, Richard B ChasePublisher:McGraw-Hill Education
- Purchasing and Supply Chain ManagementOperations ManagementISBN:9781285869681Author:Robert M. Monczka, Robert B. Handfield, Larry C. Giunipero, James L. PattersonPublisher:Cengage LearningProduction and Operations Analysis, Seventh Editi...Operations ManagementISBN:9781478623069Author:Steven Nahmias, Tava Lennon OlsenPublisher:Waveland Press, Inc.
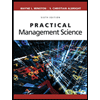
Practical Management Science
Operations Management
ISBN:9781337406659
Author:WINSTON, Wayne L.
Publisher:Cengage,
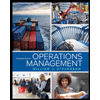
Operations Management
Operations Management
ISBN:9781259667473
Author:William J Stevenson
Publisher:McGraw-Hill Education
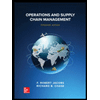
Operations and Supply Chain Management (Mcgraw-hi...
Operations Management
ISBN:9781259666100
Author:F. Robert Jacobs, Richard B Chase
Publisher:McGraw-Hill Education
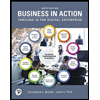
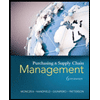
Purchasing and Supply Chain Management
Operations Management
ISBN:9781285869681
Author:Robert M. Monczka, Robert B. Handfield, Larry C. Giunipero, James L. Patterson
Publisher:Cengage Learning
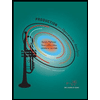
Production and Operations Analysis, Seventh Editi...
Operations Management
ISBN:9781478623069
Author:Steven Nahmias, Tava Lennon Olsen
Publisher:Waveland Press, Inc.
Process selection and facility layout; Author: Dr. Bharatendra Rai;https://www.youtube.com/watch?v=wjxS79880MM;License: Standard YouTube License, CC-BY