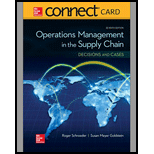
Lawn King, Inc.: Sales and Operations Planning eXcel
John Conner, marketing manager for Lawn King, looked over the beautiful countryside as he drove to the corporate headquarters in Moline, Illinois, John had asked his boss, Kathy Wayne, the general manager of Lawn King, to call a meeting in order to review the latest
John started the meeting by reviewing the latest situation: “I’ve just returned from our annual sales meeting, and I think we lost more sales last year than we thought, due to back-order conditions at the factory. We have also reviewed the forecast for next year and feel that sales will be 110,000 units in fiscal year 2015. The marketing department feels this forecast is realistic and could be exceeded if all goes well.”
At this point, James Fairday interrupted by saying, “John, you’ve got to be kidding. Just three months ago we all sat in this same room and you predicted sales of 98,000 units for fiscal ‘15. Now you’ve raised the forecast by 12 percent. How can we do a reasonable job of production planning when we have a moving target to shoot at?”
Kathy interjected, “Jim, I appreciate your concern, but we have to be responsive to changing market conditions. Here we are in September and we still haven’t got a firm plan for fiscal ‘15, which has just started. I want to use the new forecast and develop a Sales and Operations Plan (S&OP) for next year as soon as possible.”
John added, “We’ve been talking to our best customers, and they’re complaining about back orders during the peak selling season. A few have threatened to drop our product line if they don't get better service next year. We have to produce not only enough product but also the right models to service the customer.”
MANUFACTURING PROCESS
Lawn King is a medium-sized producer of lawn mower equipment. Last year, sales were $14.5 million and pretax profits were $2 million, as shown in Exhibit 1. The company makes four lines of lawn mowers: an 18-inch push mower, a 20-inch push mower, a 20-inch self-propelled mower, and a 22-inch deluxe self-propelled mower. All these mowers are made on the same assembly line. During the year, the line is changed over from one mower to the next to meet the actual and projected demand.
EXHIBIT 1
FY2013 | FY2014 | |
Sales | $11,611 | $14,462 |
Cost of goods sold | ||
Materials | 6,340 | 8,005 |
Direct labor | 2,100 | 2,595 |
743 | 962 | |
Overhead | 256 | 431 |
Total CGS | 9,439 | 11,993 |
G&A expense | 270 | 314 |
Selling expense | 140 | 197 |
Total expenses | 9,849 | 12,504 |
Pretax profit | 1,762 | 1,958 |
The changeover cost of the production line depends on which type of mower is being produced and the next production model planned. For example, it is relatively easy to change over from the 20-inch push mower to the 20-inch self-propelled mower, since the mower frame is the same. The self-propelled mower has a propulsion unit added and a slightly larger engine. The company estimated the changeover costs as shown in Exhibit 2.
EXHIBIT 2 Line changeover cost matrix.
*SP denotes “self-propelled.” Changeover cost includes the wages of the workforce used to adjust the assembly line from one model configuration to another.
Lawn King fabricates the metal frames and metal parts for its lawn mowers in its own machine shop. These fabricated parts are sent to the assembly line along with parts purchased directly from vendors. In the past year, approximately $8 million in parts and supplies were purchased; including engines, bolts, paint, wheels, and sheet steel. An inventory of $1 million in purchased parts is held to supply the machine shop and the assembly line. When a particular mower is running on the assembly line, only a few days of parts are kept at the plant, since supplies are constantly coming into the factory.
A total of 100 employees work at the main plant in Moline. These employees include 60 workers on the assembly line, 25 workers in the machine shop, 10 maintenance workers, and 5 office staff. A beginning assembly line worker is paid $10.15 per hour plus $2.90 an hour in benefits. Senior maintenance and machine-shop employees earn as much as $17 per hour.
It generally takes about two weeks for a new employee to reach full productivity on the assembly line. After three months, an employee can request rotation to other jobs on the line if job variety is desired. At least some of the workers find the work quite repetitive and boring.
The plant is unionized, but relations between the union and the company have always been good. Nevertheless, employee turnover has been high. In the past year, approximately 50 percent of the employees left the company, representing a total training cost of $42,000 for the year. There is also considerable absenteeism, especially on Mondays and Fridays, causing production disruptions. To handle this situation, six “fillers” are kept on the workforce to fill in for people who are absent on a given day. These fillers also help train the new employees when they are not needed for direct production work.
PRODUCTION PLANNING
The actual sales and forecasts are shown in Exhibit 3. Not only are the sales highly seasonal, but total sales are dependent on the weather. If the weather is good in early spring, customers will be more inclined to buy a new mower. A good grass-growing season also encourages sales during the summer.
EXHIBIT 3 Sales data in units.
It appears that customers are more likely to buy the high-priced self-propelled mowers in good economic times. In recessionary periods, the bottom-of-the-line 18-inch mower does better.
The production strategy in current use might be described as a one-shift level-workforce strategy with overtime used as needed. The workforce is not always exactly level due to turnover and short-run production requirements. Nevertheless, the policy is to keep the workforce as level as possible. Overtime is used when the regular workforce cannot meet production requirements.2
The actual monthly production output and sales for fiscal year 2014 are shown in Exhibit 4. Differences between sales and production were absorbed by the inventory. If stockouts occurred, the order was backlogged and filled from the next available production run. Lawn King utilized a 30 percent carrying cost per year for inventory.3
EXHIBIT 4 Units of production and sales, fiscal year 2014.
Each June, a S&OP plan is prepared for the upcoming fiscal year. The plan shows the level of production for each model type and month of the year. This plan is used for personnel planning, inventory planning, and budget preparation. Each month during the year, the plan is revised on the basis of the latest conditions and data.
BACK TO THE MEETING
The meeting continued with Joan Peterson saying, “We must find a way to reduce our costs. Last year we carried too much inventory, which required a great deal of capital. At 30 percent carrying cost, we cannot afford to build up as much inventory again next year.”
Harold Pinter added, “If we reduce our inventories by more nearly chasing demand, the labor force will fluctuate from month to month and our hiring and layoff costs will increase. It currently costs $800 to hire an employee, including the lower productivity on the line during the training period and the effort required to find new employees. I also believe it costs $1,500 to lay off an employee, including the severance costs and supplemental
James Fairday expressed concern that a new shift might have to be added to accommodate the higher forecast. "We are already at plant capacity, and the additional units in the new forecast can't be made with one shift. I want to be sure these sales forecasts are realistic before we go through the trouble of hiring an entire second shift.”
Lunchtime had arrived and the meeting was drawing to a close. Kathy Wayne emphasized that she wanted a new production plan developed soon. “Jim, I want you to develop a S&OP plan that considers the costs of inventory, overtime, hiring, and layoff. If your plan results in back orders, we will have to incur greater costs later in the year to meet demand. I will not allow the same stockout situation that we experienced last year.” The meeting adjourned for lunch.
Discussion Questions
- 1. Develop a forecast to use as a basis for Sales and Operations Planning.
- 2. Develop a S&OP plan by month for fiscal year 2015. Consider the use of several different production strategies. Which strategy do you recommend? Use of Excel will greatly save time in making these plans.
This case was prepared as a basis for class discussion, not to illustrate either effective or ineffective handling of an administrative situation.

Want to see the full answer?
Check out a sample textbook solution
Chapter CS Solutions
OPERATIONS MANAGMENT IN...-ACCESS
- Scenario 4 Sharon Gillespie, a new buyer at Visionex, Inc., was reviewing quotations for a tooling contract submitted by four suppliers. She was evaluating the quotes based on price, target quality levels, and delivery lead time promises. As she was working, her manager, Dave Cox, entered her office. He asked how everything was progressing and if she needed any help. She mentioned she was reviewing quotations from suppliers for a tooling contract. Dave asked who the interested suppliers were and if she had made a decision. Sharon indicated that one supplier, Apex, appeared to fit exactly the requirements Visionex had specified in the proposal. Dave told her to keep up the good work. Later that day Dave again visited Sharons office. He stated that he had done some research on the suppliers and felt that another supplier, Micron, appeared to have the best track record with Visionex. He pointed out that Sharons first choice was a new supplier to Visionex and there was some risk involved with that choice. Dave indicated that it would please him greatly if she selected Micron for the contract. The next day Sharon was having lunch with another buyer, Mark Smith. She mentioned the conversation with Dave and said she honestly felt that Apex was the best choice. When Mark asked Sharon who Dave preferred, she answered, Micron. At that point Mark rolled his eyes and shook his head. Sharon asked what the body language was all about. Mark replied, Look, I know youre new but you should know this. I heard last week that Daves brother-in-law is a new part owner of Micron. I was wondering how soon it would be before he started steering business to that company. He is not the straightest character. Sharon was shocked. After a few moments, she announced that her original choice was still the best selection. At that point Mark reminded Sharon that she was replacing a terminated buyer who did not go along with one of Daves previous preferred suppliers. Ethical decisions that affect a buyers ethical perspective usually involve the organizational environment, cultural environment, personal environment, and industry environment. Analyze this scenario using these four variables.arrow_forwardScenario 4 Sharon Gillespie, a new buyer at Visionex, Inc., was reviewing quotations for a tooling contract submitted by four suppliers. She was evaluating the quotes based on price, target quality levels, and delivery lead time promises. As she was working, her manager, Dave Cox, entered her office. He asked how everything was progressing and if she needed any help. She mentioned she was reviewing quotations from suppliers for a tooling contract. Dave asked who the interested suppliers were and if she had made a decision. Sharon indicated that one supplier, Apex, appeared to fit exactly the requirements Visionex had specified in the proposal. Dave told her to keep up the good work. Later that day Dave again visited Sharons office. He stated that he had done some research on the suppliers and felt that another supplier, Micron, appeared to have the best track record with Visionex. He pointed out that Sharons first choice was a new supplier to Visionex and there was some risk involved with that choice. Dave indicated that it would please him greatly if she selected Micron for the contract. The next day Sharon was having lunch with another buyer, Mark Smith. She mentioned the conversation with Dave and said she honestly felt that Apex was the best choice. When Mark asked Sharon who Dave preferred, she answered, Micron. At that point Mark rolled his eyes and shook his head. Sharon asked what the body language was all about. Mark replied, Look, I know youre new but you should know this. I heard last week that Daves brother-in-law is a new part owner of Micron. I was wondering how soon it would be before he started steering business to that company. He is not the straightest character. Sharon was shocked. After a few moments, she announced that her original choice was still the best selection. At that point Mark reminded Sharon that she was replacing a terminated buyer who did not go along with one of Daves previous preferred suppliers. What should Sharon do in this situation?arrow_forwardScenario 4 Sharon Gillespie, a new buyer at Visionex, Inc., was reviewing quotations for a tooling contract submitted by four suppliers. She was evaluating the quotes based on price, target quality levels, and delivery lead time promises. As she was working, her manager, Dave Cox, entered her office. He asked how everything was progressing and if she needed any help. She mentioned she was reviewing quotations from suppliers for a tooling contract. Dave asked who the interested suppliers were and if she had made a decision. Sharon indicated that one supplier, Apex, appeared to fit exactly the requirements Visionex had specified in the proposal. Dave told her to keep up the good work. Later that day Dave again visited Sharons office. He stated that he had done some research on the suppliers and felt that another supplier, Micron, appeared to have the best track record with Visionex. He pointed out that Sharons first choice was a new supplier to Visionex and there was some risk involved with that choice. Dave indicated that it would please him greatly if she selected Micron for the contract. The next day Sharon was having lunch with another buyer, Mark Smith. She mentioned the conversation with Dave and said she honestly felt that Apex was the best choice. When Mark asked Sharon who Dave preferred, she answered, Micron. At that point Mark rolled his eyes and shook his head. Sharon asked what the body language was all about. Mark replied, Look, I know youre new but you should know this. I heard last week that Daves brother-in-law is a new part owner of Micron. I was wondering how soon it would be before he started steering business to that company. He is not the straightest character. Sharon was shocked. After a few moments, she announced that her original choice was still the best selection. At that point Mark reminded Sharon that she was replacing a terminated buyer who did not go along with one of Daves previous preferred suppliers. What does the Institute of Supply Management code of ethics say about financial conflicts of interest?arrow_forward
- Scenario 3 Ben Gibson, the purchasing manager at Coastal Products, was reviewing purchasing expenditures for packaging materials with Jeff Joyner. Ben was particularly disturbed about the amount spent on corrugated boxes purchased from Southeastern Corrugated. Ben said, I dont like the salesman from that company. He comes around here acting like he owns the place. He loves to tell us about his fancy car, house, and vacations. It seems to me he must be making too much money off of us! Jeff responded that he heard Southeastern Corrugated was going to ask for a price increase to cover the rising costs of raw material paper stock. Jeff further stated that Southeastern would probably ask for more than what was justified simply from rising paper stock costs. After the meeting, Ben decided he had heard enough. After all, he prided himself on being a results-oriented manager. There was no way he was going to allow that salesman to keep taking advantage of Coastal Products. Ben called Jeff and told him it was time to rebid the corrugated contract before Southeastern came in with a price increase request. Who did Jeff know that might be interested in the business? Jeff replied he had several companies in mind to include in the bidding process. These companies would surely come in at a lower price, partly because they used lower-grade boxes that would probably work well enough in Coastal Products process. Jeff also explained that these suppliers were not serious contenders for the business. Their purpose was to create competition with the bids. Ben told Jeff to make sure that Southeastern was well aware that these new suppliers were bidding on the contract. He also said to make sure the suppliers knew that price was going to be the determining factor in this quote, because he considered corrugated boxes to be a standard industry item. Is Ben Gibson acting legally? Is he acting ethically? Why or why not?arrow_forwardScenario 3 Ben Gibson, the purchasing manager at Coastal Products, was reviewing purchasing expenditures for packaging materials with Jeff Joyner. Ben was particularly disturbed about the amount spent on corrugated boxes purchased from Southeastern Corrugated. Ben said, I dont like the salesman from that company. He comes around here acting like he owns the place. He loves to tell us about his fancy car, house, and vacations. It seems to me he must be making too much money off of us! Jeff responded that he heard Southeastern Corrugated was going to ask for a price increase to cover the rising costs of raw material paper stock. Jeff further stated that Southeastern would probably ask for more than what was justified simply from rising paper stock costs. After the meeting, Ben decided he had heard enough. After all, he prided himself on being a results-oriented manager. There was no way he was going to allow that salesman to keep taking advantage of Coastal Products. Ben called Jeff and told him it was time to rebid the corrugated contract before Southeastern came in with a price increase request. Who did Jeff know that might be interested in the business? Jeff replied he had several companies in mind to include in the bidding process. These companies would surely come in at a lower price, partly because they used lower-grade boxes that would probably work well enough in Coastal Products process. Jeff also explained that these suppliers were not serious contenders for the business. Their purpose was to create competition with the bids. Ben told Jeff to make sure that Southeastern was well aware that these new suppliers were bidding on the contract. He also said to make sure the suppliers knew that price was going to be the determining factor in this quote, because he considered corrugated boxes to be a standard industry item. As the Marketing Manager for Southeastern Corrugated, what would you do upon receiving the request for quotation from Coastal Products?arrow_forwardQ: Using exponential smoothing with a weight ex of 0.6 on actual values: (a) if sales are $45,000 and $50,000 for 2010 and 2011, what would you forecast for 2012? (b) given this forecast and actual 2012 sales of $53,000, what would you then forecast for 20013? (a) (b)arrow_forward
- 5. (a) When a new business is started, or a patent idea needs funding, venture capitalists or investment bankers will want to see a business plan that includes forecast information related to a profit and loss statement. What type of forecasting information do you suppose would be required? (b) A picnic spot is open on Thursday, Friday and Saturday. The manager hopes to improve resource availability and scheduling of part-time employees by forecasting visitors in the next week. Data on visitors of the recent 5 weeks at the spot has been found. On Saturday, Thursday, and Friday there were 182. 95, and 280 in week 1; 197, 105, and 295 in week2; 178, 92, and 275 in week 3; 210, 109, and 305 in week 4; and 192, 100. and 284 in week 5. i. Find seasonal relatives of the days. ii. Forecast number of visitors in the resort for week 6 and that is for the days of week 6.arrow_forward4, The accompanying dataset provides the closing prices for four stocks and the stock exchange over 12 days. Complete parts a through c. Complete the exponential smoothing forecast model for stock B. (Type integers or decimals rounded to two decimal places as needed.) Date Forecast B 09/03/2010 09/07/2010 enter your response here 09/08/2010 enter your response here 09/09/2010 enter your response here 09/10/2010 enter your response here 09/13/2010 enter your response here 09/14/2010 enter your response here 09/15/2010 enter your response here 09/16/2010 enter your response here 09/17/2010 enter your response here 09/20/2010 enter your response here 09/21/2010 enter your response here Date A B C D Stock Exchange 09/03/2010 127.07 18.54 20.84 15.44 10,536.56 09/07/2010 124.84 18.21 20.45 15.55 10,245.77 09/08/2010 125.67 17.77 20.83 15.72…arrow_forwardFlamingo Educational Services, a company located in the Tema metropolis, is a nationwide market leader in the publishing and distribution of textbooks for first and second cycle schools. Somehow, Flamingo does not use forecasts for production planning. Instead, the operations manager decides which books to produce and the batch size, based on orders and the amounts in inventory. The books that have the fewest amounts in inventory get the highest priority. Demand is uneven, and the company has experienced being overstocked on some items and out of others. Being under-stocked has occasionally created tensions with managers of the retail bookstores the company works with. Flamingo is on the verge of losing a lucrative contract with the Ghana Education Service over a complaint that the books produced over the last four months have defective binding as well as slight but noticeable variations in print quality and sizes of the finished books. Some staff members, however,…arrow_forward
- A store’s demand figures are given in the table. According to this, what is the linear regression forecast for Week 12. (You need to use Excel to solve this problem. Do not round intermediate calculations. Round your final answers to two decimal places.arrow_forwardFollowing are two weekly forecasts made by twodifferent methods for the number of gallons of gasoline, inthousands, demanded at a local gasoline station. Also shownare actual demand levels, in thousands of gallons. What are the MAD and MSE for each method?arrow_forwardThe Handy-Dandy Department Store had forecast sales of $110,000 for the previous week. The actual sales were $130,000.a. What is the forecast for this week, using exponential smoothing and α = .1?b. If sales this week turn out to be $120,000, what is the forecast for next week?arrow_forward
- Purchasing and Supply Chain ManagementOperations ManagementISBN:9781285869681Author:Robert M. Monczka, Robert B. Handfield, Larry C. Giunipero, James L. PattersonPublisher:Cengage LearningPractical Management ScienceOperations ManagementISBN:9781337406659Author:WINSTON, Wayne L.Publisher:Cengage,Management, Loose-Leaf VersionManagementISBN:9781305969308Author:Richard L. DaftPublisher:South-Western College Pub
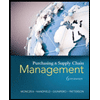
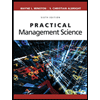
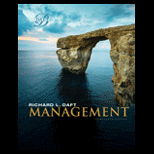