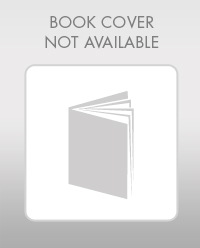
a)
To determine: The theoretical minimum number of workstations.
a)

Answer to Problem 23P
The theoretical minimum number of workstations is 5 workstations.
Explanation of Solution
Given information:
Task | Time (seconds) | Immediate predecessors |
A | 40 | - |
B | 30 | A |
C | 50 | A |
D | 40 | B |
E | 6 | B |
F | 25 | C |
G | 15 | C |
H | 20 | D, E |
I | 18 | F, G |
J | 30 | H, I |
Total | 274 |
- Output is 60 iStars / hour
Calculation of cycle time:
The requirement is to produce 60 iStars / hour. Hence, the cycle time for one iStar will be:
Formula to calculate theoretical minimum number of workstations:
Calculation of theoretical minimum number of workstations:
The theoretical minimum number of workstations is 5 workstations.
b)
To balance: The assembly line.
b)

Explanation of Solution
Precedence diagram:
List of most following tasks:
Tasks | Following tasks |
A | 9 |
B | 4 |
C | 4 |
D | 2 |
E | 2 |
F | 2 |
G | 2 |
H | 1 |
I | 1 |
J | 0 |
Assignment of different tasks to different workstations:
Workstation | Elligible tasks | Selected tasks | Task time (seconds) | Available cycle time (seconds) | Remarks |
1 | 60 | ||||
A | A | 40 | 20 | ||
B,C | 20 (Idle time) | Cycle time is less than task time | |||
2 | 60 | ||||
B, C | C | 7 | 50 | Tie broken randomnly | |
B, F, G | 10 (Idle time) | Cycle time is less than task time | |||
3 | 60 | ||||
B, F, G | B | 30 | 30 | Task B has most following tasks. | |
D, E, F, G | F | 25 | 24 | Tie broken randomnly | |
D, E, G | 1 (Idle time) | Cycle time is less than task time | |||
4 | 60 | ||||
D, E, G | D | 40 | 20 | Tie broken randomnly | |
E, G | G | 15 | 5 | Tie broken randomnly | |
E,I | 5 (Idle time) | Cycle time is less than task time | |||
5 | 60 | ||||
E, I | E | 6 | 54 | Task E has most following tasks. | |
I, H | H | 20 | 34 | Tie broken randomnly | |
I | I | 18 | 2 | Task I is only elligible task | |
2 (Idle time) | |||||
6 | 60 | ||||
J | J | 30 | 30 | Task J is the remaining task | |
30 (Idle time) |
Workstation | Task assigned | Idle time |
1 | A | 20 |
2 | C | 10 |
3 | B, F | 1 |
4 | D, G | 5 |
5 | E, H, I | 2 |
6 | J | 30 |
Total | 68 |
c)
To determine: The actual number of workstations.
c)

Answer to Problem 23P
The actual number of workstations is 6.
Explanation of Solution
Workstation | Task assigned | Idle time |
1 | A | 20 |
2 | C | 10 |
3 | B, F | 1 |
4 | D, G | 5 |
5 | E, H, I | 2 |
6 | J | 30 |
Total | 68 |
The actual number of workstations is 6.
d)
To determine: The efficiency.
Introduction:
Efficiency:
Efficiency is the measure of what is actually produced as opposed to what can be theoretically produced with the same amount of resources.
d)

Answer to Problem 23P
The efficiency is 76.11%.
Explanation of Solution
Formula to calculate efficiency:
Calculation of efficiency:
The efficiency is 76.11%.
Want to see more full solutions like this?
Chapter 9 Solutions
Principles Of Operations Management
- A Missouri job shop bas four departments- machining (M), dipping in a chemical bath (D), finishing (F), and plating (P)-assigned to four work areas. The operations manager, MaryMarrs, bas gathered the following data for this job shop as it is currently laid out (Plan A). It costs $0.50 to move workpiece foot in the job shop.Marrs's goal is to find a layout that bas the lowest materialhandlingcost.a) Detemline cost of the current layout, Plan A, from the given data.b) One alternative is to switch those departments with the high loads, namely, finishing (F) and plating (P), which alters the distance between them and machining (M) and dipping (D), as follows: What is the cost of this layout?Marrs now wants you to evaluate Plan C, which also switches milling (M) and dri lling (D), below.…arrow_forwardWhat are the key factors that firms consider while designing a facility layout? List five major factors. What kind of layout is best suited for a Pharmaceuticals manufacturing firm?arrow_forwardFor the given set of tasks, do the following:a. Develop the precedence diagram.b. Determine the minimum cycle time and then calculate the cycle time for a desired output of 500 units in a seven-hour day. Why might a manager use a cycle time of 50 seconds?c. Determine the minimum number of workstations for output of 500 units per day. Balance the line using the greatest positional weight heuristic. Break ties with the most following tasks heuristic. Use a cycle time of 50 seconds.e. Calculate the percentage idle time for the line.TaskTask Time(seconds)ImmediatePredecessorA 45 —B 11 AC 9 BD 50 —E 26 DF 11 EG 12 CH 10 CI 9 F, G, HJ 10 I193arrow_forward
- An assembly line is to operate eight hours per day with a desired output of 240 units perday. The following table contains information on this product’s task times and precedencerelationships: Task Task Time (Seconds) Immediate Predecessor A 60 — B 80 A C 20 A D 50 A E 90…arrow_forwardReid Chocolates (see Problem 9.6) has another Jayoutto consider. Layout 4 is shown below. What is the total tripdistance?arrow_forwardBob’s Boat Factory is reevaluating its boat’s facility layout. The current layout is shown below along with the from–to matrix. Bob has to leave department C in its current location because relocation costs are too high. It is considering exchanging departments B and D. Evaluate the proposal by computing the ld score for both layouts.arrow_forward
- Smart Manufacturing's production engineers are reviewing the layout of their assembly line for their leading product. The line will operate eight hours a day with a desired output of 240 units per day. The following table contains information about this product's task times and precedence relationships: TASK Task Time (seconds) Immediate Precedent A 60 -- B 80 A C 20 A D 50 A E 90 B,C F 30 C,D G 30 E, F H 60 G Determine: a) Network of activities (precedence diagram) b) Cycle time c) The required number of workstations d) Evaluate the solution by the appropriate line balance heuristicarrow_forwardSue Helms Appliances wants to establish an assembly line to manufacture its new product, the Micro Popcorn Popper. The goal is to produce five poppers per hour. The tasks, task times, and immediate predecessors for producing one Micro Popcorn Popper are as follows: Task Performance Time (mins) Task Must Follow Task Listed Below A 8 − B 11 A C 10 A, B D 9 B, C E 8 C F 4 D, E A C F B E D In the diagram, there are 6 circles labeled using the letters from A to F. There are 8 of arrows, and each arrow connects one circle to another circle. The arrows are situated in the following manner: A to B, A to C, B to C, C to D, B to D, C to E, D to F, and E to F. Part 2 a) The theoretical minimum number of workstations=55 (round your response up to the…arrow_forwardStanford Rosenberg Computing wants to establish anassembly line for producing a new product, the Personal DigitalAssistant (PDA). The tasks, task times, and immediate predecessorsfor the tasks are as follows: Rosenberg's goal is to produce 180 PDAs per hour.a) What is the cycle time?b) What is the theoretical minimum for the number of workstations that Rosenberg can achieve in this assembly line?c) Can the theoretical minimum actually be reached when workstations are assigned?arrow_forward
- Use the longest work element rule to balance the assembly line described in the following table and Figure so that it will produce 40 units per hour.a. What is the cycle time?b. What is the theoretical minimum number of workstations?c. Which work elements are assigned to each workstation?d. What are the resulting efficiency and balance delay percentages?e. Use the shortest work element rule to balance the assembly line. Do you note any changes in solution? Work Element Time (Sec) Immediate Predecessor(s) A B C D E F G H I J K 40 80 30 25 20 15 60 45 10 75 15 None A A B C B B D E,G F H,I,Jarrow_forwardWhat make each construction project unique? a. Size of the proposed structure b. Location c. Design features d. Site constraints e. All of the abovearrow_forwardWhat is a criterion for evaluating the layout of a workcenter ?arrow_forward
- Practical Management ScienceOperations ManagementISBN:9781337406659Author:WINSTON, Wayne L.Publisher:Cengage,Operations ManagementOperations ManagementISBN:9781259667473Author:William J StevensonPublisher:McGraw-Hill EducationOperations and Supply Chain Management (Mcgraw-hi...Operations ManagementISBN:9781259666100Author:F. Robert Jacobs, Richard B ChasePublisher:McGraw-Hill Education
- Purchasing and Supply Chain ManagementOperations ManagementISBN:9781285869681Author:Robert M. Monczka, Robert B. Handfield, Larry C. Giunipero, James L. PattersonPublisher:Cengage LearningProduction and Operations Analysis, Seventh Editi...Operations ManagementISBN:9781478623069Author:Steven Nahmias, Tava Lennon OlsenPublisher:Waveland Press, Inc.
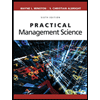
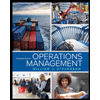
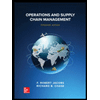
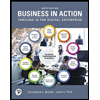
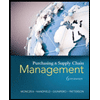
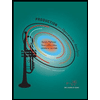