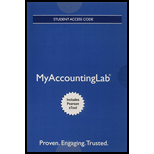
Concept explainers
Quality improvement, relevant costs, and relevant revenues. The Crimson Corporation uses multicolored molding to make plastic lamps. The molding operation has a capacity of 200,000 units per year. The demand for lamps is very strong. Crimson will be able to sell whatever output quantities it can produce at $40 per lamp.
Crimson can start only 200,000 units into production in the molding department because of capacity constraints on the molding machines. If a defective unit is produced at the molding operation, it must be scrapped at a net disposal value of zero. Of the 200,000 units started at the molding operation, 20,000 defective units (10%) are produced. The cost of a defective unit, based on total (fixed and variable)
Direct materials (variable) | $10 per unit |
Direct manufacturing labor, setup labor, and materials-handling labor (variable) | 2 per unit |
Equipment, rent, and other allocated overhead, including inspection and testing costs on scrapped parts (fixed) | 8 per unit |
Total | $20 per unit |
Crimson’s designers have determined that adding a different type of material to the existing direct materials would result in no defective units being produced, but it would increase the variable costs by $3 per lamp in the molding department.
- 1. Should Crimson use the new material? Show your calculations.
Required
- 2. What nonfinancial and qualitative factors should Crimson consider in making the decision?

Want to see the full answer?
Check out a sample textbook solution
Chapter 19 Solutions
MyLab Accounting with Pearson eText -- Access Card -- for Horngren's Cost Accounting
- Nico Parts, Inc., produces electronic products with short life cycles (of less than two years). Development has to be rapid, and the profitability of the products is tied strongly to the ability to find designs that will keep production and logistics costs low. Recently, management has also decided that post-purchase costs are important in design decisions. Last month, a proposal for a new product was presented to management. The total market was projected at 200,000 units (for the two-year period). The proposed selling price was 130 per unit. At this price, market share was expected to be 25 percent. The manufacturing and logistics costs were estimated to be 120 per unit. Upon reviewing the projected figures, Brian Metcalf, president of Nico, called in his chief design engineer, Mark Williams, and his marketing manager, Cathy McCourt. The following conversation was recorded: BRIAN: Mark, as you know, we agreed that a profit of 15 per unit is needed for this new product. Also, as I look at the projected market share, 25 percent isnt acceptable. Total profits need to be increased. Cathy, what suggestions do you have? CATHY: Simple. Decrease the selling price to 125 and we expand our market share to 35 percent. To increase total profits, however, we need some cost reductions as well. BRIAN: Youre right. However, keep in mind that I do not want to earn a profit that is less than 15 per unit. MARK: Does that 15 per unit factor in preproduction costs? You know we have already spent 100,000 on developing this product. To lower costs will require more expenditure on development. BRIAN: Good point. No, the projected cost of 120 does not include the 100,000 we have already spent. I do want a design that will provide a 15-per-unit profit, including consideration of preproduction costs. CATHY: I might mention that post-purchase costs are important as well. The current design will impose about 10 per unit for using, maintaining, and disposing our product. Thats about the same as our competitors. If we can reduce that cost to about 5 per unit by designing a better product, we could probably capture about 50 percent of the market. I have just completed a marketing survey at Marks request and have found out that the current design has two features not valued by potential customers. These two features have a projected cost of 6 per unit. However, the price consumers are willing to pay for the product is the same with or without the features. Required: 1. Calculate the target cost associated with the initial 25 percent market share. Does the initial design meet this target? Now calculate the total life-cycle profit that the current (initial) design offers (including preproduction costs). 2. Assume that the two features that are apparently not valued by consumers will be eliminated. Also assume that the selling price is lowered to 125. a. Calculate the target cost for the 125 price and 35 percent market share. b. How much more cost reduction is needed? c. What are the total life-cycle profits now projected for the new product? d. Describe the three general approaches that Nico can take to reduce the projected cost to this new target. Of the three approaches, which is likely to produce the most reduction? 3. Suppose that the Engineering Department has two new designs: Design A and Design B. Both designs eliminate the two nonvalued features. Both designs also reduce production and logistics costs by an additional 8 per unit. Design A, however, leaves post-purchase costs at 10 per unit, while Design B reduces post-purchase costs to 4 per unit. Developing and testing Design A costs an additional 150,000, while Design B costs an additional 300,000. Assuming a price of 125, calculate the total life-cycle profits under each design. Which would you choose? Explain. What if the design you chose cost an additional 500,000 instead of 150,000 or 300,000? Would this have changed your decision? 4. Refer to Requirement 3. For every extra dollar spent on preproduction activities, how much benefit was generated? What does this say about the importance of knowing the linkages between preproduction activities and later activities?arrow_forwardBienestar, Inc., has two plants that manufacture a line of wheelchairs. One is located in Kansas City, and the other in Tulsa. Each plant is set up as a profit center. During the past year, both plants sold their tilt wheelchair model for 1,620. Sales volume averages 20,000 units per year in each plant. Recently, the Kansas City plant reduced the price of the tilt model to 1,440. Discussion with the Kansas City manager revealed that the price reduction was possible because the plant had reduced its manufacturing and selling costs by reducing what was called non-value-added costs. The Kansas City manufacturing and selling costs for the tilt model were 1,260 per unit. The Kansas City manager offered to loan the Tulsa plant his cost accounting manager to help it achieve similar results. The Tulsa plant manager readily agreed, knowing that his plant must keep pacenot only with the Kansas City plant but also with competitors. A local competitor had also reduced its price on a similar model, and Tulsas marketing manager had indicated that the price must be matched or sales would drop dramatically. In fact, the marketing manager suggested that if the price were dropped to 1,404 by the end of the year, the plant could expand its share of the market by 20 percent. The plant manager agreed but insisted that the current profit per unit must be maintained. He also wants to know if the plant can at least match the 1,260 per-unit cost of the Kansas City plant and if the plant can achieve the cost reduction using the approach of the Kansas City plant. The plant controller and the Kansas City cost accounting manager have assembled the following data for the most recent year. The actual cost of inputs, their value-added (ideal) quantity levels, and the actual quantity levels are provided (for production of 20,000 units). Assume there is no difference between actual prices of activity units and standard prices. Required: 1. Calculate the target cost for expanding the Tulsa plants market share by 20 percent, assuming that the per-unit profitability is maintained as requested by the plant manager. 2. Calculate the non-value-added cost per unit. Assuming that non-value-added costs can be reduced to zero, can the Tulsa plant match the Kansas City per-unit cost? Can the target cost for expanding market share be achieved? What actions would you take if you were the plant manager? 3. Describe the role that benchmarking played in the effort of the Tulsa plant to protect and improve its competitive position.arrow_forwardMallette Manufacturing, Inc., produces washing machines, dryers, and dishwashers. Because of increasing competition, Mallette is considering investing in an automated manufacturing system. Since competition is most keen for dishwashers, the production process for this line has been selected for initial evaluation. The automated system for the dishwasher line would replace an existing system (purchased one year ago for 6 million). Although the existing system will be fully depreciated in nine years, it is expected to last another 10 years. The automated system would also have a useful life of 10 years. The existing system is capable of producing 100,000 dishwashers per year. Sales and production data using the existing system are provided by the Accounting Department: All cash expenses with the exception of depreciation, which is 6 per unit. The existing equipment is being depreciated using straight-line with no salvage value considered. The automated system will cost 34 million to purchase, plus an estimated 20 million in software and implementation. (Assume that all investment outlays occur at the beginning of the first year.) If the automated equipment is purchased, the old equipment can be sold for 3 million. The automated system will require fewer parts for production and will produce with less waste. Because of this, the direct material cost per unit will be reduced by 25 percent. Automation will also require fewer support activities, and as a consequence, volume-related overhead will be reduced by 4 per unit and direct fixed overhead (other than depreciation) by 17 per unit. Direct labor is reduced by 60 percent. Assume, for simplicity, that the new investment will be depreciated on a pure straight-line basis for tax purposes with no salvage value. Ignore the half-life convention. The firms cost of capital is 12 percent, but management chooses to use 20 percent as the required rate of return for evaluation of investments. The combined federal and state tax rate is 40 percent. Required: 1. Compute the net present value for the old system and the automated system. Which system would the company choose? 2. Repeat the net present value analysis of Requirement 1, using 12 percent as the discount rate. 3. Upon seeing the projected sales for the old system, the marketing manager commented: Sales of 100,000 units per year cannot be maintained in the current competitive environment for more than one year unless we buy the automated system. The automated system will allow us to compete on the basis of quality and lead time. If we keep the old system, our sales will drop by 10,000 units per year. Repeat the net present value analysis, using this new information and a 12 percent discount rate. 4. An industrial engineer for Mallette noticed that salvage value for the automated equipment had not been included in the analysis. He estimated that the equipment could be sold for 4 million at the end of 10 years. He also estimated that the equipment of the old system would have no salvage value at the end of 10 years. Repeat the net present value analysis using this information, the information in Requirement 3, and a 12 percent discount rate. 5. Given the outcomes of the previous four requirements, comment on the importance of providing accurate inputs for assessing investments in automated manufacturing systems.arrow_forward
- Shelby Industries has a capacity to produce 45.000 oak shelves per year and is currently selling 40,000 shelves for $32 each. Martin Hardwoods has approached Shelby about buying 1,200 shelves for a new project and is willing to pay $26 each. The shelves can be packaged in bulk; this saves Shelby $1.50 per shelf compared to the normal packaging cost. Shelves have a unit variable cost of $27 with fixed costs of $350,000. Because the shelves dont require packaging, the unit variable costs for the special order will drop from $27 per shelf to $25.50 per shelf. Shelby has enough idle capacity to accept the contract. What is the minimum price per shelf that Shelby should accept for this special order?arrow_forwardBienestar, Inc., implemented cellular manufacturing as recommended by a consultant. The production flow improved dramatically. However, the company was still faced with the competitive need to improve its cycle time so that the production rate is one bottle every four minutes (15 bottles per hour). The cell structure is shown below; the times above the process represent the time required to process one unit. Required: 1. How many units can the cell produce per hour (on a continuous running basis)? 2. How long does it take the cell to produce one unit, assuming the cell is producing on a continuous basis? 3. What must happen so that the cell can produce one bottle every four minutes or 15 per hour, assuming the cell produces on a continuous basis?arrow_forwardArtisan Metalworks has a bottleneck in their production that occurs within the engraving department. Jamal Moore, the COO, is considering hiring an extra worker, whose salary will be $55,000 per year, to solve the problem. With this extra worker, the company could produce and sell 3,000 more units per year. Currently, the selling price per unit is $25 and the cost per unit is $7.85. Using the information provided, calculate the annual financial impact of hiring the extra worker.arrow_forward
- Javier Company has sales of 8 million and quality costs of 1,600,000. The company is embarking on a major quality improvement program. During the next three years, Javier intends to attack failure costs by increasing its appraisal and prevention costs. The right prevention activities will be selected, and appraisal costs will be reduced according to the results achieved. For the coming year, management is considering six specific activities: quality training, process control, product inspection, supplier evaluation, prototype testing, and redesign of two major products. To encourage managers to focus on reducing non-value-added quality costs and select the right activities, a bonus pool is established relating to reduction of quality costs. The bonus pool is equal to 10 percent of the total reduction in quality costs. Current quality costs and the costs of these six activities are given in the following table. Each activity is added sequentially so that its effect on the cost categories can be assessed. For example, after quality training is added, the control costs increase to 320,000, and the failure costs drop to 1,040,000. Even though the activities are presented sequentially, they are totally independent of each other. Thus, only beneficial activities need be selected. Required: 1. Identify the control activities that should be implemented, and calculate the total quality costs associated with this selection. Assume that an activity is selected only if it increases the bonus pool. 2. Given the activities selected in Requirement 1, calculate the following: a. The reduction in total quality costs b. The percentage distribution for control and failure costs c. The amount for this years bonus pool 3. Suppose that a quality engineer complained about the gainsharing incentive system. Basically, he argued that the bonus should be based only on reductions of failure and appraisal costs. In this way, investment in prevention activities would be encouraged, and eventually, failure and appraisal costs would be eliminated. After eliminating the non-value-added costs, focus could then be placed on the level of prevention costs. If this approach were adopted, what activities would be selected? Do you agree or disagree with this approach? Explain.arrow_forwardBrahma Industries sells vinyl replacement windows to home improvement retailers nationwide. The national sales manager believes that if they invest an additional $25,000 in advertising, they would increase sales volume by 10,000 units. Prepare a forecasted contribution margin income statement for Brahma if they incur the additional advertising costs, using this information:arrow_forwardMaterials used by the Instrument Division of Ziegler Inc. are currently purchased from outside suppliers at a cost of 1,350 per unit. However, the same materials are available from the Components Division. The Components Division has unused capacity and can produce the materials needed by the Instrument Division at a variable cost of 900 per unit. a. If a transfer price of 1,000 per unit is established and 75,000 units of materials are transferred, with no reduction in the Components Divisions current sales, how much would Ziegler Inc.s total operating income increase? b. How much would the Instrument Divisions operating income increase? c. How much would the Components Divisions operating income increase?arrow_forward
- Boxer Production, Inc., is in the process of considering a flexible manufacturing system that will help the company react more swiftly to customer needs. The controller, Mick Morrell, estimated that the system will have a 10-year life and a required return of 10% with a net present value of negative $500,000. Nevertheless, he acknowledges that he did not quantify the potential sales increases that might result from this improvement on the issue of on-time delivery, because it was too difficult to quantify. If there is a general agreement that qualitative factors may offer an additional net cash flow of $150,000 per year, how should Boxer proceed with this Investment?arrow_forwardVariety Artisans has a bottleneck in their production that occurs within the engraving department. Arjun Naipul, the COO, is considering hiring an extra worker, whose salary will be $45,000 per year, to solve the problem. With this extra worker, the company could produce and sell 3,500 more units per year. Currently, the selling price per unit is $18 and the cost per unit is $5.85. Using the information provided, calculate the annual financial impact of hiring the extra worker.arrow_forwardLindell Manufacturing embarked on an ambitious quality program that is centered on continual improvement. This improvement is operationalized by declining quality costs from year to year. Lindell rewards plant managers, production supervisors, and workers with bonuses ranging from 1,000 to 10,000 if their factory meets its annual quality cost goals. Len Smith, manager of Lindells Boise plant, felt obligated to do everything he could to provide this increase to his employees. Accordingly, he has decided to take the following actions during the last quarter of the year to meet the plants budgeted quality cost targets: a. Decrease inspections of the process and final product by 50% and transfer inspectors temporarily to quality training programs. Len believes this move will increase the inspectors awareness of the importance of quality; also, decreasing inspection will produce significantly less downtime and less rework. By increasing the output and decreasing the costs of internal failure, the plant can meet the budgeted reductions for internal failure costs. Also, by showing an increase in the costs of quality training, the budgeted level for prevention costs can be met. b. Delay replacing and repairing defective products until the beginning of the following year. While this may increase customer dissatisfaction somewhat, Len believes that most customers expect some inconvenience. Besides, the policy of promptly dealing with customers who are dissatisfied could be reinstated in 3 months. In the meantime, the action would significantly reduce the costs of external failure, allowing the plant to meet its budgeted target. c. Cancel scheduled worker visits to customers plants. This program, which has been very well received by customers, enables Lindell workers to see just how the machinery they make is used by the customer and also gives them first-hand information on any remaining problems with the machinery. Workers who went on previous customer site visits came back enthusiastic and committed to Lindells quality program. Lindells quality program staff believes that these visits will reduce defects during the following year. Required: 1. Evaluate Lens ethical behavior. In this evaluation, consider his concern for his employees. Was he justified in taking the actions described? If not, what should he have done? 2. Assume that the company views Lens behavior as undesirable. What can the company do to discourage it? 3. Assume that Len is a CMA and a member of the IMA. Refer to the ethical code for management accountants in Chapter 1. Were any of these ethical standards violated?arrow_forward
- Cornerstones of Cost Management (Cornerstones Ser...AccountingISBN:9781305970663Author:Don R. Hansen, Maryanne M. MowenPublisher:Cengage LearningEssentials of Business Analytics (MindTap Course ...StatisticsISBN:9781305627734Author:Jeffrey D. Camm, James J. Cochran, Michael J. Fry, Jeffrey W. Ohlmann, David R. AndersonPublisher:Cengage LearningManagerial AccountingAccountingISBN:9781337912020Author:Carl Warren, Ph.d. Cma William B. TaylerPublisher:South-Western College Pub
- Principles of Accounting Volume 2AccountingISBN:9781947172609Author:OpenStaxPublisher:OpenStax CollegeManagerial Accounting: The Cornerstone of Busines...AccountingISBN:9781337115773Author:Maryanne M. Mowen, Don R. Hansen, Dan L. HeitgerPublisher:Cengage LearningEBK CONTEMPORARY FINANCIAL MANAGEMENTFinanceISBN:9781337514835Author:MOYERPublisher:CENGAGE LEARNING - CONSIGNMENT
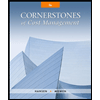
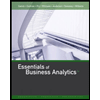
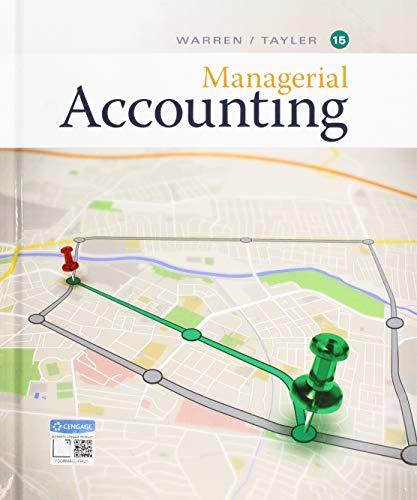
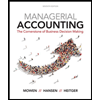
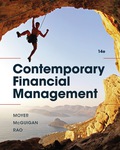