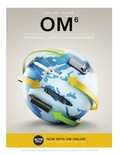
EBK OM
6th Edition
ISBN: 9781305888210
Author: Collier
Publisher: YUZU
expand_more
expand_more
format_list_bulleted
Concept explainers
Question
Chapter 17, Problem 9PA
Summary Introduction
Interpretation: The CT scan process of the hospital is to be depicted in a flowchart. The Lean principles to be followed to reduce throughput time is to be suggested based on the value added and non-value-added tasks.
Concept Introduction: Lean process is a method that aims to reduce waste and improve efficiency. It focuses on effectively providing value to the customers by improving the products and services delivered.
Expert Solution & Answer

Want to see the full answer?
Check out a sample textbook solution
Students have asked these similar questions
Bayside General Hospital is trying to streamline its operations. A problem-solving group consisting of a nurse, a technician, a doctor, an administrator, and a patient is examining outpatient procedures in an effort to speed up the process and make it more cost-effective. Listed here are the steps that a typical patient follows for diagnostic imaging:
• Patient enters main hospital entrance
• Patient takes a number and waits to be called to registration desk
• Patient registers
• Patient is taken to diagnostic imaging department
• Patient registers at diagnostic imaging reception
• Patient sits in department waiting area until dressing area clears
• Patient changes in dressing area
• Patient waits in dressing area
• Patient is taken to exam room
• Exam is performed
• Patient is taken to dressing area
• Patient dresses
• Patient leaves
1. Create a service blueprint of the procedure and identify opportunities for improvement.
2. Describe what elements of a servicescape would make this…
Bayside General Hospital is trying to streamline its operations. A problem-solving group consisting of a nurse, a technician, a doctor, an administrator, and a patient is examining outpatient procedures in an effort to speed up the process and make it more cost-effective. Listed here are the steps that a typical patient follows for diagnostic imaging:
Patient enters main hospital entrance
Patient takes a number and waits to be called to registration desk
Patient registers
Patient is taken to diagnostic imaging department
Patient registers at diagnostic imaging reception
Patient sits in department waiting area until dressing area clears
Patient changes in dressing area
Patient waits in dressing area
Patient is taken to exam room
Exam is performed
Patient is taken to dressing area
Patient dresses
Patient leaves
Create a service blueprint of the procedure and identify opportunities for improvement.
Describe what elements of a servicescape would make this…
In the welding operations of a bicycle manufacturer, a bike frame has a flow time of about 11.5 hours. The time in the welding operation is spent as follows: 2 hours waiting in front of the cutting machine for the batch to start, 2 hours waiting for the setup of the machine, 1 hour waiting for the other pieces of the batch to go through cutting, 1 minute at the cutting machine, and 3 hours waiting for the transfer to the welding machine. Then, at the welding machine, the unit spends 1 hour waiting in front of the welding machine for the batch to start, 1 hour waiting for the setup of the welding machine, 0.5 hour waiting for the other pieces of the batch to go through welding, 0.5 minute at the welding machine, and 1 hour waiting for the transfer to the next department.
Determine the exact flow time. What is the value-added percentage of the flow time?(round percentage answer to 4 decimal places.)
answer:_______percent
Knowledge Booster
Learn more about
Need a deep-dive on the concept behind this application? Look no further. Learn more about this topic, operations-management and related others by exploring similar questions and additional content below.Similar questions
- Please build and simulate the following model in ARENA.In this model, car loan applications arrive at processing center approximately every 5 minutes. At this point, 1 of 5 loan officers will review the application to ensure that it is complete. This review step usually takes 15 minutes, but can be as short as 12 minutes or as long as 18 minutes. Applications are sent to an automatic processing machine where they are processed. This process can take from 0.5 to 1.5 hours to complete, but usually requires 1 hour. It is assumed that the automatic processor can process as many applications as needed.After processing, the results are reviewed by a loan officer who will write either an acceptance or rejection document. This task usually takes 7 minutes, but can require anywhere from 5 to 10 minutes to complete.At this point the loan application process is complete, and the acceptance or rejection document is sent to the customer.Run this simulation for one 8-hour day (5 replications).arrow_forwardSouth Beach University is conducting an online exam. There are 1,200 students taking this exam. Students are required to download the exam questions from the university’s learning management system (LMS), solve the questions, type their workings and answers in a computer word processing application, and submit the files back to the LMS. It is estimated that the LMS takes an average of 30 seconds to process a submission. For example, if a student submits his files at time T and the LMS is able to start processing his submitted files right away, it is estimated that the LMS accepts the submission at T + 30 seconds. The cut-off time of the exam is 12pm on the exam day, that is, if a submission cannot be accepted by the LMS by 12pm, it is considered late submission. Due to the capacity of the LMS servers, a maximum of 150 submissions can be processed at any point of time. Submissions are processed on a first-come-first-serve basis. If the number of submissions exceeds the capacity, some…arrow_forwardSouth Beach University is conducting an online exam. There are 1,200 students taking this exam. Students are required to download the exam questions from the university’s learning management system (LMS), solve the questions, type their workings and answers in a computer word processing application, and submit the files back to the LMS. It is estimated that the LMS takes an average of 30 seconds to process a submission. For example, if a student submits his files at time T and the LMS is able to start processing his submitted files right away, it is estimated that the LMS accepts the submission at T + 30 seconds. The cut-off time of the exam is 12pm on the exam day, that is, if a submission cannot be accepted by the LMS by 12pm, it is considered late submission.Due to the capacity of the LMS servers, a maximum of 150 submissions can be processed at any point of time. Submissions are processed on a first-come-first-serve basis. If the number of submissions exceeds the capacity, some…arrow_forward
- South Beach University is conducting an online exam. There are 1,200 students taking this exam. Students are required to download the exam questions from the university’s learning management system (LMS), solve the questions, type their workings and answers in a computer word processing application, and submit the files back to the LMS. It is estimated that the LMS takes an average of 30 seconds to process a submission. For example, if a student submits his files at time T and the LMS is able to start processing his submitted files right away, it is estimated that the LMS accepts the submission at T + 30 seconds. The cut-off time of the exam is 12pm on the exam day, that is, if a submission cannot be accepted by the LMS by 12pm, it is considered late submission. Due to the capacity of the LMS servers, a maximum of 150 submissions can be processed at any point of time. Submissions are processed on a first-come-first-serve basis. If the number of submissions exceeds the capacity, some…arrow_forwardBacala Software Systems operates a technical support center for its software customers. If customers have installation or user problems with Bacala software products, they may telephone the technical support center and obtain free consultation. Currently, Bacala operates its support center with one consultant. If the consultant is busywhen a new customer call arrives, the customer hears a recorded message stating that all consultants are currently busy with other customers. The customer is then asked to hold and the consultant will provide assistance as soon as possible. The customer calls follow a Poisson probability distribution with an arrival rate of five calls per hour.On average, it takes 7.5 minutes for a consultant to answer a customer’s questions. The service time follows an exponential probability distribution. (Please Answer a-c) thank you! a. What is the service rate in terms of customers per hour?b. What is the probability that no customers are in the system and the…arrow_forwardA hospital Emergency Room currently registers each patient first through an initial check-in process, where s/he is seen by a doctor at the check-in, and then exits the process, either with a prescription or with admission to the hospital. Currently, 50 people per hour arrive at the Emergency Room, 10 percent of who are admitted to the hospital. On average, 35 registered patients are waiting to see a doctor at any time during this process. The registration process takes, on average, 6 minutes per patient. Among patients who receive prescriptions, average time spent with a doctor is 10 minutes. Among those admitted to the hospital, average time of stay is 30 minutes. Steps 1, 3, and 5 have zero duration (triggers or decision points). On average, how many patients are waiting to be registered or in the registation process (step 1)? On average, how long does a patient spend in the ER? On average, how many patients are there in the ER? Assume the process to be stable; that is,…arrow_forward
- Glenn Dental Clinic provides general dental care to residents of Philadelphia on a walk-in basis. The clinic has started receiving complaints from patients that the waiting time is too long and has asked you to investigate whether this problem can be solved. Upon arrival, customers receive a form from the receptionist and fill out relevant information such as personal health records and insurance provider. The form is then handed back to the receptionist who enters the information into the computer system for the dentist to see. A dental assistant then takes an X-ray from the patient. A dentist then performs the checkup and discusses any issues with the patient. Based on conversations with staff members at the clinic, you have obtained the following information on the process: It takes about 5 minutes for a customer to fill out the paperwork. Entry of information on the paperwork into the system and verification with past records takes another 5 minutes for a receptionist. There are…arrow_forwardGlenn Dental Clinic provides general dental care to residents of Philadelphia on a walk-in basis. The clinic has started receiving complaints from patients that the waiting time is too long and has asked you to investigate whether this problem can be solved. Upon arrival, customers receive a form from the receptionist and fill out relevant information such as personal health records and insurance provider. The form is then handed back to the receptionist who enters the information into the computer system for the dentist to see. A dental assistant then takes an X-ray from the patient. A dentist then performs the checkup and discusses any issues with the patient. Based on conversations with staff members at the clinic, you have obtained the following information on the process: It takes about 5 minutes for a customer to fill out the paperwork. Entry of information on the paperwork into the system and verification with past records takes another 5 minutes for a receptionist. There are…arrow_forwardAt a cruise ship terminal, each day on average 1000 passengers embark on ships. Onaverage, passengers spend 5 days on their cruise before returning to this terminal. If theflow unit is a passenger, then what are the flow rate and flow time of this process?arrow_forward
- Please show in excel. The template is provided in the image. This is for a two-server system, not one. The Burger Dome is a fast-food restaurant that is currently appraising its customer service. In its current operation, an employee takes a customer’s order, tabulates the cost, receives payment from the customer, and then fills the order. Once the customer’s order is filled, the employee takes the order of the next customer waiting for service. Assume that time between each customer’s arrival is an exponential random variable with a mean of 1.35 minutes. Assume also that the time for the employee to complete the customer’s service is an exponential random variable with mean of 1 minute. Use the BurgerDome.xlsx template to complete a simulation model for the waiting line at Burger Dome for a 14-hour work day. Using the summary statistics gathered at the bottom of the spreadsheet model, answer the following questions. What is the average wait time experienced by a customer?…arrow_forwardFind a Doctor is a small startup that helps people find a physician who best meets their needs (location, insurance accepted, etc.). During a “slow” time for it, it has 8 staff members taking calls from customers. On average, one call arrives every 5 minutes (with a standard deviation of 5 minutes). Each staff member spends on average 18 minutes with each customer (with a standard deviation of 27.00 minutes). How long does one of their customers spend, on average, waiting on hold before he or she can start speaking to a representative?arrow_forwardMom and Pop own and operate the Fuzzy Belly Deli. On average, customers arrive at the deli every 6 minutes. Pop fulfills their orders one at a time. It takes him an average of 3 minutes to fulfill each order. Customers then proceed to the cash register, where Mom receives their payment. Mom loves to chat and is somewhat slow in operating the cash register, taking an average of 4 minutes to receive payment from each customer. Assume that customer interarrival times, as well as order fulfillment and payment times are exponentially distributed. What is the throughput of the deli's operation? What is the capacity of the deli's operation? On average, how long does a customer spend at the deli from the time she arrives until her order is fulfilled by Pop?arrow_forward
arrow_back_ios
SEE MORE QUESTIONS
arrow_forward_ios
Recommended textbooks for you
- Practical Management ScienceOperations ManagementISBN:9781337406659Author:WINSTON, Wayne L.Publisher:Cengage,
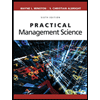
Practical Management Science
Operations Management
ISBN:9781337406659
Author:WINSTON, Wayne L.
Publisher:Cengage,