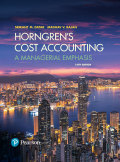
EBK HORNGREN'S COST ACCOUNTING
16th Edition
ISBN: 9780134475950
Author: Datar
Publisher: PEARSON CO
expand_more
expand_more
format_list_bulleted
Textbook Question
Chapter 19, Problem 19.28E
Nonfinancial measures of quality, manufacturing cycle efficiency. (CMA, adapted) Turnkey Manufacturing evaluates the performance of its production managers based on a variety of factors, including cost, quality, and cycle time. The following are nonfinancial measures for quality and time for 2016 and 2017 for its only product:
Nonfinancial Quality Measures | 2016 | 2017 |
Number of returned goods | 500 | 1,000 |
Number of defective units reworked | 2,500 | 2,000 |
Annual hours spent on quality training per employee | 36 | 54 |
Number of units delivered on time | 20,000 | 34,000 |
Annual Totals | 2016 | 2017 |
Units of finished goods shipped | 25,000 | 1,800 |
Average total hours worked per employee | 40,000 | 1,800 |
The following information relates to the average amount of time needed to complete an order:
Time to Complete an Order | 2016 | 2017 |
Wait time | ||
From customer placing order to order being received by production | 14 | 10 |
From order received by production to machine being set up for production | 9 | 7 |
Inspection time | 5 | 3 |
Process time | 4 | 4 |
Move time | 2 | 2 |
- 1. Compute the manufacturing cycle efficiency for an order for 2016 and 2017.
Required
- 2. For each year 2016 and 2017, calculate the following:
- a. Percentage of goods returned
- b. Defective units reworked as a percentage of units shipped
- c. Percentage of on-time deliveries
- d. Percentage of hours spent by each employee on quality training
- 3. Evaluate management’s performance on quality and timeliness in 2016 and 2017.
Expert Solution & Answer

Trending nowThis is a popular solution!

Students have asked these similar questions
Techno
Instruments uses a manufacturing costing system with one direct-cost category (direct materials) and three indirect-cost categories:
a.
Setup, production-order, and materials-handling costs that vary with the number of batches
b.
Manufacturing-operations costs that vary with machine-hours
c.
Costs of engineering changes that vary with the number of engineering changes made
In response to competitive pressures at the end of
2016,
Techno
Instruments used value-engineering techniques to reduce manufacturing costs. Actual information for
2016
and
2017
is as follows:
2016
2017
Setup, production-order, and materials-handling costs per batch
$8,600
$7,800
Total manufacturing-operations cost per machine-hour
$59
$53
Cost per engineering change
$18,750
$14,000
The management of Techno Instruments wants to evaluate whether value engineering has succeeded in reducing the target manufacturing cost per unit of one…
Question 3
The Buffalo Machine Sdn. Bhd. was evaluating its cost structure relating to quality costs. Below
items are the cost of quality in the year 2020. With this allocation of quality costs, the company lost
20% of sales due to poor performance. To improve the situation, the company would like to perform
the cost of quality analysis.
Items
Product Reliability Test
Process Quality Assurance Audit
Rework Cost
Production Inspection
Supplier Quality System Audit
Defect Repair Cost
Market Defect Cost
Sampling Inspection
Quality Assurance Training
Product Warranty Cost
Cost/RM
10000
8500
12000
12000
5500
18000
80000
8000
16000
40000
a) Identify the items for prevention, appraisal, and failure costs.
b) Compute the ratio of prevention, appraisal, and failure costs to total quality costs.
c) Based on the analysis of the cost of quality, recommend the company's actions to improve the
product quality.
Brant Freezer Warehouse Performance
2016 Figures
Units Shipped
12 Months 5 Months
Jan.-Dec. through
May 31
Units Shipped
Projected Actual
12 Months 5 Months
Jan.-Dec. May 31
Atlanta
17,431
4,080
35,890
18,000
Boston
6,920
3,061
27,915
7,200
Chicago 28,104
14,621 246,315
131,618 30,000
Denver
3,021
1,005a
28,019
8,600*
3,100
Fargo
2,016
980
16,411
8,883
2,000
Los Angeles 16,491 11,431
151,975 109,690
17,000
Portland
8,333
4,028
73,015
36,021
9,000
St. Louis
5,921
2,331
51,819
23,232
8,000
Warehouse Costs
12 Months 5 Months
Jan.-Dec. through
May 31
156,830
63,417
2017 Figures
a Denver warehouse closed by strike March 4-19, 2016.
Warehouse Costs
Budgeted Actual Costs
12 Months
Jan.-Dec.
4,035
178,000
3,119
73,000
15,230 285,000
1,421
31,000
804
17,000
9,444
176,000
4,600
85,000
2,116
56,000
through
May 31
40,228
29,416
141,222
14,900
9,605
93,280
42,616
19,191
Chapter 19 Solutions
EBK HORNGREN'S COST ACCOUNTING
Ch. 19 - Describe two benefits of improving quality.Ch. 19 - Prob. 19.2QCh. 19 - Name two items classified as prevention costs.Ch. 19 - Give two examples of appraisal costs.Ch. 19 - Distinguish between internal failure costs and...Ch. 19 - Describe three methods that companies use to...Ch. 19 - Companies should focus on financial measures of...Ch. 19 - Give two examples of nonfinancial measures of...Ch. 19 - Give two examples of nonfinancial measures of...Ch. 19 - When evaluating alternative ways to improve...
Ch. 19 - Distinguish between customer-response time and...Ch. 19 - Prob. 19.12QCh. 19 - Give two reasons why delays occur.Ch. 19 - Companies should always make and sell all products...Ch. 19 - Prob. 19.15QCh. 19 - Rector Corporation is examining its quality...Ch. 19 - Six Sigma is a continuous quality improvement...Ch. 19 - Costs of quality. (CMA, adapted) Osborn, Inc.,...Ch. 19 - Costs of quality analysis. Adirondack Company...Ch. 19 - Costs-of-quality analysis. Safe Travel produces...Ch. 19 - Costs of quality, quality improvement. iCover...Ch. 19 - Prob. 19.22ECh. 19 - Prob. 19.23ECh. 19 - Waiting time. Its a Dogs World (IDW) makes toys...Ch. 19 - Waiting time, service industry. The registration...Ch. 19 - Waiting time, cost considerations, customer...Ch. 19 - Nonfinancial measures of quality and time. For the...Ch. 19 - Nonfinancial measures of quality, manufacturing...Ch. 19 - Statistical quality control. Harvest Cereals...Ch. 19 - Quality improvement, Pareto diagram,...Ch. 19 - Quality improvement, relevant costs, and relevant...Ch. 19 - Quality improvement, relevant costs, and relevant...Ch. 19 - Waiting times, manufacturing cycle times. The...Ch. 19 - Prob. 19.34PCh. 19 - Manufacturing cycle times, relevant revenues, and...Ch. 19 - Compensation linked with profitability, waiting...Ch. 19 - Ethics and quality. Weston Corporation...Ch. 19 - Prob. 19.38P
Knowledge Booster
Learn more about
Need a deep-dive on the concept behind this application? Look no further. Learn more about this topic, accounting and related others by exploring similar questions and additional content below.Similar questions
- Nabors Company had actual quality costs for the year ended June 30, 20x5, as given below. At the zero-defect state, Nabors expects to spend 375,000 on quality engineering, 75,000 on vendor certification, and 50,000 on packaging inspection. Assume sales to be 25,000,000. Required: 1. Prepare a long-range performance report for 20x5. What does this report tell the management of Nabors? 2. Explain why quality costs still are present for the zero-defect state. 3. What if Nabors achieves the zero-defect state reflected in the report? What are some of the implications of this achievement?arrow_forwardIn 20X1, Don Blackburn, president of Price Electronics, received a report indicating that quality costs were 31% of sales. Faced with increasing pressures from imported goods. Don resolved to take measures to improve the overall quality of the companys products. After hiring a consultant in 20X1, the company began an aggressive program of total quality control. At the end of 20X5, Don requested an analysis of the progress the company had made in reducing and controlling quality costs. The accounting department assembled the following data: Required: 1. Compute the quality costs as a percentage of sales by category and in total for each year. 2. Prepare a multiple-year trend graph for quality costs, both by total costs and by category. Using the graph, assess the progress made in reducing and controlling quality costs. Does the graph provide evidence that quality has improved? Explain. 3. Using the 20X1 quality cost relationships (assume all costs are variable), calculate the quality costs that would have prevailed in 20X4. By how much did profits increase in 20X4 because of the quality improvement program? Repeat for 20X5.arrow_forwardCMA-ADAPTED PERFORMANCE MEASURES The Star Paper Division of Royal Industries is located near Los Angeles. A major expansion of the divisions only plant was completed in April 2015. The expansion consisted of an addition to the existing building, additions to the production line machinery, and the replacement of obsolete and fully depreciated equipment that was no longer efficient or cost-effective. On May 1, 2015, George Harris became manager of Star. Harris had a meeting with Marie Fortner, vice president of operations for Royal, who explained to Harris that the company measured the performance of divisions and division managers on the basis of return on gross assets (ROA). When Harris asked if other measures were used in conjunction with ROA, Fortner replied, Royals top management prefers to use a single performance measure. Star should do well this year now that it has expanded and replaced all of that old equipment. You should have no problem exceeding the divisions historical rate. Ill check with you at the end of each quarter to see how you are doing. Fortner called Harris after the first quarter results were completed because Stars ROA was considerably below the historical rate for the division. Harris told Fortner that he did not believe that ROA was a valid performance measure for Star. Fortner indicated that she would discuss this with others at headquarters and get back to Harris. However, there was no further discussion of the use of ROA but only reports on divisional performance at the end of the second and third quarters. Now that the fiscal year has ended, Harris has received the memorandum in the figure designated for Problem 14. PROBLEM 14: PERFORMANCE MEASURES TO: George Harris, Star Paper Division FROM: Marie Fortner, Royal Industries SUBJECT: Divisional Performance The operating results for the fourth quarter and for our fiscal year ended on April 30 are now complete. Your fourth quarter return on gross assets was only 9 percent, resulting in a return for the year of slightly under 11 percent. I recall discussing your low return after the first quarter and reminding you after the second and third quarters that this level of return is not considered adequate for the Star Paper Division. The return on gross assets at Star has ranged from 15 to 18 percent for the past five years. An 11 percent return may be acceptable at some of Royals other divisions, but not at a proven winner like Star, especially in light of your recently improved facility. Please arrange to meet with me in the near future to discuss ways to restore Stars return on gross assets to its former level. Harris is looking forward to meeting with Fortner as he plans to pursue the discussion about the appropriateness of ROA as a performance measure for Star. While the ROA for Star is below historical levels, the divisions profits for the year are higher than at any previous time. Harris is going to recommend that ROA be replaced with multiple criteria for evaluating performancenamely, dollar profit, receivable turnover, and inventory turnover. Required a. Identify general criteria that should be used in selecting performance measures to evaluate operating managers. b. Describe the probable cause of the decline in the Star Paper Divisions return on gross assets during the fiscal year ended April 30, 2007. c. On the basis of the relationship between Fortner and Harris, as well as the memorandum from Fortner, discuss apparent weaknesses in the performance evaluation process at Royal Industries. d. Discuss whether the multiple performance evaluation criteria that Harris suggested would be appropriate for the evaluation of the Star Paper Division.arrow_forward
- In 2011, Milton Thayne, president of Carbondale Electronics, received a report indicating that quality costs were 31 percent of sales. Faced with increasing pressures from imported goods, Milton resolved to take measures to improve the overall quality of the companys products. After hiring a consultant in 20x0, the company began an aggressive program of total quality control. At the end of 20x5, Milton requested an analysis of the progress the company had made in reducing and controlling quality costs. The Accounting Department assembled the following data: Required: 1. Compute the quality costs as a percentage of sales by category and in total for each year. 2. Prepare a multiple-year trend graph for quality costs, both by total costs and by category. Using the graph, assess the progress made in reducing and controlling quality costs. Does the graph provide evidence that quality has improved? Explain. 3. Using the 20x1 quality cost relationships (assume all costs are variable), calculate the quality costs that would have prevailed in 20x4. By how much did profits increase in 20x4 because of the quality improvement program? Repeat for 20x5.arrow_forwardRizzo Goal Inc. produces and sells hockey equipment, often custom made for online orders. The company has the following performance metrics on its balanced scorecard: days from ordered to delivered, number of shipping errors, customer retention rate, and market share. A measure map illustrates that the days from ordered to delivered and the number of shipping errors are both expected to directly affect the customer retention rate, which affects market share. Additional internal analysis finds that: Every shipping error over three shipping errors per month reduces the customer retention rate by 1.5%. On average, each day above three days from ordered to delivered yields a reduction in the customer retention rate of 1%. Each day before three days from order to delivery yields an increase in the customer retention rate of 1%, on average. Rizzo Goal Inc.s current customer retention rate is 60%. The company estimates that for every 1% increase or decrease in the customer retention rate, market share changes 0.5% in the same direction. Rizzo Goal Inc.s current market share is 21.4%. Ignoring any other factors, if the company has six shipping errors this month and an average of 3.5 days from ordered to delivered, determine (a) the new customer retention rate and (b) the new market share that Rizzo Goal Inc. expects to have.arrow_forwardAs a direct result of your committee's work, quality significantly improved during the latest year while costs and rework decreased. Titan Computer Company also reduced manufacturing capacity because of lowered rework support needs. Sales of AllPad have increased in tandem with a decrease in unit price (following the intent to increase market share). Information about the current period (2016) and prior period (2015) follows. Type of Data 2015 2016 Units of AIIPad produced and sold 800 900 Selling price $450 $430 Pounds of direct material used 3,200 3,300 Direct material cost per pound $35 $35 Manufacturing capacity in units 12,000 11,000 Total conversion costs $1,800,000 $1,650,000 Conversion cost per unit of capacity $150 $150 Selling and customer service capacity customers 90 customers Total selling and customer service costs $495,000 $495,000 Selling and customer service capacity cost and customer…arrow_forward
- As a direct result of your committee's work, quality significantly improved during the latest year while costs and rework decreased. Titan Computer Company also reduced manufacturing capacity because of lowered rework support needs. Sales of AllPad have increased in tandem with a decrease in unit price (following the intent to increase market share). Information about the current period (2016) and prior period (2015) follows. Type of Data 2015 2016 Units of AIIPad produced and sold 800 900 Selling price $450 $430 Pounds of direct material used 3,200 3,300 Direct material cost per pound $35 $35 Manufacturing capacity in units 12,000 11,000 Total conversion costs $1,800,000 $1,650,000 Conversion cost per unit of capacity $150 $150 Selling and customer service capacity customers 90 customers Total selling and customer service costs $495,000 $495,000 Selling and customer service capacity cost and customer $500 $550 Assuming Titan had 70 customers in 2015 and…arrow_forwardClassifying quality costs Darrel & Co. makes electronic components. Chris Darrel, the president, recently instructed Vice President Jim Bruegger to develop a total quality control program. “If we don’t at least match the quality improvements our competitors are making,” he told Bruegger, “we’ll soon be out of business.” Bruegger began by listing various “costs of quality” that Darrel incurs. The first six items that came to mind were: Costs incurred by Darrel customer representatives traveling to customer sites to repair defective products, $13,000. Lost profits from lost sales due to reputation for less-than-perfect products, $35,000. Costs of inspecting components in one of Darrel’s production processes, $40,000 Salaries of engineers who are redesigning components to withstand electrical overloads, $65,000. Costs of reworking defective components after discovery by company inspectors, $50,000. Costs of electronic components returned by customers, $70,000. Classify each item…arrow_forwardStrategy, balanced scorecard, service company. Compton Associates is an architectural firm that has been in practice only a few years. Because it is a relatively new firm, the market for the firm’s services is very competitive. To compete successfully, Compton must deliver quality services at a low cost. Compton presents the following data for 2016 and 2017. Architect labor-hour costs are variable costs. Architect support costs for each year depend on the Architect support capacity that Compton chooses to maintain each year (that is, the number of jobs it can do each year). Architect support costs do not vary with the actual number of jobs done that year. 1. Is Compton Associate’s strategy one of product differentiation or cost leadership? Explain briefly. 2. Describe key measures you would include in Compton’s balanced scorecard and your reasons for doing so.arrow_forward
- Berlin Corp. makes a special-purpose machine called HTW used in the textile industry. Berlin Corp. has designed the HTW machine for 2017 to be distinct from its competitors. It has been generally regarded as a superior machine. Berlin Corp. presents the following data for 2016 and 2017.)(see picture) Berlin Corp. produces no defective machines, but it wants to reduce direct materials usage per HTW machine in 2017. Conversion costs in each year depend on production capacity defined in terms of HTW units that can be produced, not the actual units produced. Selling and customer- service costs depend on the number of customers that Berlin Corp. can support, not the actual number of customers it serves. Berlin Corp. has 75 customers in 2016 and 80 customers in 2017. 2(a). Calculate the growth component from 2016 to 20172(b). Calculate the price-recovery component from 2016 to 2017 2(c). Calculate the growth productivity component from 2016 to 2017arrow_forwardMeasures of Internal Business Process Performance Management of Mittel Rhein AG of Köln, Germany, would like to reduce the amount of time between when a customer places an order and when the order is shipped. For the first quarter of operations during the current year the following data were reported: Required: 1. Compute the throughput time. 2. Compute the manufacturing cycle efficiency (MCE) for the quarter. 3. What percentage of the throughput time was spent in non-value-added activities? 4. Compute the delivery cycle time. 5. If by using Lean Production all queue time during production is eliminated, what will be the new MCE?arrow_forwardApply the Concepts, Cost Reporting Medco Inc., a manufacturing firm, has four activities: purchasing materials, molding, inspecting molds, and grinding imperfect molds. Purchasing materials and molding are necessary activities; inspection and grinding are unnecessary. SQ provides the value-added quantity for each activity; AQ is the actual activity output. The following data pertain to the four activities for the year ending (actual price per unit of the activity driver is assumed to be equal to the standard price): Activity Activity Driver Purchasing Purchasing hours Molding Inspecting Inspection hours Molding hours Grinding. Number of units Required: SQ AQ SP 28,000 34,000 $20 42,000 47,600 121 0 8,400 15 0 6,000 6 1. Prepare a cost report for the year 1 ended that shows value-added costs, non-value-added costs, and total costs for each activity by completing the following table: Value-and Non-Value-Added Cost Report for the Year 1 Ended Activity Value-Added Costs Non-Value-Added…arrow_forward
arrow_back_ios
SEE MORE QUESTIONS
arrow_forward_ios
Recommended textbooks for you
- Managerial AccountingAccountingISBN:9781337912020Author:Carl Warren, Ph.d. Cma William B. TaylerPublisher:South-Western College PubFinancial And Managerial AccountingAccountingISBN:9781337902663Author:WARREN, Carl S.Publisher:Cengage Learning,Managerial Accounting: The Cornerstone of Busines...AccountingISBN:9781337115773Author:Maryanne M. Mowen, Don R. Hansen, Dan L. HeitgerPublisher:Cengage Learning
- Cornerstones of Cost Management (Cornerstones Ser...AccountingISBN:9781305970663Author:Don R. Hansen, Maryanne M. MowenPublisher:Cengage LearningPrinciples of Cost AccountingAccountingISBN:9781305087408Author:Edward J. Vanderbeck, Maria R. MitchellPublisher:Cengage LearningAccounting Information SystemsAccountingISBN:9781337619202Author:Hall, James A.Publisher:Cengage Learning,
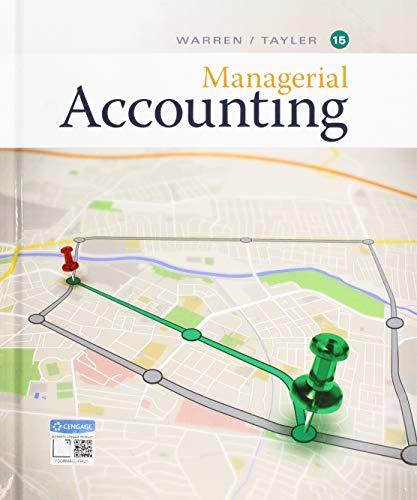
Managerial Accounting
Accounting
ISBN:9781337912020
Author:Carl Warren, Ph.d. Cma William B. Tayler
Publisher:South-Western College Pub
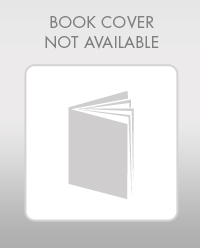
Financial And Managerial Accounting
Accounting
ISBN:9781337902663
Author:WARREN, Carl S.
Publisher:Cengage Learning,
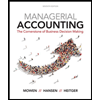
Managerial Accounting: The Cornerstone of Busines...
Accounting
ISBN:9781337115773
Author:Maryanne M. Mowen, Don R. Hansen, Dan L. Heitger
Publisher:Cengage Learning
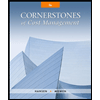
Cornerstones of Cost Management (Cornerstones Ser...
Accounting
ISBN:9781305970663
Author:Don R. Hansen, Maryanne M. Mowen
Publisher:Cengage Learning
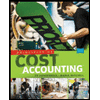
Principles of Cost Accounting
Accounting
ISBN:9781305087408
Author:Edward J. Vanderbeck, Maria R. Mitchell
Publisher:Cengage Learning
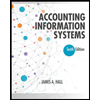
Accounting Information Systems
Accounting
ISBN:9781337619202
Author:Hall, James A.
Publisher:Cengage Learning,
Inspection and Quality control in Manufacturing. What is quality inspection?; Author: Educationleaves;https://www.youtube.com/watch?v=Ey4MqC7Kp7g;License: Standard youtube license